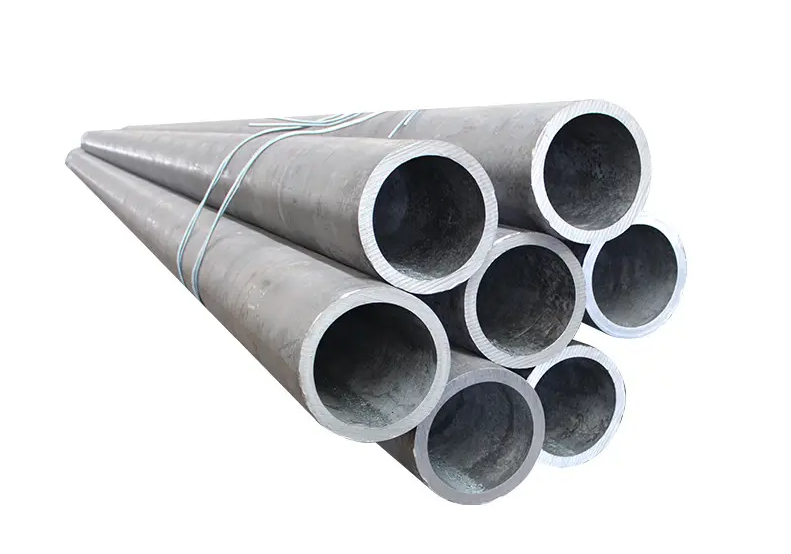
Метод зварювання товстостінних трубопроводів з товстого тиску домашньої сталі A335 P91: область техніки – Цей винахід стосується сфери зварювальної технології, особливо пов'язаний з методом зварювання товстостінних трубопроводів високого тиску.
We have Largest inventory of ASTM A335 P91 Alloy Steel Seamless Pipe
Alloy Steel Pipe A 335 P91:
Розмір : 1/2″ для 24 “І від & NB
Розклад: СЧ20, Сч30, Труба sch40.
тип : Зварні / виготовлений / Безшовні
Довжина : Single Random, Double Random & Cut Length.
кінець : Простый Кінець, Скошений кінець.
Матеріали :
Alloy Steel Pipe A335 P91 – AS Pipe A335 P91
ASTM A335, Гр. P5, P9, P11, P12, P21, P22 & P91
ASTM A335 P91 Chrome Pipe Composition Composition
Сорт | США | C≤ | MN | Р≤ | З≤ | Si≤ | Кл | МО |
P1 | K11522 | 0.10~0.20 | 0.30~0.80 | 0.025 | 0.025 | 0.10~0.50 | - | 0.44~0.65 |
P2 | К11547 | 0.10~0.20 | 0.30~0.61 | 0.025 | 0.025 | 0.10~0.30 | 0.50~0.81 | 0.44~0.65 |
P5 | K41545 | 0.15 | 0.30~0.60 | 0.025 | 0.025 | 0.50 | 4.00~6.00 | 0.44~0.65 |
P5b | K51545 | 0.15 | 0.30~0.60 | 0.025 | 0.025 | 1.00~2.00 | 4.00~6.00 | 0.44~0.65 |
P5c | K41245 | 0.12 | 0.30~0.60 | 0.025 | 0.025 | 0.50 | 4.00~6.00 | 0.44~0.65 |
P9 | S50400 | 0.15 | 0.30~0.60 | 0.025 | 0.025 | 0.50~1.00 | 8.00~10.00 | 0.44~0.65 |
P11 | К11597 | 0.05~0.15 | 0.30~0.61 | 0.025 | 0.025 | 0.50~1.00 | 1.00~1,50 | 0.44~0.65 |
P12 | К11562 | 0.05~0.15 | 0.30~0.60 | 0.025 | 0.025 | 0.50 | 0.80~1.25 | 0.44~0.65 |
P15 | K11578 | 0.05~0.15 | 0.30~0.60 | 0.025 | 0.025 | 1.15~1.65 | - | 0.44~0.65 |
P21 | K31545 | 0.05~0.15 | 0.30~0.60 | 0.025 | 0.025 | 0.50 | 2.65~3.35 | 0.80~1.60 |
P22 | К21590 | 0.05~0.15 | 0.30~0.60 | 0.025 | 0.025 | 0.50 | 1.90~2.60 | 0.87~1.13 |
P91 | K91560 | 0.08~0.12 | 0.30~0.60 | 0.020 | 0.010 | 0.20~0.50 | 8.00~9.50 | 0.85~1.05 |
P92 | K92460 | 0.07~0.13 | 0.30~0.60 | 0.020 | 0.010 | 0.50 | 8.50~9.50 | 0.30~0.60 |
A335 Gr P91 Pipes Composition Standard
Сі, % | Кл, % | C, % | МО, % | MN, % | P, % | N, % | S, % | V, % | Н, % | NB, % | Ал, % |
0.2 для 0.5 | 8.0 для 9.5 | 0.08 для 0.12 | 0.85 для 1.05 | 0.3 для 0.6 | 0.02 | 0.03 для 0.07 | 0.01 | 0.18 для 0.25 | 0.4 | 0.06 для 0.10 | 0.04 |
ASTM A335 P91 Pipes Mechanical Strength Table
Elongational | Tensile Properties | НВ | Yield Properties |
20 | 585 | 250 | 415 |
Equivalent Material Grade Of SA335 Gr P91 Pipes
США | ASTM | Equivalent Матеріал | АСМЭ |
---|---|---|---|
K91560 | A335 P91 | K90901, T91, 1.4903, X10CrMoVNb9-1 | SA335 P 91 |
ASTM | АСМЭ | ВІН Г 3458 | США | BS | DIN | ISO | ABS | NK | LRS |
---|---|---|---|---|---|---|---|---|---|
A335 P9 | SA335 P9 | STPA 26 | S50400 | 3604 P1 629-470 | 2604 II TS38 |
Фон: A335 P91 steel is a modified 9Cr-1Mo steel, primarily incorpo
A335P11 A335P91 A335P22 40cr 10CrMO910 35crmo 27SiMn Q345B 16Mn Welded Alloy Steel Pipe
rating alloy elements such as V and Nb into the original 9Cr-1Mo martensitic heat-resistant steel. This steel possesses excellent high-temperature oxidation resistance, high-temperature steam corrosion resistance, and creep resistance, effectively reducing structural weight and finding widespread application in large boiler units, pipeline systems, and the petrochemical industry. однак, due to the air-cooled martensitic nature of A335 P91 steel, it exhibits lower plasticity and poorer weldability, imposing high requirements on welding processes, impact toughness of welded joints, weld brittleness, Термічна обробка після зварювання, and heat-affected zones of welds. Traditional A335 P91 steel welding generally employs manual gas tungsten arc welding (GTAW) for root pass and manual shielded metal arc welding (SMAW) for filling and capping, necessitating strict control of line energy, preheat temperature, and interpass temperature during the welding process. This method demands a high level of welding environment and welder skill, and manual welding efficiency is extremely low, consuming time and effort, severely restricting piping progress, affecting construction schedules, and particularly evident for large-diameter thick-walled pipelines.
Тому, the rational selection of welding parameters and processes for A335 P91 steel and the development of welding process conditions suitable for production hold significant practical and economic value.
Invention Content: To address the shortcomings of existing technology, the technical problem to be solved by the present invention is to provide a method for welding high-pressure thick-walled pipelines of domestic A335 P91 steel, aiming to improve welding efficiency and weld якість, reduce construction costs and labor intensity, and improve the working environment.
To achieve the above objectives, the present invention employs the following technical solutions:
Метод зварювання товстостінних трубопроводів з товстого тиску домашньої сталі A335 P91, comprising the following steps in sequence:
(1) Pre-weld bevel processing: Process the welding area of the pipeline to be welded into a double V-shaped bevel, perform dye penetrant inspection on the bevel surface to ensure no surface cracks, and clean the bevel and the surface rust, масло, and oxides within a 20mm area on both sides of the bevel;
Continuing with the welding method for domestically produced A335 P91 high-pressure thick-walled steel pipes:
- Термічна обробка після зварювання: Після зварювання, seal both ends of the pipe and use electric heating to heat the area on both sides of the weld, at least 3 times the width of the weld and no less than 25mm. Heat the area to a temperature range of 750-770°C and hold it for 2.5-4 години, depending on the pipe thickness.
Please note that the temperature in this method is monitored using an infrared thermometer. This welding method for A335 P91 high-pressure thick-walled steel pipes has the following advantages:
-
The use of multi-layer, multi-pass welding reduces the cross-sectional area of each weld layer, improving the toughness of the welded joint and avoiding the narrowing of the heat-affected zone in thick welds, as well as the softening of the weld joint during long-term operation at high temperatures.
-
Manual gas tungsten arc welding (GTAW) for root welding has a slower welding speed, and sealing both ends of the pipe helps control the interlayer temperature. Automatic submerged arc welding (Бачив) for filling and covering layers has a faster welding speed and higher current, releasing heat more quickly. At least one end of the pipe should be unsealed, and continuous welding can be performed without the need for interlayer temperature control.
-
Using small-diameter welding wires (no more than 2.5mm) and low-hydrogen flux for welding can reduce the linear energy during the welding process, improve the welding deposition rate, refine the base material grains, and reduce the possibility of defects such as porosity and cracks in the weld.
-
In windy environments, the protection effect of automatic submerged arc welding is better than other arc welding processes.
-
Compared to traditional manual welding methods, this method effectively shortens the heat treatment and welding cycle, improves weld якість and welding efficiency, reduces labor intensity, and saves construction costs.
Implementation example 1: Using domestic A335P91 pipeline DN350 as the base material, the following welding method is adopted:
(1) The welding area of the pipe to be welded is processed into a double V-shaped groove as shown in Figure 1, with a blunt edge height of 1mm, a bottom angle of 60±5° in the direction of the pipe length, a height of 15mm, and an upper angle of 78-82° in the direction of the pipe length. The groove surface is colored inspected to ensure that there are no surface cracks on the groove. The surface rust, oil stains, oxides, д. within 20mm on both sides of the groove are cleaned;
(2) The two sections of the welded pipe are assembled, ensuring that the end face gap of the butt joint is 3-6mm, the height is even, and the misalignment is not greater than 1mm;
(3) Manual argon arc welding GTAW is used for the bottom welding. Перед зварюванням, the end ports of the pipe to be welded are blocked, and the inner wall or back of the weld is filled with argon gas for protection. The steel pipe to be welded is preheated, and the temperature of the groove is monitored in real-time using an infrared thermometer. When the temperature reaches 160℃, welding begins, using ER90S-B9 welding wire with a diameter of to weld three layers. The process parameters are selected as follows: DC positive connection of the power supply, welding current of 118A, arc voltage of 14V, and welding speed of 3-10cm/min. Attention should be paid to the following points during manual argon arc welding GTAW: A) The surface of the workpiece to be welded should not be ignited by the arc, tested for current, or temporarily welded to support or clamp;b) The manual argon arc welding starts from the lowest point of the pipe to be welded, and is symmetrically welded by two people, with the welding joints staggered between 100-150mm; C) During manual argon arc welding, the preheating temperature on both sides of the groove should be monitored in real-time, and the preheating temperature should be strictly controlled between 150℃ and 200℃; D) During manual argon arc welding, wind protection measures should be taken, and the wind speed in the welding environment should not exceed 2m/s. There should be no draft in the pipe to be welded, and moisture, rain, and snow protection measures should be taken;
(4) Automatic submerged arc welding SAW is used for filling and covering. Before automatic submerged arc welding filling and covering, at least one end of the pipe to be welded is unblocked, and the welding area is preheated. When the temperature reaches 200℃, continuous welding begins, using EB9 welding wire with a diameter of and MARATHON543 welding flux for multi-layer and multi-pass filling and covering welding. The SAW welding parameters are selected as follows: DC reverse connection of the power supply, welding current of 280A, arc voltage of 28V, and welding speed of 25-45cm/min.
Attention should be paid to the following points during automatic submerged arc welding SAW:
A) The welding wire should be kept clean and dry, and the welding flux should be stored in a dry place to prevent moisture absorption;
b) The welding wire should be fed smoothly and evenly, and the welding flux should be added in time to ensure the welding якість;
C) The welding speed should be stable, and the welding gun should be kept perpendicular to the pipe axis to ensure the consistency of the weld bead;
D) The welding slag should be removed in time after each layer of welding is completed, and the surface of the weld should be cleaned with a wire brush or grinding wheel to ensure the quality of the next layer of welding;
Е) The welding process should be monitored in real-time, and the welding parameters should be adjusted in time according to the actual situation to ensure the welding quality. After the welding is completed, the weld surface should be inspected visually and by non-destructive testing to ensure that there are no defects such as cracks, pores, шлакові включення, and incomplete penetration. Нарешті, the welded joint should be heat-treated according to the process requirements to eliminate welding stress and improve the mechanical properties of the welded joint.
Implementation example 2: Using imported A335P91 pipeline DN500 as the base material, the following welding method is adopted:
(1) The welding area of the pipe to be welded is processed into a double V-shaped groove as shown in Figure 1, with a blunt edge height of 1.5mm, a bottom angle of 60±5° in the direction of the pipe length, a height of 20mm, and an upper angle of 78-82° in the direction of the pipe length. The groove surface is colored inspected to ensure that there are no surface cracks on the groove. The surface rust, oil stains, oxides, д. within 20mm on both sides of the groove are cleaned;
(2) The two sections of the welded pipe are assembled, ensuring that the end face gap of the butt joint is 4-8mm, the height is even, and the misalignment is not greater than 1.5mm;
(3) Automatic submerged arc welding SAW is used for bottom welding. Перед зварюванням, the end ports of the pipe to be welded are blocked, and the inner wall or back of the weld is filled with argon gas for protection. The steel pipe to be welded is preheated, and the temperature of the groove is monitored in real-time using an infrared thermometer. When the temperature reaches 200℃, welding begins, using EB9 welding wire with a diameter of and MARATHON543 welding flux for multi-layer and multi-pass filling and covering welding. The SAW welding parameters are selected as follows: DC reverse connection of the power supply, welding current of 350A, arc voltage of 32V, and welding speed of 25-45cm/min. Attention should be paid to the following points during automatic submerged arc welding SAW: A) The welding wire should be kept clean and dry, and the welding flux should be stored in a dry place to prevent moisture absorption; b) The welding wire should be fed smoothly and evenly, and the welding flux should be added in time to ensure the welding quality; C) The welding speed should be stable, and the welding gun should be kept perpendicular to the pipe axis to ensure the consistency of the weld bead; D) The welding slag should be removed in time after each layer of welding is completed, and the surface of the weld should be cleaned with a wire brush or grinding wheel to ensure the quality of the next layer of welding; Е) The welding process should be monitored in real-time, and the welding parameters should be adjusted in time according to the actual situation to ensure the welding quality.
(4) Automatic submerged arc welding SAW is used for filling and covering. Before automatic submerged arc welding filling and covering, at least one end of the pipe to be welded is unblocked, and the welding area is preheated. When the temperature reaches 250℃, continuous welding begins, using EB9 welding wire with a diameter of and MARATHON543 welding flux for multi-layer and multi-pass filling and covering welding. The SAW welding parameters are selected as follows: DC reverse connection of the power supply, welding current of 450A, arc voltage of 36V, and welding speed of 25-45cm/min. After the welding is completed, the weld surface should be inspected visually and by non-destructive testing to ensure that there are no defects such as cracks, pores, шлакові включення, and incomplete penetration. Нарешті, the welded joint should be heat-treated according to the process requirements to eliminate welding stress and improve the mechanical properties of the welded joint.
Ви повинні бути увійшли в Щоб залишити коментар.