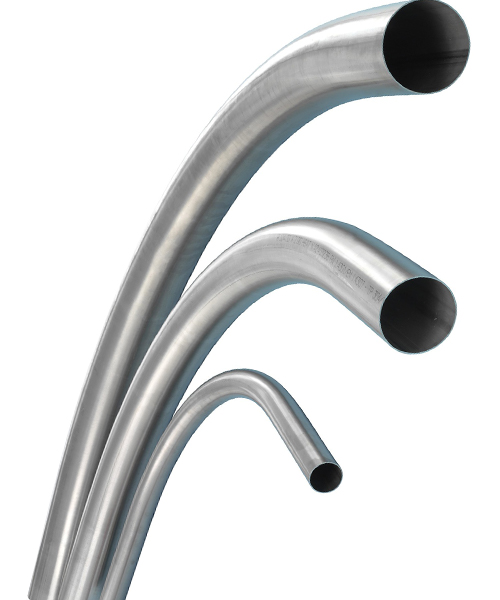
Introduction
As energy and petrochemical infrastructure expands globally, efficient flow routing through varied terrains requires flexible pipeline configuration. A crucial component enabling re-direction and optimization of routes are steel buttwelding induction bends. Induction bending allows full-radius weld joints between pipe sections maintaining through-bore capacity for unhindered transportation. This paper examines the manufacturing process, performance advantages, standards, and applications of induction bending facilitating transportation and distribution system construction.
Design Considerations
Proper bend selection depends on service parameters like contents, pressures up to Class 600, and operational temperatures from cryogenic to 600°F. Key factors include:
Bend Radius: Short vs Long radius designs depend on required angle changes per location; radii typically 5-20x pipe diameter.
Bend Leg Length: Varies based on fitting within space allotments; minimums are 1.5x diameter or per code.
Angle of Deflection: Standard mitred designs provide 22.5-45° direction changes for intersecting pipelines.
Pipe Dimensions: Schedule 5-XXXL wall thicknesses from 0.219-1.315″ suit a range of gas, petrochemical and water applications.
Codes like ASME B31.4/8 provide construction guidelines to ensure bends achieve specified designs and pressures for lifespan. Proper specification precludes over-stressing during and after construction.
Manufacturing Process
Fabricating standardized and custom bends requires precise equipment to form consistent geometries meeting tolerances. The process entails:
Beveling and Face Preparation: CNC machines create consistent 35-37.5° bevels on pipe ends for full-penetration welds.
Fixturing: A bending frame positions pipe ends at the programmed bend angle and leg length with hydraulic clamps.
Heating: Powerful induction coils rapidly heat the steel interface to 1900-2100°F plasticizing range without external flames or filler rods.
Forming: Hydraulic presses synchronize to fold the molten steel to the die radius, consolidating the weld.
Cooling: Temperature controlled water sprays quench the joint, locking in the desired microstructure.
Non-Destructive Examination
Rigorous inspection qualifies bends for reliable long-term service. Techniques such as:
Visual Exams: Checks for cracks, laps or surface imperfections indicating faults.
Dye-Penetrant Tests: Detects surface-connected discontinuities down to 1/32″.
Radiography: X-ray or gamma-ray imaging identifies internal flaws unsuitable for welding.
Ultrasonics: Measures weld penetration depth and homogeneity per API 1104.
Only bends passing all tests to codes like ASME Section 9 are approved for distribution to job sites.
Installation and Testing
At locations, bends require proper supports according to stress analyses and allowances for thermal growth. Connections utilize internal seal gaskets and self-aligning follower flanges or slip-type flanges for ease-of-installation at any deflection angle. Further testing includes:
Hydrotesting: Pressurizes pipelines to 1.5x MAOP for 8 hours minimum leakage testing.
In-Line Inspection: Smart pigs validate full-bore integrity for cleaning/sizing application.
Cathodic Protection: Electrical anodes and coatings prevent external corrosion.
Thus qualified, induction bends join pipelines dependably despite environmental and operational stresses.
Performance Benefits
Advantages include reduced construction schedules via simultaneous preparation and bending of joints at a central factory. Full-size flow bores maintain friction losses. Compact designs optimize usage of congested right-of-ways. Resilient metallurgy absorbs terrain movement and seismic loads. Overall, reliable induction bending enables cost-effective construction of critical energy distribution networks.
Future Applications
Ongoing applications involve renewable natural gas and hydrogen injection requiring conversion of existing gas systems. Metrics are established for tracking carbon savings from infrastructure modernization facilitated by induction bending technology. As energy transitions accelerate, steady bending innovations will continue streamlining flow routing sustainably.
Conclusion
Steel buttwelding induction bending establishes efficient, standardized joint production meeting stringent code qualification. Proper design, manufacturing and installation provide structural integrity ensuring unimpeded flow throughout asset service lives. Induction bends thereby enable construction and optimization of large-scale transportation and distribution pipelines transporting vital resources nationwide and beyond.
You must be logged in to post a comment.