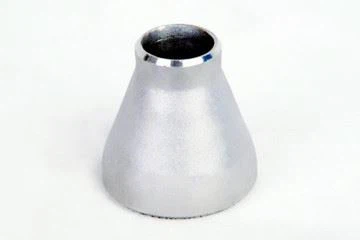
In-Depth Dissection of Specific Grades
WP304 and WP304H
WP304: This grade is the most widely used stainless steel, known for its versatility and balance of properties. It offers excellent resistance to corrosion in atmospheric environments and many corrosive media. Its good mechanical properties and formability make it suitable for a wide range of applications, from kitchen equipment to chemical processing.
WP304H: The high-carbon version of WP304, WP304H is designed for high-temperature applications. The increased carbon content enhances its strength at temperatures above 500°C (932°F). Common applications include boiler and heat exchanger components.
WP309
WP309 stainless steel contains higher levels of chromium and nickel compared to WP304, providing superior oxidation resistance. This grade is often used in environments where high temperatures and corrosive conditions coexist, such as furnace parts, thermal oxidizers, and heat exchangers.
WP310
WP310 is another high-temperature resistant grade, with even higher chromium and nickel content than WP309. It maintains excellent resistance to oxidation and corrosion in environments up to 1100°C (2012°F). Typical applications include furnace components, heat treatment baskets, and chemical processing equipment.
WP316 and WP316L
WP316: The inclusion of molybdenum in WP316 enhances its resistance to chloride pitting and crevice corrosion, making it ideal for marine and chemical environments. It is commonly used in pharmaceutical and food processing equipment, as well as in coastal architectural applications.
WP316L: The low-carbon variant of WP316 offers improved weldability and reduced risk of carbide precipitation during welding. This makes it a preferred choice for welded applications in harsh environments, such as chemical tanks and pipeline systems.
WP317L
WP317L stainless steel contains higher molybdenum content than WP316, providing even better resistance to pitting and crevice corrosion. It is used in highly corrosive environments such as chemical processing, petrochemical, and pharmaceutical industries.
WP321
WP321 is stabilized with titanium, which prevents the formation of chromium carbides at high temperatures, thereby enhancing its resistance to intergranular corrosion. It is suitable for applications involving continuous and intermittent heating, such as exhaust manifolds and aerospace components.
WP347
Similar to WP321, WP347 is stabilized, but with columbium (niobium). This grade offers excellent resistance to intergranular corrosion and is commonly used in high-temperature chemical processing and power generation applications.
WP904L
WP904L is a high-alloy austenitic stainless steel with exceptional corrosion resistance, especially against sulfuric acid and chloride environments. Its high nickel and molybdenum content, along with additions of copper, enhance its resistance to pitting and crevice corrosion. Typical applications include seawater cooling devices, chemical processing, and oil refinery components.
Detailed Usage Scenarios
Chemical Processing
In the chemical industry, the resistance to various acids and chlorides is crucial. Grades such as WP316, WP316L, WP317L, and WP904L are preferred for their superior corrosion resistance. These materials are used in reactors, storage tanks, and piping systems where exposure to harsh chemicals is common.
Oil and Gas Industry
The oil and gas sector demands materials that can withstand high pressures, temperatures, and corrosive environments. WP304H, WP309, WP310, and WP347 are often used in this industry. They are found in applications such as refinery components, pipelines, and offshore drilling equipment.
Marine Applications
Marine environments are highly corrosive, especially due to the presence of chlorides. WP316, WP316L, and WP904L are ideal for such conditions. They are used in shipbuilding, offshore structures, and desalination plants.
Power Generation
Power plants require materials that can withstand high temperatures and pressures. WP321 and WP347 are well-suited for these applications due to their stability and resistance to intergranular corrosion. They are used in boiler components, heat exchangers, and turbine parts.
Food and Beverage Industry
Sanitation and corrosion resistance are paramount in the food and beverage industry. WP304 and WP316 are commonly used due to their non-reactivity with food substances and ease of cleaning. Applications include food processing equipment, storage tanks, and piping.
Summary
Stainless steel reducers compliant with ASTM A403 WP grades offer a diverse range of properties tailored to specific industrial needs. The selection of the appropriate grade depends on factors such as corrosion resistance, temperature resilience, mechanical properties, and weldability. Understanding the unique benefits and applications of each grade ensures optimal performance and longevity of piping systems across various industries.
References
- ASTM A403/A403M: Standard Specification for Wrought Austenitic Stainless Steel Piping Fittings.
- ASM International: Handbook of Stainless Steels.
- NACE International: Corrosion Basics: An Introduction.
- Technical Literature: Material properties and manufacturing processes for stainless steel reducers.
- Market Reports: Trends and forecasts for the stainless steel industry.
This comprehensive document should provide a thorough understanding of stainless steel reducers in the ASTM A403 WP grades, guiding the selection and application of these materials in various industrial contexts.
Detailed Manufacturing Processes
To fully understand the capabilities and limitations of ASTM A403 WP stainless steel reducers, it is essential to delve into the manufacturing processes involved. These processes greatly influence the mechanical properties, microstructure, and overall quality of the final product.
Forging
Forging is a common method used to manufacture stainless steel reducers. This process involves heating the steel to a high temperature and then shaping it using compressive forces. Forging improves the grain structure, resulting in enhanced mechanical properties, including strength and toughness.
- Open-Die Forging: Involves deforming the metal between multiple dies that do not completely enclose the material. It’s suitable for large, custom shapes.
- Closed-Die Forging: Utilizes dies that fully enclose the material, allowing for precise and consistent shapes. This method is ideal for high-volume production of smaller reducers.
Machining
Machining is often employed to achieve the final dimensions and tolerances required for stainless steel reducers. This process involves removing material from a workpiece using cutting tools.
- Turning: Used to create cylindrical parts by rotating the workpiece against a cutting tool.
- Milling: Involves using a rotating cutting tool to remove material and create flat or complex surfaces.
- Drilling and Tapping: Essential for creating holes and threads in the reducers.
Heat Treatment
Heat treatment processes are crucial in enhancing the mechanical properties and corrosion resistance of stainless steel reducers. Common heat treatment methods include:
- Annealing: Involves heating the steel to a specific temperature and then slowly cooling it. This process relieves internal stresses, improves ductility, and refines the microstructure.
- Solution Annealing: Specific to austenitic stainless steels, this process dissolves precipitated carbides, enhancing corrosion resistance.
Welding
Welding is often required to join stainless steel reducers to other components in a piping system. The welding process must be carefully controlled to prevent issues such as carbide precipitation, which can compromise corrosion resistance.
- TIG (Tungsten Inert Gas) Welding: Offers precise control and high-quality welds, making it suitable for thin sections and critical applications.
- MIG (Metal Inert Gas) Welding: Provides faster welding speeds and is suitable for thicker sections.
Surface Finishing
Surface finishing processes are essential for improving the appearance, corrosion resistance, and cleanliness of stainless steel reducers.
- Pickling and Passivation: Involves removing surface contaminants and oxide scales, followed by passivation to restore the protective chromium oxide layer.
- Electropolishing: An electrochemical process that smooths and polishes the surface, enhancing its corrosion resistance and reducing the risk of contamination.
Quality Control and Testing
Ensuring the quality and performance of stainless steel reducers is paramount. Various testing and quality control measures are implemented throughout the manufacturing process.
Chemical Analysis
Chemical analysis verifies the composition of the stainless steel, ensuring it meets the specified grade requirements. Techniques such as Optical Emission Spectroscopy (OES) and X-ray Fluorescence (XRF) are commonly used.
Mechanical Testing
Mechanical testing assesses the strength, ductility, and toughness of the material. Common tests include:
- Tensile Testing: Measures the material’s response to tensile forces, providing data on yield strength, tensile strength, and elongation.
- Hardness Testing: Determines the material’s resistance to indentation and wear.
- Impact Testing: Evaluates the material’s toughness, particularly at low temperatures.
Non-Destructive Testing (NDT)
Non-destructive testing methods are used to detect surface and subsurface defects without damaging the material. Common NDT methods include:
- Ultrasonic Testing (UT): Uses high-frequency sound waves to detect internal flaws.
- Radiographic Testing (RT): Employs X-rays or gamma rays to reveal internal defects.
- Dye Penetrant Testing (DPT): Used for detecting surface cracks and defects.
Dimensional Inspection
Dimensional inspection ensures that the reducers meet the specified dimensions and tolerances. Techniques such as Coordinate Measuring Machines (CMM) and calipers are commonly used.
Conclusion
The selection and application of ASTM A403 WP stainless steel reducers require a thorough understanding of the various grades, their properties, and the manufacturing processes involved. By considering factors such as corrosion resistance, mechanical properties, and specific application requirements, industries can ensure optimal performance and longevity of their piping systems.
References
- ASTM A403/A403M: Standard Specification for Wrought Austenitic Stainless Steel Piping Fittings.
- ASM International: Handbook of Stainless Steels.
- NACE International: Corrosion Basics: An Introduction.
- Technical Literature: Material properties and manufacturing processes for stainless steel reducers.
- Market Reports: Trends and forecasts for the stainless steel industry.
This comprehensive guide should provide valuable insights into the intricate world of stainless steel reducers, aiding in the selection, application, and quality assurance of these critical components in various industries.
You must be logged in to post a comment.