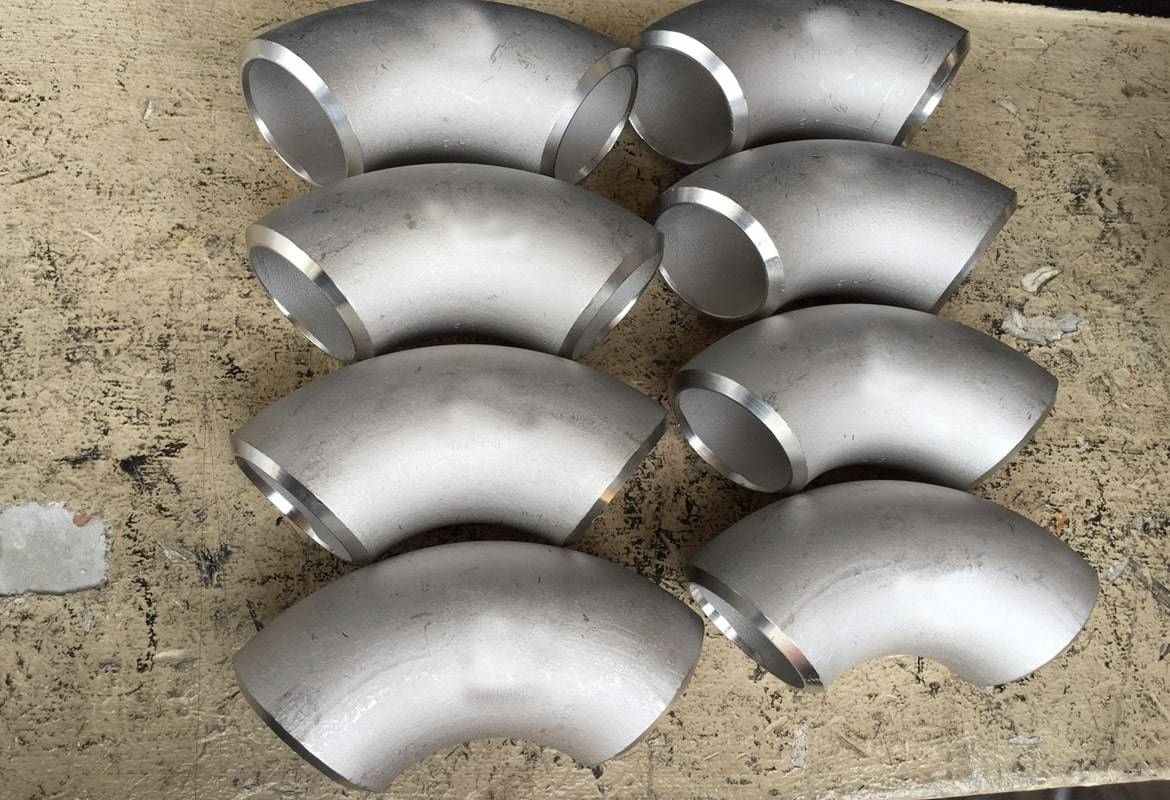
Exploring ASTM B366-WPNCMC-GR.1 SMLS Pipe Fittings: INCONEL ALLOY 625 N06625 Elbows, Tees, and Reducers According to ASME B16.9
Introduction
In the realm of industrial piping systems, the selection of appropriate materials and fittings is crucial for ensuring the efficiency, safety, and longevity of operations. Among the myriad of materials available, INCONEL ALLOY 625, designated as N06625, stands out due to its exceptional properties. This article delves into the specifics of ASTM B366-WPNCMC-GR.1 seamless (SMLS) pipe fittings, focusing on INCONEL ALLOY 625 elbows, tees, and reducers, all conforming to the ASME B16.9 standard. We will explore the material’s properties, applications, and the significance of adhering to these standards in industrial settings.
1. Understanding INCONEL ALLOY 625 (N06625)
1.1 Composition and Properties
INCONEL ALLOY 625 is a nickel-chromium-molybdenum alloy known for its high strength, excellent fabricability, and outstanding corrosion resistance. Its composition typically includes:
- Nickel (Ni): Approximately 58% minimum, providing the alloy with its corrosion resistance and high-temperature stability.
- Chromium (Cr): Around 20-23%, contributing to oxidation resistance.
- Molybdenum (Mo): About 8-10%, enhancing resistance to pitting and crevice corrosion.
- Niobium (Nb): 3.15-4.15%, which, along with molybdenum, imparts strength and stability.
These elements combine to give INCONEL 625 its unique properties, making it suitable for extreme environments.
1.2 Key Properties
- Corrosion Resistance: INCONEL 625 exhibits exceptional resistance to a wide range of corrosive environments, including seawater, acidic media, and oxidizing conditions.
- High-Temperature Stability: The alloy maintains its mechanical properties across a broad temperature range, from cryogenic to elevated temperatures.
- Strength and Toughness: It possesses high tensile, creep, and rupture strength, making it suitable for high-stress applications.
- Fabricability: The alloy is easily fabricated using conventional techniques, allowing for the production of complex shapes and fittings.
2. ASTM B366-WPNCMC-GR.1 SMLS Pipe Fittings
2.1 Overview of ASTM B366
ASTM B366 is a standard specification for factory-made wrought nickel and nickel alloy fittings. The designation WPNCMC-GR.1 refers to a specific grade of seamless pipe fittings made from INCONEL ALLOY 625. These fittings are designed to withstand high pressures and temperatures, making them ideal for demanding applications.
2.2 Seamless Pipe Fittings
Seamless (SMLS) pipe fittings are manufactured without a welded seam, providing superior strength and reliability compared to welded fittings. The absence of a seam eliminates potential weak points, ensuring the integrity of the fitting under high-pressure conditions.
2.3 Types of Fittings
- Elbows: Used to change the direction of flow in a piping system. Available in various angles, such as 45°, 90°, and 180°.
- Tees: Allow for the branching of a pipe system, facilitating the distribution of fluids.
- Reducers: Used to connect pipes of different diameters, ensuring a smooth transition and maintaining flow efficiency.
3. ASME B16.9 Standard
3.1 Importance of ASME B16.9
ASME B16.9 is a standard that specifies the dimensions, tolerances, and testing requirements for factory-made wrought butt-welding fittings. Adhering to this standard ensures that fittings are compatible with other components in a piping system, facilitating seamless integration and reliable performance.
3.2 Key Specifications
- Dimensions: The standard provides detailed dimensions for various types of fittings, ensuring consistency and compatibility across different manufacturers.
- Tolerances: Specifies acceptable deviations in dimensions, ensuring that fittings meet precise engineering requirements.
- Testing Requirements: Includes guidelines for testing the mechanical properties and integrity of fittings, ensuring their suitability for high-pressure applications.
4. Applications of INCONEL ALLOY 625 Fittings
4.1 Oil and Gas Industry
In the oil and gas sector, INCONEL 625 fittings are used extensively in offshore drilling, subsea pipelines, and refining operations. Their corrosion resistance and high-temperature stability make them ideal for handling hydrocarbons and corrosive fluids.
- Offshore Drilling: The harsh marine environment requires materials that can withstand seawater corrosion and high pressures. INCONEL 625 fittings provide the necessary durability and reliability.
- Refineries: In refineries, fittings are exposed to high temperatures and aggressive chemicals. INCONEL 625 ensures the integrity of piping systems, preventing leaks and failures.
4.2 Chemical Processing
Chemical plants rely on INCONEL 625 fittings to handle corrosive chemicals and high-temperature processes. The alloy’s resistance to a wide range of acids and bases makes it suitable for transporting aggressive media.
- Acid Production: In facilities producing sulfuric and hydrochloric acids, INCONEL 625 fittings prevent corrosion and maintain the purity of the product.
- Pharmaceutical Manufacturing: The alloy’s resistance to contamination and corrosion ensures the safe transport of sensitive chemicals.
4.3 Aerospace and Defense
In aerospace and defense applications, INCONEL 625 fittings are used in jet engines, exhaust systems, and other high-temperature components. Their strength and stability at elevated temperatures ensure the safe and efficient operation of critical systems.
- Jet Engines: The high-temperature stability of INCONEL 625 makes it suitable for use in jet engine components, where temperatures can reach extreme levels.
- Exhaust Systems: The alloy’s corrosion resistance ensures the longevity of exhaust systems exposed to high temperatures and corrosive gases.
5. Manufacturing Process of INCONEL 625 Fittings
5.1 Raw Material Selection
The manufacturing process begins with the selection of high-quality INCONEL 625 raw material. The composition and properties of the alloy are verified to ensure compliance with ASTM B366 specifications.
5.2 Forming and Shaping
The raw material is then formed and shaped into the desired fitting using various techniques, such as hot forging and extrusion. These processes ensure the uniformity and integrity of the fitting.
- Hot Forging: Involves heating the material to a high temperature and shaping it using a press or hammer. This process enhances the mechanical properties of the fitting.
- Extrusion: The material is forced through a die to create a seamless fitting with precise dimensions.
5.3 Heat Treatment
Heat treatment is applied to enhance the mechanical properties and corrosion resistance of the fitting. This process involves heating the fitting to a specific temperature and then cooling it at a controlled rate.
- Solution Annealing: The fitting is heated to a high temperature and then rapidly cooled to dissolve any precipitates and enhance corrosion resistance.
- Aging: The fitting is heated to a lower temperature and held for a specific time to enhance strength and toughness.
5.4 Machining and Finishing
The fitting is machined to achieve the final dimensions and surface finish. This process involves precision cutting, grinding, and polishing to meet the specifications outlined in ASME B16.9.
- Precision Cutting: Ensures the fitting meets the required dimensions and tolerances.
- Polishing: Provides a smooth surface finish, enhancing the fitting’s appearance and corrosion resistance.
5.5 Quality Control and Testing
Rigorous quality control measures are implemented to ensure the integrity and performance of the fitting. This includes non-destructive testing, dimensional inspection, and mechanical testing.
- Non-Destructive Testing (NDT): Techniques such as ultrasonic testing and radiography are used to detect any internal defects or discontinuities.
- Dimensional Inspection: Ensures the fitting meets the precise dimensions and tolerances specified in ASME B16.9.
- Mechanical Testing: Evaluates the tensile, yield, and impact strength of the fitting to ensure it meets the required specifications.
6. Challenges and Considerations
6.1 Cost
INCONEL 625 fittings are more expensive than those made from conventional materials. However, their long-term benefits, such as reduced maintenance and extended lifespan, often justify the initial investment.
- Cost-Benefit Analysis: A thorough analysis should be conducted to determine the feasibility of using INCONEL 625 fittings for a specific application.
- Return on Investment: The alloy’s durability and reliability contribute to a favorable return on investment over time.
6.2 Technical Expertise
The fabrication and installation of INCONEL 625 fittings require specialized technical expertise and equipment. Ensuring the proper selection of materials and adherence to standards is crucial for achieving optimal results.
- Training and Certification: Personnel involved in the manufacturing and installation process should receive appropriate training and certification to ensure quality and safety.
- Quality Assurance: Rigorous quality assurance measures should be implemented to ensure the integrity and performance of the fittings.
6.3 Compatibility
The compatibility of INCONEL 625 fittings with the operating environment and other system components should be carefully considered. Factors such as thermal expansion and galvanic corrosion must be addressed to prevent issues during service.
- Material Selection: The selection of compatible materials is essential for ensuring the long-term performance of the fittings.
- Environmental Considerations: The operating environment, including temperature, pressure, and chemical exposure, should be considered when selecting fittings.
Conclusion
INCONEL ALLOY 625 (N06625) fittings, including elbows, tees, and reducers, offer a range of advantages that make them an attractive choice for industrial piping systems. Their exceptional corrosion resistance, high-temperature stability, and mechanical strength ensure the reliable performance of piping systems in demanding environments. While the initial cost may be higher, the long-term benefits of reduced maintenance, extended lifespan, and improved reliability make INCONEL 625 fittings a cost-effective solution for many industries. Adhering to standards such as ASTM B366 and ASME B16.9 ensures the compatibility and performance of these fittings, facilitating seamless integration and reliable operation. As technology advances and the demand for durable materials grows, INCONEL 625 fittings are poised to play an increasingly important role in the future of industrial engineering.
You must be logged in to post a comment.