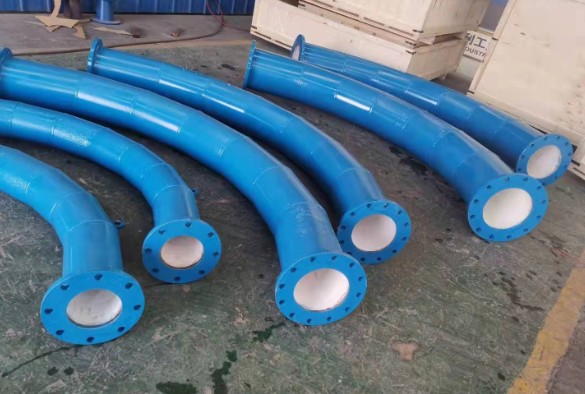
Codo forrado de cerámica: Análisis completo
Los codos forrados de cerámica son componentes críticos en los sistemas de tuberías industriales, diseñado para manejar abrasivo, corrosivo, y materiales de alta temperatura. Estos codos combinan la durabilidad del acero con el desgaste excepcional y la resistencia a la corrosión de los revestimientos de cerámica, haciéndolos indispensables en industrias como la generación de energía, La minería de, Metalurgia, y procesamiento químico. Este documento proporciona un análisis en profundidad de los codos forrados de cerámica, incluyendo una tabla de parámetros, Composición de material, Propiedades mecánicas, Resistencia al desgaste, ángulos de flexión, y una discusión detallada de su desempeño y aplicaciones.
Tabla de parámetros
Parámetro | Descripción | Valores típicos |
---|---|---|
Material de la tubería exterior | Material base del codo | Acero al carbono (por ejemplo, 20# acero sin costura), Acero inoxidable |
Material de revestimiento de cerámica | Material de revestimiento interno | Alúmina (Al₂O₃, ≥90%), Alúmina endurecida por circonio (ZTA) |
Diámetro de la tubería | Diámetro interno de la tubería | 0.5 pulgada a 24 pulgadas (personalizable) |
Espesor cerámico | Grosor del revestimiento de cerámica | 6 mm – 25 mm |
Ángulo de flexión | Cambio de ángulo de dirección | 22.5°, 45°, 90°, 180° (ángulos personalizados disponibles) |
De la curva Radio | Radio de curvatura | 1.5D – 5D (D = diámetro de la tubería) |
Temperatura de funcionamiento | Resistencia a la temperatura máxima | -50° C a 900 ° C (a largo plazo), hasta 2000 ° C (Corto plazo) |
Resistencia a la presión | Fuerza de aro | 300 – 500 MPa |
Resistencia al desgaste | En relación con el acero al carbono | 15 – 20 veces más alto |
Microdoridad | Dureza del revestimiento de cerámica | alto voltaje 1000 – 1600 |
Densidad | Densidad de revestimiento de cerámica | 3.62 g/cm³ (Alúmina) |
vida de servicio | Vida útil esperada en condiciones abrasivas | 5 – 20 años (Dependiendo de la aplicación) |
Composición de material
Los codos forrados de cerámica consisten en dos capas de material principal: la tubería de acero exterior y el revestimiento de cerámica interior. La tubería exterior está hecha generalmente de acero al carbono. (por ejemplo, 20# acero sin costura) o acero inoxidable, proporcionar integridad estructural y facilidad de soldadura o brida. El revestimiento de cerámica, generalmente compuesto por alúmina de alta pureza (Al₂O₃) o alúmina endurecida por zirconia (ZTA), se une a la superficie interna utilizando adhesivos resistentes a la temperatura o técnicas de enclavamiento mecánicos.
Material de la tubería exterior
La tubería exterior sirve como la columna estructural del codo. El acero al carbono se usa comúnmente debido a su rentabilidad, alta resistencia, y soldabilidad. Para aplicaciones que involucran entornos corrosivos, Se puede preferir acero inoxidable para mejorar la resistencia a la corrosión. La capa de acero asegura que el codo pueda soportar tensiones mecánicas, como presión e impacto, mientras facilita la integración en los sistemas de tuberías existentes.
Material de revestimiento de cerámica
El revestimiento de cerámica es la clave del rendimiento excepcional del codo. Alúmina, con un contenido de Al₂o₃ de 90% o más alto, es el material más utilizado debido a su alta dureza, Resistencia al desgaste, y estabilidad térmica. Alúmina endurecida por circonio (ZTA) es una variante avanzada que ofrece una resistencia mejorada y resistencia al impacto, haciéndolo adecuado para sistemas dinámicos con alto shock mecánico. La capa de cerámica se aplica típicamente como fichas, mangas, o un revestimiento monolítico, Dependiendo del proceso de fabricación.
La estructura de grano fino del material cerámico y la alta densidad contribuyen a su durabilidad. por ejemplo, La cerámica de alúmina exhibe una dureza similar a un diamante y una resistencia mecánica superior, haciéndolos ideales para aplicaciones exigentes. La elección del material cerámico se puede adaptar a requisitos operativos específicos, como abrasión extrema o exposición química.
Propiedades mecánicas
Las propiedades mecánicas de los codos forrados de cerámica son un compuesto de la capa externa de acero y el revestimiento interno de cerámica. Estas propiedades determinan la capacidad del codo para resistir la presión, Impacto, y choque térmico, Asegurar un rendimiento confiable en entornos duros.
fuerza
La fuerza del aro de los codos forrados de cerámica, que mide la resistencia a la presión radial, típicamente varía de 300 a 500 MPa. Esta resistencia se deriva principalmente de la capa exterior de acero, que proporciona soporte estructural. El revestimiento de cerámica, mientras quebradiza, contribuye a la integridad general al resistir la degradación de la superficie y mantener la forma del codo en condiciones abrasivas.
Resistencia a la flexión, o fuerza de flexión, es una propiedad crítica para el revestimiento de cerámica. Cerámica de alúmina exhibir alta resistencia a la flexión, a menudo probado a través de pruebas de flexión de 3 puntos o 4 puntos. Los valores pueden exceder 300 MPa, Dependiendo del tamaño de grano, porosidad, y fabricación calidad. sin embargo, La fragilidad de la cerámica significa que se basa en la capa de acero para absorber las tensiones de flexión sin agrietarse.
Dureza
La microdureza del revestimiento de cerámica, medido en la escala de Vickers, rangos de HV 1000 a 1600 Para materiales a base de alúmina. Esta dureza es significativamente mayor que la del acero al carbono. (aproximadamente HV 150-200 Después de enfriar) o incluso el carburo de tungsteno (alto voltaje 1200-1500), Hacer la capa de cerámica excepcionalmente resistente al rascado y al desgaste. La alta dureza asegura que el codo pueda manejar materiales abrasivos como el polvo de carbón, ceniza, o lechada de mineral sin daños de superficie significativos.
Resistencia a la dureza y el impacto
Mientras que la cerámica de alúmina es inherentemente frágil, Su resistencia se puede mejorar utilizando ZTA o optimizando la unión con la capa de acero. La tubería exterior de acero proporciona una excelente resistencia al impacto, absorber choques mecánicos que de otro modo podrían fracturar el revestimiento de cerámica. En la práctica, Los codos forrados de cerámica han demostrado resiliencia en aplicaciones que involucran impactos de partículas de alta velocidad, tales como sistemas de transmisión neumática.
Resistencia a choque térmico
Los codos forrados de cerámica pueden funcionar en temperaturas que van desde -50 ° C a 900 ° C durante períodos prolongados, con resistencia a corto plazo de hasta 2000 ° C. El coeficiente de expansión térmica baja del forro de cerámica minimiza el agrietamiento bajo rápidos cambios de temperatura, mientras que la capa de acero proporciona estabilidad adicional. Esta resistencia al choque térmico es crucial en industrias como la generación de energía, donde las tuberías pueden experimentar temperaturas fluctuantes.
Resistencia al desgaste
La resistencia al desgaste es la característica definitoria de los codos forrados de cerámica, Darles aparte de los accesorios tradicionales de acero o de hierro fundido. La capacidad del forro de cerámica para resistir la abrasión y la erosión extiende la vida útil del codo por 15 a 20 tiempos en comparación con los codos de acero al carbono sin forro, Reducir los costos de mantenimiento y el tiempo de inactividad.
Mecanismo de resistencia al desgaste
La alta dureza y la superficie lisa del revestimiento de cerámica minimizan la pérdida de material debido al desgaste abrasivo. En aplicaciones que involucran slorns o polvos de alta velocidad (por ejemplo, ceniza de carbón, caliza, o arena), La capa de cerámica resiste la erosión reduciendo la fricción y evitando el incrustación de partículas. La resistencia al desgaste se cuantifica comparando el rendimiento del forro de cerámica con el de acero al carbono, con estudios que muestran un aumento de la vida útil de hasta 20 tiempos en condiciones abrasivas.
El factor de baja fricción de la cerámica a ángulos de bajo impacto mejora aún más la resistencia al desgaste al reducir el impacto abrasivo de las partículas. Esta propiedad es particularmente beneficiosa en los codos, donde los cambios en la dirección del flujo aumentan la turbulencia y el desgaste. La superficie interna lisa también previene la acumulación de material., Asegurar tasas de flujo consistentes y reducir el riesgo de bloqueos.
Análisis comparativo
En comparación con otros materiales resistentes al desgaste, como basalto fundido o acero de aleación, Los revestimientos de cerámica ofrecen un rendimiento superior. Fundir basalto, aunque duradero, tiene una menor resistencia al desgaste y es propensa a agrietarse bajo impactos de alta velocidad. Acero de aleación, con una dureza superficial de aproximadamente 60 HRC, se desgasta más rápido que la cerámica (80+ HRC equivalente). En aplicaciones del mundo real, tales como plantas de energía a carbón, Los codos forrados de cerámica han sobrevivido a los codos de acero de paredes gruesas por un factor de cinco o más.
vida de servicio
La vida útil de un codo forrado de cerámica depende de la gravedad de la aplicación. En sistemas de transmisión neumática para cenizas volantes o cemento, donde la abrasión es intensa, El revestimiento de cerámica puede durar 5 a 10 años, en comparación con 1-2 Años para los codos de acero. En condiciones menos abrasivas, como el procesamiento químico, la vida útil puede exceder 20 años. La tasa de desgaste promedio de la capa de cerámica es aproximadamente 0.5-1 mm por año, que significa un 6 El revestimiento de mm podría durar 5 años en entornos exigentes.
ángulos de flexión
Los codos forrados de cerámica están disponibles en varios ángulos de flexión para acomodar diferentes diseños de tuberías. El ángulo determina el grado de cambio de dirección, Afectando la dinámica del flujo y los patrones de desgaste dentro del codo.
Ángulos de flexión estándar
Los ángulos de flexión más comunes son 22.5 °, 45°, 90°, y 180°, Aunque se pueden fabricar ángulos personalizados para cumplir con los requisitos específicos. Estos ángulos corresponden al estándar instalación de tuberías diseños:
- 22.5° Codo: Utilizado para ajustes direccionales ligeros en los sistemas de tuberías.
- 45° Codo: Proporciona un cambio moderado en la dirección, Turbulencia reductora en comparación con los codos de 90 °.
- 90° Codo: El ángulo más utilizado para giros perpendiculares, Común en diseños ajustados.
- 180° Codo: Una curva de retorno para revertir la dirección del flujo, a menudo se usa en intercambiadores de calor o sistemas compactos.
Radio de curvatura
El radio de la curva, típicamente expresado como un múltiplo del diámetro de la tubería (D), varía de 1.5d a 5d. Un radio más grande (por ejemplo, 5D) Resulta en una curva más suave, Reducción de la resistencia al flujo y la concentración de desgaste en la curva. Codos de radio corto (1.5D) son más compactos pero experimentan un mayor desgaste debido a giros más nítidos. La elección del radio depende de las limitaciones de espacio, requisitos de flujo, y usar consideraciones.
Impacto en el rendimiento
El ángulo de flexión y el radio influyen significativamente en el rendimiento del codo. Ángulos más nítidos (por ejemplo, 90°) y radios más pequeños aumentan la turbulencia y el impacto de las partículas, desgaste acelerando en la curva exterior. Los revestimientos de cerámica mitigan esto proporcionando un duro, superficie lisa que desvía partículas abrasivas. En contraste, Los radios más grandes y los ángulos más pequeños distribuyen el desgaste de manera más uniforme, Mejora de la longevidad.
Análisis detallado
Los codos forrados de cerámica representan una fusión de materiales avanzados y diseño de ingeniería, personalizado para abordar los desafíos del transporte de material abrasivo y corrosivo. Esta sección explora sus procesos de fabricación, Aplicaciones, Ventajas, Limitaciones, y avances recientes, Proporcionar una comprensión holística de su papel en la industria moderna.
procesos de manufactura
Los codos forrados de cerámica se producen utilizando varias técnicas, cada uno influye en su rendimiento y costo:
- Fundición centrífuga: La alúmina fundida se lanza dentro de una tubería de acero bajo fuerza centrífuga, formando un denso, capa de cerámica uniforme. Este método garantiza una alta resistencia de unión y es ideal para codos de gran diámetro.
- Revestimiento de baldosas: Las baldosas de cerámica preformadas se adhieren a la superficie interna de la tubería de acero utilizando adhesivos de alta temperatura o entrelazamiento mecánico. Este enfoque permite un control preciso sobre el grosor del revestimiento y es adecuado para formas complejas..
- Revestimiento de la manga: Se inserta una manga de cerámica prefabricada en la tubería de acero y se asegura con adhesivos o ajustados. Este método es eficiente para los codos estándar y garantiza una superficie interna lisa.
La tubería de acero se forma típicamente mediante flexión o soldadura en caliente, con opciones perfectas preferidas para aplicaciones de alta presión. Posterior a, El codo sufre tratamiento térmico para solidificar el enlace de acero de cerámica, Asegurar la durabilidad bajo tensión operativa.
Aplicaciones
Los codos forrados de cerámica se implementan en una amplia gama de industrias debido a su versatilidad y robustez:
- Generación de energía: Utilizado en plantas de carbón para transmitir carbón pulverizado, ceniza, y lactancia de piedra caliza en sistemas de desulfuración de gases de combustión.
- La minería de: Maneja lloses abrasivos, como relaves de mineral y arena, En tuberías de procesamiento de minerales.
- Metalurgia: Transporta metal fundido o escoria en entornos de alta temperatura.
- Procesamiento químico: Administra líquidos y gases corrosivos, beneficiarse de la inercia química de la cerámica.
- Industria del cemento: Transmite clinker de cemento y materias primas, resistir el desgaste de las partículas abrasivas.
Ventajas
La adopción de codos forrados de cerámica ofrece numerosos beneficios:
- Vida útil extendida: Hacer más tiempo los codos de acero tradicionales por un margen significativo, Reducción de la frecuencia de reemplazo.
- Rentabilidad: Los costos de menor mantenimiento y tiempo de inactividad compensan la mayor inversión inicial.
- Flujo mejorado: Las superficies cerámicas suaves reducen la fricción y la pérdida de presión, Mejorar la eficiencia del sistema.
- Versatilidad: Adecuado para una amplia gama de temperaturas, presiones, y tipos de medios.
- Fácil instalación: Diseño liviano y compatibilidad con bridas estándar simplifican la integración.
Limitaciones
A pesar de sus ventajas, Los codos forrados de cerámica tienen algunos inconvenientes:
- Mayor costo inicial: El uso de cerámica y procesos de fabricación especializados aumenta los gastos por adelantado en comparación con los codos de acero.
- fragilidad: El revestimiento de cerámica puede agrietarse bajo un choque mecánico extremo si no es soportado por la capa de acero.
- Reparaciones complejas: Los revestimientos de cerámica dañados son difíciles de reparar en el sitio, a menudo requiere reemplazo.
Avances recientes
Los desarrollos recientes en la tecnología de codo forrado de cerámica se han centrado en mejorar el rendimiento y reducir los costos:
- Cerámica avanzada: El uso de ZTA y el carburo de silicio (Sic) ha mejorado la dureza y la resistencia al desgaste, Expandir rangos de aplicaciones.
- Diseño de mochila: Agregar una placa de acero o una "mochila" de cerámica en la curva exterior del codo aumenta la resistencia al desgaste en zonas de alto impacto.
- Azulejos automáticos: Diseños innovadores de baldosas con 360 ° Interlucking mecánico Mejoran la fuerza de unión y reducen los riesgos de delaminación.
- Revestimiento híbrido: La combinación de cerámica con polímeros o metales crea revestimientos híbridos que equilibran el costo, Dureza, y resistencia al desgaste.
Estos avances reflejan los esfuerzos en curso para optimizar los codos forrados de cerámica para condiciones industriales cada vez más exigentes, Asegurarse de que sigan siendo una solución preferida para aplicaciones intensivas.
Conclusión
Los codos forrados de cerámica son un testimonio de la sinergia entre la ciencia de los materiales y la ingeniería, ofreciendo resistencia al desgaste inigualable, Resistencia a la corrosión, y estabilidad térmica. Sus parámetros, que van desde la composición del material hasta los ángulos de flexión, se pueden adaptar para satisfacer las necesidades operativas específicas, haciéndolos una elección versátil para las industrias de todo el mundo. Mientras que su mayor costo inicial y fragilidad plantean desafíos, Los beneficios a largo plazo del mantenimiento reducido y la vida útil prolongada superan con creces estos inconvenientes. A medida que avanza la tecnología, Los codos forrados de cerámica continuarán evolucionando, solidificar su papel como piedra angular de los sistemas de tuberías industriales modernas.
Debes ser identificado introducir un comentario.