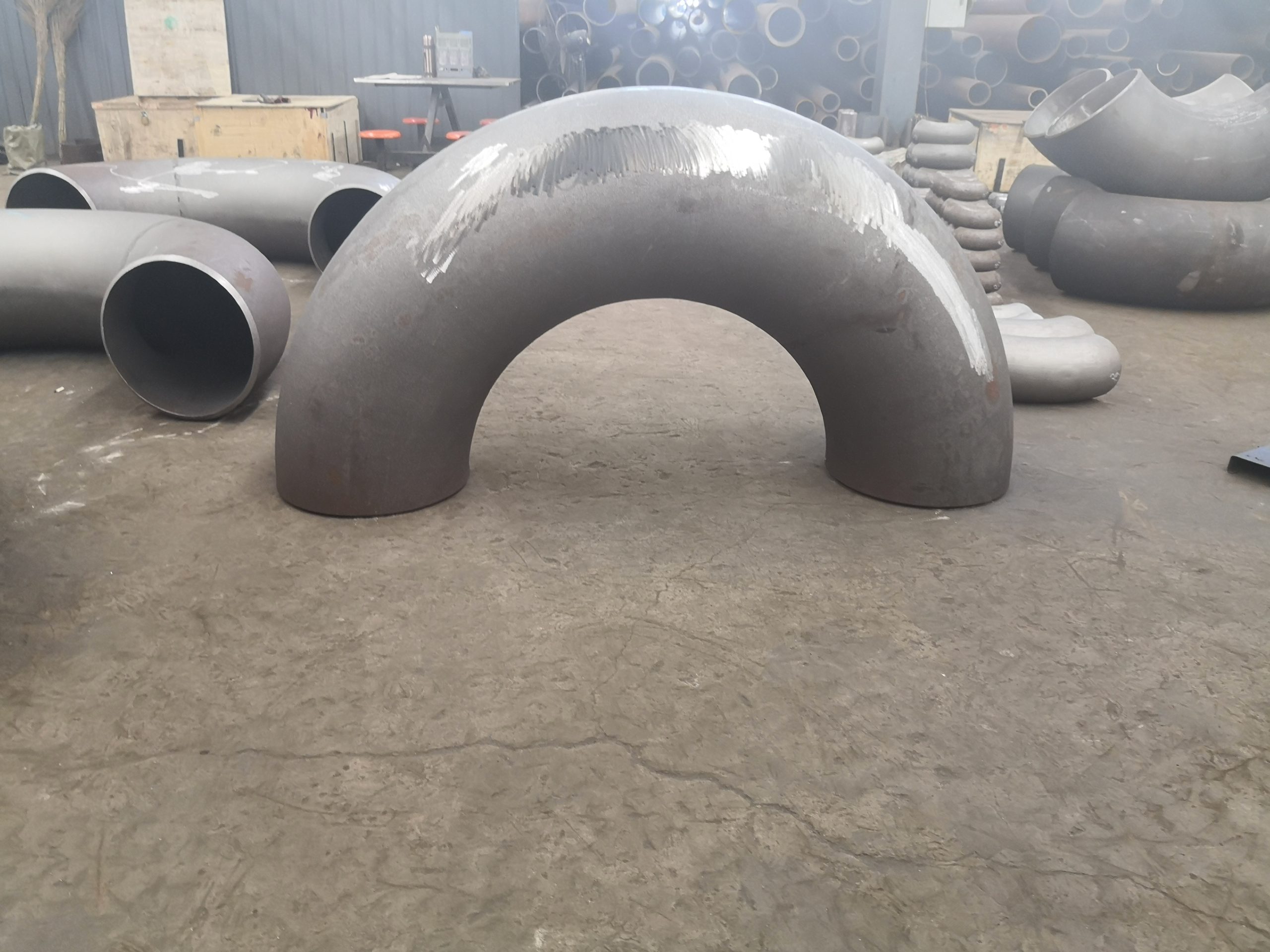
Butt welding fittings, such as those complying with the ASTM A234 standard, are produced through a series of steps that involve the shaping, heating, and cooling of metal. Here is a general overview of the process:
-
Procurement of Raw Material: The raw material, often in the form of a billet or a plate of carbon steel or alloy steel, is procured.
-
Cutting: The raw material is cut to the size of the fitting to be produced. For example, for an elbow, the material is cut to a length that is somewhat larger than the final product will be.
-
Heating: The cut piece of metal is heated until it reaches a malleable state. This is typically done in a furnace.
-
Shaping: Once the metal is malleable, it is shaped into the desired form. For some fittings, such as elbows and bends, this involves using a die of the appropriate shape.
-
For seamless fittings, the heated and malleable billet is pushed over a die, also termed as ‘mandrel’ which starts to shape the billet into an elbow, while the billet is being pushed, it is simultaneously being stretched as well.
-
For welded fittings, a plate is pressed into the shape of a half elbow (or other fitting). Two of these pieces are then welded together to form the complete fitting.
-
-
Heat Treatment: After the fitting has been shaped, it is heat-treated to enhance its mechanical properties. This usually involves heating it to a specific temperature and then cooling it at a controlled rate to achieve the desired hardness and strength.
-
Finishing: The fitting is then finished. This can involve processes like sand blasting, painting, galvanizing, or coating, depending on the requirements of the final product.
-
Inspection and Testing: The final step involves inspecting and testing the fitting to ensure it meets all relevant specifications and standards. This can include visual inspections, dimensional checks, tensile tests, hardness tests, and impact tests.
Please note that the specific production process can vary based on the type of fitting being produced, the specific material being used, and the manufacturer’s production methods. Always refer to the manufacturer’s guidelines or the relevant standards for the most accurate information.
information about the heat treatment process for butt welding fittings
Heat treatment is an important step in the manufacturing process of butt welding fittings because it significantly enhances the mechanical properties of the fittings, such as hardness, toughness, and resistance to wear. Here are the main stages of the heat treatment process:
-
Austenitizing: This is the first stage of the heat treatment process. In this stage, the steel fitting is heated to a temperature at which the steel becomes austenitic. The exact temperature can vary depending on the specific grade of steel, but it is generally between 815-870 °C (1500-1600 °F) for carbon and low-alloy steels. The purpose of this stage is to prepare the steel for the subsequent quenching process.
-
Quenching: After austenitizing, the steel fitting is rapidly cooled, or “quenched.” This is usually done by immersing the steel in a quenching medium, such as water, oil, or air. Quenching causes the austenitic steel to transform into martensite, which is a hard and brittle phase of steel.
-
Tempering: Quenched steel is very hard, but it’s also brittle. To improve its toughness and reduce its brittleness, the steel is then reheated to a lower temperature (typically between 205-650 °C, or 400-1200 °F) in a process known as tempering. The exact temperature and duration of the tempering process depend on the desired balance of hardness and toughness. After the steel has been tempered, it is cooled slowly to room temperature.
Some important points to remember about the heat treatment process:
-
The heat treatment process must be carefully controlled to ensure that the steel achieves the desired properties. Factors such as the heating rate, soaking time, cooling rate, and the temperatures used for austenitizing and tempering can all affect the final properties of the steel.
-
After heat treatment, the steel fittings should be inspected and tested to ensure that they meet the required specifications. This can involve hardness testing, impact testing, and other types of tests.
-
Heat treatment can cause some distortion of the steel fittings, so they may need to be straightened or otherwise reworked after heat treatment.
This is a typical heat treatment process for steel butt welding fittings, but the exact process can vary depending on the specific grade of steel and the requirements of the final product. Always refer to the relevant standards or the manufacturer’s guidelines for the most accurate information.
You must be logged in to post a comment.