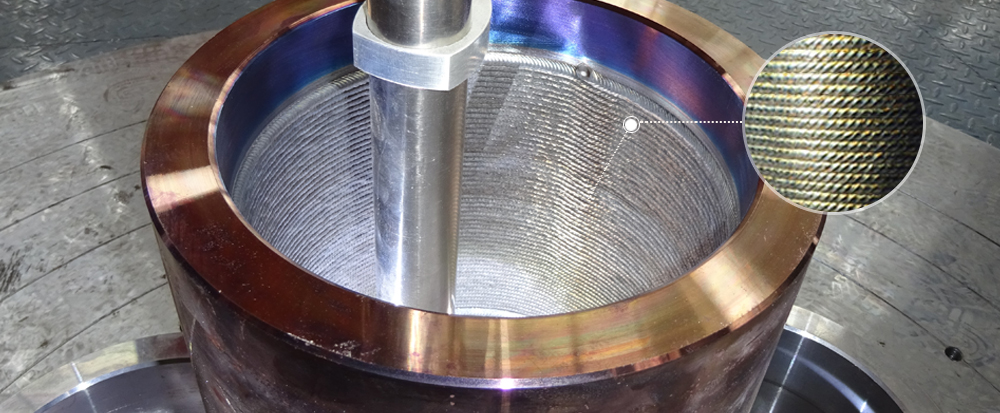
Penerapan pipa baja komposit berjajar dalam transportasi minyak dan gas bawah laut
Pengembangan ladang minyak dan gas lepas pantai harus memainkan peran penting dalam produksi industri dan pembangunan ekonomi sebagai jaminan energi yang penting bagi Tiongkok. Sebagai proses penting pengembangan lapangan minyak dan gas lepas pantai, transportasi minyak dan gas berkaitan dengan penggunaan sumber daya minyak dan gas. Karena adanya lebih banyak karbon dioksida, hidrogen sulfida dan gas lainnya dalam media minyak dan gas, baja karbon biasa dan bahan paduan yang dipilih oleh pipa sering kali menimbulkan korosi, mempengaruhi pekerjaan pengangkutan minyak dan gas serta mempengaruhi keselamatan pengangkutan; Dan berdasarkan karakteristik transportasi migas, pipa yang dipilih secara umum harus dapat memastikan bahwa tidak terjadi kegagalan korosi dan kebocoran di dalamnya 20 tahun, dan dapat memastikan bahwa pemeliharaan sesedikit mungkin atau tidak ada pemeliharaan selama pengoperasian. Oleh karena itu, sangat penting untuk memilih aplikasi pipa yang sesuai untuk transportasi minyak dan gas yang dikombinasikan dengan material dan proses yang ada untuk mencapai masalah korosi dan masalah penggunaan yang aman dalam jangka panjang.. Dikombinasikan dengan keunggulan pipa baja karbon dan pipa paduan, penggunaan BERJAJAR PIPA adalah solusi yang baik untuk masalah di atas, dan secara umum diyakini di dalam dan luar negeri bahwa pipa jenis ini merupakan bahan yang sangat baik untuk mengatasi masalah korosi transportasi minyak dan gas serta penggunaan jangka panjang., dan penelitian serta kemajuan spesifiknya adalah sebagai berikut.
1 Kemajuan penelitian dan analisis proses produksi utama pipa baja Clad Lined
Pipa baja komposit berjajar terutama terdiri dari tabung dasar dan tabung dalam. Diantaranya, pipa dasar terutama terdiri dari pipa baja karbon atau pipa baja paduan rendah, dan fungsinya terutama untuk menopang ban dalam dan ketahanan kompresi, sedangkan bahan utama lapisan dalam terbuat dari baja tahan karat, paduan besi-nikel dan bahan tahan korosi lainnya, dan fungsi utamanya adalah untuk menahan korosi pada pipa oleh zat korosif yang terkandung dalam media minyak dan gas untuk meningkatkan umur layanan pipa.; Untuk lapisan dalam, sesuai dengan karakteristik teknologi pengolahannya, itu juga bisa disebut lapisan kelongsong bagian dalam atau liner, dan struktur spesifiknya ditunjukkan pada Gambar 1.
Situasi saat ini yang komprehensif, Pipa baja komposit berjajar menurut pipa dasar dan lapisan dalam mode komposit material dapat dibagi menjadi komposit mekanis (melapisi pipa komposit) dan komposit metalurgi (pipa komposit bagian dalam), sesuai dengan standar American Petroleum Institute, teknologi pemrosesan dan pencetakan komposit mekanis utama adalah komposit hidrolik, komposit gambar dingin, komposit deflagrasi, dan lain-lain, dan komposit metalurgi terutama memiliki komposit ekstrusi panas, komposit canai panas, komposit pengecoran sentrifugal, dll. Proses spesifik serta kelebihan dan kekurangannya ditunjukkan pada Tabel 1.
Meja 1 Tabel perbandingan teknologi pemrosesan pipa baja komposit Berjajar Umum
kombinasi |
Klasifikasi proses |
Karakteristik proses |
Proses peracikan mekanis |
Senyawa hidrolik |
Kesesuaian yang rapat dicapai dengan memperluas liner dan pipa dasar secara hidraulik |
Komposit yang ditarik dingin |
Tabung liner disambung secara diametral ke permukaan bagian dalam tabung dasar dengan cara ekstrusi dan ekspansi melalui cetakan gambar |
|
senyawa deflagrasi |
Tekanan air di dalam pipa langsung meningkat karena ledakan bahan peledak, sehingga pipa pelapis dekat dengan permukaan bagian dalam pipa dasar, tekanan dilepaskan, pipa dasar berubah bentuk secara elastis dan memantul, dan deformasi plastis pada pipa pelapis menghasilkan peracikan. |
|
Proses komposit metalurgi |
Peracikan ekstrusi panas |
Permukaan kedua logam dibersihkan dan dirangkai menjadi billet yang diekstrusi, dan kedua logam tersebut dikontakkan secara rapat dan digabungkan pada suhu dan tekanan tertentu. |
komposit canai panas |
Proses produksi material komposit dengan cara pengerolan panas dua atau lebih material logam; kekuatan ikatan yang tinggi, efisiensi produksi yang tinggi, dan aplikasi yang luas |
|
komposit mematri |
Logam pengisi brazing ditempatkan di antara tabung kelongsong dan tabung dasar, dan Senyawa pemanas induksi berkelanjutan |
Dikombinasikan dengan karakteristik di atas, Tiongkok telah membuat kemajuan besar dalam penelitian dan pembuatan pipa baja komposit berjajar. Selama bertahun-tahun, berbagai produsen pipa telah banyak melakukan penelitian, seperti menambahkan sejumlah besar elemen paduan ke pipa logam, sehingga kekuatan dan ketahanan aus pipa dapat ditingkatkan secara signifikan. Secara umum, seperti Jepang, Amerika Serikat dan teknologi serta standar canggih lainnya, produksi pipa baja komposit berjajar di industri petrokimia dan industri nuklir telah digunakan, dan untuk memenuhi persyaratan pembangkit listrik dan pertambangan serta lingkungan dengan tingkat keausan tinggi lainnya. Pada waktu bersamaan, menurut laporan literatur, gulungan panas + proses pembentukan dingin yang dikembangkan dan diteliti di Jepang telah mewujudkan pemrosesan pipa baja komposit berjajar yang efektif, dengan teknologi unggul, kualitas yang dapat diandalkan, ketahanan korosi yang kuat dan ketahanan tekan, dan telah memainkan nilai besar dalam bahan kimia, ladang minyak dan gas.
2 Persyaratan kinerja pipa baja komposit berjajar dan analisis aplikasi
2.1 Penelitian tentang kebutuhan material dan sifat mekanik tabung dasar
Sesuai dengan persyaratan API 5LD-2015 Standar, baja karbon atau pipa baja seamless paduan rendah dipilih untuk pembuatan pipa baja komposit berjajar, dan dibuat dengan perlakuan panas, peregangan, proses squashing dan lainnya. Untuk pipa komposit berjajar, ditemukan bahwa uji tumbukan Charpy pada substrat sebelum memasang pipa pelapis dapat mewujudkan pemeriksaan pipa dasar dan memastikan kekuatan pipa.. Metode ini konsisten dengan tujuan uji drop hammer pada pipa dengan diameter lebih dari 508 mm dan grade baja X52 atau lebih tinggi yang disyaratkan oleh standar API5LD-2015., dan penggunaan metode pengujian ini dapat secara efektif memastikan kinerja pipa. namun, untuk beberapa aplikasi dengan ketahanan korosi yang lebih kuat dan peringkat tekanan yang lebih tinggi, Amerika Serikat telah mengajukan persyaratan uji kinerja tarik suhu tinggi dalam penelitian ini, dan Tiongkok juga telah menerapkan hal ini. Misalnya, dalam pemilihan pipa Guangzhou Panyu 35-1/35-2 ladang minyak dan gas, uji kinerja tarik suhu tinggi diusulkan, dan pipa seamless X65 yang dipilih di ladang minyak dan gas mensyaratkan bahwa pipa tersebut harus tahan terhadap persyaratan tidak ada retakan pada 419MPa pada 103 ° C. Terlihat bahwa pemilihan pipa di ladang minyak dan gas Tiongkok serta ladang tahan korosi dan tekanan tinggi lainnya telah memperkuat pembatasan persyaratan material untuk pipa dasar., menjamin kualitas pipa dan keamanan media transportasi.
2.2 Analisis dan studi penggunaan material pipa dan ketahanan korosi pada lapisan dalam pipa dasar
Lapisan lapisan pipa baja komposit berjajar bersentuhan langsung dengan media pengangkut, dan kinerja anti korosinya merupakan indikator penting, yang harus dipertimbangkan sepenuhnya dalam pemilihan material. Misalnya, Persyaratan standar API5LD-2015 dengan jelas menetapkan bahan yang digunakan untuk lapisan pelapis pipa baja komposit berjajar, termasuk baja tahan karat dan bahan paduan tahan korosi, seperti baja tahan karat austenitik, paduan feronikel dan sebagainya. Untuk pemilihan bahan tersebut, setiap pabrikan dan pabrikan pipa harus memilih material yang sesuai yang dikombinasikan dengan kondisi spesifik media pengangkut untuk memastikan bahwa sifat kimia dan sifat mekaniknya memenuhi persyaratan standar API5LD-2015. Misalnya, lapisan lapisan dalam yang dipilih oleh Perusahaan Ladang Minyak dan Gas Yacheng adalah pipa baja komposit berlapis dari paduan besi-nikel, yang secara efektif menjamin korosi pada pipa oleh zat CO2 dan H2S yang terkandung dalam media minyak dan gas.
Berdasarkan pertimbangan di atas, pemilihan lapisan pelapis sesuai dengan jenis media pengangkut dan tingkat kekerasan korosi adalah kuncinya, seperti kebutuhan material lapisan pelapis di SY/T 6855-2012 Standar, seperti ketentuan yang mengharuskan lapisan lapisan logam dasar dan pengelasan harus memenuhi ketentuan SNI 15156-2015, dan harus mampu memiliki sifat retak tegangan belerang dan retak korosi; Pada waktu bersamaan, Ditegaskan bahwa pemilihan material harus dipertimbangkan sesuai dengan parameter medium, suhu dan tekanan untuk memastikan kinerja dan persyaratannya.
2.3 Persyaratan kinerja lainnya dan kemajuan penelitian pipa baja Clad Lined s
Untuk pipa komposit, kekuatan rekat antara lapisan dalam dan lapisan luar adalah kuncinya, tetapi juga termasuk dalam indikator kinerja penting dari pipa komposit, penerapan dan pemrosesan sebenarnya harus diukur dengan cara yang tepat, seperti standar API5LD-2015 untuk memperjelas persyaratan kekuatan ikatan, menunjukkan penggunaan uji kuat geser standar ASTM A264-2012, untuk memastikan bahwa kekuatan ikatan memenuhi persyaratan. Sesuai dengan persyaratan standar, pengujian harus dilakukan dalam beberapa batch 50 pipa baja untuk memastikan kinerjanya. namun, untuk pipa yang diproses dengan proses komposit mekanis, ada celah makroskopis antara lapisan pelapis dan pipa dasar, seperti jika celah tersebut tercampur dengan udara atau kotoran, itu akan berdampak serius pada keketatannya. Misalnya, ditemukan dalam penelitian bahwa ketika suhu media pembawa terlalu tinggi, koefisien muai pipa dasar dan liner berbeda, yang mudah menyebabkan ketidakstabilan liner, dan lain-lain, yang dapat menyebabkan keruntuhan dan penonjolan pada kasus yang parah, yang akan mempengaruhi media transportasi. Untuk permasalahan di atas, para sarjana menggunakan perhitungan elemen hingga untuk menyesuaikan parameter proses komposit dalam penelitian ini, yang secara efektif memecahkan pemisahan lembu jantan dan liner bersuhu tinggi. Sebagai tambahan, ketika berbagai jenis logam digunakan untuk pipa dasar dan pelapis, proses operasi pengelasan harus memastikan ketahanan korosi pada lapisan lapisan dan lapisan kelongsong bagian dalam, dan sifat mekanik pipa dasar harus dipertimbangkan, dan kesulitan pengelasan lebih besar. Untuk ini, para sarjana menggunakan kawat las paduan rendah dalam penelitian ini, karena potensial elektrokimia pada dasarnya sama, las tidak terlalu terpengaruh oleh korosi, yang tidak hanya mengurangi biaya pengelasan, tetapi juga menghindari retaknya lapisan las transisi, yang memiliki nilai penerapan tertentu dalam produksi aktual.
3 Penerapan dan analisis ekonomi pipa baja Clad Lined dalam transportasi minyak dan gas bawah laut
3.1 Penelitian penerapan pipa baja komposit berjajar pada transportasi minyak dan gas bawah laut
Pipa baja komposit berjajar memiliki sifat mekanik dan ketahanan korosi yang sangat baik, dan bahan yang sesuai harus dipilih dalam pemilihan pipa yang dikombinasikan dengan kondisi tertentu untuk memastikan penghematan logam mulia dan mengurangi biaya, dan meningkatkan kepadatan efisiensi. Material pipa baja komposit berjajar yang dipilih di ladang minyak dan gas asing telah tercapai 200,000 Ton, seperti pipa komposit paduan Cu-Ni yang digunakan oleh perusahaan NKK Jepang memiliki ketahanan korosi yang kuat dan kemampuan las untuk air laut, dan banyak digunakan dalam pipa pengantar sistem desalinasi air laut. Pada waktu bersamaan, penerapan 316L sebagai pipa baja komposit berlapis di ladang minyak Tarim Tiongkok telah memainkan peran positif dalam memastikan transportasi minyak dan gas, mengurangi jumlah perbaikan dan pemeliharaan, dan memastikan manfaat ekonomi perusahaan. namun, Secara umum, masih terdapat kekurangan dalam penerapannya, seperti pipa dasar, standar API 5LD-2015 saat ini menetapkan persyaratan minimum yang harus dipenuhi oleh pipa baja komposit berjajar, namun dikarenakan perbedaan zat korosif dan konsentrasi yang terkandung pada media transportasi lain seperti minyak dan gas, tingkat korosinya berbeda-beda, dan pengangkutan beberapa zat tidak dapat menjamin keamanannya; Sebagai tambahan, indeks ketangguhan pipa dasar merupakan persyaratan penting dari pipa dasar, dan standar yang berlaku saat ini tidak ditetapkan dengan jelas, dan mungkin ada risiko keamanan tertentu. Dalam hal lapisan, standar saat ini tidak mencantumkan bahan yang digunakan dalam lingkungan CO2 dan H2S, dan korosivitas adalah kunci masa pakai material tersebut; Oleh karena itu, pemilihan sebenarnya harus berupa analisis kondisi kerja dan kondisi lingkungan yang komprehensif untuk memastikan pemilihan material dan keamanan penggunaan.
3.2 Analisis keuntungan ekonomi pipa baja komposit berjajar dalam aplikasi transportasi minyak dan gas bawah laut
Dari media transportasi migas lepas pantai saat ini, langkah-langkah pengendalian media korosi pipa terutama mencakup kategori berikut: Pertama, inhibitor korosi ditambahkan ke pipa baja karbon; Kedua, penggunaan bahan pelapis bagian dalam; Ketiga, penggunaan bahan stainless steel dan tahan korosi; Keempat, penggunaan berpakaian berjajar tabung baja komposit. Dengan cara-cara di atas, inhibitor korosi akan mempengaruhi efisiensi karena perubahan media di dalam tabung, dan biaya material dan tenaga kerja tinggi; Teknologi pengikatan pada tempat pengelasan lapisan dalam tidak sempurna, dan ada risiko tertentu; Baja tahan karat mahal dan memiliki risiko ekonomi yang besar dalam aplikasi ladang minyak dan gas lepas pantai. Pipa baja komposit berjajar memiliki kekuatan mekanik dan kinerja korosi yang kuat, memiliki keuntungan yang jelas, dan memiliki nilai penerapan tertentu. Ditinjau dari analisis manfaat ekonominya, meskipun biaya penggunaan pipa baja komposit berjajar lebih tinggi, biaya pemeliharaan lebih sedikit pada tahap selanjutnya, dan itu aman dan dapat diandalkan, dibandingkan dengan ketiga skema di atas, biaya investasinya lebih kecil, terutama bila manfaat ekonominya semakin nyata setelah masa penggunaan terlampaui 10 tahun. Pada waktu bersamaan, proses dan bahan pembuatan pipa baja komposit berjajar berbeda, dan perbedaan nilainya juga besar, seperti harga pipa baja komposit berjajar yang umum saat ini 7000 ~ 25000 dolar AS / Ton, perbedaan harga lebih besar. Oleh karena itu, dalam transportasi pipa setiap ladang minyak dan gas lepas pantai, lingkungan korosi yang sesuai harus digabungkan untuk memastikan penggunaan jangka panjang yang andal, dan lapisan lapisan yang ekonomis harus dipilih untuk memastikan ketahanan terhadap korosi dan memenuhi persyaratan ekonomi, dan untuk memastikan transportasi media yang aman.
4 Kesimpulan
Singkatnya, Pipa baja komposit berjajar memiliki nilai penting dalam transportasi minyak dan gas laut. Saat ini, Teknologi pipa baja komposit berlapis Tiongkok telah mengalami kemajuan besar, namun masih ada kesenjangan tertentu antara beberapa bidang dan tingkat internasional. Untuk memastikan pengembangan teknologi manufaktur pipa baja komposit berjajar Tiongkok, negara dan perusahaan harus mengambil langkah-langkah efektif untuk meresponsnya, meningkatkan investasi dalam penelitian dan pengembangan, dan menyempurnakan produk pendukungnya, seperti pengembangan berbagai jenis aksesoris, dan lain-lain, untuk mencapai nasionalisasi materi terkait, mengurangi monopoli produk luar negeri, untuk memastikan pengembangan dan penerapan teknologi manufaktur pipa baja komposit berjajar Tiongkok.
Kamu harus login untuk mengirim komentar.