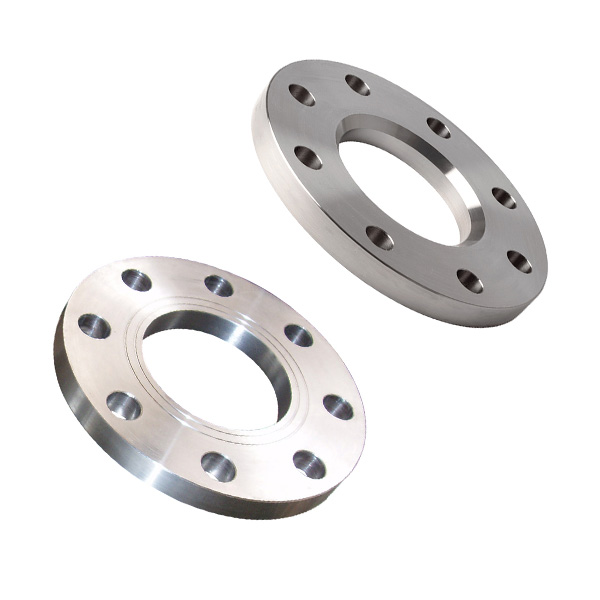
Einführung
Flansche sind wesentliche Rohrleitungskomponenten, die zur Verbindung von Rohrabschnitten dienen und gleichzeitig eine einfache Demontage ermöglichen. Der Flachschweißflansch ist eine häufig verwendete Ausführung, Sie finden häufige Anwendung in Branchen, in denen Flüssigkeiten über Rohrleitungsnetze transportiert werden. Als primäres Druckbegrenzungselement, Flansche müssen robuste Dichtungsfähigkeiten aufweisen, um auch unter schwierigen Betriebsbedingungen dichte Verbindungen zu gewährleisten. Ziel dieses Dokuments ist es, einen detaillierten Überblick über das Dichtungsprinzip und die wichtigsten Eigenschaften zu geben, die die Leistung flacher Schweißflansche bestimmen. Durch das Verständnis der Mechanik, die der Abdichtung zugrunde liegt, Der Flanschstil kann richtig spezifiziert und installiert werden, um eine langfristige strukturelle Integrität zu gewährleisten.
Dichtungsprinzip
Um eine wirksame Abdichtung innerhalb der Flansch-Rohr-Baugruppe zu erreichen, ist die Kombination von Druckbelastungen erforderlich, inniger Oberflächenkontakt, und plastische Verformung. Beim Verschrauben eines Flanschpaares, Das Anziehen der Schrauben erzeugt nach außen gerichtete Radialkräfte, die die flachen Flächen fest gegeneinander ziehen. Die verbundenen Flächen unterliegen dann je nach Materialeigenschaften und auferlegten Belastungen einer begrenzten elastischen und plastischen Verformung. allerdings, Es bleiben mikroskopisch kleine Oberflächenfehler zurück, die, wenn sie unverändert bleiben, zu Undichtigkeiten führen würden.
Ein kritisches Dichtungselement ist die „Dichtung“., normalerweise ein Ring oder eine Unterlegscheibe, die aus einem flexiblen, aber komprimierbaren Material wie Elastomeren geschnitten ist, Graphit, oder Metalle. Wird zwischen den Flanschflächen installiert, Durch das Anziehen wird die Dichtung zusammengedrückt und fließt in Hohlräume oder Spalten entlang der Dichtflächen. Wichtig, es verformt sich plastisch und verfestigt sich, anstatt sich einfach nur elastisch zu komprimieren. Dieser „Dichtungsfluss“ blockiert physisch die Flüssigkeitsdurchgänge durch alle Unregelmäßigkeiten, indem er sich fest in jedes mikroskopisch kleine Tal einkeilt. Beim Laden entfernt, Restklemmkräfte und der ausgehärtete Füllstoff sorgen für die Dichtungsintegrität bei wechselnden Drücken und Temperaturen.
Materialauswahl
Die Materialien der Flanschkomponenten haben direkten Einfluss auf die Robustheit und Lebensdauer einer bestimmten Dichtungskonstruktion. Gängige Materialien sind:
-
Flanschkörper: c-Stahl (ASTM A105), niedriglegierter Stahl, Duplex-/Super-Duplex-Edelstahl für Korrosionsbeständigkeit. Entscheidend ist eine ausreichende Zähigkeit im Verhältnis zur Lebensdauer.
-
Verschrauben: Standardschrauben aus Kohlenstoffstahl reichen für viele nicht korrosive Aufgaben aus. Für Offshore-/Sauerdienste, Legierungsschrauben mit Festigkeit/Korrosionsbeständigkeit wie A193 B7, Es werden ASTM A490 verwendet.
-Dichtung: Weicheres, mit Stoff eingelegtes Gummi für niedrige Drücke 300 PSI, Spiralförmig gewickelte Asbestfaser für höhere Drücke bis zu 1500 psi, flexible Graphit- oder PTFE-Platten für >=1500 psi, einschließlich Hochtemperaturanwendungen.
Bei Materialkombinationen müssen Inkompatibilitäten wie galvanische Korrosion vermieden und die Komprimierbarkeit der Dichtung bei Drücken berücksichtigt werden. Die richtige Spezifikation stellt die strukturelle Integrität und Dichtungsleistung über Jahrzehnte hinweg sicher.
Flanschoberflächenausführungen
Die Oberflächenbeschaffenheit wirkt sich direkt auf die Kontaktfläche der Dichtung und die Fließeigenschaften der Dichtung aus:
-
Bearbeitetes Gesicht (MF): Standard 125-250 Ra-Mikrozoll-Oberfläche mit scharfen Kanten für beste Metall-Metall-Abdichtung. allerdings, Große Flansche lassen sich nur schwer bearbeiten.
-
Geschweißtes Gesicht (WF): Die geschweißte Oberfläche weist eine höhere Rauheit auf 80-160 Ra Mikrozoll, aber abgerundete Kanten erleichtern den Einbau der Dichtung. Etwas geringeres Dichtungspotenzial als MF.
-
Blind fertiges Gesicht (Beste Freundin): Eine spezielle Bearbeitung vertieft die Schweißnahtverstärkung und hinterlässt eine MF-ähnliche Oberfläche. Bietet das Beste aus MF-Dichtung und vereinfachter WF-Installation. Teurer als andere Oberflächen.
Eine höhere Oberflächenrauheit vergrößert die Metallkontaktfläche zum Abdichten, sollte jedoch gleichmäßig und kontrolliert sein. Die Kantenschärfe beeinflusst auch die anfängliche Kompression der Dichtung und die Anfälligkeit für Schnitte während der Montage-/Demontagezyklen. Die richtige Auswahl der Oberfläche sorgt für ein ausgewogenes Verhältnis zwischen Leistung und Wirtschaftlichkeit.
Flanschstile und -konfigurationen
Zusammen mit fertigen Gesichtern, Die äußere Flanschmorphologie beeinflusst die Flexibilität der Rohrleitungen, gemeinsamer Zugang, und langfristige Stressverteilung:
-
Schweißhals (WN): Der in das Rohr eingeschweißte integrierte Rohrhals sorgt für die stärkste Verbindung. allerdings, weniger Einbauraum im Flansch im Vergleich zu Aufstecktypen.
-
Schlüpfen (SO): Direkt über das Rohrende geschraubt. Mehr Platz im Inneren, aber ein kleiner Hals führt zu lokalen Spannungserhöhungen. Wird oft mit Gegenringen verwendet, um die Flexibilität der Rohrleitungen zu erhöhen.
-
Überlappungsverbindung (LJ): Über zwei aneinanderstoßende Rohrenden verschraubt. In den Abmessungen ähnlich wie bei Aufsteckhülsen, es treten jedoch höhere Spannungen an der Schnittstelle zwischen Rohr und Flansch auf.
-
Schweißmuffe (SW): In das Rohrende eingeschweißte integrierte Innenmuffe zum Anschrauben der flachen Stirnkappe. Bietet den größten Innenspielraum und die schwächste Verbindungsfestigkeit.
Bei der richtigen Flanschauswahl werden die Verbindungsspannungen berücksichtigt, erforderliche Zugänglichkeit, Pipelinelasten, Herstellungs-/Installationsbeschränkungen, und ganzheitliche Integrität. Standardisierte Bohrungsdurchmesser erleichtern die Lagerhaltung.
Flanschinstallation und -integrität
Korrekte Installations- und Montageverfahren erweisen sich als entscheidend für eine zuverlässige langfristige Flanschdichtleistung:
-
Reinigen Sie die Flanschflächen und tragen Sie ein Anti-Seize-Mittel auf die Oberflächen der Gleitbolzen auf, um ein Festfressen zu verhindern.
-
Zentrieren Sie die Dichtung zwischen den Flächen und drücken Sie sie richtig zusammen, ohne sie zu verdrehen oder zu rollen. Verwenden Sie bei Bedarf Schmiermittel.
-
Ziehen Sie die Schrauben über Kreuz handfest an und ziehen Sie sie dann schrittweise schrittweise mit dem vorgeschriebenen Drehmoment an, während Sie gleichzeitig auf eine gleichmäßige Kompression achten. Vermeiden Sie zu starkes oder zu geringes Anziehen.
-
Führen Sie eine abschließende Dichtheitsprüfung der Verbindung durch, bevor Sie Außenlackierungen und Beschichtungen auftragen. Überprüfen Sie es regelmäßig während des Betriebs.
-
Ziehen Sie Balgeinsätze in Betracht, Schutzvorrichtungen oder Rückhaltevorrichtungen für Vibrations- oder seismische Belastungen, die die Belastungen beim Sitzen/Abheben mildern.
-
Überprüfen Sie die Flansche regelmäßig im Rahmen der vorbeugenden Wartung, Austausch von Dichtungen, Schrauben oder Flansche weisen Anzeichen von Beschädigung auf, Korrosion oder Verschleiß.
Fazit
Das Verständnis der Dichtungsprinzipien und -eigenschaften flacher Schweißflansche ermöglicht deren zuverlässigen Einsatz für die Übertragung von Flüssigkeiten über Rohrleitungsnetze. Materialauswahl, Oberflächenfinish, Flanschkonfiguration und Installationsverfahren wirken sich alle direkt auf die langfristige Integrität der Verbindung aus. Bei richtiger Angabe, hergestellt und gepflegt, Flansche bieten eine robuste Druckdichtung selbst unter schwierigen Betriebsbedingungen und unterstützen wichtige Industriezweige. Fortschritte in der Metallurgie, Zerstörungsfreie Prüfungen und Inspektionen sichern auch die Flanschleistung bis weit in die Zukunft.
Sie müssen eingeloggt sein, um ein Kommentar abzugeben.