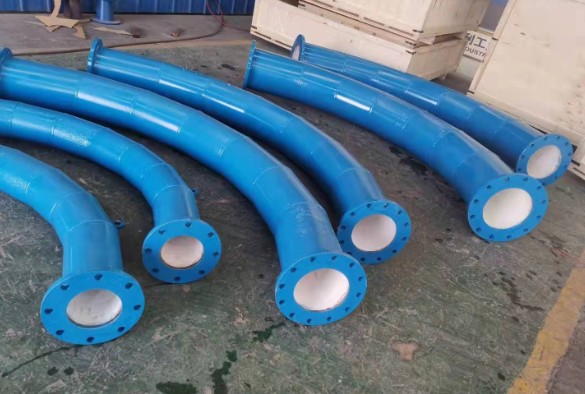
Gomito foderato in ceramica: Comprehensive Analysis
Ceramic lined elbows are critical components in industrial piping systems, designed to handle abrasive, corrosive, and high-temperature materials. These elbows combine the durability of steel with the exceptional wear and corrosion resistance of ceramic linings, making them indispensable in industries such as power generation, Data Mining, metallurgia, e lavorazione chimica. This document provides an in-depth analysis of ceramic lined elbows, including a parameters table, Composizione materiale, Proprietà meccaniche, Resistenza all'usura, Angoli di piegatura, and a detailed discussion of their performance and applications.
Parameters Table
Parametro | Descrizione | Valori tipici |
---|---|---|
Materiale del tubo esterno | Base material of the elbow | ACCIAIO AL CARBONIO (es, 20# seamless steel), IN ACCIAIO INOX |
Ceramic Lining Material | Inner lining material | Allumina (Al₂O₃, ≥90%), Zirconia ha rafforzato l'allumina (ZTA) |
Diametro del tubo | Inner diameter of the pipe | 0.5 pollici a 24 pollici (customizable) |
Ceramic Thickness | Thickness of the ceramic lining | 6 mm – 25 mm |
Angolo di curvatura | Angolo di direzione Cambia | 22.5°, 45°, 90°, 180° (angoli personalizzati disponibili) |
Bend Raggio | Raggio di curvatura | 1.5D – 5D (D = diametro del tubo) |
temperatura di esercizio | Resistenza alla temperatura massima | -50° C a 900 ° C. (a lungo termine), fino a 2000 ° C. (a breve termine) |
Resistenza alla pressione | Forza del cerchio | 300 – 500 MPa |
Resistenza all'usura | Rispetto all'acciaio al carbonio | 15 – 20 volte più alto |
Microdurezza | Durezza del rivestimento in ceramica | alta tensione 1000 – 1600 |
Densità | Densità del rivestimento ceramico | 3.62 g/cm³ (Allumina) |
vita utile | Durata prevista in condizioni abrasive | 5 – 20 anni (a seconda dell'applicazione) |
Composizione materiale
I gomiti foderati in ceramica sono costituiti da due strati di materiale primario: il tubo in acciaio esterno e il rivestimento in ceramica interna. Il tubo esterno è in genere realizzato in acciaio al carbonio (es, 20# seamless steel) o acciaio inossidabile, Fornire integrità strutturale e facilità di saldatura o flancia. Il rivestimento in ceramica, di solito composto da allumina di alta purezza (Al₂O₃) o allumina tempestiva di zirconia (ZTA), è legato alla superficie interna usando adesivi resistenti ad alta temperatura o tecniche di interblocco meccanico.
Materiale del tubo esterno
Il tubo esterno funge da spina dorsale strutturale del gomito. L'acciaio al carbonio è comunemente usato per il suo costo-efficacia, molta forza, e saldabilità. Per applicazioni che coinvolgono ambienti corrosivi, L'acciaio inossidabile può essere preferito per migliorare la resistenza alla corrosione. Lo strato in acciaio garantisce che il gomito può resistere alle sollecitazioni meccaniche, come pressione e impatto, Pur facilitando l'integrazione nei sistemi di tubazioni esistenti.
Ceramic Lining Material
Il rivestimento in ceramica è la chiave delle prestazioni eccezionali del gomito. Allumina, con un contenuto Al₂o₃ di 90% o superiore, è il materiale più utilizzato per la sua alta durezza, Resistenza all'usura, e stabilità termica. Zirconia ha rafforzato l'allumina (ZTA) è una variante avanzata che offre una migliore durezza e resistenza all'impatto, renderlo adatto a sistemi dinamici con elevato shock meccanico. Lo strato ceramico viene in genere applicato come piastrelle, maniche, o un rivestimento monolitico, A seconda del processo di produzione.
La struttura a grana fine del materiale ceramico e l'alta densità contribuiscono alla sua durata. ad esempio, Le ceramiche di allumina presentano una durezza da diamante e una resistenza meccanica superiore, rendendoli ideali per applicazioni impegnative. La scelta del materiale ceramico può essere adattata a requisiti operativi specifici, come estrema abrasione o esposizione chimica.
Proprietà meccaniche
Le proprietà meccaniche dei gomiti foderati in ceramica sono un composito dello strato esterno in acciaio e del rivestimento interno ceramico. Queste proprietà determinano la capacità del gomito di resistere alla pressione, Impatto, e shock termico, Garantire prestazioni affidabili in ambienti difficili.
forza
La resistenza del cerchio dei gomiti foderati in ceramica, che misura la resistenza alla pressione radiale, tipicamente varia da 300 per 500 MPa. Questa forza deriva principalmente dallo strato esterno in acciaio, che fornisce supporto strutturale. Il rivestimento in ceramica, mentre fragile, contribuisce all'integrità complessiva resistendo al degrado superficiale e mantenendo la forma del gomito in condizioni abrasive.
Resistenza alla flessione, o piegare la forza, è una proprietà critica per il rivestimento in ceramica. Le ceramiche di allumina presentano un'alta resistenza alla flessione, Spesso testato tramite test di flessione a 3 o 4 punti. I valori possono superare 300 MPa, A seconda della dimensione del grano, porosità, e produzione qualità. tuttavia, La fragilità della ceramica significa che si basa sullo strato d'acciaio per assorbire le sollecitazioni di piegatura senza cracking.
Durezza
La microdurezza del rivestimento in ceramica, misurato sulla scala Vickers, vanno da Hv 1000 per 1600 per materiali a base di allumina. Questa durezza è significativamente più alta di quella dell'acciaio al carbonio (approssimativamente Hv 150-200 Dopo aver spedito) o anche in carburo di tungsteno (alta tensione 1200-1500), rendere lo strato ceramico eccezionalmente resistente ai graffi e all'usura. L'elevata durezza assicura che il gomito possa gestire materiali abrasivi come la polvere di carbone, cenere, o sospensione del minerale senza significativi danni alla superficie.
Dolusità e resistenza all'impatto
Mentre le ceramiche di allumina sono intrinsecamente fragili, La loro tenacità può essere migliorata usando ZTA o ottimizzando il legame con lo strato d'acciaio. Il tubo esterno in acciaio offre un'eccellente resistenza all'impatto, Assorbendo gli shock meccanici che potrebbero altrimenti fratturare il rivestimento in ceramica. In pratica, I gomiti foderati in ceramica hanno dimostrato resilienza nelle applicazioni che coinvolgono impatti delle particelle ad alta velocità, come i sistemi di trasporto pneumatico.
Resistenza agli shock termici
I gomiti foderati in ceramica possono funzionare a temperature che vanno da -50 ° C a 900 ° C per periodi prolungati, con resistenza a breve termine fino a 2000 ° C. Il coefficiente di espansione termica bassa del rivestimento in ceramica riduce al minimo le cracking in rapidi cambiamenti di temperatura, Mentre lo strato in acciaio fornisce ulteriore stabilità. Questa resistenza agli shock termici è cruciale in settori come la generazione di energia, dove le condutture possono sperimentare temperature fluttuanti.
Resistenza all'usura
La resistenza all'usura è la caratteristica distintiva dei gomiti foderati in ceramica, distinguerli dagli accessori tradizionali in acciaio o ghisa. La capacità del rivestimento in ceramica di resistere all'abrasione e all'erosione estende la vita di servizio del gomito 15 per 20 tempi rispetto ai gomiti di acciaio al carbonio sfoderato, Ridurre i costi di manutenzione e i tempi di inattività.
Meccanismo di resistenza all'usura
L'elevata durezza e la superficie liscia del rivestimento in ceramica minimizzano la perdita di materiale a causa dell'usura abrasiva. Nelle applicazioni che coinvolgono fanghi o polveri ad alta velocità (es, cenere di carbone, calcare, o sabbia), Lo strato ceramico resiste all'erosione riducendo l'attrito e prevenendo l'incorporamento delle particelle. La resistenza all'usura viene quantificata confrontando le prestazioni del rivestimento in ceramica con quelle dell'acciaio al carbonio, con studi che mostrano un aumento della durata di una vita fino a 20 volte in condizioni abrasive.
Il basso fattore di attrito della ceramica a bassi angoli di impingement migliora ulteriormente la resistenza all'usura riducendo l'impatto abrasivo delle particelle. Questa proprietà è particolarmente vantaggiosa nei gomiti, dove i cambiamenti della direzione del flusso aumentano la turbolenza e l'usura. La superficie interna liscia impedisce anche l'accumulo di materiale, Garantire portate coerenti e ridurre il rischio di blocchi.
Analisi comparativa
Rispetto ad altri materiali resistenti all'usura, come basalto fuso o acciaio in lega, I rivestimenti in ceramica offrono prestazioni superiori. Basalto cast, sebbene durevole, ha una resistenza all'usura inferiore ed è soggetto a cracking sotto impatti ad alta velocità. Acciaio legato, con una durezza superficiale di approssimativamente 60 HRC, si consuma più velocemente delle ceramiche (80+ Equivalente HRC). In applicazioni del mondo reale, come centrali elettriche a carbone, I gomiti foderati in ceramica hanno superato i gomiti in acciaio a parete spessa di un fattore di cinque o più.
vita utile
La durata di servizio di un gomito foderato in ceramica dipende dalla gravità dell'applicazione. Nei sistemi di trasporto pneumatico per cenere volante o cemento, dove l'abrasione è intensa, Il rivestimento in ceramica può durare 5 per 10 anni, rispetto a 1-2 anni per i gomiti in acciaio. In condizioni meno abrasive, come la lavorazione chimica, La durata della vita può superare 20 anni. Il tasso medio di usura dello strato ceramico è approssimativamente 0.5-1 mm all'anno, Significato a 6 Il rivestimento MM potrebbe durare 5 anni in ambienti esigenti.
Angoli di piegatura
I gomiti foderati in ceramica sono disponibili in vari angoli di flessione per ospitare diversi layout di tubazioni. L'angolo determina il grado di cambio di direzione, influire sulla dinamica del flusso e i motivi di usura all'interno del gomito.
Angoli di piegatura standard
Gli angoli di piegatura più comuni sono 22,5 °, 45°, 90°, e 180°, Sebbene gli angoli personalizzati possano essere fabbricati per soddisfare i requisiti specifici. Questi angoli corrispondono allo standard Tubo Di Raccordo disegni:
- 22.5° Gomito: Utilizzato per lievi regolazioni direzionali nei sistemi di tubazioni.
- 45° Gomito: Fornisce un moderato cambiamento di direzione, Riduzione della turbolenza rispetto ai gomiti a 90 °.
- 90° Gomito: L'angolo più utilizzato per le curve perpendicolari, Comune in layout stretti.
- 180° Gomito: Una curva di ritorno per la direzione del flusso invertito, Spesso utilizzato negli scambiatori di calore o nei sistemi compatti.
Raggio di curvatura
Il raggio di curva, tipicamente espresso come un multiplo del diametro del tubo (D), vanno da 1.5d a 5d. Un raggio maggiore (es, 5D) si traduce in una curva delicata, Ridurre la resistenza del flusso e la concentrazione di usura alla curva. Gomiti a raggio corto (1.5D) sono più compatti ma sperimentano un'usura più elevata a causa di curve più nitide. La scelta del raggio dipende dai vincoli di spazio, Requisiti di flusso, e indossare considerazioni.
Impatto sulle prestazioni
L'angolo di flessione e il raggio influenzano significativamente le prestazioni del gomito. Angoli più nitidi (es, 90°) e raggi più piccoli aumentano la turbolenza e l'impatto delle particelle, usura accelerata alla curva esterna. I rivestimenti in ceramica mitigano questo fornendo un duro, superficie liscia che devia le particelle abrasive. Al contrario, raggi più grandi e angoli più piccoli distribuiscono l'usura in modo più uniforme, Migliorare la longevità.
Analisi dettagliata
I gomiti foderati in ceramica rappresentano una fusione di materiali avanzati e progettazione ingegneristica, Su misura per affrontare le sfide del trasporto di materiali abrasivi e corrosivi. Questa sezione esplora i loro processi di produzione, applicazioni, Vantaggi, Limitazioni, e recenti progressi, Fornire una comprensione olistica del loro ruolo nell'industria moderna.
processo di produzione
I gomiti foderati in ceramica sono prodotti utilizzando diverse tecniche, ognuno influenza le loro prestazioni e il costo:
- Colata centrifuga: L'allumina fusa è lanciata all'interno di un tubo d'acciaio sotto la forza centrifuga, formare un denso, strato in ceramica uniforme. Questo metodo garantisce un'elevata resistenza al legame ed è ideale per i gomiti di grande diametro.
- Rivestimento in piastrelle: Le piastrelle di ceramica pre-formate vengono rispettate alla superficie interna del tubo di acciaio usando adesivi ad alta temperatura o interblocco meccanico. Questo approccio consente un controllo preciso sullo spessore del rivestimento ed è adatto a forme complesse.
- Rivestimento per maniche: Una manica in ceramica prefabbricata viene inserita nel tubo in acciaio e fissata con adesivi o aderenti. Questo metodo è efficiente per i gomiti standard e garantisce una superficie interna liscia.
Il tubo in acciaio è in genere formato dalla flessione o dalla saldatura a caldo, con opzioni senza soluzione di continuità preferite per applicazioni ad alta pressione. Post-allineamento, Il gomito subisce un trattamento termico per solidificare il legame in acciaio ceramico, Garantire la durata sotto stress operativi.
applicazioni
I gomiti foderati in ceramica sono schierati in una vasta gamma di settori a causa della loro versatilità e robustezza:
- produzione di energia: Utilizzato nelle piante a carbone per trasmettere carbone polverizzato, cenere, e liquame calcarea nei sistemi di desolforazione del gas di combustione.
- Data Mining: Gestisce i fanghi abrasivi, come sterili minerali e sabbia, nelle condutture di elaborazione minerale.
- metallurgia: Trasporta metallo fuso o scorie in ambienti ad alta temperatura.
- lavorazione chimica: Gestisce liquidi corrosivi e gas, beneficiare dell'inerzia chimica della ceramica.
- Industria del cemento: Trasmette clinker e materie prime, resistere all'usura da particelle abrasive.
Vantaggi
L'adozione di gomiti foderati in ceramica offre numerosi vantaggi:
- Durata utile estesa: Sopravvivono ai gomiti di acciaio tradizionali con un margine significativo, Ridurre la frequenza di sostituzione.
- Efficienza dei costi: I costi di manutenzione e tempi di inattività inferiori compensano l'investimento iniziale più elevato.
- Flusso migliorato: Le superfici ceramiche lisce riducono l'attrito e la perdita di pressione, Migliorare l'efficienza del sistema.
- Versatilità: Adatto per una vasta gamma di temperature, pressioni, e tipi di media.
- Installazione facile: Design leggero e compatibilità con le flange standard semplificano l'integrazione.
Limitazioni
Nonostante i loro vantaggi, I gomiti foderati in ceramica hanno alcuni svantaggi:
- Costo iniziale più elevato: L'uso di ceramiche e processi di produzione specializzati aumenta le spese anticipate rispetto ai gomiti in acciaio.
- fragilità: Il rivestimento in ceramica può rompersi sotto un'estrema shock meccanico se non supportato dallo strato in acciaio.
- Riparazioni complesse: I rivestimenti ceramici danneggiati sono difficili da riparare in loco, spesso richiede la sostituzione.
Recenti progressi
I recenti sviluppi nella tecnologia del gomito foderato in ceramica si sono concentrati sul miglioramento delle prestazioni e sulla riduzione dei costi:
- Ceramica avanzata: L'uso di ZTA e silicio in carburo (SiC) ha una resistenza migliorata e resistenza all'usura, Intervalli di applicazioni in espansione.
- Design dello zaino: L'aggiunta di una piastra in acciaio o uno "zaino" in ceramica nella curva esterna del gomito aumenta la resistenza all'usura nelle zone ad alto impatto.
- Piastrelle autobloccanti: I progetti di piastrelle innovativi con interblocco meccanico a 360 ° migliorano la resistenza al legame e riducono i rischi di delaminazione.
- Rivestimenti ibridi: La combinazione di ceramiche con polimeri o metalli crea rivestimenti ibridi che bilanciano il costo, tenacità, e resistenza all'usura.
Questi progressi riflettono gli sforzi in corso per ottimizzare i gomiti foderati in ceramica per condizioni industriali sempre più esigenti, Garantire che rimangono una soluzione preferita per applicazioni ad alta intensità di usura.
Conclusione
I gomiti foderati in ceramica sono una testimonianza della sinergia tra scienza dei materiali e ingegneria, Offrire resistenza all'usura senza pari, Resistenza alla corrosione, e stabilità termica. I loro parametri - che si lanciano dalla composizione materiale agli angoli di piegatura - possono essere adattati a soddisfare le esigenze operative specifiche, rendendoli una scelta versatile per le industrie in tutto il mondo. Mentre i loro costi iniziali più elevati e la fragilità pongono sfide, I vantaggi a lungo termine della riduzione della manutenzione e della durata di servizio estesa superano di gran lunga questi svantaggi. Con l’avanzare della tecnologia, I gomiti foderati in ceramica continueranno ad evolversi, solidificare il loro ruolo di pietra miliare dei moderni sistemi di tubazioni industriali.
Devi essere loggato per lasciare un commento.