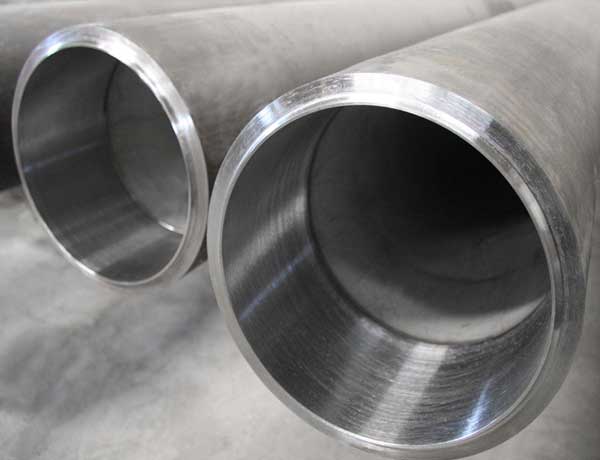
Industry Standards for Mechanically Lined Pipe Inspection
The inspection of mechanically lined pipes (MLPs) is governed by various industry standards to ensure their safety, reliability, and quality. These standards vary by region and industry, but a few of the most common ones include:
-
API 5LD: Published by the American Petroleum Institute, this standard covers the manufacturing and testing of clad and lined steel pipe. It specifies requirements for pipe grades, manufacturing processes, inspection, and certification.
-
ASME B31.3: This standard from the American Society of Mechanical Engineers covers the design and construction of process piping systems. It includes provisions for inspection, examination, and testing.
-
DIN EN 13445-5: This is a European standard for unfired pressure vessels. It defines requirements for inspection and testing of pressure vessels, including MLPs.
-
ISO 21809-5: This international standard provides guidelines for the qualification, application, testing, and inspection of polyethylene or polypropylene lining systems for the internal corrosion protection of pipelines.
Advantages of Mechanically Lined Pipes
There are several benefits to using MLPs over other types of pipes, particularly in applications involving corrosive fluids or high-pressure environments. These advantages include:
Corrosion Resistance
MLPs comprise an inner layer made from corrosion-resistant alloys (CRAs), providing excellent resistance to corrosive substances. This characteristic makes MLPs ideal for use in oil and gas, chemical, and other industries where pipelines frequently come into contact with corrosive fluids.
Cost-Effectiveness
While CRAs provide excellent corrosion resistance, they are often expensive. By using these alloys only for the inner layer and a cheaper, but strong, material like carbon steel for the outer layer, MLPs represent a more cost-effective solution than pipes made entirely from CRA.
High Strength and Durability
The combination of a strong outer layer and a corrosion-resistant inner layer makes MLPs both durable and robust. They can withstand high pressures and temperatures, making them suitable for challenging industrial applications.
Flexibility
The mechanical bonding process used in the production of MLPs allows for flexibility in choosing the materials for the inner and outer pipes. This flexibility means that MLPs can be customized to meet the specific requirements of various applications.
Reduced Maintenance Costs
Due to their corrosion resistance, MLPs often require less maintenance than pipes made from less resistant materials. This feature can result in significant cost savings over the life of the pipeline.
In conclusion, mechanically lined pipes offer a combination of strength, corrosion resistance, and cost-effectiveness that’s hard to match with other types of pipes. These advantages, along with strict adherence to industry inspection standards, make MLPs a preferred choice for many challenging industrial applications.
You must be logged in to post a comment.