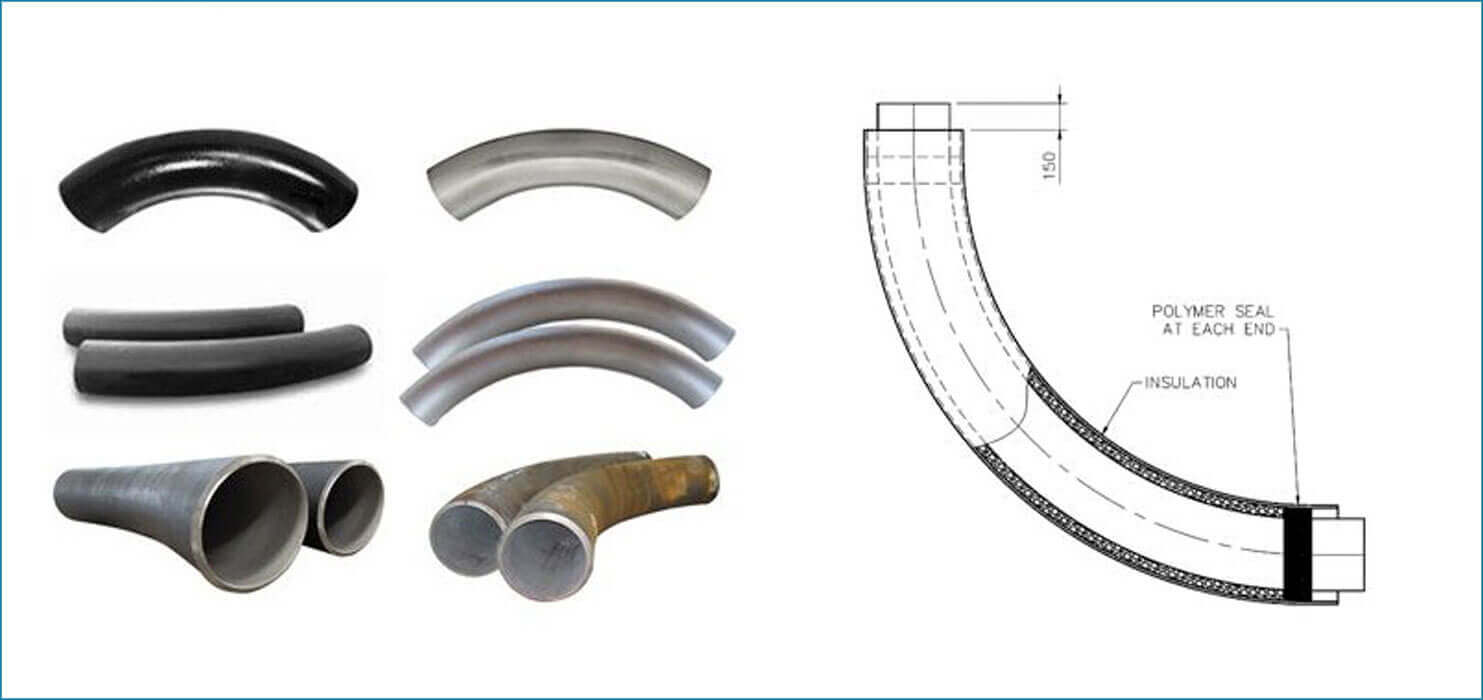
Production of Pipe Bends for Power Stations by the Induction Bending Process
Introduction
Pipe bending is a critical process in the construction and operation of power stations, where complex piping systems are required to transport steam, water, and other fluids under high pressure and temperature. Among the various pipe bending techniques available, the induction bending process stands out as a highly efficient and precise method for producing high-quality pipe bends. This process is particularly suitable for power station applications due to its ability to handle large-diameter pipes, maintain material integrity, and produce bends with minimal distortion.
In this article, we will explore the production of pipe bends for power stations using the induction bending process. The discussion will include the principles of induction bending, its advantages over traditional methods, the steps involved in the process, and its applications in power station piping systems. We will also examine the challenges, quality control measures, and future trends in induction bending for power station projects.
Standard Specification For Buttweld Hot Induction Bend
Dimensions : ASME/ANSI B16.9, ASME B16.28, MSS-SP-43
Size : 2″NB TO 18″ NB
Type : Seamless / ERW / Welded / Fabricated
Bend Radii : 75 / 100 / 150 / 250 / 300 / 500 / 800 / 1,000 / 1,200 / 1,500 mm
Bending Radius(R): R=1D, 2D, 3D, 5D, 6D, 8D, 10D or Custom
Bending angle (θ): 15°, 30°, 45°, 60°, 90°, 135°, 180°
Material & Grades of Hot Induction Pipe Bend :
Stainless Steel Hot Induction Bend :
ASTM A403 WP316/316L, ASTM A403 SA / A 774 WP-S, WP-W, WP-WX 304/304L, ASTM A182 F316L, 304L, DIN 1.4301, DIN1.4306, DIN 1.4401, DIN 1.4404
Duplex & Super Duplex Steel Hot Induction Bend :
ASTM A 815, ASME SA 815 UNS NO S31803, S32205. UNS S32750, S32950. Werkstoff No. 1.4462
Carbon Steel Hot Induction Bend :
ASTM A234, ASME SA234 WPB , WPBW, WPHY 42, WPHY 46, WPHY 52, WPH 60, WPHY 65 & WPHY 70.
Low Temperature Carbon Steel Hot Induction Bend : ASTM A420 WPL3, A420 WPL6
Alloy Steel Hot Induction Bend :
ASTM / ASME A/SA 234 Gr. WP 1, WP 5, WP 9, WP 11, WP 12, WP 22, WP 91
Nickel Alloy Hot Induction Bend :
ASTM B336, ASME SB336, Nickel 200 (UNS No. No2200), Nickel 201 (UNS No. N02201), Monel 400 (UNS No. N04400), Monel 500 (UNS No. N05500), Inconel 800 (UNS No. N08800), Inconel 825 (UNS No. N08825), Inconel 600 (UNS No. N06600), Inconel 625 (UNS No. N06625), Inconel 601 (UNS No. N06601), Hastelloy C 276 (UNS No. N10276), Alloy 20 (UNS No. N08020), Titanium (Grade I & II), Cupro-Nickel 70/30, CuNi10Fe1Mn, CuNi30Mn1Fe.
Importance of Pipe Bends in Power Stations
1. Role of Piping Systems in Power Stations
Piping systems are the backbone of power stations, enabling the transport of steam, water, and other fluids between boilers, turbines, condensers, and other critical components. Pipe bends are essential for:
- Changing the direction of fluid flow.
- Connecting equipment in confined spaces.
- Reducing stress and vibration in piping systems.
2. Challenges in Power Station Piping
- High Temperatures and Pressures: Pipes must withstand extreme operating conditions, often exceeding 500°C and 20 MPa.
- Material Integrity: Bends must maintain the mechanical properties of the pipe material to ensure safety and reliability.
- Complex Geometries: Power station layouts require custom bends with precise angles and radii.
3. Why Induction Bending?
The induction bending process addresses these challenges by producing high-quality bends with:
- Minimal material distortion.
- Enhanced mechanical properties.
- Tight control over bend geometry.
The Induction Bending Process: Overview
Induction bending is a thermo-mechanical process that uses localized heating through electromagnetic induction to bend pipes to the desired shape. The process is highly controlled, ensuring precision and consistency in the final product.
Key Features of Induction Bending:
- Localized Heating: Only the bending area is heated, preserving the properties of the rest of the pipe.
- Controlled Cooling: Cooling is carefully managed to prevent residual stresses and distortion.
- Wide Applicability: Suitable for a variety of materials, including carbon steel, stainless steel, and alloy steel.
Steps in the Induction Bending Process
The production of pipe bends for power stations involves several steps, each critical to achieving the desired quality and performance. Below is a detailed description of the process:
1. Preparation
- Material Selection:
- Pipes are typically made from materials such as carbon steel (e.g., ASTM A106, A53), stainless steel, or alloy steel (e.g., P91, P22), depending on the application.
- The material must meet the required mechanical and thermal properties for power station use.
- Pipe Inspection:
- Pipes are inspected for surface defects, dimensional accuracy, and material consistency.
- Setup:
- The pipe is clamped at one end, while the other end is free to move during bending.
- The induction coil is positioned at the bending point.
2. Induction Heating
- Localized Heating:
- An induction coil generates a high-frequency electromagnetic field, inducing eddy currents in the pipe material.
- These currents produce heat, raising the pipe temperature to the plastic deformation range (typically 800–1100°C, depending on the material).
- Controlled Heating Zone:
- Only a small section of the pipe is heated, minimizing thermal stress and distortion in the surrounding areas.
3. Bending
- Mechanical Force Application:
- Once the pipe section reaches the desired temperature, a bending arm or mechanical force is applied to bend the pipe.
- The bending radius is determined by the setup and can range from tight bends (e.g., 3D) to large-radius bends (e.g., 10D).
- Continuous Movement:
- The pipe is gradually moved through the induction coil, allowing for continuous bending along its length.
4. Cooling
- Controlled Cooling:
- The heated section is cooled using water or air jets to solidify the shape and prevent further deformation.
- Controlled cooling helps maintain the mechanical properties of the pipe and minimizes residual stresses.
5. Post-Bend Processing
- Inspection:
- The bent pipe is inspected for dimensional accuracy, surface quality, and mechanical properties.
- Heat Treatment (if required):
- Additional heat treatment, such as stress relieving or normalizing, may be performed to enhance the pipe’s structural integrity.
- Finishing:
- The pipe is cleaned, and any excess material (e.g., scale or oxidation) is removed.
Advantages of Induction Bending for Power Stations
The induction bending process offers several advantages that make it ideal for producing pipe bends for power stations:
1. Precision and Accuracy
- Tight control over bend radius, angle, and location ensures consistent results.
- Suitable for complex geometries required in power station layouts.
2. Minimal Distortion
- Localized heating reduces the risk of ovality, wall thinning, and other distortions.
3. Enhanced Mechanical Properties
- Controlled heating and cooling preserve or even improve the material’s mechanical properties, such as tensile strength and toughness.
4. Cost-Effectiveness
- Reduces material waste and eliminates the need for welding or additional fittings.
- Faster production compared to traditional bending methods.
5. Wide Material Compatibility
- Can handle a variety of materials, including high-strength alloys used in power station piping.
6. Environmental Benefits
- Uses electricity as the primary energy source, making it cleaner and more sustainable.
Applications of Induction Bending in Power Stations
Induction bending is used in various piping systems within power stations, including:
1. Steam Lines
- High-temperature steam pipes connecting boilers and turbines.
- Bends must withstand extreme heat and pressure without deformation.
2. Water Circulation Systems
- Pipes for circulating cooling water between condensers and cooling towers.
- Large-diameter bends are required for efficient flow.
3. Gas Lines
- Piping for transporting natural gas or other fuels to power generation units.
- Bends must ensure smooth flow and minimal pressure loss.
4. Exhaust Systems
- Custom bends for exhaust pipes in gas turbines and other equipment.
Comparison with Other Bending Methods
Aspect | Induction Bending | Cold Bending | Mandrel Bending |
---|---|---|---|
Heating | Localized heating with induction | No heating | No heating |
Precision | High | Moderate | High |
Material Distortion | Minimal | Higher risk of distortion | Minimal |
Pipe Size | Suitable for large-diameter pipes | Limited to smaller pipes | Limited to smaller pipes |
Cost | Moderate | Low | High |
Applications | Power station pipelines, structural systems | Simple bends for low-stress applications | Complex bends for small-diameter pipes |
Quality Control in Induction Bending
To ensure the quality and reliability of induction-bent pipes, rigorous quality control measures are implemented throughout the process:
1. Dimensional Inspection
- Measurements of bend radius, angle, and ovality are taken to verify compliance with design specifications.
2. Non-Destructive Testing (NDT)
- Techniques such as ultrasonic testing and radiography are used to detect internal defects or cracks.
3. Mechanical Testing
- Tests such as tensile strength, hardness, and impact resistance are conducted to evaluate the pipe’s mechanical properties.
4. Surface Inspection
- Visual inspection is performed to identify surface defects, such as cracks or oxidation.
Challenges in Induction Bending for Power Stations
While induction bending offers numerous advantages, it also presents some challenges:
1. Material Limitations
- Some materials, such as brittle alloys, may not respond well to the induction bending process.
2. Equipment Costs
- The initial investment in induction bending equipment can be high, making it less accessible for small-scale operations.
3. Operator Skill
- The process requires skilled operators to ensure precise control of heating, bending, and cooling parameters.
4. Surface Oxidation
- High temperatures can cause surface oxidation, which may require additional finishing steps.
Case Study: Induction Bending for a Power Station Project
Project Overview:
- Location: A 500 MW coal-fired power station.
- Pipe Material: ASTM A335 P91 alloy steel.
- Pipe Diameter: 24 inches.
- Bending Radius: 5D (five times the pipe diameter).
Results:
- Dimensional Accuracy: All bends met the required specifications with minimal distortion.
- Mechanical Properties: The pipes retained their tensile strength and toughness after bending.
- Cost Savings: The project achieved significant cost savings by eliminating the need for welded fittings.
- Efficiency: The induction bending process reduced production time by 30% compared to traditional methods.
Future Trends in Induction Bending for Power Stations
As power station designs become more complex and demanding, the induction bending process is expected to evolve in the following ways:
1. Automation
- Integration of advanced sensors and control systems to automate the bending process and improve precision.
2. Advanced Materials
- Development of new materials and coatings to enhance the performance and durability of induction-bent pipes.
3. Energy Efficiency
- Innovations in induction heating technology to reduce energy consumption and environmental impact.
4. Digital Simulation
- Use of computational tools, such as finite element analysis (FEA), to simulate the bending process and optimize parameters.
Conclusion
The induction bending process is a versatile and efficient method for producing high-quality pipe bends for power stations. Its ability to handle large-diameter pipes, maintain material integrity, and produce precise bends makes it an ideal choice for power station piping systems. By addressing the challenges and implementing rigorous quality control measures, manufacturers can leverage induction bending to meet the demands of modern power station projects.
As technology advances, the induction bending process will continue to play a vital role in shaping the future of power station construction, offering improved precision, sustainability, and cost-effectiveness.
You must be logged in to post a comment.