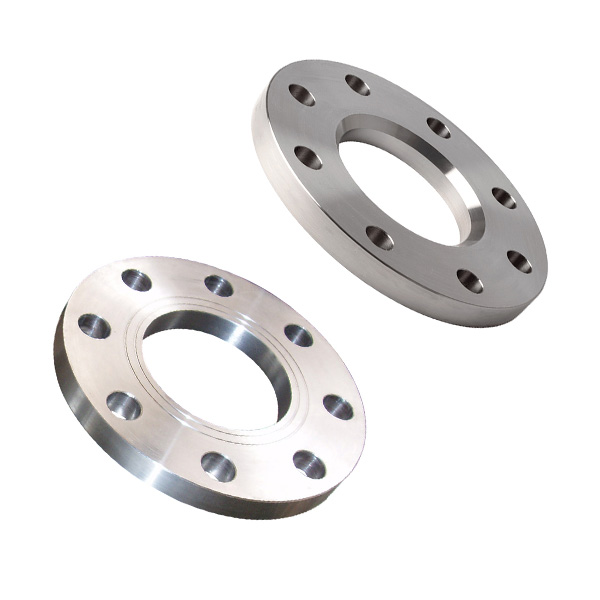
Introduction
Flanges are essential pipeline components used to join pipe sections while permitting easy disassembly. The flat face welding flange is one commonly used style, finding frequent application across industries that transfer fluids via piping networks. As a primary pressure boundary element, flanges must exhibit robust sealing abilities to ensure leakproof joints even under challenging service conditions. This paper aims to provide a detailed overview of the sealing principle and key characteristics that govern the performance of flat welding flanges. By understanding the mechanics underlying sealing, the flange style can be rightly specified and installed to deliver long-term structural integrity.
Sealing Principle
Achieving an effective seal within the flange-pipe assembly relies on the combined actions of compressive loading, intimate surface contact, and plastic deformation. When bolting a flange pair together, the bolt tightening produces outward radial forces that pull the flat faces firmly against one another. The conjoined faces then undergo limited elastic and plastic deformation depending on material properties and imposed loads. However, microscopic surface imperfections remain and if left unmodified would permit leakage.
A critical sealing element is the ‘gasket’, usually a ring or washer cut from a flexible but compressible material like elastomers, graphite, or metals. Installed between the flange faces, tightening causes the gasket to squeeze and flow into voids or crevices along the sealing surfaces. Importantly, it deforms plastically and work-hardens rather than simply compressing elastically. This ‘gasket flow’ physically blocks fluid passageways through any irregularities by wedging tightly into every microscopic valley. When loading removes, residual clamping forces plus the hardened filler sustains sealing integrity under changing pressures and temperatures.
Material Selection
Flange component materials directly influence the robustness and lifespan of a given sealing design. Common materials are:
-
Flange Body: Carbon steel (ASTM A105), low alloy steel, duplex/super duplex stainless for corrosion resistance. Key is adequate toughness over service life.
-
Bolting: Standard carbon steel bolts suffice for many non-corrosive duties. For offshore/sour services, alloy bolts with strength/corrosion resistance like A193 B7, ASTM A490 are used.
-Gasket: Softer cloth-inserted rubber for low pressures under 300 psi, spirally wound asbestos fiber for higher pressures up to 1500psi, flexible graphite or PTFE sheets for >=1500psi including high-temperature applications.
Material combinations must avoid incompatibilities like galvanic corrosion and consider gasket compressibility with pressures. Proper specification ensures structural integrity and sealing performance over decades of service.
Flange Face Finishes
Face finish directly impacts the sealing contact area and gasket flow characteristics:
-
Machined Face (MF): Standard 125-250 Ra microinch surface with sharp edges for best metal-metal sealing. However, difficult to machine large flanges.
-
Welded Face (WF): As-welded surface has higher roughness 80-160 Ra microinch but rounded edges ease gasket installation. Slightly lower sealing potential than MF.
-
Blind Finished Face (BFF): Special machining hollows the weld reinforcement leaving an MF-like surface. Provides best of both MF sealing and eased WF installation benefits. More expensive than other finishes.
Higher surface roughness increases metal contact area for sealing but should be uniform and controlled. Edge sharpness also influences initial gasket compression and vulnerability to cuts during assembly/disassembly cycles. Proper finish selection balances performance and economy.
Flange Styles and Configurations
Along with finished faces, the external flange morphology impacts piping flexibility, joint access, and long-term stress distribution:
-
Weld Neck (WN): Integral tubular neck welded into pipe creates strongest joint. However, less installation space inside flange compared to slip-on types.
-
Slip-On (SO): Bolted directly over pipe end. More room inside but small neck creates local stress risers. Often used with companion rings for piping flexibility.
-
Lap Joint (LJ): Bolted over two abutting pipe ends. Similar in dimensions to slip-on but higher stresses develop at pipe/flange intersection.
-
Socket Weld (SW): Integral female socket welded into pipe end for bolting flat face cap. Provides most internal clearance and weakest joint strength.
Proper flange selection considers joint stresses, required accessibility, pipeline loads, fabrication/installation constraints, and whole-of-life integrity. Standardized bore diameters ease inventory.
Flange Installation and Integrity
Correct installation and assembly procedures prove crucial for dependable long-term flange sealing performance:
-
Clean flange faces and apply anti-seize compound to sliding bolt surfaces prevents galling.
-
Center and properly compress gasket between faces without twists or rolls using lubricants if needed.
-
Hand-tighten bolts in a crossing pattern then repeatedly torque bolts to specification in stages while checking uniform compression. Avoid over/under tightening.
-
Perform final leak test on joint before applying external finishes and coatings. Check periodically during operation.
-
Consider bellows inserts, protectors or restraints for vibrational or seismic services mitigating seating/unseating stresses.
-
Inspect flanges regularly as part of preventative maintenance, replacing gaskets, bolts or flanges showing signs of damage, corrosion or wear.
Conclusion
Understanding the sealing principles and characteristics of flat welding flanges enables their reliable application for transferring fluids via piping networks. Material selection, surface finish, flange configuration and installation procedures all directly affect long-term joint integrity. When properly specified, fabricated and maintained, flanges deliver robust pressure sealing even under onerous service conditions supporting vital industries. Advances in metallurgy, non-destructive testing and inspection also safeguard flange performance well into the future.
You must be logged in to post a comment.