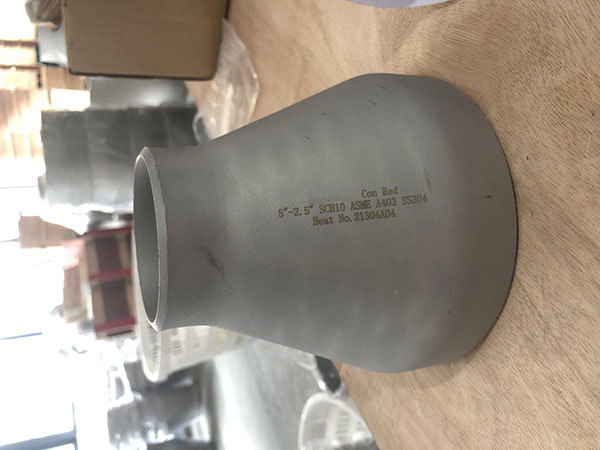
Stainless Steel Reducer: ASTM A403 WP Grades
Introduction
Stainless steel reducers are vital components in piping systems, designed to connect pipes of different diameters while maintaining a smooth flow of fluids or gases. They come in two primary types: concentric reducers, which have a common centerline, and eccentric reducers, which have an offset centerline. This document provides a detailed introduction and in-depth analysis of stainless steel reducers, specifically those compliant with ASTM A403 WP grades, including 304, 304H, 309, 310, 316, 316L, 317L, 321, 347, and 904L.
ASTM A403 WP Grades Overview
ASTM A403 WP304 and WP304H
- WP304: The standard 18/8 stainless steel (18% chromium, 8% nickel) known for its excellent corrosion resistance and formability.
- WP304H: A high-carbon version of WP304, providing better high-temperature strength.
ASTM A403 WP309
- A high-chromium, high-nickel stainless steel offering superior oxidation resistance and strength at elevated temperatures.
ASTM A403 WP310
- Known for its high temperature and corrosion resistance, WP310 is ideal for high-temperature service applications.
ASTM A403 WP316 and WP316L
- WP316: Enhanced with molybdenum for better corrosion resistance, especially against chlorides and other industrial solvents.
- WP316L: A low-carbon version of WP316, providing excellent weldability and minimizing the risk of carbide precipitation during welding.
ASTM A403 WP317L
- Similar to WP316 but with higher molybdenum content, offering superior resistance to pitting and crevice corrosion.
ASTM A403 WP321
- Titanium-stabilized austenitic stainless steel providing excellent resistance to intergranular corrosion after exposure to temperatures in the chromium carbide precipitation range.
ASTM A403 WP347
- Columbium-stabilized stainless steel with excellent resistance to intergranular corrosion, suitable for high-temperature applications.
ASTM A403 WP904L
- A high-alloy austenitic stainless steel with excellent corrosion resistance, particularly against sulfuric acid, and improved mechanical properties.
Detailed Introduction
Composition and Properties
Grade | Cr (%) | Ni (%) | Mo (%) | Other Elements | Key Properties |
---|---|---|---|---|---|
WP304 | 18-20 | 8-10.5 | – | – | Corrosion resistance, formability |
WP304H | 18-20 | 8-10.5 | – | High C | High-temperature strength |
WP309 | 22-24 | 12-15 | – | – | Oxidation resistance, high strength |
WP310 | 24-26 | 19-22 | – | – | High-temperature resilience |
WP316 | 16-18 | 10-14 | 2-3 | – | Chloride resistance, durability |
WP316L | 16-18 | 10-14 | 2-3 | Low C | Weldability, corrosion resistance |
WP317L | 18-20 | 11-15 | 3-4 | Low C | Pitting and crevice corrosion resistance |
WP321 | 17-19 | 9-12 | – | Ti | Intergranular corrosion resistance |
WP347 | 17-19 | 9-12 | – | Nb | Intergranular corrosion resistance |
WP904L | 19-23 | 23-28 | 4-5 | Cu, Mn, Si | Sulfuric acid resistance, toughness |
Mechanical Properties
Grade | Tensile Strength (MPa) | Yield Strength (MPa) | Elongation (%) | Hardness (HB) |
---|---|---|---|---|
WP304 | 515 | 205 | 40 | 201 |
WP304H | 515 | 205 | 40 | 201 |
WP309 | 620 | 310 | 30 | 220 |
WP310 | 620 | 310 | 30 | 220 |
WP316 | 515 | 205 | 40 | 217 |
WP316L | 485 | 170 | 40 | 217 |
WP317L | 515 | 205 | 40 | 217 |
WP321 | 515 | 205 | 40 | 217 |
WP347 | 515 | 205 | 40 | 201 |
WP904L | 490 | 220 | 35 | 192 |
In-Depth Analysis
Corrosion Resistance
- WP304 and WP304H: Excellent resistance to a wide range of atmospheric environments and many corrosive media.
- WP309 and WP310: Superior oxidation resistance, suitable for high-temperature environments.
- WP316 and WP316L: Enhanced resistance to chlorides and industrial solvents, making them ideal for marine and chemical environments.
- WP317L: Offers even better resistance to pitting and crevice corrosion than WP316.
- WP321 and WP347: Both grades resist intergranular corrosion, with WP321 stabilized by titanium and WP347 by columbium.
- WP904L: Provides exceptional resistance to sulfuric acid and other highly corrosive environments.
High-Temperature Performance
- WP304H, WP309, WP310: These grades are specifically designed for high-temperature applications, with WP304H offering improved high-temperature strength due to higher carbon content.
- WP321 and WP347: Both grades perform well at elevated temperatures, with stabilization elements helping to prevent carbide precipitation.
Weldability and Fabrication
- WP304 and WP316 Series: Excellent weldability and formability, suitable for a wide range of applications.
- WP316L and WP317L: Low-carbon versions offer superior weldability by minimizing the risk of carbide precipitation.
- WP321 and WP347: Stabilized grades prevent intergranular corrosion after welding, making them suitable for high-temperature, welded applications.
- WP904L: Though more challenging to weld due to its high alloy content, it can be successfully welded using appropriate techniques.
Applications
- WP304 and WP304H: Commonly used in food processing, chemical, and petrochemical industries.
- WP309 and WP310: Ideal for furnace parts, heat exchangers, and other high-temperature applications.
- WP316 and WP316L: Widely used in marine environments, chemical processing, and pharmaceutical equipment.
- WP317L: Suitable for chemical processing and petrochemical industries where higher corrosion resistance is needed.
- WP321 and WP347: Used in high-temperature chemical and petrochemical processing, power generation, and aerospace applications.
- WP904L: Found in chemical processing, particularly where sulfuric acid is present, as well as in seawater cooling devices and oil refinery components.
Manufacturing Processes
Forming and Shaping
-
Hot Forming: Involves heating the material to a high temperature and then shaping it using presses or rollers. This process improves the material’s ductility and reduces the risk of cracking.
-
Cold Forming: Performed at room temperature, providing better surface finish and dimensional accuracy. However, it requires more force and may induce work hardening.
Welding
-
TIG (Tungsten Inert Gas) Welding: Provides high-quality welds with excellent control over the heat input, suitable for thin-walled components.
-
MIG (Metal Inert Gas) Welding: Faster than TIG welding, suitable for thicker materials and production environments.
Heat Treatment
- Solution Annealing: Involves heating the material to a high temperature and then rapidly cooling it to dissolve any precipitated carbides, restoring its corrosion resistance.
Surface Treatment
- Pickling and Passivation: Removes surface contaminants and enhances the natural protective oxide layer of stainless steel, improving its corrosion resistance.
Quality Control
-
Non-Destructive Testing (NDT): Techniques such as radiographic, ultrasonic, and dye penetrant testing ensure the integrity and quality of the welds and materials.
-
Dimensional Inspection: Ensures that the reducers meet the required specifications and tolerances.
Market Trends
Demand Drivers
- Infrastructure Development: Increasing investments in infrastructure projects globally drive the demand for reliable piping systems.
- Oil and Gas Industry: The ongoing exploration and production activities necessitate high-performance materials that can withstand harsh environments.
- Chemical Processing: Growing chemical processing industries require materials with excellent corrosion resistance and high-temperature performance.
Regional Analysis
- North America: Significant demand due to advanced infrastructure, stringent regulations, and a robust oil and gas industry.
- Europe: Focus on sustainable development and stringent environmental regulations drive the market.
- Asia-Pacific: Rapid industrialization and urbanization contribute to the growing demand for stainless steel reducers.
Challenges
- Raw Material Costs: Fluctuations in the prices of raw materials like nickel, chromium, and molybdenum can impact production costs.
- Technological Advancements: Continuous innovation is required to meet evolving industry standards and improve material performance.
Conclusion
Stainless steel reducers compliant with ASTM A403 WP grades, including 304, 304H, 309, 310, 316, 316L, 317L, 321, 347, and 904L, offer a wide range of properties suitable for various applications. Their excellent corrosion resistance, high-temperature performance, and weldability make them indispensable in industries such as chemical processing, oil and gas, and infrastructure development. Continuous advancements in material science and manufacturing processes ensure that these components meet the ever-evolving demands of modern engineering applications.
References
- ASTM A403/A403M: Standard Specification for Wrought Austenitic Stainless Steel Piping Fittings.
- ASM International: Handbook of Stainless Steels.
- NACE International: Corrosion Basics: An Introduction.
- Technical Literature: Material properties and manufacturing processes for stainless steel reducers.
- Market Reports: Trends and forecasts for the stainless steel industry.
You must be logged in to post a comment.