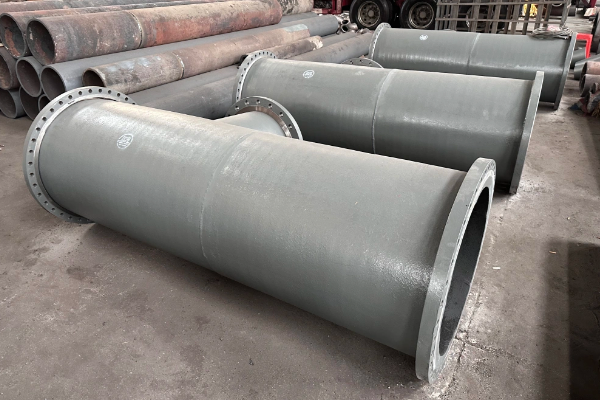
Bimetalik Kompozit Boru: Erozyona Dayanıklı Astarın Hazırlanması ve Performans Değerlendirilmesi
giriiş
Birçok endüstriyel sektörde, petrol ve gaz gibi, Madencilik, ve kimyasal işleme, Boru sistemleri şiddetli aşındırıcı ortamlara maruz kalır. Bu ortamlar genellikle aşındırıcı malzemelerin taşınmasını içerir, çamur gibi, Kum, veya diğer parçacıklar, boruların iç yüzeylerinde ciddi aşınma ve yıpranmaya neden olabilecek. Geleneksel metalik borular, güçlü iken, genellikle erozyona bağlı arızalardan muzdariptir, pahalı onarımlara yol açıyor, aksama süresi, ve operasyonel verimliliğin azalması. Bu zorluğun üstesinden gelmek için, bimetalik kompozit borular umut verici bir çözüm olarak ortaya çıktı, Metalik bir dış katmanın gücünü özel bir iç astarın erozyon direnciyle birleştiriyor.
Bimetalik kompozit boru konsepti iki farklı malzemenin kullanımını içerir: bir baz metal (tipik olarak çelik) yapısal bütünlük ve korozyon için- veya erozyona dayanıklı astar malzemesi, sert alaşım veya seramik gibi, aşınmaya karşı korumak için. Bu makale, bimetalik kompozit borulardaki erozyona dayanıklı kaplamaların hazırlanması ve performans değerlendirmesinin derinlemesine araştırılmasını sağlar.. Kullanılan malzemeleri inceleyeceğiz, üretim süreçleri, ve bu boruların aşındırıcı ortamlardaki performansı, tablolar ve verilerle desteklenir.
Bimetalik kompozit borunun yapısı, korozyona dayanıklı bir malzemeden yapılmış bir iç katmandan oluşur., genellikle kaplama veya astar tabakası olarak anılır, ve yapısal bir temel malzemeden oluşan bir dış katman. Kaplama malzemesi korozyona karşı dayanıklılığı nedeniyle seçilmiştir, erozyon, ve spesifik çevresel koşullar, temel malzeme mekanik mukavemeti ve maliyet etkinliği nedeniyle seçilirken.
Kaplama ile taban malzemeleri arasındaki bağlanma patlayıcı bağlama gibi yöntemlerle sağlanır., rulo yapıştırma, veya kaynak. Bu teknikler güçlü ve dayanıklı bir bağlantı sağlar, borunun amaçlanan çalışma koşullarına dayanmasına izin vermek.
Bimetalik kompozit borular çeşitli endüstrilerde kullanılmaktadır, petrol ve gaz dahil, Kimyasal işleme, enerji üretimi, ve madencilik. Özellikle korozyonun olduğu ortamlarda etkilidirler., erozyon, veya yüksek sıcaklıklar endişe vericidir. Korozyona dayanıklı kaplama boruyu kimyasal hasarlardan korur, taban malzemesi yapısal bütünlük sağlarken.
Bimetalik kompozit boruların spesifik özelliklerinin ve performansının, kullanılan malzemelere göre değişebileceğini bilmek çok önemlidir., üretim süreçleri, ve başvuru koşulları. Bu nedenle, Bu boruların seçilmesi ve kullanılması konusunda ayrıntılı rehberlik için üreticilere veya endüstri uzmanlarına danışılması önerilir..
Teknik Özellikler
- Dış Katman: Sıradan çelik borudan yapılmıştır.
- İç Astar: Yüksek kromlu dökme demirden oluşur, bir döküm işlemiyle oluşturulmuş.
- Dirsek için Malzeme Sınıfı: KMTBCr26
- Çalışma Sıcaklığı: 150° C
- Çalışma basıncı: 0.4 MPA
- Çalışma Ortamı: Toz haline getirilmiş kömür ve hava iki fazlı akış
- Maksimum Akış Hızı: 28 m/sn
Teknik Gereksinimler
Bimetalik aşınmaya dayanıklı kompozit dirsek aşağıdaki performans kriterlerini karşılamalıdır:
- Eğilme Dayanımı: > 610 MN/m²
- Çekme dayanımı: > 415 MN/m²
- Darbe Dayanıklılığı: > 15 J/cm²
- Aşınmaya Dirençli Katmanın Sertliği: > 50
Bimetalik aşınmaya dayanıklı kompozit dirseğin iç ve dış yüzeyleri pürüzsüz ve çapak gibi kusurlardan arındırılmış olmalıdır., çatlaklar, gözeneklilik, ve hava kabarcıkları. Ortamın akış yönü açıkça işaretlenmelidir. Her dirseğin iç astarı tek bir işlemle oluşturulmalıdır, Üretim sonrası kaynak dikişine izin verilmeden.
Boyut ve Malzeme Özellikleri
- Boyutsal Sapma: GB3092 ile uyumluluk, GB8162, ve GB8163 standartları.
- İç Astar Kalınlık Sapması: ≤ +1.2 mm.
- Ağırlık: Her dirsek tasarım ağırlığını aşmamalıdır, açıkça işaretlenmesi gerekenler.
Kompozit boru kullanılarak üretilir DİKİŞSİZ ÇELİK BORU, İlgili performans anlaşmalarına bağlı kalmak. Bimetalik aşınmaya dayanıklı kompozit dirseğin montajı doğrudan kaynak yoluyla gerçekleştirilir, dış kaynaklı boru için 16MnR# çelik kullanılması.
Kurulum ve Bakım
Dirseğin her giriş ve çıkışında belirli uzunlukta düz bir bölüm bulunur, dirsek gövdesinin malzemesi ve duvar kalınlığı ile tutarlı. Toz besleme boru hattına kaynak yapmak için ilave 100 mm'lik bir geçiş bölümü sağlanmıştır. Sahadaki kaynak, oda sıcaklığında iyi performans sağlamalıdır.
Bimetalik aşınmaya dayanıklı kompozit dirseğin hizmet ömrünün en az sürmesi beklenmektedir. 10 yıl (Yaklaşık olarak 8,000 yıllık çalışma saatleri). Anormal koşullar altında, toz besleme boru hattında kendiliğinden yanma gibi, astarın aşınmaya dayanıklı tabakası çatlamadan veya soyulmadan sağlam kalmalıdır. Tasarım, kolay boşaltmayı kolaylaştırmalıdır, Kurulum, ve bakım.
Kalite güvencesi
Fabrikadan ayrılmadan önce, her dirsek ilgili standartlara göre sızdırmazlık performansı testine tabi tutulur. Belirtilen şartları karşılayamayan ürünler kalite ve performans standartlarının fabrikadan çıkmasına izin verilmiyor. “DL/T” ile uyumluluk 680-1999 Aşınmaya Dirençli Boru Hatları için Teknik Koşullar Standardı zorunludur.
Bimetal Kompozit Aşınmaya Dayanıklı Dirsek Ana Teknik Parametreler
- Kalınlığı:
- İç Yay: 22 mm
- Dış Yay: 32 mm
- Eksantriklik: 5 mm
- Tasarım Basıncı: 1.6 MPA
- Hidrolik Test Basıncı: 5.6-19 MPA
- Tasarım Sıcaklığı: 350° C
Özel korindon seramikleri, nadir metal oksitlerden yapılmış ve 1730°C'de sinterlenmiştir, aşınma direncini arttırmak için aşınma yüzeyine dahil edilir, matris sıradan bir metal kompozit boru olarak kalırken.
Endüstriyel Borularda Erozyona Dirençli Astar İhtiyacı
Aşındırıcı Ortamlardaki Zorluklar
Petrol ve gaz gibi endüstrilerde kullanılan borular, Madencilik, ve kimyasal işlemler sıklıkla aşındırıcı parçacıkların yüksek hızlarda taşındığı zorlu koşullara maruz kalır.. Bu parçacıklar neden olabilir erozyon, maddi kayıplara yol açıyor, boru duvarlarının incelmesi, ve nihai başarısızlık. Aşındırıcı ortamların ortaya çıkardığı temel zorluklar arasında şunlar bulunmaktadır::
- Maddi Kayıp: Aşındırıcı parçacıkların sürekli etkisi, malzemenin boru yüzeyinden kademeli olarak çıkarılmasına yol açar.
- Kısaltılmış Ömür: Erozyon boruların bozulmasını hızlandırır, operasyonel ömrünün azaltılması.
- Artan Bakım Maliyetleri: Aşınmış boruların sık sık onarılması veya değiştirilmesi, daha yüksek bakım maliyetlerine ve operasyonel kesintilere neden olur.
- Güvenlik Riskleri: Erozyonla ilgili arızalar sızıntılara neden olabilir, dökülmeler, ve hatta felaketle sonuçlanan başarısızlıklar, personel ve çevre için güvenlik riskleri oluşturma.
Bimetalik Kompozit Boruların Avantajları
Bimetalik kompozit borular, iki malzemenin avantajlarını birleştirerek aşındırıcı ortamların yarattığı zorluklara çözüm sunar:
- yapısal güç: Dış katman, tipik olarak karbon çeliğinden veya paslanmaz çelikten yapılır, İç basınca ve dış kuvvetlere dayanmak için gerekli mekanik gücü sağlar.
- Erozyon Direnci: İç astar, sert alaşım veya seramik malzemeden yapılmış, erozyona karşı üstün direnç sunar, boruyu aşındırıcı aşınmaya karşı korumak.
Bimetalik kompozit borular kullanılarak, endüstriler boru sistemlerinin ömrünü önemli ölçüde uzatabilir, bakım maliyetlerini azaltmak, ve genel operasyonel verimliliği artırın.
Bimetalik Kompozit Borularda Kullanılan Malzemeler
Baz Metal (Dış Katman)
Bimetalik kompozit borunun ana metali, uygulamanın mekanik gereksinimlerine göre seçilir. Dış katman için kullanılan yaygın malzemeler şunları içerir::
- Karbon çelik: Karbon çeliği yüksek mukavemeti nedeniyle yaygın olarak kullanılmaktadır., düşük maliyetli, ve imalat kolaylığı. Korozyonun önemli bir sorun olmadığı uygulamalar için uygundur.
- Paslanmaz çelik: Paslanmaz çelik, karbon çeliğinden daha iyi korozyon direnci sunar ve genellikle hem erozyon hem de korozyonun söz konusu olduğu ortamlarda kullanılır..
- alaşımlı çelik: Alaşımlı Çelikler, krom-molibden çelikleri gibi, gelişmiş güç ve sıcaklık direnci sağlar, onları yüksek sıcaklık uygulamaları için uygun hale getirir.
Astar Malzemesi (İç Katman)
İç astar malzemesi, erozyona ve taşınan malzemelerin aşındırıcı kuvvetlerine dayanma kabiliyetine göre seçilmiştir.. Ortak astar malzemeleri şunları içerir::
- Sert Alaşımlar: Sert Alaşımlar, krom karbür veya tungsten karbür gibi, erozyona dayanıklı astarlar için yaygın olarak kullanılır. Bu malzemeler mükemmel sertlik ve aşınma direnci sunar, aşındırıcı parçacıklara karşı koruma sağlamak için onları ideal kılar.
- Seramik: Seramik malzemeler, alümina gibi (Al₂O₃) veya silisyum karbür (SiC), olağanüstü sertlikleri ve erozyona dayanıklılıklarıyla tanınırlar. Seramikler genellikle metal astarların yeterli koruma sağlayamadığı yüksek derecede aşındırıcı ortamlarda kullanılır..
- Polimer Esaslı Astarlar: Bazı durumlarda, Polimer Esaslı Astarlar, poliüretan veya epoksi kaplamalar gibi, Erozyon direnci sağlamak için kullanılır. Bu malzemeler genellikle orta düzeyde erozyona sahip uygulamalarda ve esnekliğin gerekli olduğu uygulamalarda kullanılır..
tablo 1: Bimetalik Kompozit Borularda Kullanılan Ortak Malzemeler
Bileşen | Malzeme | özellikler | Uygulamalar |
---|---|---|---|
Dış Katman | Karbon çelik | yüksek güç, düşük maliyetli, yapımı kolay | Genel endüstriyel uygulamalar |
Paslanmaz çelik | korozyon direnci, iyi mekanik özellikler | Kimyasal işleme, Petrol & Gaz | |
alaşımlı çelik | Yüksek sıcaklık dayanımı, geliştirilmiş güç | Yüksek sıcaklık boru sistemleri | |
İç Astar | Krom Karbür | yüksek sertlik, mükemmel aşınma direnci | Madencilik, çamur taşıma |
Tungsten Karbür | Aşırı sertlik, üstün erozyon direnci | Petrol & Gaz, yüksek aşınmalı ortamlar | |
alümina (Al₂O₃) | Olağanüstü sertlik, yüksek erozyon direnci | Kimyasal işleme, yüksek aşınma uygulamaları | |
silisyum karbür (SiC) | yüksek sertlik, termal kararlılık, Kimyasal direnç | Yüksek sıcaklık, yüksek aşınmalı ortamlar | |
Poliüretan | Esneklik, orta derecede erozyon direnci | Düşük ila orta dereceli aşınma uygulamaları | |
Epoksi Kaplamalar | Kimyasal direnç, orta derecede erozyon direnci | Kimyasal işleme, su arıtma |
Bimetalik Kompozit Boruların Hazırlanması
Kaplama ve Kaplama Teknikleri
Bimetalik kompozit boruların hazırlanması, erozyona dayanıklı astarın ana metale uygulanmasını içerir.. Dış katman ile iç astar arasında güçlü bir bağ elde etmek için çeşitli teknikler kullanılır, kompozit borunun aşındırıcı ortamların zorlu koşullarına dayanabilmesinin sağlanması. Yaygın teknikler şunları içerir::
1. Kaynaklı Kaplama
Kaynak kaplama kaplaması, sert alaşımlı bir malzemenin kaynak teknikleri kullanılarak ana metal borunun iç yüzeyi üzerine biriktirilmesini içerir.. Süreç genellikle aşağıdaki adımları içerir:
- Yüzey hazırlığı: Ana metal borunun iç yüzeyi temizlenerek kaplama malzemesinin düzgün yapışmasını sağlayacak şekilde hazırlanır..
- Kaynak: Sert alaşımlı bir malzeme, krom karbür gibi, gibi kaynak teknikleri kullanılarak iç yüzeye biriktirilir. plazma ark kaynağı ya Tozaltı ark kaynağı.
- Kaynak Sonrası İşlem: Kaplama uygulandıktan sonra, boru, artık gerilimleri azaltmak ve ana metal ile kaplama arasındaki bağı geliştirmek için ısıl işleme tabi tutulabilir.
2. Savurma döküm
Santrifüj döküm, bir borunun iç yüzeyine seramik veya metal kaplama uygulamak için kullanılan bir tekniktir.. Süreç aşağıdaki adımları içerir:
- Kalıp Hazırlama: Borunun istenilen ölçülerinde kalıp hazırlanır.
- döküm: Erimiş metal veya seramik malzeme kalıba dökülür., ve kalıp yüksek hızda döndürülür. Merkezkaç kuvveti malzemeyi kalıbın iç yüzeyine doğru iter, düzgün bir astar oluşturmak.
- Soğutma ve Katılaştırma: Astar malzemesinin soğumasına ve katılaşmasına izin verilir, baz metal ile güçlü bir bağ oluşturmak.
3. Termal Püskürtme
Termal püskürtme, sert alaşım veya seramik malzemenin eritilip borunun iç yüzeyine püskürtülmesi işlemidir.. Süreç aşağıdaki adımları içerir:
- Yüzey hazırlığı: Yapışmanın iyileştirilmesi için borunun iç yüzeyi temizlenir ve pürüzlendirilir.
- Püskürtme: Astar malzemesi eritilip yüzeye püskürtme gibi teknikler kullanılarak püskürtülür. plazma püskürtme ya yüksek hızlı oksijen yakıtı (HVOF) Püskürtme.
- Püskürtme Sonrası Tedavi: İstenilen yüzey kalitesini ve mekanik özellikleri elde etmek için boru ısıl işleme veya işleme tabi tutulabilir..
tablo 2: Bimetalik Kompozit Borular için Yaygın Kaplama ve Kaplama Teknikleri
Tekniği | Astar Malzemesi | Süreç Açıklaması | Avantajları | Uygulamalar |
---|---|---|---|---|
Kaynaklı Kaplama | Krom Karbür, Tungsten Karbür | Sert alaşım kaynak teknikleri kullanılarak iç yüzeye biriktirilir | Güçlü bağ, yüksek erozyon direnci | Petrol & Gaz, Madencilik, çamur taşıma |
Savurma döküm | Seramik, Metal Alaşımları | Erimiş malzeme merkezkaç kuvveti kullanılarak iç yüzeye dökülür | Üniforma astar, iyi yapışma | Yüksek sıcaklık, yüksek aşınmalı ortamlar |
Termal Püskürtme | Seramik, Sert Alaşımlar | Astar malzemesi eritilip yüzeye püskürtülür | Çok yönlü, çok çeşitli malzemeleri uygulayabilir | Kimyasal işleme, yüksek aşınma uygulamaları |
Erozyona Dirençli Kaplamaların Performans Değerlendirmesi
Test Yöntemleri
Bimetalik kompozit borulardaki erozyona dayanıklı kaplamaların performansı, gerçek dünyadaki aşındırıcı koşulları simüle etmek için tasarlanmış bir dizi testle değerlendirilir.. Yaygın test yöntemleri şunları içerir::
1. Erozyon Testi
Erozyon testi, BORU KAPLI aşındırıcı parçacıkların akışına, kum veya bulamaç gibi, yüksek hızda. Test, zaman içinde astardan kaynaklanan malzeme kaybının oranını ölçmek için tasarlanmıştır.. Erozyon testi sırasında ölçülen temel parametreler şunları içerir::
- Erozyon oranı: Aşındırıcı parçacıkların etkisi nedeniyle malzemenin astardan ayrılma hızı.
- kilo kaybı: Belirli bir test süresi sonrasında kaplama malzemesinin toplam ağırlık kaybı.
- yüzey pürüzlülüğü: Erozyona bağlı olarak kaplama malzemesinin yüzey pürüzlülüğünde meydana gelen değişiklikler.
2. Sertlik Testi
Sertlik testi, astar malzemesinin girinti ve aşınmaya karşı direncini değerlendirmek için kullanılır.. Yaygın sertlik testleri şunları içerir: Vickers sertlik testi ve Rockwell sertlik testi. Daha yüksek sertlik değerleri aşınma ve erozyona karşı daha iyi direnç gösterir.
3. Yapışma Testi
Yapışma testi, ana metal ile kaplama malzemesi arasındaki bağın gücünü değerlendirmek için kullanılır.. Zayıf yapışma, astarın ayrılmasına veya dökülmesine yol açabilir, etkinliğini azaltmak. Yaygın yapışma testleri şunları içerir: çekme testleri ve kesme testleri.
tablo 3: Erozyona Dirençli Astarlar için Performans Test Yöntemleri
Test | Amaç | Ölçülen Parametreler | Önem |
---|---|---|---|
Erozyon Testi | Erozyon direncini değerlendirin | Erozyon oranı, kilo kaybı, yüzey pürüzlülüğü | Aşındırıcı ortamlarda astarın dayanıklılığını belirler |
Sertlik Testi | Malzeme sertliğini ölçün | Vickers Sertliği, Rockwell sertliği | Daha yüksek sertlik daha iyi aşınma direncini gösterir |
Yapışma Testi | Bağ gücünü değerlendirin | Çekme gücü, kesme mukavemeti | Servis sırasında astarın sağlam kalmasını sağlar |
Performans Sonuçları
Erozyon Direnci
Bimetalik kompozit boruların erozyon testi, sert alaşım veya seramik kaplamaların kullanılmasının borunun erozyon direncini önemli ölçüde artırdığını göstermiştir.. Tipik bir erozyon testinde, Krom karbür veya alümina ile kaplanmış borular, 50-70% daha düşük astarsız karbon çelik borulardan daha. Sonuçlar, erozyona dayanıklı kaplamaların kullanılmasının borunun çalışma ömrünü birkaç yıl uzatabileceğini göstermektedir., son derece aşındırıcı ortamlarda bile.
Sertlik
Astar malzemelerinin sertlik testi, seramik astarların, alümina ve silisyum karbür gibi, en yüksek sertlik değerlerine sahip, arasında değişen 1500 Hedef 2000 YG (Vickers Sertliği). Sert alaşımlı astarlar, krom karbür gibi, aralığında sertlik değerlerine sahip olmuştur. 600 Hedef 800 YG, Astarsız karbon çeliğinin sertliği 150 Hedef 200 YG. Astar malzemelerinin daha yüksek sertliği, geliştirilmiş erozyon direnciyle ilişkilidir.
Yapışma
Astarlı boruların yapışma testi, hem kaynaklı kaplama kaplamasının hem de santrifüj döküm tekniklerinin, ana metal ile astar malzemesi arasında güçlü bağlar ürettiğini gösterdi.. Çekme testleri, astarın yapışma mukavemetinin ana metalin çekme mukavemetinden daha yüksek olduğunu gösterdi, normal çalışma koşulları altında astarın katmanlarına ayrılmayacağını veya parçalanmayacağını belirtir.
Çözüm
Erozyona dayanıklı astarlara sahip bimetalik kompozit borular, aşındırıcı ortamlarla karşı karşıya kalan endüstriler için oldukça etkili bir çözüm sunar. Metalik dış katmanın yapısal gücünü sert alaşım veya seramik kaplamanın üstün aşınma direnciyle birleştirerek, bu borular boru sistemlerinin ömrünü önemli ölçüde uzatabilir, bakım maliyetlerini azaltmak, ve operasyonel verimliliği artırın. Bu boruların hazırlanması, kaynakla kaplama gibi ileri teknikleri içerir., Savurma döküm, ve termal püskürtme, her biri uygulamaya bağlı olarak benzersiz avantajlar sunar.
Performans değerlendirmeleri, erozyon testi dahil, Sertlik Testi, ve yapışma testi, aşındırıcı aşınmaya karşı korumada erozyona dayanıklı astarların etkinliğini kanıtlamıştır. Bu testlerin sonuçları bimetalik kompozit boruların aşındırıcı ortamların zorlu koşullarına dayanabildiğini göstermektedir., onları petrol ve gaz gibi endüstriler için ideal bir seçim haline getiriyor, Madencilik, ve kimyasal işleme.
SSS
Bimetalik kompozit borular nelerdir?
Bimetalik kompozit borular iki farklı malzemeden oluşur: bir baz metal (tipik olarak çelik) yapısal dayanıklılık ve erozyona dayanıklı kaplama malzemesi için, sert alaşım veya seramik gibi, aşınmaya karşı korumak için.
Bimetalik kompozit borularda astar olarak hangi malzemeler kullanılır??
Yaygın astar malzemeleri sert alaşımları içerir (örneğin, Krom Karbür, Tungsten Karbür) ve seramik (örneğin, alümina, silisyum karbür), üstün erozyon direnci sunan.
Bimetalik kompozit borular nasıl hazırlanır??
Bimetalik kompozit borular kaynak kaplama kaplama gibi teknikler kullanılarak hazırlanır, Savurma döküm, ve termal püskürtme, Ana metal ile kaplama malzemesi arasında güçlü bir bağ sağlayan.
Erozyona dayanıklı astarların performansını değerlendirmek için hangi testler kullanılır??
Performans değerlendirmesi erozyon testini içerir, Sertlik Testi, ve dayanıklılığı değerlendirmek için yapışma testleri, aşınma direnci, ve astar malzemesinin bağlanma mukavemeti.
Aşındırıcı ortamlarda bimetalik kompozit boru kullanmanın faydaları nelerdir??
Bimetalik kompozit borular daha uzun kullanım ömrü sunar, Azalan Bakım Maliyetleri, ve erozyona bağlı aşınma ve yıpranmaya karşı koruma sağlayarak operasyonel verimliliğin artırılması.
Olmalısın giriş Yorum yazmak için.