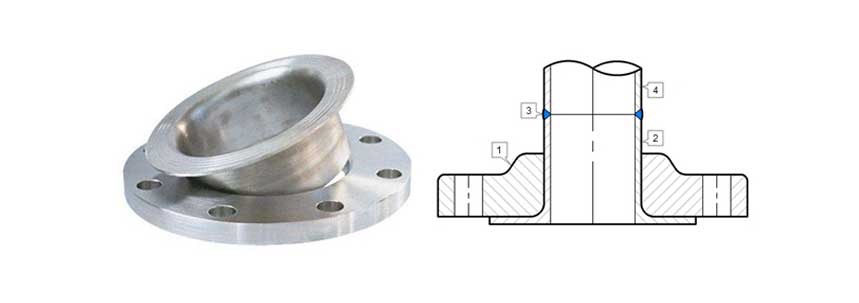
Lap Joint Flange: Overview, Applications, and Benefits
Introduction
In the world of piping systems, flanges play a critical role in connecting pipes, valves, pumps, and other equipment to form a complete piping network. Among the various types of flanges used in industrial applications, the Lap Joint Flange stands out for its unique design and specific advantages. This type of flange is commonly used in systems where frequent disassembly and maintenance are required, as well as in applications where alignment flexibility is a priority.
This article provides an in-depth look at Lap Joint Flanges, covering their design, applications, benefits, and key considerations for use. We will also compare them with other types of flanges to highlight their unique features and advantages.
What is a Lap Joint Flange?
A Lap Joint Flange is a type of flange that is used in conjunction with a stub end. Unlike other flanges, the Lap Joint Flange does not come into direct contact with the fluid or gas inside the pipe. Instead, it is designed to slide over the pipe and rest against the back of the stub end. The stub end is welded to the pipe, while the Lap Joint Flange remains loose, allowing for easy alignment and adjustment.
Key Components of a Lap Joint Flange Assembly:
- Lap Joint Flange: A loose flange that slides over the pipe and rests against the stub end.
- Stub End: A short piece of pipe that is welded to the end of the pipe and provides a seating surface for the Lap Joint Flange.
Design Features
- Loose Flange: The Lap Joint Flange is not welded or fixed to the pipe, allowing it to rotate freely around the pipe. This feature makes it easier to align bolt holes during assembly.
- Stub End: The stub end is welded to the pipe, and the Lap Joint Flange rests against it. The stub end provides the sealing surface, while the flange is used for bolting the connection.
- Raised Face or Flat Face: Lap Joint Flanges can have either a raised face or a flat face, depending on the sealing requirements of the application.
Table 1: Key Characteristics of Lap Joint Flanges
Characteristic | Description |
---|---|
Flange Type | Loose flange used with a stub end |
Connection | Flange slides over the pipe and rests against the stub end |
Welding | Stub end is welded to the pipe, while the flange remains loose |
Alignment | Flange can rotate around the pipe, allowing for easy alignment of bolt holes |
Sealing Surface | The stub end provides the sealing surface, while the flange is used for bolting |
Face Type | Available in raised face or flat face configurations |
Design of Lap Joint Flange
A lap joint flange consists of two main components:
-
Flat Face Flange: The flat face flange is the main body of the lap joint flange. It has a flat surface with bolt holes to secure the flange to the mating flange or pipe.
-
Stub End: The stub end is a short piece of pipe with a lap joint configuration. It slides over the pipe end and allows the flange to rotate freely, providing flexibility during alignment.
The lap joint flange is typically used with a gasket to ensure a leak-proof joint between the flanges.
Stub End – Key Fittings for Lap Joint Flange
A stub end is always used with a lap joint flange as a backing flange. There are three different types of stub ends, type A, B and C.
- Type A stub end can be machined to fit the standard lap joint support flange.
- Type B stub end is designed to be used with standard slip on flange.
- Either a lap joint flange or slip on flange, the type C stub end can be used
Stub end include long or short pattern length. The end of long pattern is also known as ASA Stub Ends. The short end is used with the larger flanges of ANSI 300 and 600. They are commonly used in most sizes ANSI 900 and above.
Lap joint flange datasheets
The datasheets we have on this site are shown below. For simplicity sake, only datasheets that adhere to B16.5 are shown. ASME B16.5 covers flange dimensions from ½” to 24”. For sizes larger than this (ASME B16.47 Series A & B), please visit our flange datasheets page.
Class | Flat Face |
ANSI 150 | Lap Joint, ANSI Class 150 (in) |
ANSI 300 | Lap Joint, ANSI Class 300 (in) |
ANSI 400 | Lap Joint, ANSI Class 400 (in) |
ANSI 600 | Lap Joint, ANSI Class 600 (in) |
ANSI 900 | Lap Joint, ANSI Class 900 (in) |
ANSI 1500 | Lap Joint, ANSI Class 1500 (in) |
ANSI 2500 | Lap Joint, ANSI Class 2500 (in) |
Applications of Lap Joint Flanges
Lap Joint Flanges are commonly used in applications where frequent disassembly and maintenance are required, as well as in systems where alignment flexibility is important. Some of the key industries and applications where Lap Joint Flanges are used include:
1. Petrochemical and Oil & Gas Industry
In the oil and gas industry, piping systems often require frequent inspection, cleaning, and maintenance. Lap Joint Flanges are ideal for these applications because they allow for easy disassembly and reassembly of the piping system. The ability to rotate the flange around the pipe makes it easier to align bolt holes, reducing the time and effort required for maintenance.
2. Chemical Processing Plants
In chemical processing plants, where corrosive fluids and gases are often transported, Lap Joint Flanges are used with corrosion-resistant stub ends made from materials such as stainless steel or nickel alloys. The flange itself can be made from a less expensive material, as it does not come into direct contact with the corrosive fluid. This reduces costs while maintaining the integrity of the system.
3. Water Treatment and Desalination Plants
Water treatment and desalination plants often require piping systems that can be easily disassembled for cleaning and maintenance. Lap Joint Flanges are used in these systems because of their ability to be easily removed and reinstalled. Additionally, the use of corrosion-resistant stub ends ensures the longevity of the system in harsh environments.
4. Food and Beverage Industry
In the food and beverage industry, hygiene and cleanliness are critical. Lap Joint Flanges allow for the easy disassembly of piping systems for cleaning and sterilization. The use of corrosion-resistant materials, such as stainless steel, ensures that the piping system remains sanitary and free from contamination.
5. Marine and Shipbuilding Industry
In the marine industry, where piping systems are exposed to harsh environmental conditions, Lap Joint Flanges are used in conjunction with corrosion-resistant stub ends to ensure the longevity of the system. The ability to easily disassemble and reassemble the piping system is also beneficial for maintenance and repairs in marine applications.
Table 2: Common Applications of Lap Joint Flanges
Industry | Application |
---|---|
Oil & Gas | Piping systems requiring frequent maintenance and alignment flexibility |
Chemical Processing | Corrosive environments with the need for corrosion-resistant materials |
Water Treatment | Systems requiring easy disassembly for cleaning and maintenance |
Food & Beverage | Hygienic piping systems that require frequent cleaning and sterilization |
Marine & Shipbuilding | Corrosion-resistant piping systems exposed to harsh environmental conditions |
Frequently used astm grades
Material | Fittings | Flanges | Valves | Bolts & Nuts |
---|---|---|---|---|
Carbon Steel | A234 Gr WPA | A105 | A216 Gr WCB | A193 Gr B7 A194 Gr 2H |
A234 Gr WPB | A105 | A216 Gr WCB | ||
A234 Gr WPC | A105 | A216 Gr WCB | ||
Carbon Steel Alloy High-Temp |
A234 Gr WP1 | A182 Gr F1 | A217 Gr WC1 | A193 Gr B7 A194 Gr 2H |
A234 Gr WP11 | A182 Gr F11 | A217 Gr WC6 | ||
A234 Gr WP12 | A182 Gr F12 | A217 Gr WC6 | ||
A234 Gr WP22 | A182 Gr F22 | A217 Gr WC9 | ||
A234 Gr WP5 | A182 Gr F5 | A217 Gr C5 | ||
A234 Gr WP9 | A182 Gr F9 | A217 Gr C12 | ||
Carbon Steel Alloy Low-Temp |
A420 Gr WPL6 | A350 Gr LF2 | A352 Gr LCB | A320 Gr L7 A194 Gr 7 |
A420 Gr WPL3 | A350 Gr LF3 | A352 Gr LC3 | ||
Austenitic Stainless Steel | A403 Gr WP304 | A182 Gr F304 | A182 Gr F304 | A193 Gr B8 A194 Gr 8 |
A403 Gr WP316 | A182 Gr F316 | A182 Gr F316 | ||
A403 Gr WP321 | A182 Gr F321 | A182 Gr F321 | ||
A403 Gr WP347 | A182 Gr F347 | A182 Gr F347 |
Benefits of Lap Joint Flanges
Lap Joint Flanges offer several advantages over other types of flanges, particularly in applications where frequent disassembly, alignment flexibility, and cost savings are important considerations.
1. Ease of Assembly and Disassembly
One of the primary advantages of Lap Joint Flanges is their ability to be easily assembled and disassembled. Since the flange is not welded to the pipe, it can be rotated around the pipe to align the bolt holes, making installation and maintenance faster and easier. This feature is particularly beneficial in systems that require frequent disassembly for cleaning, inspection, or repairs.
2. Alignment Flexibility
The ability of the Lap Joint Flange to rotate around the pipe provides significant alignment flexibility. This is especially useful in applications where precise alignment of bolt holes is required, such as in large piping systems or systems with multiple connections. The flexibility to adjust the flange’s position without having to move the pipe makes installation more efficient.
3. Cost Savings
In applications where corrosion resistance is required, using a Lap Joint Flange can result in significant cost savings. The stub end, which is in direct contact with the fluid, can be made from a corrosion-resistant material, while the flange itself can be made from a less expensive material. This reduces the overall cost of the piping system without compromising its performance.
4. Reduced Stress on the Pipe
Since the Lap Joint Flange is not welded to the pipe, it does not introduce additional stress to the pipe during installation or operation. This can help reduce the risk of stress-related failures, particularly in systems that are subjected to thermal expansion or mechanical vibrations.
5. Versatility
Lap Joint Flanges are versatile and can be used in a wide range of applications, from low-pressure systems to high-pressure systems. They are available in various sizes, materials, and pressure ratings, making them suitable for a wide range of industries and applications.
Table 3: Benefits of Lap Joint Flanges
Benefit | Description |
---|---|
Ease of Assembly | Flange can be rotated for easy alignment of bolt holes |
Alignment Flexibility | Flange can be adjusted without moving the pipe |
Cost Savings | Corrosion-resistant stub end with less expensive flange material |
Reduced Stress | No additional stress introduced to the pipe during installation |
Versatility | Suitable for a wide range of applications and pressure ratings |
Comparison with Other Flange Types
While Lap Joint Flanges offer several advantages, they are not always the best choice for every application. It is important to compare them with other types of flanges to determine the most suitable option for a given application.
1. Lap Joint Flange vs. Weld Neck Flange
A Weld Neck Flange is welded directly to the pipe, providing a strong and permanent connection. This type of flange is commonly used in high-pressure and high-temperature applications where strength and durability are critical. However, Weld Neck Flanges do not offer the same alignment flexibility as Lap Joint Flanges, and they are more difficult to disassemble for maintenance.
- Lap Joint Flange: Easier to assemble and disassemble, better alignment flexibility, but not as strong as Weld Neck Flanges.
- Weld Neck Flange: Stronger and more durable, but more difficult to align and disassemble.
2. Lap Joint Flange vs. Slip-On Flange
A Slip-On Flange is slipped over the pipe and welded in place. It is easier to install than a Weld Neck Flange but does not provide the same level of strength. Slip-On Flanges are commonly used in low-pressure applications. Like Lap Joint Flanges, Slip-On Flanges are easier to align than Weld Neck Flanges, but they do not offer the same flexibility in terms of disassembly.
- Lap Joint Flange: Easier to disassemble and offers better alignment flexibility.
- Slip-On Flange: Easier to install than Weld Neck Flanges but not as flexible as Lap Joint Flanges.
3. Lap Joint Flange vs. Threaded Flange
A Threaded Flange is screwed onto the pipe, making it easy to install without welding. Threaded Flanges are commonly used in low-pressure applications and systems where welding is not feasible. However, they are not suitable for high-pressure or high-temperature applications, and they do not offer the same alignment flexibility as Lap Joint Flanges.
- Lap Joint Flange: Suitable for a wider range of applications, including high-pressure systems, and offers better alignment flexibility.
- Threaded Flange: Easier to install but limited to low-pressure applications.
Table 4: Comparison of Lap Joint Flanges with Other Flange Types
Flange Type | Strength | Ease of Assembly | Alignment Flexibility | Disassembly | Applications |
---|---|---|---|---|---|
Lap Joint Flange | Moderate | Easy | High | Easy | Frequent maintenance, alignment required |
Weld Neck Flange | High | Moderate | Low | Difficult | High-pressure, high-temperature systems |
Slip-On Flange | Moderate | Easy | Moderate | Moderate | Low-pressure systems |
Threaded Flange | Low | Very Easy | Low | Moderate | Low-pressure, non-welded applications |
Considerations for Using Lap Joint Flanges
When selecting a Lap Joint Flange for a specific application, several factors should be considered to ensure optimal performance and longevity.
1. Pressure and Temperature Ratings
Lap Joint Flanges are available in various pressure ratings, typically ranging from Class 150 to Class 2500. It is important to select a flange with the appropriate pressure rating for the application to ensure that it can withstand the operating conditions. Additionally, the temperature rating of the flange and stub end materials should be considered, especially in high-temperature applications.
2. Material Compatibility
The material of the stub end must be compatible with the fluid or gas being transported to prevent corrosion or degradation. Common materials for stub ends include stainless steel, nickel alloys, and carbon steel. The Lap Joint Flange itself can be made from a less expensive material, as it does not come into direct contact with the fluid.
3. Corrosion Resistance
In corrosive environments, it is essential to select materials that offer adequate corrosion resistance. The stub end, which is in direct contact with the fluid, should be made from a corrosion-resistant material, such as stainless steel or nickel alloys. The flange can be made from a less expensive material, but it should still offer some level of corrosion resistance to ensure longevity.
4. Maintenance Requirements
Lap Joint Flanges are ideal for systems that require frequent disassembly and maintenance. However, if the system does not require regular maintenance, other types of flanges, such as Weld Neck Flanges, may be more suitable due to their superior strength and durability.
Conclusion
Lap Joint Flanges offer a versatile and cost-effective solution for piping systems that require frequent disassembly, alignment flexibility, and corrosion resistance. By using a corrosion-resistant stub end and a less expensive flange material, industries can reduce costs without compromising the performance of the system. The ability to rotate the flange around the pipe makes installation and maintenance easier, while the reduced stress on the pipe helps prevent failures.
Lap Joint Flanges are widely used in industries such as oil and gas, chemical processing, water treatment, and food and beverage, where frequent maintenance and alignment flexibility are critical. By understanding the benefits and limitations of Lap Joint Flanges, engineers can select the most appropriate flange type for their specific application, ensuring the long-term reliability and efficiency of the piping system.
FAQ
What is a Lap Joint Flange?
A Lap Joint Flange is a type of flange used in conjunction with a stub end. The flange is loose and can rotate around the pipe, allowing for easy alignment of bolt holes. The stub end is welded to the pipe, while the flange is used for bolting the connection.
What are the advantages of using a Lap Joint Flange?
Lap Joint Flanges offer several advantages, including ease of assembly and disassembly, alignment flexibility, cost savings, reduced stress on the pipe, and versatility in a wide range of applications.
Where are Lap Joint Flanges commonly used?
Lap Joint Flanges are commonly used in industries such as oil and gas, chemical processing, water treatment, food and beverage, and marine applications. They are ideal for systems that require frequent maintenance and alignment flexibility.
How does a Lap Joint Flange differ from a Weld Neck Flange?
A Lap Joint Flange is not welded to the pipe and can rotate around the pipe for easy alignment, while a Weld Neck Flange is welded directly to the pipe, providing a stronger and more permanent connection. Weld Neck Flanges are typically used in high-pressure and high-temperature applications.
What materials are used for Lap Joint Flanges and stub ends?
Lap Joint Flanges can be made from materials such as carbon steel, stainless steel, or alloy steel. The stub end, which is in direct contact with the fluid, is typically made from corrosion-resistant materials such as stainless steel or nickel alloys.
You must be logged in to post a comment.