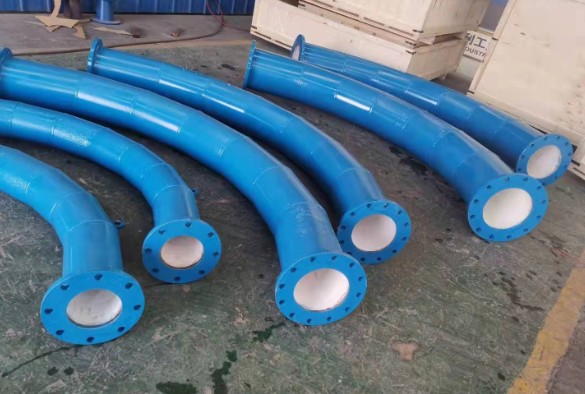
Cotovelo forrado de cerâmica: Análise abrangente
Cotovelos revestidos de cerâmica são componentes críticos em sistemas de tubulação industrial, projetado para lidar com abrasivo, corrosivo, e materiais de alta temperatura. Esses cotovelos combinam a durabilidade do aço com o desgaste excepcional e a resistência à corrosão dos revestimentos de cerâmica, tornando -os indispensáveis em indústrias como geração de energia, Mineração, metalurgia, e processamento químico. Este documento fornece uma análise aprofundada dos cotovelos forrados de cerâmica, incluindo uma tabela de parâmetros, Composição do material, Propriedades mecânicas, Resistência ao desgaste, ângulos de flexão, e uma discussão detalhada de seu desempenho e aplicativos.
Tabela de parâmetros
Parâmetro | Descrição | Valores tipicos |
---|---|---|
Material do tubo externo | Material base do cotovelo | Aço de carbono (v.g., 20# Aço sem costura), Aço inoxidável |
Material de revestimento de cerâmica | Material de revestimento interno | Alumina (Al₂O₃, ≥90%), A alumina endurecida de zircônia (ZTA) |
Diâmetro do tubo | Diâmetro interno do tubo | 0.5 polegadas para 24 polegadas (personalizável) |
Espessura de cerâmica | Espessura do forro de cerâmica | 6 mm – 25 mm |
Ângulo de dobra | Mudança de ângulo de direção | 22.5°, 45°, 90°, 180° (ângulos personalizados disponíveis) |
Bend Raio | Raio de curvatura | 1.5d – 5d (D = diâmetro do tubo) |
Temperatura de operação | Resistência máxima à temperatura | -50° C a 900 ° C. (a longo prazo), até 2000 ° C. (curto prazo) |
Resistência à pressão | Força de argola | 300 – 500 MPa |
Resistência ao desgaste | Em relação ao aço carbono | 15 – 20 vezes maior |
Microheridade | Dureza do forro de cerâmica | Alta tensão 1000 – 1600 |
Densidade | Densidade do revestimento de cerâmica | 3.62 g/cm³ (Alumina) |
vida de serviço | Vida útil esperada em condições abrasivas | 5 – 20 anos (dependendo da aplicação) |
Composição do material
Os cotovelos revestidos de cerâmica consistem em duas camadas de material primário: o tubo de aço externo e o forro de cerâmica interna. O tubo externo é normalmente feito de aço carbono (v.g., 20# Aço sem costura) ou aço inoxidável, fornecendo integridade estrutural e facilidade de soldagem ou flange. O forro de cerâmica, geralmente composto de alumina de alta pureza (Al₂O₃) ou alumina endurecida de zircônia (ZTA), está ligado à superfície interna usando adesivos resistentes à temperatura ou técnicas de intertravamento mecânico.
Material do tubo externo
O tubo externo serve como a espinha dorsal do cotovelo. O aço carbono é comumente usado devido à sua relação custo-benefício, força elevada, e soldabilidade. Para aplicações envolvendo ambientes corrosivos, aço inoxidável pode ser preferido para aumentar a resistência à corrosão. A camada de aço garante que o cotovelo possa suportar tensões mecânicas, como pressão e impacto, enquanto facilitando a integração nos sistemas de tubulação existentes.
Material de revestimento de cerâmica
O forro cerâmico é a chave para o desempenho excepcional do cotovelo. Alumina, com um conteúdo de Al₂o₃ de 90% ou superior, é o material mais amplamente usado devido à sua alta dureza, Resistência ao desgaste, e estabilidade térmica. A alumina endurecida de zircônia (ZTA) é uma variante avançada que oferece melhor resistência e resistência ao impacto, tornando -o adequado para sistemas dinâmicos com alto choque mecânico. A camada de cerâmica é normalmente aplicada como ladrilhos, mangas, ou um revestimento monolítico, dependendo do processo de fabricação.
A estrutura de grãos finos do material cerâmico e a alta densidade contribuem para sua durabilidade. por exemplo, Cerâmica de alumina exibe uma dureza semelhante a um diamante e força mecânica superior, tornando-os ideais para aplicações exigentes. A escolha do material de cerâmica pode ser adaptada a requisitos operacionais específicos, como extrema abrasão ou exposição química.
Propriedades mecânicas
As propriedades mecânicas dos cotovelos revestidos de cerâmica são um composto da camada externa de aço e do forro interno de cerâmica. Essas propriedades determinam a capacidade do cotovelo de suportar a pressão, Impacto, e choque térmico, Garantir desempenho confiável em ambientes severos.
força
A força do aro dos cotovelos forrados de cerâmica, que mede a resistência à pressão radial, normalmente varia de 300 Para 500 MPa. Esta força é derivada principalmente da camada externa de aço, que fornece suporte estrutural. O forro de cerâmica, enquanto quebradiço, contribui para a integridade geral resistindo à degradação da superfície e mantendo a forma do cotovelo em condições abrasivas.
Resistência Flexural, ou força de flexão, é uma propriedade crítica para o forro de cerâmica. Cerâmica de alumina exibe alta resistência à flexão, frequentemente testado por meio de testes de flexão de 3 ou 4 pontos. Os valores podem exceder 300 MPa, Dependendo do tamanho do grão, porosidade, e fabricação qualidade. no entanto, A fragilidade da cerâmica significa que ele depende da camada de aço para absorver tensões de flexão sem rachaduras.
Dureza
A microheridade do forro de cerâmica, medido na escala de Vickers, varia de hv 1000 Para 1600 Para materiais à base de alumina. Essa dureza é significativamente maior que a do aço carbono (aproximadamente hv 150-200 Depois de ter a queima) ou mesmo carboneto de tungstênio (Alta tensão 1200-1500), tornando a camada cerâmica excepcionalmente resistente a arranhar e desgaste. A alta dureza garante que o cotovelo possa lidar com materiais abrasivos como o pó de carvão, cinzas, ou pasta de minério sem danos significativos na superfície.
Resistência à resistência e impacto
Enquanto a cerâmica de alumina é inerentemente quebradiça, Sua resistência pode ser aprimorada usando o ZTA ou otimizando a ligação com a camada de aço. O tubo externo de aço fornece excelente resistência ao impacto, absorvendo choques mecânicos que, de outra forma, poderiam fraturar o forro de cerâmica. Na prática, cotovelos revestidos de cerâmica demonstraram resiliência em aplicações envolvendo impactos de partículas de alta velocidade, como sistemas de transporte pneumático.
Resistência ao choque térmico
Os cotovelos revestidos de cerâmica podem operar em temperaturas que variam de -50 ° C a 900 ° C por períodos prolongados, com resistência a curto prazo até 2000 ° C. O coeficiente de baixa expansão térmica do revestimento de cerâmica minimiza as rachaduras sob mudanças rápidas de temperatura, Enquanto a camada de aço fornece estabilidade adicional. Essa resistência ao choque térmico é crucial em indústrias como a geração de energia, onde os oleodutos podem experimentar temperaturas flutuantes.
Resistência ao desgaste
Resistência ao desgaste é a característica definidora dos cotovelos revestidos de cerâmica, diferenciando -os dos acessórios de aço tradicional ou de ferro fundido. A capacidade do revestimento de cerâmica de suportar a abrasão e a erosão estende a vida de serviço do cotovelo por 15 Para 20 tempos comparados aos cotovelos de aço carbono sem revestimento, reduzindo os custos de manutenção e tempo de inatividade.
Mecanismo de resistência ao desgaste
A alta dureza e superfície lisa do revestimento cerâmico minimizam a perda de material devido ao desgaste abrasivo. Em aplicações envolvendo lascas ou pós de alta velocidade (v.g., cinzas de carvão, calcário, ou areia), A camada cerâmica resiste à erosão, reduzindo o atrito e prevenindo a incorporação de partículas. A resistência ao desgaste é quantificada comparando o desempenho do revestimento de cerâmica com o de aço carbono, com estudos mostrando um aumento de vida útil 20 tempos em condições abrasivas.
O fator de baixo atrito da cerâmica em ângulos de baixo impacto aumenta ainda mais a resistência ao desgaste, reduzindo o impacto abrasivo das partículas. Esta propriedade é particularmente benéfica nos cotovelos, onde a direção do fluxo muda aumenta a turbulência e o desgaste. A superfície interna lisa também impede o acúmulo de material, garantir taxas de fluxo consistentes e reduzir o risco de bloqueios.
Análise Comparativa
Comparado a outros materiais resistentes ao desgaste, como basalto fundido ou aço de liga, Finios de cerâmica oferecem desempenho superior. Basalto fundido, enquanto durável, tem menor resistência ao desgaste e é propenso a rachaduras sob impactos de alta velocidade. Liga de aço, com uma dureza superficial de aproximadamente 60 HRC, veste mais rápido que a cerâmica (80+ HRC equivalente). Em aplicativos do mundo real, como usinas a carvão, Os cotovelos revestidos de cerâmica superaram os cotovelos de aço de paredes grossas por um fator de cinco ou mais.
vida de serviço
A vida útil de um cotovelo forrado de cerâmica depende da gravidade do aplicativo. Em sistemas de transporte pneumático para cinzas volantes ou cimento, Onde a abrasão é intensa, o forro de cerâmica pode durar 5 Para 10 anos, comparado com 1-2 anos para cotovelos de aço. Em condições menos abrasivas, como processamento químico, A vida útil pode exceder 20 anos. A taxa média de desgaste da camada de cerâmica é aproximadamente 0.5-1 mm por ano, Significado a 6 MM Linering poderia durar 5 anos em ambientes exigentes.
ângulos de flexão
Cotovelos revestidos de cerâmica estão disponíveis em vários ângulos de flexão para acomodar diferentes layouts de tubulação. O ângulo determina o grau de mudança de direção, afetando a dinâmica de fluxo e padrões de desgaste dentro do cotovelo.
Ângulos de flexão padrão
Os ângulos de flexão mais comuns são 22,5 °, 45°, 90°, e 180°, Embora os ângulos personalizados possam ser fabricados para atender aos requisitos específicos. Esses ângulos correspondem ao padrão encaixe de tubulação desenhos:
- 22.5° Cotovelo: Usado para pequenos ajustes direcionais em sistemas de tubulação.
- 45° Cotovelo: Fornece uma mudança moderada de direção, Reduzindo a turbulência em comparação com os cotovelos de 90 °.
- 90° Cotovelo: O ângulo mais amplamente usado para turnos perpendiculares, comum em layouts apertados.
- 180° Cotovelo: Uma curva de retorno para reverter a direção do fluxo, frequentemente usado em trocadores de calor ou sistemas compactos.
Raio de curvatura
O raio de curvagem, normalmente expresso como um múltiplo do diâmetro do tubo (d), varia de 1,5d a 5d. Um raio maior (v.g., 5d) resulta em uma curva mais suave, redução da resistência ao fluxo e concentração de desgaste na curva. Cotovelos curtos-radius (1.5d) são mais compactos, mas experimentam um desgaste mais alto devido a curvas mais nítidas. A escolha do raio depende de restrições de espaço, Requisitos de fluxo, e desgastar considerações.
Impacto no desempenho
O ângulo de flexão e o raio influenciam significativamente o desempenho do cotovelo. Ângulos mais nítidos (v.g., 90°) e raios menores aumentam a turbulência e o impacto das partículas, desgaste acelerando na curva externa. Forros de cerâmica atenuam isso, fornecendo um difícil, superfície lisa que desvia partículas abrasivas. Em contraste, raios maiores e ângulos menores distribuem desgaste de maneira mais uniforme, melhorando a longevidade.
Análise detalhada
Os cotovelos revestidos de cerâmica representam uma fusão de materiais avançados e projeto de engenharia, adaptado para enfrentar os desafios do transporte de material abrasivo e corrosivo. Esta seção explora seus processos de fabricação, Aplicações, Vantagens, Limitações, e avanços recentes, Fornecendo uma compreensão holística de seu papel na indústria moderna.
processos de fabricação
Os cotovelos revestidos de cerâmica são produzidos usando várias técnicas, cada um influenciando seu desempenho e custo:
- fundição centrífuga: A alumina fundida é fundida dentro de um tubo de aço sob força centrífuga, formando um denso, camada de cerâmica uniforme. Este método garante alta resistência à ligação e é ideal para cotovelos de grande diâmetro.
- Forro de telha: As telhas cerâmicas pré-formadas são aderidas à superfície interna do tubo de aço usando adesivos de alta temperatura ou intertravamento mecânico. Essa abordagem permite controle preciso sobre a espessura do revestimento e é adequado para formas complexas.
- Forro de manga: Uma manga de cerâmica pré-fabricada é inserida no tubo de aço e presa com adesivos ou encolhimento. Este método é eficiente para os cotovelos padrão e garante uma superfície interna suave.
O tubo de aço é normalmente formado por flexão ou soldagem a quente, com opções sem costura preferidas para aplicações de alta pressão. Pós-linha, O cotovelo passa por tratamento térmico para solidificar a ligação de aço cerâmica, garantir a durabilidade sob tensões operacionais.
Aplicações
Os cotovelos revestidos de cerâmica são implantados em uma ampla gama de indústrias devido à sua versatilidade e robustez:
- geração de energia: Usado em plantas a carvão para transmitir carvão pulverizado, cinzas, e pasta de calcário em sistemas de dessulfurização de gases de combustível.
- Mineração: Lida com lamas abrasivas, como rejeitos de minério e areia, em pipelines de processamento mineral.
- metalurgia: Transporta metal fundido ou escória em ambientes de alta temperatura.
- Processamento químico: Gerencia líquidos e gases corrosivos, beneficiando -se da inércia química da cerâmica.
- Indústria de cimento: Transmita clínquer de cimento e matérias -primas, resistindo ao desgaste de partículas abrasivas.
Vantagens
A adoção de cotovelos revestidos de cerâmica oferece inúmeros benefícios:
- Vida útil estendida: Supera os cotovelos tradicionais de aço por uma margem significativa, redução da frequência de reposição.
- Eficiência de custos: Os custos com menor manutenção e tempo de inatividade compensam o maior investimento inicial.
- Fluxo aprimorado: As superfícies de cerâmica suaves reduzem o atrito e a perda de pressão, Aprimorando a eficiência do sistema.
- Versatilidade: Adequado para uma ampla gama de temperaturas, pressões, e tipos de mídia.
- Instalação fácil: Design leve e compatibilidade com flanges padrão simplificam a integração.
Limitações
Apesar de suas vantagens, cotovelos revestidos de cerâmica têm algumas desvantagens:
- Maior custo inicial: O uso de cerâmica e processos especializados de fabricação aumenta as despesas iniciais em comparação com os cotovelos de aço.
- fragilidade: O revestimento de cerâmica pode rachar sob o choque mecânico extremo se não for suportado pela camada de aço.
- Reparos complexos: Os revestimentos cerâmicos danificados são difíceis de reparar no local, muitas vezes exigindo substituição.
Avanços recentes
Desenvolvimentos recentes em tecnologia de cotovelo forrada de cerâmica se concentraram em melhorar o desempenho e reduzir os custos:
- Cerâmica avançada: O uso de zta e carboneto de silício (SiC) melhorou a resistência e resistência ao desgaste, Expandindo faixas de aplicativos.
- Design de mochila: Adicionar uma placa de aço ou "mochila" de cerâmica na curva externa do cotovelo aumenta a resistência ao desgaste em zonas de alto impacto.
- Telhas de bloqueio de auto-bloqueio: Designs inovadores de ladrilhos com intertravamento mecânico de 360 ° Aumente a força de ligação e reduz os riscos de delaminação.
- Finos híbridos: A combinação de cerâmica com polímeros ou metais cria revestimentos híbridos que o balanço custa, Dureza, e resistência ao desgaste.
Esses avanços refletem os esforços contínuos para otimizar os cotovelos revestidos de cerâmica para condições industriais cada vez mais exigentes, garantir que eles continuem sendo uma solução preferida para aplicações intensivas em desgaste.
Conclusão
Os cotovelos revestidos de cerâmica são uma prova da sinergia entre ciência material e engenharia, Oferecendo resistência inigualável ao desgaste, Resistência à corrosão, e estabilidade térmica. Seus parâmetros - distantes da composição do material a ângulos de flexão - podem ser adaptados para atender às necessidades operacionais específicas, tornando -os uma escolha versátil para indústrias em todo o mundo. Enquanto seu custo inicial mais alto e fragilidade apresentam desafios, Os benefícios de longo prazo da redução de manutenção e vida útil prolongada superam em muito essas desvantagens. À medida que a tecnologia avança, cotovelos revestidos de cerâmica continuarão a evoluir, solidificando seu papel como pedra angular dos modernos sistemas de tubulação industrial.
Você deve ser logado postar um comentário.