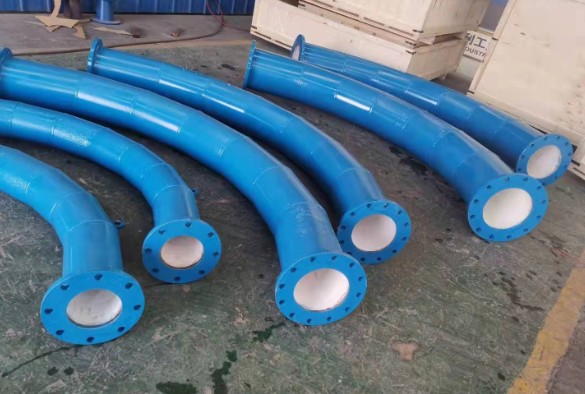
Seramik astarlı dirsek: Kapsamlı analiz
Seramik astarlı dirsekler, endüstriyel boru sistemlerinde kritik bileşenlerdir, Aşındırıcı ile başa çıkmak için tasarlanmış, aşındırıcı, ve yüksek sıcaklık malzemeleri. Bu dirsekler, çeliğin dayanıklılığını seramik astarların olağanüstü aşınması ve korozyon direnci ile birleştirir, onları enerji üretimi gibi sektörlerde vazgeçilmez kılmak, Madencilik, Metalurji, ve kimyasal işleme. Bu belge, seramik astarlı dirseklerin derinlemesine bir analizini sağlar, Bir parametre tablosu dahil, Malzeme bileşimi, Mekanik Özellikler, aşınma direnci, bükme açıları, ve performansları ve uygulamaları hakkında ayrıntılı bir tartışma.
Parametreler Tablosu
Parametre | Açıklama | Tipik değerler |
---|---|---|
Dış Boru Malzemesi | Dirseğin temel malzemesi | Karbon çelik (örneğin, 20# dikişsiz çelik), Paslanmaz çelik |
Seramik astar malzemesi | İç astar malzemesi | alümina (Al₂O₃, ≥% 90), Zirkonya sertleştirilmiş alümina (ZTA) |
Boru çapı | Borunun iç çapı | 0.5 inç 24 inç (özelleştirilebilir) |
Seramik kalınlığı | Seramik astarın kalınlığı | 6 mm – 25 mm |
Bükme açısı | Yön açısı değişimi | 22.5°, 45°, 90°, 180° (Özel açılar mevcut) |
viraj yarıçap | Eğri yarıçapı | 1.5D – 5D (D = Boru çapı) |
Çalışma sıcaklığı | Maksimum sıcaklık direnci | -50° C ila 900 ° C (uzun vadeli), 2000 ° C'ye kadar (kısa vadeli) |
Basınç Dayanımı | Çember gücü | 300 – 500 MPA |
aşınma direnci | Karbon çeliğine göre | 15 – 20 Kıda Yüksek |
Mikro korsanlık | Seramik astarın sertliği | YG 1000 – 1600 |
Yoğunluk | Seramik astar yoğunluğu | 3.62 g/cm³ (alümina) |
hizmet ömrü | Aşındırıcı koşullar altında beklenen ömür | 5 – 20 yıl (Uygulamaya bağlı olarak) |
Malzeme bileşimi
Seramik astarlı dirsekler iki birincil malzeme katmanından oluşur: dış çelik boru ve iç seramik astar. Dış boru tipik olarak karbon çeliğinden yapılır (örneğin, 20# dikişsiz çelik) veya paslanmaz çelik, Yapısal bütünlük ve kaynak veya flanş kolaylığı sağlamak. Seramik astar, genellikle yüksek saflıkta alüminden oluşur (Al₂O₃) veya zirkonya sertleştirilmiş alümina (ZTA), yüksek sıcaklık dirençli yapıştırıcılar veya mekanik birbirine konulma teknikleri kullanılarak iç yüzeye bağlanır.
Dış Boru Malzemesi
Dış boru, dirseğin yapısal omurgası görevi görür. Karbon çeliği, maliyet etkinliği nedeniyle yaygın olarak kullanılır, yüksek güç, ve kaynaklanabilirlik. Aşındırıcı ortamları içeren uygulamalar için, Korozyon direncini arttırmak için paslanmaz çelik tercih edilebilir. Çelik tabaka, dirseğin mekanik gerilmelere dayanmasını sağlar, baskı ve etki gibi, Mevcut boru sistemlerine entegrasyonu kolaylaştırırken.
Seramik astar malzemesi
Seramik astar, dirseğin olağanüstü performansının anahtarıdır. alümina, bir al₂o₃ içeriği ile 90% veya daha yüksek, yüksek sertliği nedeniyle en yaygın kullanılan malzemedir, aşınma direnci, ve termal stabilite. Zirkonya sertleştirilmiş alümina (ZTA) iyileştirilmiş tokluk ve darbe direnci sunan gelişmiş bir varyanttır, Yüksek mekanik şoklu dinamik sistemler için uygun hale getirmek. Seramik tabakası tipik olarak fayans olarak uygulanır, kollu, veya monolitik bir kaplama, Üretim sürecine bağlı olarak.
Seramik malzemesinin ince tahıl yapısı ve yüksek yoğunluğu dayanıklılığına katkıda bulunur. örneğin, Alümina seramikleri elmas benzeri sertlik ve üstün mekanik güç sergiler, onları zorlu uygulamalar için ideal hale getiriyor. Seramik malzeme seçimi belirli operasyonel gereksinimlere göre uyarlanabilir, aşırı aşınma veya kimyasal maruziyet gibi.
Mekanik Özellikler
Seramik astarlı dirseklerin mekanik özellikleri, çelik dış tabakanın ve seramik iç astarın bir bileşimidir.. Bu özellikler, dirseğin baskıya dayanma yeteneğini belirler, Etkisi, ve termal şok, zorlu ortamlarda güvenilir performans sağlamak.
Gücü
Seramik astarlı dirseklerin kasnak mukavemeti, radyal basınca karşı direnci ölçen, tipik olarak değişir 300 Hedef 500 MPA. Bu mukavemet esas olarak çelik dış katmandan türetilmiştir., yapısal destek sağlar. Seramik astar, kırılganken, Yüzey bozulmasına direnerek ve aşındırıcı koşullar altında dirseğin şeklini koruyarak genel bütünlüğe katkıda bulunur.
Eğilme Dayanımı, veya bükme gücü, seramik astar için kritik bir özelliktir. Alümina seramikleri yüksek bükülme mukavemeti sergiler, Genellikle 3 noktalı veya 4 noktalı bükülme testleri ile test edilir. Değerler aşabilir 300 MPA, Tahıl boyutuna bağlı olarak, gözeneklilik, ve imalat kalite. ancak, Seramiğin kırılganlığı.
Sertlik
Seramik astarının mikro sertliği, Vickers ölçeğinde ölçüldü, HV'den değişir 1000 Hedef 1600 Alümina bazlı malzemeler için. Bu sertlik karbon çeliğinden önemli ölçüde daha yüksektir (Yaklaşık HV 150-200 Söndürdükten sonra) hatta tungsten karbür (YG 1200-1500), Seramik tabakayı çizilmeye ve aşınmaya son derece dirençli hale getirmek. Yüksek sertlik, dirseğin kömür tozu gibi aşındırıcı malzemeleri işleyebilmesini sağlar, kül, veya önemli yüzey hasarı olmadan cevher bulamaç.
Tokluk ve etki direnci
Alümina seramikleri doğal olarak kırılgan olsa da, Zorlukları, ZTA kullanılarak veya çelik katmanla bağlanmayı optimize ederek arttırılabilir.. Çelik dış boru, mükemmel darbe direnci sağlar, Seramik astarını başka türlü kırabilecek mekanik şokları emme. Pratikte, Seramik astarlı dirsekler, yüksek hızlı partikül etkilerini içeren uygulamalarda esneklik göstermiştir, pnömatik taşıma sistemleri gibi.
Termal şok direnci
Seramik astarlı dirsekler, uzun süreler boyunca -50 ° C ila 900 ° C arasında değişen sıcaklıklarda çalışabilir, 2000 ° C'ye kadar kısa süreli direnç. Seramik astarın düşük termal genleşme katsayısı, hızlı sıcaklık değişiklikleri altında çatlamayı en aza indirir, Çelik tabaka ek stabilite sağlarken. Bu termal şok direnci, enerji üretimi gibi sektörlerde çok önemlidir, Boru hatlarının dalgalanan sıcaklıklar yaşayabileceği yer.
aşınma direnci
Aşınma direnci, seramik astarlı dirseklerin tanımlayıcı özelliğidir, Bunları geleneksel çelik veya dökme demir bağlantı parçalarından ayırma. Seramik astarın aşınmaya ve erozyona dayanma yeteneği, dirseğin hizmet ömrünü uzatır 15 Hedef 20 Çizilmemiş karbon çelik dirseklerine kıyasla zamanlar, Bakım maliyetlerini ve kesinti süresini azaltmak.
Aşınma direnci mekanizması
Seramik astarın yüksek sertliği ve pürüzsüz yüzeyi, aşındırıcı aşınma nedeniyle malzeme kaybını en aza indirir. Yüksek hızlı bulamaç veya toz içeren uygulamalarda (örneğin, kömür külü, kireçtaşı, veya kum), Seramik tabaka, sürtünmeyi azaltarak ve parçacık gömülmesini önleyerek erozyona direnir. Aşınma direnci, seramik astarın performansı karbon çeliğiyle karşılaştırılarak ölçülür, ömür boyu artış gösteren çalışmalarla 20 aşındırıcı koşullarda zamanlar.
Seramiğin düşük çarpma açılarında düşük sürtünme faktörü, parçacıkların aşındırıcı etkisini azaltarak aşınma direncini daha da artırır. Bu tesis, dirseklerde özellikle faydalıdır, Akış yönünün değiştiği yerde türbülansı ve aşınma. Pürüzsüz iç yüzey ayrıca malzeme birikmesini önler, tutarlı akış hızlarının sağlanması ve tıkanma riskini azaltmak.
Karşılaştırmalı Analiz
Gazete dayanıklı diğer malzemelerle karşılaştırıldığında, dökme bazalt veya alaşım çelik gibi, Seramik astarlar üstün performans sunar. Bazalt, Dayanıklı iken, daha düşük aşınma direncine sahiptir ve yüksek hızlı etkiler altında çatlamaya eğilimlidir. alaşımlı çelik, Yaklaşık yüzey sertliği ile 60 HRC, seramiklerden daha hızlı yıpranıyor (80+ HRC eşdeğeri). Gerçek dünya uygulamalarında, kömür yakıtlı enerji santralleri gibi, Seramik astarlı dirsekler, kalın duvarlı çelik dirsekleri beş veya daha fazla bir faktörle geride bırakmıştır..
hizmet ömrü
Seramik astarlı bir dirseğin hizmet ömrü, uygulamanın şiddetine bağlıdır. Uçucu kül veya çimento için pnömatik taşıma sistemlerinde, aşınma yoğun olduğu yer, Seramik astar sürebilir 5 Hedef 10 yıl, nazaran 1-2 Çelik dirsekler için yıllar. Daha az aşındırıcı koşullarda, kimyasal işleme gibi, Yaşamlar aşabilir 20 yıl. Seramik tabakasının ortalama aşınma oranı yaklaşık 0.5-1 yılda mm, yani 6 mm astar bitebilir 5 Zorlu ortamlarda yıllar.
bükme açıları
Seramik astarlı dirsekler, farklı boru düzenlerini karşılamak için çeşitli bükme açılarında mevcuttur. Açı, yön değiştirme derecesini belirler, Dirsek içindeki akış dinamiklerini ve aşınma desenlerini etkilemek.
Standart bükme açıları
En yaygın bükülme açıları 22.5 °, 45°, 90°, ve 180°, özel açılar belirli gereksinimleri karşılamak için üretilebilir olsa da. Bu açılar standarda karşılık gelir boru montajı tasarımlar:
- 22.5° Dirsek: Boru sistemlerinde hafif yönlü ayarlar için kullanılır.
- 45° Dirsek: Yönde ılımlı bir değişiklik sağlar, 90 ° dirseklere kıyasla türbülansı azaltmak.
- 90° Dirsek: Dik dönüşler için en yaygın kullanılan açı, Sıkı düzenlerde yaygın.
- 180° Dirsek: Akış yönünü tersine çevirmek için bir dönüş virajı, genellikle ısı eşanjörlerinde veya kompakt sistemlerde kullanılır.
Bend RADIUS
Viraj yarıçapı, tipik olarak boru çapının katı olarak ifade edilir (D), 1.5D ile 5D arasında değişir. Daha büyük bir yarıçap (örneğin, 5D) daha yumuşak bir eğri ile sonuçlanır, Virajda akış direncini ve aşınma konsantrasyonunu azaltmak. Kısa Radius Dirsekleri (1.5D) daha kompakt ama daha keskin dönüşler nedeniyle daha yüksek aşınma yaşıyor. Yarıçap seçimi uzay kısıtlamalarına bağlıdır, Akış Gereksinimleri, ve düşünceler giy.
Performans üzerindeki etki
Bükme açısı ve yarıçapı dirseğin performansını önemli ölçüde etkiler. Daha keskin açılar (örneğin, 90°) ve daha küçük yarıçaplar türbülansı ve parçacık etkisini arttırır, Dış Eğride Hızlandırıcı Aşınma. Seramik astarlar, zor bir, Aşındırıcı parçacıkları saptıran pürüzsüz yüzey. Tersine, Daha büyük yarıçaplar ve daha küçük açılar aşınmayı daha eşit olarak dağıtıyor, uzun ömürlülüğü geliştirmek.
Ayrıntılı analiz
Seramik astarlı dirsekler, gelişmiş malzemeler ve mühendislik tasarımının bir kaynaşmasını temsil eder, Aşındırıcı ve aşındırıcı malzeme taşımacılığının zorluklarını ele almak için uyarlanmış. Bu bölüm üretim süreçlerini araştırıyor, Uygulamalar, Avantajları, sınırlamalar, ve son gelişmeler, Modern endüstrideki rolleri hakkında bütünsel bir anlayış sağlamak.
üretim süreçleri
Seramik astarlı dirsekler birkaç teknik kullanılarak üretilir, her biri performanslarını ve maliyetlerini etkiler:
- Savurma döküm: Erimiş alümina, santrifüj kuvvet altında çelik bir borunun içine dökülür, Yoğun bir, tekdüze seramik tabakası. Bu yöntem, yüksek bağlanma mukavemeti sağlar ve büyük çaplı dirsekler için idealdir.
- Karo astar: Önceden oluşturulmuş seramik karolar, yüksek sıcaklık yapıştırıcılar veya mekanik birbirine geçme kullanılarak çelik borunun iç yüzeyine yapıştırılır.. Bu yaklaşım, astar kalınlığı üzerinde hassas kontrole izin verir ve karmaşık şekiller için uygundur.
- Kol astarı: Çelik boruya önceden fabriklanmış bir seramik manşon yerleştirilir ve yapıştırıcılar veya büzülme ile sabitlenir. Bu yöntem standart dirsekler için etkilidir ve pürüzsüz bir iç yüzey sağlar.
Çelik boru tipik olarak sıcak bükme veya kaynak ile oluşturulur, Yüksek basınçlı uygulamalar için sorunsuz seçeneklerle tercih edilir. Astar sonrası, Dirsek, seramik çelik bağını sağlamlaştırmak için ısıl işlemeye uğrar, operasyonel stres altında dayanıklılığı sağlamak.
Uygulamalar
Seramik astarlı dirsekler, çok çeşitli endüstrilerde çok çeşitli endüstrilere yerleştirilir.:
- enerji üretimi: Kömür yakıtlı bitkilerde toz haline getirilmiş kömür taşımak için kullanılır, kül, ve baca gazı desülfürizasyon sistemlerinde kireçtaşı bulamaç.
- Madencilik: Aşındırıcı bulamaçları ele alır, cevher atıkları ve kum gibi, Mineral işleme boru hatlarında.
- Metalurji: Yüksek sıcaklıklı ortamlarda erimiş metal veya cüruf taşır.
- Kimyasal işleme: Aşındırıcı sıvıları ve gazları yönetir, Seramiğin kimyasal inertliğinden yararlanmak.
- Çimento endüstrisi: Çimento klinker ve hammaddeleri aktarır, Aşındırıcı parçacıklardan aşınmaya direnmek.
Avantajları
Seramik astarlı dirseklerin benimsenmesi çok sayıda fayda sağlar:
- Uzatılmış Hizmet Ömrü: Geleneksel çelik dirsekleri önemli bir farkla geride bırakır, Yedek frekansını azaltma.
- Maliyet Verimliliği: Daha düşük bakım ve kesinti maliyetleri, daha yüksek ilk yatırımı dengeler.
- Geliştirilmiş Akış: Pürüzsüz seramik yüzeyler sürtünme ve basınç kaybını azaltır, Sistem verimliliğini artırma.
- Çok yönlülük: Çok çeşitli sıcaklıklar için uygun, baskılar, ve medya türleri.
- Kolay Kurulum: Standart flanşlarla hafif tasarım ve uyumluluk entegrasyonu basitleştirir.
sınırlamalar
Avantajlarına rağmen, Seramik astarlı dirsekler bazı dezavantajları var:
- Daha yüksek başlangıç maliyeti: Seramik ve özel üretim süreçlerinin kullanımı, çelik dirseklere kıyasla ön masrafları arttırır.
- kırılganlık: Seramik astar, çelik tabaka tarafından desteklenmezse, aşırı mekanik şok altında çatlayabilir.
- Karmaşık onarım: Hasarlı seramik astarların yerinde onarılması zordur, genellikle değiştirme gerektirir.
Son Gelişmeler
Seramik astarlı dirsek teknolojisindeki son gelişmeler, performansı artırmaya ve maliyetleri azaltmaya odaklanmıştır.:
- Gelişmiş seramikler: ZTA ve silikon karbür kullanımı (SiC) iyileştirilmiş tokluk ve aşınma direnci, Uygulama aralıklarını genişleten.
- Sırt çantası tasarımı: Dirseğin dış eğrisine çelik plaka veya seramik “sırt çantası” eklemek, yüksek etkili bölgelerde aşınma direncini arttırır.
- Kendi kendine kilitlenen fayanslar: 360 ° mekanik birbirine taşıyan yenilikçi karo tasarımları, bağlanma mukavemetini arttırır ve delaminasyon risklerini azaltır.
- Hibrit astarlar: Seramikleri polimerler veya metallerle birleştirmek, maliyeti dengeleyen hibrit astarlar oluşturur, Tokluk, ve aşınma direnci.
Bu gelişmeler, giderek daha talep edilen endüstriyel koşullar için seramik astarlı dirsekleri optimize etme çabalarını yansıtıyor, Aşınma yoğun uygulamalar için tercih edilen bir çözüm olarak kaldıklarından emin olmak.
Çözüm
Seramik astarlı dirsekler, malzeme bilimi ve mühendislik arasındaki sinerjinin bir kanıtıdır, Eşsiz aşınma direnci sunmak, korozyon direnci, ve termal stabilite. Parametreleri - malzeme bileşiminden bükülme açılarına kadar - belirli operasyonel ihtiyaçları karşılayacak şekilde uyarlanabilir, onları dünya çapında endüstriler için çok yönlü bir seçim yapmak. Daha yüksek başlangıç maliyetleri ve kırılganlıkları zorluklar doğururken, Azaltılmış bakım ve genişletilmiş hizmet ömrünün uzun vadeli faydaları bu dezavantajlardan çok daha ağır basıyor. Teknoloji ilerledikçe, Seramik astarlı dirsekler gelişmeye devam edecek, Modern endüstriyel boru sistemlerinin temel taşı olarak rollerini sağlamlaştırma.
Olmalısın giriş Yorum yazmak için.