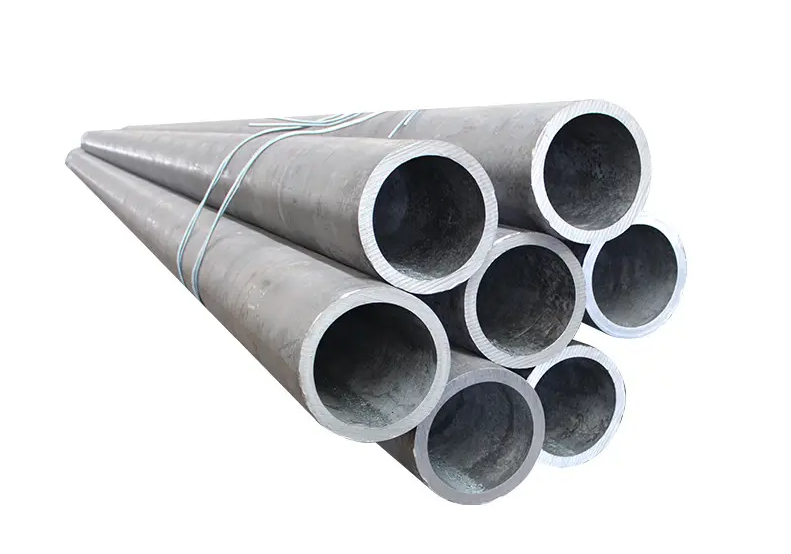
Ein Verfahren zum Schweißen dickwandiger Hochdruckrohrleitungen aus Haushaltsstahl A335 P91: Technischen Bereich – Die vorliegende Erfindung bezieht sich auf das Gebiet der Schweißtechnik, insbesondere in Bezug auf ein Verfahren zum Schweißen von dickwandigen Hochdruckrohrleitungen aus Haushaltsstahl A335 P91.
Wir haben den größten Bestand an nahtlosen Rohren aus legiertem Stahl ASTM A335 P91
Rohr aus legiertem Stahl A 335 P91:
GRÖßE : 1/2″ An 24 “UND VON & NB
Zeitplan: SCH20, Sch30, Sch40.
Geben : Geschweißt / Vorgefertigte / nahtlose
Länge : Einzeln zufällig, Doppelt zufällig & Schnittlänge.
Ende : Plain End, Abgeschrägtes Ende.
Materialien :
Legiertes Stahlrohr A335 P91 – AS-Rohr A335 P91
ASTM A335, Gr. P5, P9, P11, P12, P21, P22 & P91
ASTM A335 P91 Zusammensetzung der Chromrohre
Klasse | UNS | C≤ | MN | P≤ | S≤ | Si≤ | Cr | Mo |
P1 | K11522 | 0.10~0,20 | 0.30~0,80 | 0.025 | 0.025 | 0.10~0,50 | – | 0.44~0,65 |
P2 | K11547 | 0.10~0,20 | 0.30~0,61 | 0.025 | 0.025 | 0.10~0,30 | 0.50~0,81 | 0.44~0,65 |
P5 | K41545 | 0.15 | 0.30~0,60 | 0.025 | 0.025 | 0.50 | 4.00~6,00 | 0.44~0,65 |
P5b | K51545 | 0.15 | 0.30~0,60 | 0.025 | 0.025 | 1.00~2,00 | 4.00~6,00 | 0.44~0,65 |
P5c | K41245 | 0.12 | 0.30~0,60 | 0.025 | 0.025 | 0.50 | 4.00~6,00 | 0.44~0,65 |
P9 | S50400 | 0.15 | 0.30~0,60 | 0.025 | 0.025 | 0.50~1,00 | 8.00~10.00 | 0.44~0,65 |
P11 | K11597 | 0.05~0,15 | 0.30~0,61 | 0.025 | 0.025 | 0.50~1,00 | 1.00~1,50 | 0.44~0,65 |
P12 | K11562 | 0.05~0,15 | 0.30~0,60 | 0.025 | 0.025 | 0.50 | 0.80~1,25 | 0.44~0,65 |
P15 | K11578 | 0.05~0,15 | 0.30~0,60 | 0.025 | 0.025 | 1.15~1,65 | – | 0.44~0,65 |
P21 | K31545 | 0.05~0,15 | 0.30~0,60 | 0.025 | 0.025 | 0.50 | 2.65~3,35 | 0.80~1,60 |
P22 | K21590 | 0.05~0,15 | 0.30~0,60 | 0.025 | 0.025 | 0.50 | 1.90~2,60 | 0.87~1.13 |
P91 | K91560 | 0.08~0,12 | 0.30~0,60 | 0.020 | 0.010 | 0.20~0,50 | 8.00~9,50 | 0.85~1,05 |
P92 | K92460 | 0.07~0,13 | 0.30~0,60 | 0.020 | 0.010 | 0.50 | 8.50~9,50 | 0.30~0,60 |
A335 Gr P91 Rohrzusammensetzungsstandard
Si, % | Cr, % | C, % | Mo, % | MN, % | P, % | n, % | S, % | V, % | Ni, % | NB, % | Al, % |
0.2 An 0.5 | 8.0 An 9.5 | 0.08 An 0.12 | 0.85 An 1.05 | 0.3 An 0.6 | 0.02 | 0.03 An 0.07 | 0.01 | 0.18 An 0.25 | 0.4 | 0.06 An 0.10 | 0.04 |
ASTM A335 P91 Tabelle zur mechanischen Festigkeit von Rohren
Dehnbar | Zugeigenschaften | HB | Ertragseigenschaften |
20 | 585 | 250 | 415 |
Äquivalente Materialqualität von SA335 Gr P91-Rohren
UNS | ASTM | Äquivalent MATERIAL | ASME |
---|---|---|---|
K91560 | A335 P91 | K90901, T91, 1.4903, X10CrMoVNb9-1 | SA335 P 91 |
ASTM | ASME | ER G 3458 | UNS | BS | DIN | ISO | Abs | NK | LRS |
---|---|---|---|---|---|---|---|---|---|
A335P9 | SA335P9 | STPA 26 | S50400 | 3604 P1 629-470 | 2604 II TS38 |
Hintergrund: A335 P91-Stahl ist ein modifizierter 9Cr-1Mo-Stahl, hauptsächlich incorpo
A335P11 A335P91 A335P22 40cr 10CrMO910 35crmo 27SiMn Q345B 16Mn geschweißtes legiertes Stahlrohr
Einstufung von Legierungselementen wie V und Nb in den ursprünglichen martensitischen hitzebeständigen Stahl 9Cr-1Mo. Dieser Stahl verfügt über eine ausgezeichnete Oxidationsbeständigkeit bei hohen Temperaturen, Korrosionsbeständigkeit durch Dampf bei hohen Temperaturen, und Kriechfestigkeit, Dadurch wird das Strukturgewicht effektiv reduziert und eine weitverbreitete Anwendung in großen Kesselanlagen gefunden, Rohrleitungssysteme, und die petrochemische Industrie. allerdings, aufgrund der luftgekühlten martensitischen Natur des A335 P91-Stahls, es weist eine geringere Plastizität und eine schlechtere Schweißbarkeit auf, hohe Anforderungen an die Schweißprozesse stellen, Schlagzähigkeit von Schweißverbindungen, Sprödigkeit der Schweißnaht, Wärmebehandlung nach dem Schweißen, und Wärmeeinflusszonen von Schweißnähten. Beim herkömmlichen Schweißen von A335 P91-Stahl wird im Allgemeinen das manuelle Gas-Wolfram-Lichtbogenschweißen eingesetzt (GTAW) für Wurzelschweißen und manuelles Metalllichtbogenschweißen (SMAW) zum Befüllen und Verschließen, Dies erfordert eine strenge Kontrolle der Leitungsenergie, Vorheiztemperatur, und Zwischenlagentemperatur während des Schweißprozesses. Diese Methode erfordert ein hohes Maß an Schweißumgebung und Schweißerfähigkeiten, und die Effizienz beim manuellen Schweißen ist äußerst gering, kostet Zeit und Mühe, den Rohrleitungsfortschritt erheblich einschränken, Auswirkungen auf die Bauzeitpläne haben, Dies ist insbesondere bei dickwandigen Rohrleitungen mit großem Durchmesser der Fall.
Daher, Die rationelle Auswahl von Schweißparametern und -prozessen für A335 P91-Stahl und die Entwicklung von für die Produktion geeigneten Schweißprozessbedingungen haben einen erheblichen praktischen und wirtschaftlichen Wert.
Erfindungsinhalt: Um die Mängel der bestehenden Technologie zu beheben, Das durch die vorliegende Erfindung zu lösende technische Problem besteht darin, ein Verfahren zum Schweißen dickwandiger Hochdruckrohrleitungen aus Haushaltsstahl A335 P91 bereitzustellen, mit dem Ziel, die Schweißeffizienz und das Schweißen zu verbessern Qualität, Baukosten und Arbeitsintensität reduzieren, und das Arbeitsumfeld verbessern.
Um die oben genannten Ziele zu erreichen, Die vorliegende Erfindung verwendet die folgenden technischen Lösungen:
Ein Verfahren zum Schweißen dickwandiger Hochdruckrohrleitungen aus Haushaltsstahl A335 P91, bestehend aus den folgenden Schritten nacheinander:
(1) Bearbeitung der Fasen vor dem Schweißen: Bearbeiten Sie den Schweißbereich der zu verschweißenden Rohrleitung zu einer doppelten V-förmigen Fase, Führen Sie eine Farbeindringprüfung an der Fasenoberfläche durch, um sicherzustellen, dass keine Oberflächenrisse entstehen, und reinigen Sie die Fase und den Oberflächenrost, öl, und Oxide innerhalb eines 20-mm-Bereichs auf beiden Seiten der Abschrägung;
Fortsetzung des Schweißverfahrens für im Inland hergestellte dickwandige Hochdruckstahlrohre A335 P91:
- Wärmebehandlung nach dem Schweißen: Nach dem Schweißen, Versiegeln Sie beide Enden des Rohrs und erhitzen Sie den Bereich auf beiden Seiten der Schweißnaht mit elektrischer Heizung, mindestens 3 Mal der Breite der Schweißnaht und nicht weniger als 25 mm. Erhitzen Sie den Bereich auf einen Temperaturbereich von 750–770 °C und halten Sie ihn dort 2.5-4 Std., abhängig von der Rohrdicke.
Bitte beachten Sie, dass die Temperatur bei dieser Methode mit einem Infrarot-Thermometer überwacht wird. Dieses Schweißverfahren für dickwandige Hochdruckstahlrohre A335 P91 bietet die folgenden Vorteile:
-
Die Verwendung von Mehrschicht, Beim Mehrlagenschweißen wird die Querschnittsfläche jeder Schweißschicht verringert, Verbesserung der Zähigkeit der Schweißverbindung und Vermeidung einer Verengung der Wärmeeinflusszone bei dicken Schweißnähten, sowie das Erweichen der Schweißverbindung bei längerem Betrieb bei hohen Temperaturen.
-
Manuelles Gas-Wolfram-Lichtbogenschweißen (GTAW) Beim Wurzelschweißen ist die Schweißgeschwindigkeit geringer, Durch die Abdichtung beider Rohrenden lässt sich die Zwischenschichttemperatur besser kontrollieren. Automatisches Unterpulverschweißen (SAH) zum Füllen und Abdecken von Schichten verfügt über eine schnellere Schweißgeschwindigkeit und einen höheren Strom, Wärme schneller abgeben. Mindestens ein Ende des Rohres sollte unversiegelt sein, und kontinuierliches Schweißen kann durchgeführt werden, ohne dass eine Temperaturkontrolle zwischen den Schichten erforderlich ist.
-
Verwendung von Schweißdrähten mit kleinem Durchmesser (nicht mehr als 2,5 mm) und wasserstoffarme Flussmittel zum Schweißen können die lineare Energie während des Schweißprozesses reduzieren, Verbessern Sie die Schweißablagerungsrate, Verfeinern Sie die Körnung des Grundmaterials, und reduzieren die Möglichkeit von Fehlern wie Porosität und Rissen in der Schweißnaht.
-
In windigen Umgebungen, Die Schutzwirkung des automatischen Unterpulverschweißens ist besser als bei anderen Lichtbogenschweißverfahren.
-
Im Vergleich zu herkömmlichen manuellen Schweißmethoden, Diese Methode verkürzt effektiv den Wärmebehandlungs- und Schweißzyklus, verbessert die Schweißnaht Qualität und Schweißeffizienz, reduziert die Arbeitsintensität, und spart Baukosten.
Implementierungsbeispiel 1: Als Basismaterial wird die inländische A335P91-Rohrleitung DN350 verwendet, Es wird die folgende Schweißmethode angewendet:
(1) Der Schweißbereich des zu schweißenden Rohrs wird wie in der Abbildung gezeigt zu einer doppelten V-förmigen Nut verarbeitet 1, mit einer stumpfen Kantenhöhe von 1mm, einen Bodenwinkel von 60 ± 5° in Richtung der Rohrlänge, eine Höhe von 15mm, und einen oberen Winkel von 78–82° in Richtung der Rohrlänge. Die Nutoberfläche wird farblich geprüft, um sicherzustellen, dass die Nut keine Oberflächenrisse aufweist. Der Oberflächenrost, Ölflecken, Oxide, etc.. innerhalb von 20 mm auf beiden Seiten der Nut gereinigt werden;
(2) Die beiden Abschnitte des geschweißten Rohrs werden zusammengefügt, Achten Sie darauf, dass der stirnseitige Spalt der Stoßfuge 3–6 mm beträgt, die höhe ist gleichmäßig, und die Fehlausrichtung beträgt nicht mehr als 1 mm;
(3) Für das Bodenschweißen wird manuelles Argon-Lichtbogenschweißen GTAW verwendet. Vor dem Schweißen, Die Endanschlüsse des zu schweißenden Rohrs sind blockiert, und die Innenwand oder Rückseite der Schweißnaht wird zum Schutz mit Argongas gefüllt. Das zu verschweißende Stahlrohr wird vorgewärmt, und die Temperatur der Nut wird in Echtzeit mit einem Infrarot-Thermometer überwacht. Wenn die Temperatur 160℃ erreicht, Das Schweißen beginnt, Verwendung von ER90S-B9-Schweißdraht mit einem Durchmesser von 10 mm zum Schweißen von drei Schichten. Die Prozessparameter werden wie folgt ausgewählt: DC-Plus-Anschluss der Stromversorgung, Schweißstrom von 118A, Lichtbogenspannung von 14V, und Schweißgeschwindigkeit von 3–10 cm/min. Beim manuellen Argon-Lichtbogenschweißen GTAW sollten folgende Punkte beachtet werden: A) Die Oberfläche des zu schweißenden Werkstücks darf nicht durch den Lichtbogen entzündet werden, auf Strom geprüft, oder vorübergehend an eine Stütze oder Klemme angeschweißt;B) Das manuelle Argon-Lichtbogenschweißen beginnt am tiefsten Punkt des zu schweißenden Rohrs, und wird von zwei Personen symmetrisch verschweißt, wobei die Schweißnähte zwischen 100 und 150 mm versetzt sind; C) Beim manuellen Argon-Lichtbogenschweißen, Die Vorwärmtemperatur auf beiden Seiten der Nut sollte in Echtzeit überwacht werden, und die Vorwärmtemperatur sollte streng zwischen 150℃ und 200℃ liegen; D) Beim manuellen Argon-Lichtbogenschweißen, Windschutzmaßnahmen sollten getroffen werden, und die Windgeschwindigkeit in der Schweißumgebung sollte 2 m/s nicht überschreiten. Im zu schweißenden Rohr darf keine Zugluft vorhanden sein, und Feuchtigkeit, Regen, und Schneeschutzmaßnahmen sollten getroffen werden;
(4) Zum Füllen und Abdecken wird das automatische Unterpulverschweißen SAW verwendet. Vor dem automatischen Unterpulverschweißen Füllen und Abdecken, mindestens ein Ende des zu verschweißenden Rohres ist frei, und der Schweißbereich wird vorgewärmt. Wenn die Temperatur 200℃ erreicht, Das kontinuierliche Schweißen beginnt, Verwendung von EB9-Schweißdraht mit einem Durchmesser von 10 mm und MARATHON543-Schweißflussmittel für mehrschichtiges und mehrlagiges Füll- und Deckschweißen. Die UP-Schweißparameter werden wie folgt ausgewählt: DC-Rückwärtsanschluss der Stromversorgung, Schweißstrom von 280A, Lichtbogenspannung von 28V, und Schweißgeschwindigkeit von 25–45 cm/min.
Beim automatischen UP-Schweißen mit SAW sollten die folgenden Punkte beachtet werden:
A) Der Schweißdraht sollte sauber und trocken gehalten werden, und das Schweißpulver sollte an einem trockenen Ort gelagert werden, um eine Feuchtigkeitsaufnahme zu verhindern;
B) Der Schweißdraht sollte reibungslos und gleichmäßig zugeführt werden, und das Schweißflussmittel sollte rechtzeitig hinzugefügt werden, um das Schweißen sicherzustellen Qualität;
C) Die Schweißgeschwindigkeit sollte stabil sein, und die Schweißpistole sollte senkrecht zur Rohrachse gehalten werden, um die Konsistenz der Schweißraupe sicherzustellen;
D) Die Schweißschlacke sollte rechtzeitig nach Abschluss jeder Schweißschicht entfernt werden, und die Oberfläche der Schweißnaht sollte mit einer Drahtbürste oder einer Schleifscheibe gereinigt werden, um die Qualität der nächsten Schweißschicht sicherzustellen;
e) Der Schweißprozess soll in Echtzeit überwacht werden, und die Schweißparameter sollten rechtzeitig entsprechend der tatsächlichen Situation angepasst werden, um die Schweißqualität sicherzustellen. Nachdem das Schweißen abgeschlossen ist, Die Schweißoberfläche sollte visuell und durch zerstörungsfreie Prüfung überprüft werden, um sicherzustellen, dass keine Mängel wie Risse vorliegen, Poren, Schlackeneinschlüsse, und unvollständige Penetration. Endlich, Die Schweißverbindung sollte gemäß den Prozessanforderungen wärmebehandelt werden, um Schweißspannungen zu beseitigen und die mechanischen Eigenschaften der Schweißverbindung zu verbessern.
Implementierungsbeispiel 2: Als Grundmaterial wird die importierte A335P91-Rohrleitung DN500 verwendet, Es wird die folgende Schweißmethode angewendet:
(1) Der Schweißbereich des zu schweißenden Rohrs wird wie in der Abbildung gezeigt zu einer doppelten V-förmigen Nut verarbeitet 1, mit einer stumpfen Kantenhöhe von 1,5 mm, einen Bodenwinkel von 60 ± 5° in Richtung der Rohrlänge, eine Höhe von 20mm, und einen oberen Winkel von 78–82° in Richtung der Rohrlänge. Die Nutoberfläche wird farblich geprüft, um sicherzustellen, dass die Nut keine Oberflächenrisse aufweist. Der Oberflächenrost, Ölflecken, Oxide, etc.. innerhalb von 20 mm auf beiden Seiten der Nut gereinigt werden;
(2) Die beiden Abschnitte des geschweißten Rohrs werden zusammengefügt, Achten Sie darauf, dass der stirnseitige Spalt der Stoßfuge 4–8 mm beträgt, die höhe ist gleichmäßig, und die Fehlausrichtung beträgt nicht mehr als 1,5 mm;
(3) Für das Bodenschweißen wird das automatische Unterpulverschweißen SAW verwendet. Vor dem Schweißen, Die Endanschlüsse des zu schweißenden Rohrs sind blockiert, und die Innenwand oder Rückseite der Schweißnaht wird zum Schutz mit Argongas gefüllt. Das zu verschweißende Stahlrohr wird vorgewärmt, und die Temperatur der Nut wird in Echtzeit mit einem Infrarot-Thermometer überwacht. Wenn die Temperatur 200℃ erreicht, Das Schweißen beginnt, Verwendung von EB9-Schweißdraht mit einem Durchmesser von 10 mm und MARATHON543-Schweißflussmittel für mehrschichtiges und mehrlagiges Füll- und Deckschweißen. Die UP-Schweißparameter werden wie folgt ausgewählt: DC-Rückwärtsanschluss der Stromversorgung, Schweißstrom von 350A, Lichtbogenspannung von 32V, und Schweißgeschwindigkeit von 25–45 cm/min. Beim automatischen UP-Schweißen mit SAW sollten die folgenden Punkte beachtet werden: A) Der Schweißdraht sollte sauber und trocken gehalten werden, und das Schweißpulver sollte an einem trockenen Ort gelagert werden, um eine Feuchtigkeitsaufnahme zu verhindern; B) Der Schweißdraht sollte reibungslos und gleichmäßig zugeführt werden, und das Schweißpulver sollte rechtzeitig hinzugefügt werden, um die Schweißqualität sicherzustellen; C) Die Schweißgeschwindigkeit sollte stabil sein, und die Schweißpistole sollte senkrecht zur Rohrachse gehalten werden, um die Konsistenz der Schweißraupe sicherzustellen; D) Die Schweißschlacke sollte rechtzeitig nach Abschluss jeder Schweißschicht entfernt werden, und die Oberfläche der Schweißnaht sollte mit einer Drahtbürste oder einer Schleifscheibe gereinigt werden, um die Qualität der nächsten Schweißschicht sicherzustellen; e) Der Schweißprozess soll in Echtzeit überwacht werden, und die Schweißparameter sollten rechtzeitig entsprechend der tatsächlichen Situation angepasst werden, um die Schweißqualität sicherzustellen.
(4) Zum Füllen und Abdecken wird das automatische Unterpulverschweißen SAW verwendet. Vor dem automatischen Unterpulverschweißen Füllen und Abdecken, mindestens ein Ende des zu verschweißenden Rohres ist frei, und der Schweißbereich wird vorgewärmt. Wenn die Temperatur 250℃ erreicht, Das kontinuierliche Schweißen beginnt, Verwendung von EB9-Schweißdraht mit einem Durchmesser von 10 mm und MARATHON543-Schweißflussmittel für mehrschichtiges und mehrlagiges Füll- und Deckschweißen. Die UP-Schweißparameter werden wie folgt ausgewählt: DC-Rückwärtsanschluss der Stromversorgung, Schweißstrom von 450A, Lichtbogenspannung von 36V, und Schweißgeschwindigkeit von 25–45 cm/min. Nachdem das Schweißen abgeschlossen ist, Die Schweißoberfläche sollte visuell und durch zerstörungsfreie Prüfung überprüft werden, um sicherzustellen, dass keine Mängel wie Risse vorliegen, Poren, Schlackeneinschlüsse, und unvollständige Penetration. Endlich, Die Schweißverbindung sollte gemäß den Prozessanforderungen wärmebehandelt werden, um Schweißspannungen zu beseitigen und die mechanischen Eigenschaften der Schweißverbindung zu verbessern.
Sie müssen eingeloggt sein, um ein Kommentar abzugeben.