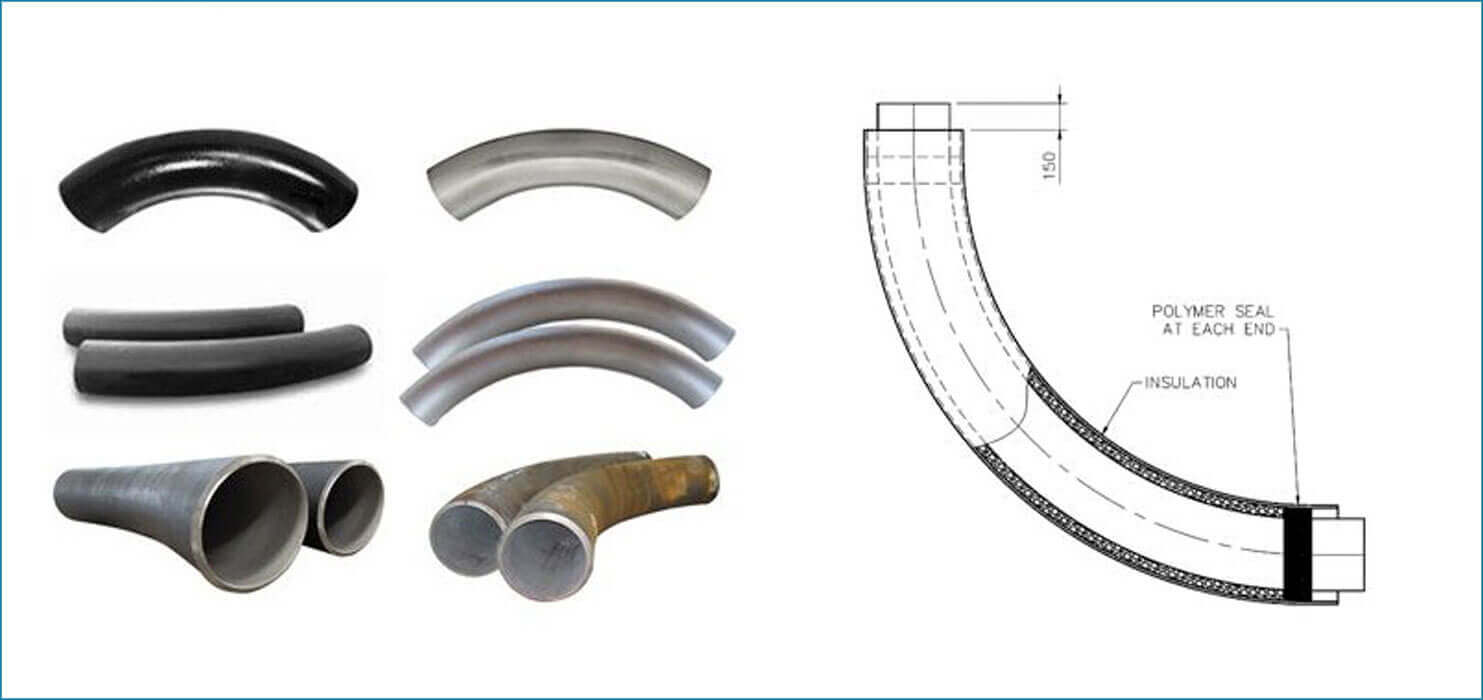
Herstellung von Rohrbögen für Kraftwerke im Induktionsbiegeverfahren
Einführung
Das Biegen von Rohren ist ein kritischer Prozess beim Bau und Betrieb von Kraftwerke, wo komplexe Rohrleitungssysteme zum Transport von Dampf erforderlich sind, Wasser, und andere Flüssigkeiten unter hohem Druck und hoher Temperatur. Unter den verschiedenen verfügbaren Rohrbiegetechniken, die Induktionsbiegeprozess zeichnet sich durch eine hocheffiziente und präzise Methode zur Herstellung hochwertiger Rohrbögen aus. Aufgrund der Fähigkeit, Rohre mit großem Durchmesser zu verarbeiten, eignet sich dieses Verfahren besonders für Kraftwerksanwendungen, Wahrung der materiellen Integrität, und erzeugen Biegungen mit minimaler Verformung.
In diesem Artikel, Wir werden das erkunden Herstellung von Rohrbögen für Kraftwerke mittels Induktionsbiegeverfahren. Die Diskussion umfasst die Prinzipien des Induktionsbiegens, seine Vorteile gegenüber herkömmlichen Methoden, die Schritte des Prozesses, und seine Anwendungen in Kraftwerksrohrleitungssystemen. Wir werden auch die Herausforderungen untersuchen, Qualitätskontrollmaßnahmen, und zukünftige Trends beim Induktionsbiegen für Kraftwerksprojekte.
Standardspezifikation für Stumpfschweiß-Heißinduktionsbiegung
Abmessungen : ASME / ANSI B16.9, ASME B16.28, MSS-SP-43
GRÖßE : 2″ACHTUNG BIS 18″ NB
Geben : nahtlose / erw / Geschweißt / Vorgefertigte
Biegeradien : 75 / 100 / 150 / 250 / 300 / 500 / 800 / 1,000 / 1,200 / 1,500 mm
Biegungsradius(R): R=1D, 2D, 3D, 5D, 6D, 8D, 10D oder Benutzerdefiniert
Biegewinkel (ich): 15°, 30°, 45°, 60°, 90°, 135°, 180°
MATERIAL & Sorten von Heißinduktionsrohrbögen :
Edelstahl Hot Induktionsbiege :
ASTM A403 WP316/316L, ASTM A403 SA / A 774 WP-S, WP-W, WP-WX 304/304L, ASTM A182 F316L, 304L, DIN 1.4301, DIN1.4306, DIN 1.4401, DIN 1.4404
duplex & Super-Duplex-Stahl Hot Induktionsbiege :
ASTM A 815, ASME SA 815 UNS NO S31803, S32205. UNS S32750, S32950. Werkstoff No. 1.4462
c-Stahl Hot Induktionsbiege :
ASTM A234, ASME SA234 WPB , WPBW, WPHY 42, WPHY 46, WPHY 52, Wph 60, WPHY 65 & WPHY 70.
Heißinduktionsbiegung aus Kohlenstoffstahl mit niedriger Temperatur : ASTM A420 WPL3, A420 WPL6
Warminduktionsbiegung aus legiertem Stahl :
ASTM / ASME A / SA 234 Gr. WP 1, WP 5, WP 9, WP 11, WP 12, WP 22, WP 91
Heiße Induktionsbiegung aus Nickellegierung :
ASTM B336, ASME SB336, Nickel 200 (UNS No. Nr. 2200), Nickel 201 (UNS No. N02201), Monel 400 (UNS No. N04400), Monel 500 (UNS No. N05500), Inconel 800 (UNS No. N08800), Inconel 825 (UNS No. N08825), Inconel 600 (UNS No. N06600), Inconel 625 (UNS No. N06625), Inconel 601 (UNS No. N06601), Hastelloy C 276 (UNS No. N10276), Legierung 20 (UNS No. N08020), Titan (Klasse I & II), Cupro-Nickel 70/30, CuNi10Fe1Mn, CuNi30Mn1Fe.
Bedeutung von Rohrbögen in Kraftwerken
1. Rolle von Rohrleitungssystemen in Kraftwerken
Rohrleitungssysteme sind das Rückgrat von Kraftwerken, den Transport von Dampf ermöglichen, Wasser, und andere Flüssigkeiten zwischen Kesseln, Turbinen, Kondensatoren, und andere kritische Komponenten. Rohrbögen sind unerlässlich für:
- Ändern der Richtung des Flüssigkeitsflusses.
- Anschließen von Geräten auf engstem Raum.
- Reduzierung von Spannungen und Vibrationen in Rohrleitungssystemen.
2. Herausforderungen bei der Kraftwerksverrohrung
- hohe Temperaturen und drücke: Rohre müssen extremen Betriebsbedingungen standhalten, oft über 500°C und 20 MPA.
- Materielle Integrität: Bögen müssen die mechanischen Eigenschaften des Rohrmaterials beibehalten, um Sicherheit und Zuverlässigkeit zu gewährleisten.
- Komplexe Geometrien: Kraftwerkslayouts erfordern maßgeschneiderte Bögen mit präzisen Winkeln und Radien.
3. Warum Induktionsbiegen?
die Induktionsbiegeprozess begegnet diesen Herausforderungen durch die Herstellung hochwertiger Biegungen mit:
- Minimale Materialverzerrung.
- Verbesserte mechanische Eigenschaften.
- Strenge Kontrolle über die Biegegeometrie.
Der Induktionsbiegeprozess: Überblick
Induktionsbiegen ist ein thermomechanischer Prozess Dabei wird lokale Erwärmung durch elektromagnetische Induktion genutzt, um Rohre in die gewünschte Form zu biegen. Der Prozess unterliegt einer strengen Kontrolle, Gewährleistung der Präzision und Konsistenz des Endprodukts.
Hauptmerkmale von INDUKTION BIEGEN:
- Lokalisierte Erwärmung: Es wird nur der Biegebereich erwärmt, die Eigenschaften des restlichen Rohres bleiben erhalten.
- Kontrollierte Kühlung: Die Kühlung wird sorgfältig gesteuert, um Eigenspannungen und Verformungen zu vermeiden.
- Breite Anwendbarkeit: Geeignet für eine Vielzahl von Materialien, einschließlich Kohlenstoffstahl, Edelstahl, und legierter Stahl.
Schritte im Induktionsbiegeprozess
Die Herstellung von Rohrbögen für Kraftwerke umfasst mehrere Schritte, Jeder Aspekt ist entscheidend für die Erzielung der gewünschten Qualität und Leistung. Nachfolgend finden Sie eine detaillierte Beschreibung des Prozesses:
1. Vorbereitung
- Materialauswahl:
- Rohre werden typischerweise aus Materialien wie hergestellt c-Stahl (z.B., ASTM A106, A53), Edelstahl, oder Legierter Stahl (z.B., P91, P22), je nach Anwendung.
- Das Material muss die erforderlichen mechanischen und thermischen Eigenschaften für den Kraftwerkseinsatz erfüllen.
- Rohrinspektion:
- Rohre werden auf Oberflächenfehler untersucht, Maßhaltigkeit, und Materialkonsistenz.
- Aufstellen:
- Das Rohr wird an einem Ende festgeklemmt, während sich das andere Ende beim Biegen frei bewegen kann.
- die Induktionsspule wird an der Biegestelle positioniert.
2. Induktionsheizung
- Lokalisierte Erwärmung:
- Eine Induktionsspule erzeugt ein hochfrequentes elektromagnetisches Feld, Wirbelströme im Rohrmaterial induzieren.
- Diese Ströme erzeugen Wärme, Erhöhen der Rohrtemperatur auf die plastischer Verformungsbereich (typischerweise 800–1100 °C, Abhängig vom Material).
- Kontrollierte Heizzone:
- Es wird nur ein kleiner Abschnitt des Rohres erhitzt, Minimierung thermischer Spannungen und Verformungen in den umliegenden Bereichen.
3. biegen
- Mechanische Kraftanwendung:
- Sobald der Rohrabschnitt die gewünschte Temperatur erreicht hat, Zum Biegen des Rohrs wird ein Biegearm oder eine mechanische Kraft angewendet.
- Der Biegeradius wird durch den Aufbau bestimmt und kann von engen Biegungen reichen (z.B., 3D) bis hin zu Biegungen mit großem Radius (z.B., 10D).
- Kontinuierliche Bewegung:
- Das Rohr wird schrittweise durch die Induktionsspule bewegt, Ermöglicht eine kontinuierliche Biegung über die gesamte Länge.
4. Kühlung
- Kontrollierte Kühlung:
- Der erhitzte Abschnitt wird mit Wasser- oder Luftstrahlen abgekühlt, um die Form zu verfestigen und eine weitere Verformung zu verhindern.
- Eine kontrollierte Kühlung trägt dazu bei, die mechanischen Eigenschaften des Rohrs aufrechtzuerhalten und Eigenspannungen zu minimieren.
5. Bearbeitung nach dem Biegen
- Inspektion:
- Das gebogene Rohr wird auf Maßhaltigkeit geprüft, Oberflächenqualität, und mechanische Eigenschaften.
- Wärmebehandlung (falls erforderlich):
- Zusätzliche Wärmebehandlung, wie Stressabbau oder Normalisierung, kann durchgeführt werden, um die strukturelle Integrität des Rohrs zu verbessern.
- Finishing:
- Das Rohr wird gereinigt, und überschüssiges Material (z.B., Ablagerungen oder Oxidation) wird entfernt.
Vorteile des Induktionsbiegens für Kraftwerke
Das Induktionsbiegeverfahren bietet mehrere Vorteile, die es ideal für die Herstellung von Rohrbögen für Kraftwerke machen:
1. Präzision und Genauigkeit
- Strenge Kontrolle über den Biegeradius, Winkel, und Standort sorgen für konsistente Ergebnisse.
- Geeignet für komplexe Geometrien, die in Kraftwerkslayouts erforderlich sind.
2. minimale Verzerrung
- Lokale Erwärmung verringert das Risiko einer Ovalität, Wandverdünnung, und andere Verzerrungen.
3. Verbesserte mechanische Eigenschaften
- Durch kontrolliertes Erhitzen und Abkühlen bleiben die mechanischen Eigenschaften des Materials erhalten oder sogar verbessert, wie Zugfestigkeit und Zähigkeit.
4. Kosteneffektivität
- Reduziert Materialverschwendung und macht Schweißen oder zusätzliche Armaturen überflüssig.
- Schnellere Produktion im Vergleich zu herkömmlichen Biegemethoden.
5. Breite Materialkompatibilität
- Kann eine Vielzahl von Materialien verarbeiten, einschließlich hochfester Legierungen, die in Kraftwerksrohren verwendet werden.
6. Vorteile für die Umwelt
- Verwendet Elektrizität als primäre Energiequelle, um es sauberer und nachhaltiger zu machen.
Anwendungen des Induktionsbiegens in Kraftwerken
Induktionsbiegen wird in verschiedenen Rohrleitungssystemen innerhalb von Kraftwerken eingesetzt, einschließlich:
1. Dampfleitungen
- Hochtemperatur-Dampfrohre, die Kessel und Turbinen verbinden.
- Bögen müssen extremer Hitze und Druck ohne Verformung standhalten.
2. Wasserzirkulationssysteme
- Rohre zur Zirkulation von Kühlwasser zwischen Kondensatoren und Kühltürmen.
- Für einen effizienten Durchfluss sind Bögen mit großem Durchmesser erforderlich.
3. Gasleitungen
- Rohrleitungen für den Transport von Erdgas oder anderen Brennstoffen zu Kraftwerken.
- Bögen müssen einen reibungslosen Durchfluss und minimalen Druckverlust gewährleisten.
4. Abgasanlagen
- Kundenspezifische Bögen für Abgasrohre in Gasturbinen und anderen Geräten.
Vergleich mit anderen Biegemethoden
Aspekt | INDUKTION BIEGEN | Kaltbiegen | Dornbiegen |
---|---|---|---|
Heizung | Lokale Erwärmung mit Induktion | Keine Heizung | Keine Heizung |
Präzision | hoch | Mäßig | hoch |
Materialverzerrung | Minimal | Höhere Gefahr einer Verzerrung | Minimal |
Rohr Größe | Geeignet für Rohre mit großem Durchmesser | Beschränkt auf kleinere Rohre | Beschränkt auf kleinere Rohre |
Kosten | Mäßig | niedrig | hoch |
Anwendungen | Kraftwerksleitungen, Strukturelle Systeme | Einfache Bögen für spannungsarme Anwendungen | Komplexe Bögen für Rohre mit kleinem Durchmesser |
Qualitätskontrolle beim Induktionsbiegen
Gewährleistung der Qualität und Zuverlässigkeit induktionsgebogener Rohre, Während des gesamten Prozesses werden strenge Qualitätskontrollmaßnahmen umgesetzt:
1. Maßkontrolle
- Messungen des Biegeradius, Winkel, und Ovalität werden herangezogen, um die Einhaltung der Designvorgaben zu überprüfen.
2. Zerstörungsfreie Prüfung (NDT)
- Zur Erkennung interner Defekte oder Risse werden Techniken wie Ultraschallprüfung und Radiographie eingesetzt.
3. Mechanische Prüfung
- Tests wie Zugfestigkeit, Härte, und Schlagfestigkeit werden durchgeführt, um die mechanischen Eigenschaften des Rohrs zu bewerten.
4. Oberflächeninspektion
- Zur Identifizierung von Oberflächenfehlern wird eine Sichtprüfung durchgeführt, wie Risse oder Oxidation.
Herausforderungen beim Induktionsbiegen für Kraftwerke
Dabei bietet das Induktionsbiegen zahlreiche Vorteile, es bringt auch einige Herausforderungen mit sich:
1. Materialbeschränkungen
- Einige Materialien, wie spröde Legierungen, reagiert möglicherweise nicht gut auf den Induktionsbiegeprozess.
2. Ausrüstungskosten
- Die Anfangsinvestition in eine Induktionsbiegeausrüstung kann hoch sein, Dies macht es für kleine Betriebe weniger zugänglich.
3. Bedienerfähigkeit
- Der Prozess erfordert erfahrene Bediener, um eine präzise Steuerung der Erwärmung sicherzustellen, biegen, und Kühlparameter.
4. Oberflächenoxidation
- Hohe Temperaturen können zu Oberflächenoxidation führen, was möglicherweise zusätzliche Nachbearbeitungsschritte erfordert.
Fallstudie: Induktionsbiegen für ein Kraftwerksprojekt
Projektübersicht:
- Standort: A 500 MW-Kohlekraftwerk.
- Rohr-Material: Legierter Stahl ASTM A335 P91.
- Rohr-Durchmesser: 24 Zoll.
- Biegungsradius: 5D (fünfmal so groß wie der Rohrdurchmesser).
Ergebnisse:
- Maßhaltigkeit: Alle Biegungen erfüllten die geforderten Spezifikationen mit minimaler Verformung.
- mechanische Eigenschaften: Die Rohre behielten nach dem Biegen ihre Zugfestigkeit und Zähigkeit.
- Kosteneinsparungen: Das Projekt erzielte erhebliche Kosteneinsparungen, da keine Schweißverbindungen erforderlich waren.
- Effizienz: Der Induktionsbiegeprozess verkürzte die Produktionszeit um 30% im Vergleich zu herkömmlichen Methoden.
Zukünftige Trends beim Induktionsbiegen für Kraftwerke
Da Kraftwerkskonstruktionen immer komplexer und anspruchsvoller werden, Der Induktionsbiegeprozess wird sich voraussichtlich wie folgt weiterentwickeln:
1. Automatisierung
- Integration fortschrittlicher Sensoren und Steuerungssysteme zur Automatisierung des Biegeprozesses und Verbesserung der Präzision.
2. Fortschrittliche Materialien
- Entwicklung neuer Materialien und Beschichtungen zur Verbesserung der Leistung und Haltbarkeit induktionsgebogener Rohre.
3. Energieeffizienz
- Innovationen in der Induktionsheiztechnologie zur Reduzierung des Energieverbrauchs und der Umweltbelastung.
4. Digitale Simulation
- Einsatz von Rechenwerkzeugen, wie zum Beispiel die Finite-Elemente-Analyse (FEA), um den Biegeprozess zu simulieren und Parameter zu optimieren.
Fazit
die Induktionsbiegeprozess ist eine vielseitige und effiziente Methode zur Herstellung hochwertiger Rohrbögen für Kraftwerke. Seine Fähigkeit, Rohre mit großem Durchmesser zu handhaben, Wahrung der materiellen Integrität, und präzise Biegungen machen es zur idealen Wahl für Kraftwerksrohrleitungssysteme. Durch die Bewältigung der Herausforderungen und die Umsetzung strenger Qualitätskontrollmaßnahmen, Hersteller können das Induktionsbiegen nutzen, um den Anforderungen moderner Kraftwerksprojekte gerecht zu werden.
Mit fortschreitender Technologie, Das Induktionsbiegeverfahren wird weiterhin eine entscheidende Rolle bei der Gestaltung der Zukunft des Kraftwerksbaus spielen, bietet verbesserte Präzision, Nachhaltigkeit, und Wirtschaftlichkeit.
Sie müssen eingeloggt sein, um ein Kommentar abzugeben.