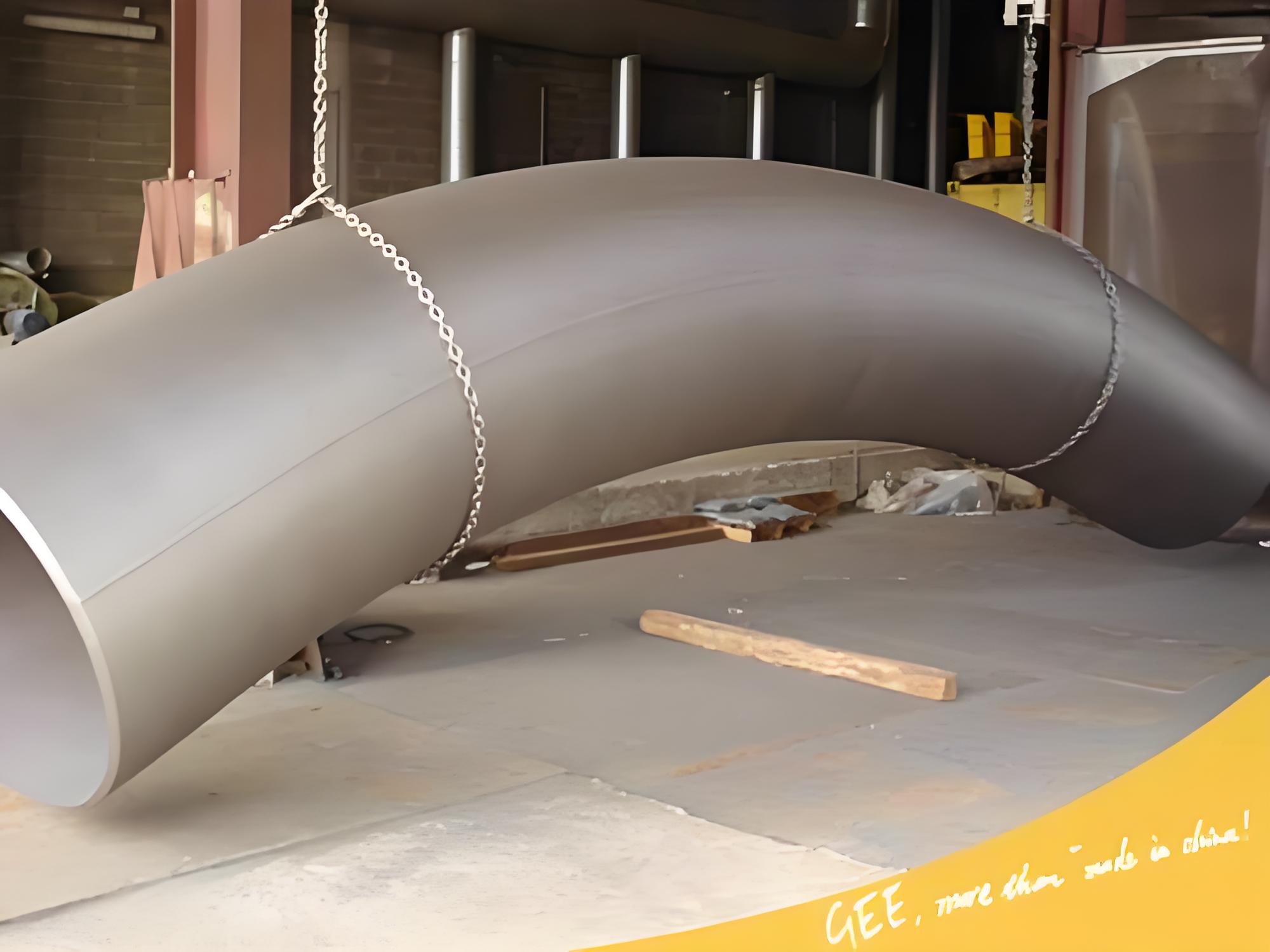
Passivation is a chemical process used to enhance the corrosion resistance of stainless steel surfaces, including stainless steel pipes. The process removes contaminants and promotes the formation of a protective oxide layer that shields the steel from environmental factors that could lead to corrosion.
What Is Passivation?
Passivation refers to the creation or restoration of a thin, uniform layer of chromium oxide on the surface of stainless steel. This layer is passive, meaning it is chemically stable and non-reactive under normal conditions, effectively protecting the underlying material from corrosion.
While stainless steel is inherently corrosion-resistant due to its chromium content (which forms a natural oxide layer in the presence of oxygen), manufacturing processes such as welding, cutting, and machining can introduce contaminants like iron particles, which compromise its resistance. Passivation ensures that the material achieves its full corrosion-resistant potential.
How Does Passivation Work?
Passivation typically involves cleaning the stainless steel to remove contaminants, followed by treating it with a chemical solution—often an acid—to enhance the formation of the chromium oxide layer. The steps are as follows:
-
Cleaning:
- The stainless steel pipe is cleaned to remove surface contaminants, such as grease, oil, dirt, or metal particles.
- Alkaline or detergent-based cleaning agents are often used.
-
Acid Treatment:
- The cleaned surface is treated with a chemical passivation solution, usually a nitric acid (HNO₃) or citric acid solution. The acid:
- Removes surface contaminants, such as free iron and other residues from manufacturing processes.
- Promotes the natural oxidation of chromium in the steel, forming a uniform chromium oxide layer.
- The cleaned surface is treated with a chemical passivation solution, usually a nitric acid (HNO₃) or citric acid solution. The acid:
-
Rinsing:
- The pipe is thoroughly rinsed with deionized water to remove any residual acid or contaminants. This prevents unwanted chemical reactions that could lead to localized corrosion.
-
Drying:
- The pipe is dried in a clean environment to avoid recontamination.
The Science Behind Passivation
The passivation process relies on the interaction between chromium in the stainless steel and oxygen in the environment. Chromium readily reacts with oxygen to form a chromium oxide (Cr₂O₃) layer, which adheres tightly to the steel surface. This oxide layer is:
- Extremely thin (only a few nanometers thick).
- Impermeable to water and air, which protects the underlying metal.
- Self-repairing: If the oxide layer is scratched or damaged, it can reform as long as there is enough oxygen present.
Why Is Passivation Important for Stainless Steel Pipes?
-
Enhanced Corrosion Resistance:
- Stainless steel pipes are often used in environments where they are exposed to moisture, chemicals, or extreme temperatures. Passivation ensures they maintain their corrosion-resistant properties, especially in demanding applications like chemical processing or food and beverage industries.
-
Removal of Contaminants:
- During fabrication and machining, stainless steel pipes can accumulate contaminants like iron particles, which can act as corrosion initiation points. Passivation removes these impurities.
-
Compliance with Standards:
- Industries such as pharmaceutical, aerospace, and food processing have strict requirements for corrosion resistance and cleanliness. Passivation helps meet these standards.
Applications of Passivated Stainless Steel Pipes
- Food and Beverage Processing: Ensures hygiene and resistance to acidic or alkaline cleaning agents.
- Pharmaceutical Industry: Maintains purity by preventing contamination from corrosion.
- Chemical Processing: Protects against harsh chemicals and extreme conditions.
- Marine Environments: Offers resistance to saltwater and humidity-induced corrosion.
- Oil and Gas: Extends the lifespan of pipes in corrosive environments.
Limitations of Passivation
While passivation significantly enhances corrosion resistance, it is not a cure-all. Key limitations include:
- It cannot repair deep scratches or mechanical damage to the stainless steel surface.
- It does not protect against pitting or crevice corrosion caused by chloride-rich environments (e.g., seawater).
- Certain grades of stainless steel, such as those with low chromium content, may not benefit significantly from passivation.
Standards and Guidelines for Passivation
Passivation processes are governed by industry standards to ensure consistency and effectiveness. Key standards include:
- ASTM A967 / A967M: Specifies requirements for chemical passivation treatments for stainless steel.
- ASTM A380 / A380M: Covers cleaning, descaling, and passivation of stainless steel parts, equipment, and systems.
Summary
Passivation is a vital process for enhancing the corrosion resistance of stainless steel pipes. By cleaning the surface and chemically promoting the formation of a chromium oxide layer, passivation extends the life and reliability of stainless steel in a wide range of industries. Following proper procedures and adhering to industry standards ensures optimal results, making passivation a critical step in the maintenance and preparation of stainless steel piping systems.
Maintenance of Passivated Stainless Steel Pipes
After passivation, maintaining the integrity of the passive layer is crucial for long-term corrosion resistance. Here are some best practices:
-
Routine Cleaning:
- Regularly clean the surface to remove dirt, grease, and other contaminants that can compromise the passive layer.
- Use non-abrasive cleaning agents suitable for stainless steel, avoiding products containing chlorides or harsh chemicals.
-
Avoid Mechanical Damage:
- Handle pipes carefully to prevent scratches, dents, or gouges that could expose the underlying metal.
- Minimize contact with carbon steel tools or equipment, as they can deposit iron particles that lead to corrosion.
-
Monitor Exposure to Chlorides:
- Stainless steel pipes exposed to chloride-rich environments (e.g., seawater, de-icing salts) may experience pitting or crevice corrosion.
- Regularly inspect and, if necessary, re-passivate pipes used in such environments.
-
Periodic Inspection and Testing:
- Inspect pipes for signs of corrosion, discoloration, or contamination.
- Perform tests, such as the water break test or ferroxyl test, to verify the effectiveness of the passive layer.
-
Re-Passivation:
- Over time, the passive layer may degrade due to wear, exposure to harsh chemicals, or environmental factors.
- Re-passivation can restore corrosion resistance and prolong the service life of the pipes.
Common Misconceptions About Passivation
-
Passivation Is Not Coating:
- Unlike coatings (e.g., paint or plating), passivation does not add an additional layer of material to the surface. It enhances the natural properties of stainless steel by optimizing the chromium oxide layer.
-
Passivation Is Not a Cure-All for Corrosion:
- While passivation significantly improves corrosion resistance, it does not eliminate all forms of corrosion. Localized issues, such as pitting in chloride environments, require additional protective measures.
-
Passivation Does Not Replace Cleaning:
- Passivation removes contaminants and promotes the oxide layer but does not eliminate the need for regular cleaning and maintenance to ensure long-term performance.
Passivation is a critical process for maximizing the corrosion resistance of stainless steel pipes. By cleaning and chemically treating the surface, passivation restores the integrity of the protective chromium oxide layer, ensuring durability in harsh and demanding environments. Industries ranging from food and beverage to aerospace rely on passivated stainless steel pipes for their strength, cleanliness, and resistance to environmental degradation.
To achieve optimal results, follow industry standards such as ASTM A967 or ASTM A380, ensure proper handling and maintenance, and monitor pipes for signs of wear or contamination. Properly executed passivation enhances the lifespan and reliability of stainless steel piping systems, reducing maintenance costs and ensuring consistent performance over time.
You must be logged in to post a comment.