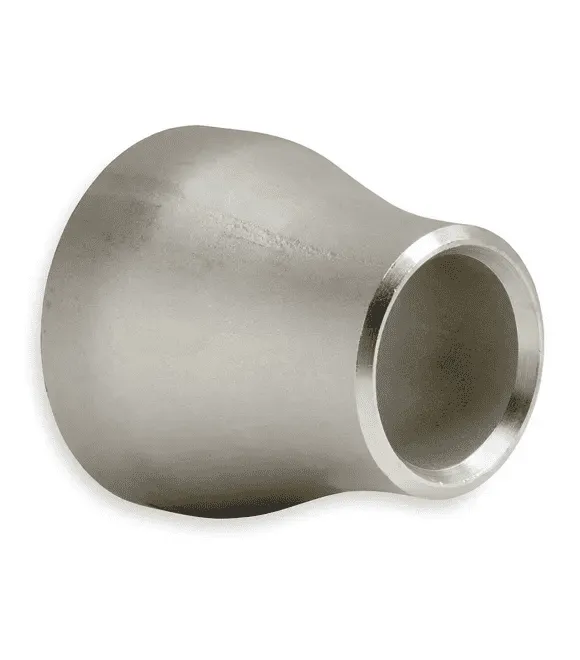
Zukünftige Trends und Innovationen
Die Edelstahlindustrie entwickelt sich ständig weiter, angetrieben durch Fortschritte in der Materialwissenschaft, Fertigungstechnologien, und die Nachfrage nach verbesserter Leistung in extremen Umgebungen. Hier sind einige zukünftige Trends und Innovationen, die sich auf die Produktion und Anwendung von Reduzierstücken aus Edelstahl ASTM A403 WP auswirken könnten.
Hochleistungslegierungen
Die Entwicklung von Hochleistungslegierungen ist ein bedeutender Trend. Diese Materialien sind so konstruiert, dass sie einen überlegenen Korrosionsbeständigkeit bieten, Stärke, und Haltbarkeit in immer härteren Umgebungen.
- Superaustenitische Edelstähle: Verbesserte Versionen traditioneller austenitischer Klassen, wie al-6xn, Bessere Widerstand gegen Lochfraß- und Spaltkorrosion bieten.
- Duplex und Super Duplex Edelstahlstähle: Kombinieren Sie die besten Eigenschaften von austenitischen und ferritischen Stählen, Diese Materialien bieten hervorragende Festigkeit und Beständigkeit gegen Stresskorrosionsrisse.
Generative Fertigung
Generative Fertigung (BIN), allgemein bekannt als 3D -Druck, revolutioniert die Produktion komplexer Komponenten, einschließlich Edelstahl -Reduzierungen.
- Pulverbettfusion (PBF): Eine beliebte AM-Technik zur Herstellung von Edelstahlteilen aus rostfreiem Stahl für Schicht aus Metallpulver.
- Gerichtete Energieabscheidung (Ded): Geeignet zum Reparieren und Hinzufügen von Material zu vorhandenen Komponenten, Verlängerung ihrer Lebensdauer und Verringerung von Abfall.
Fortgeschrittene Wärmebehandlungstechniken
Innovationen in Wärmebehandlungstechniken verbessern die Eigenschaften von Edelstahl -Reduzierern.
- Low-Temperatur-Kohlensäure (LTC): Verbessert Oberflächenhärte und Verschleißfestigkeit, ohne die Korrosionsbeständigkeit zu beeinträchtigen.
- Fortgeschrittene Glühprozesse: Ergeben eine bessere Kontrolle über mikrostrukturelle Eigenschaften, Verbesserung sowohl mechanischer Eigenschaften als auch Korrosionsbeständigkeit.
Smart Fertigung und Industrie 4.0
Die Integration von Industrie 4.0 Prinzipien, einschließlich IoT (Internet der Dinge), Big Data, Und du hast (Künstliche Intelligenz), transformiert Herstellungsprozesse.
- Vorhersagewartung: Verwendung von Sensoren und Datenanalysen, um Geräteausfälle vorherzusagen und zu verhindern, Gewährleistung eines konstanten Produkts Qualität.
- Intelligente Fabriken: Implementierung automatisierter Systeme und Robotik, um die Präzision zu verbessern, Effizienz, und Anpassungsfähigkeit in Produktionslinien.
Ökologische Nachhaltigkeit
Umweltverträgliche Nachhaltigkeit wird in der Edelstahlindustrie immer wichtiger.
- Recycling und kreisförmige Wirtschaftlichkeit: Betonung des Recyclings von Edelstahl zur Reduzierung des Rohstoffverbrauchs und der Umweltauswirkungen.
- Umweltfreundliche Prozesse: Entwicklung von Herstellungsprozessen, die den Energieverbrauch und die Emissionen minimieren, wie die Verwendung erneuerbarer Energiequellen und sauberere Produktionstechniken.
Fallstudien
Fallstudie 1: Chemische Verarbeitungsanlage
Eine wichtige chemische Verarbeitungsanlage benötigte Edelstahl -Reduzierer, die stark ätzenden Umgebungen mit Schwefelsäure und Chloriden standhalten konnten. Die Pflanze wählte WP904L für ihre außergewöhnliche Resistenz gegen diese harten Chemikalien.
Durchführung:
- Materialauswahl: WP904L wurde für seinen hohen Nickel ausgewählt, Molybdän, und Kupferinhalt.
- HERSTELLUNGSPROZESS: Die Reduzierer wurden mit geschlossenem Schmieden hergestellt, gefolgt von Lösungsglühen und Elektropolieren, um den Korrosionsbeständigkeit zu verbessern.
- Leistung: Die WP904L -Redakteure zeigten eine hervorragende Leistung, mit minimaler Wartung und Ausfallzeiten über mehrere Jahre.
Fallstudie 2: Offshore -Ölplattform
Eine Offshore -Ölplattform erforderte robuste Reduzierer, die hohen Drücken standhalten können, Temperaturen, und ätzende Meerwasserumgebungen. WP316L wurde für seine ausgewogenen Eigenschaften ausgewählt.
Durchführung:
- Materialauswahl: WP316L wurde wegen seines Widerstands gegen Chlorid-induzierte Korrosion und gute mechanische Eigenschaften ausgewählt.
- HERSTELLUNGSPROZESS: Schmieden und anschließende Bearbeitung wurden verwendet, um die Reduzierer herzustellen, gefolgt von Wickling und Passivierung, um die Schutzchromoxidschicht wiederherzustellen.
- Leistung: Die WP316L -Reduzierer wurden unter harten Bedingungen zuverlässig durchgeführt, Gewährleistung der Integrität des Rohrleitungssystems.
Fallstudie 3: Stromerzeugungseinrichtung
Eine Stromerzeugungsanlage benötigte hochtemperaturbeständige Reduzierer für seine Kesselkomponenten. WP321 wurde aufgrund seiner Stabilität bei erhöhten Temperaturen und Resistenz gegen intergranuläre Korrosion ausgewählt.
Durchführung:
- Materialauswahl: WP321 wurde für seine Titanstabilisierung ausgewählt, Verhinderung von Vergaser Niederschlag.
- HERSTELLUNGSPROZESS: Offenes Schmieding, gefolgt von Lösung Glühen, wurde verwendet, um die Reduzierer zu produzieren.
- Leistung: Die WP321 -Reduzierer lieferten eine hervorragende Leistung, Aufrechterhaltung ihrer Integrität und Widerstand gegen Korrosion in Hochtemperaturumgebungen.
Anhang
Glossar der Begriffe
- Austenitischem Edelstahl: Eine Kategorie von Edelstahl, bekannt für seine hervorragende Korrosionsbeständigkeit und Formbarkeit, gekennzeichnet durch eine Gesichts-zentrierte kubische Kristallstruktur.
- Karbidniederschlag: Die Bildung von Chromcarbiden an Korngrenzen, Dies kann den Korrosionsbeständigkeit verringern.
- Interkristalline Korrosion: Korrosion, die entlang der Korngrenzen eines Materials auftritt, Oft aufgrund von Vergaser Niederschlägen.
- Molybdän: Ein chemisches Element, das zu rostfreien Stählen hinzugefügt wurde, um die Korrosionsbeständigkeit zu verbessern, besonders gegen Chloride.
- Passivierung: Ein Prozess, der die natürliche Oxidschicht auf Edelstahl verbessert, Verbesserung der Korrosionsbeständigkeit.
FAQs
-
Was ist der Unterschied zwischen WP304 und WP316?
- WP316 enthält Molybdän, Dies verbessert seine Resistenz gegen Chlorid -Lochfraß und Spaltkorrosion, Dadurch geeigneter für Meeres- und chemische Umgebungen im Vergleich zu WP304 geeignet ist.
-
Warum wird WP904L in hochkarrosiven Umgebungen bevorzugt??
- WP904L hat einen hohen Nickel- und Molybdängehalt, zusammen mit Kupfer, Bereitstellung einer außergewöhnlichen Resistenz gegen Schwefelsäure und Chloridumgebungen.
-
Wie kommt die additive Fertigung der Produktion von Edelstahl -Reduzierern zugute??
- Die additive Fertigung ermöglicht die Erstellung komplexer Formen, reduziert Materialabfälle, und ermöglicht schnelle Prototypen und Anpassung.
-
Was sind die Vorteile der Verwendung von Duplex -Edelstählen?
- Duplex -Edelstähle kombinieren die besten Eigenschaften von austenitischen und ferritischen Stählen, Anbieten hoher Festigkeit und hervorragender Beständigkeit gegen Stresskorrosionsrisse.
-
Wie verbessert die Wärmebehandlung die Eigenschaften von Edelstahl -Reduzierern aus Edelstahl??
- Wärmebehandlungsprozesse wie Tempern und Lösung Glühen verfeinern die Mikrostruktur, interne Belastungen lindern, und die mechanische Eigenschaften und Korrosionsbeständigkeit verbessern.
Dieser erweiterte Leitfaden sollte ein umfassendes Verständnis von ASTM A403 WP Edelstahlreduzierern vermitteln, Abdecken Sie alles von Materialeigenschaften und Herstellungsprozessen bis hin zu zukünftigen Trends und praktischen Anwendungen.
Sie müssen eingeloggt sein, um ein Kommentar abzugeben.