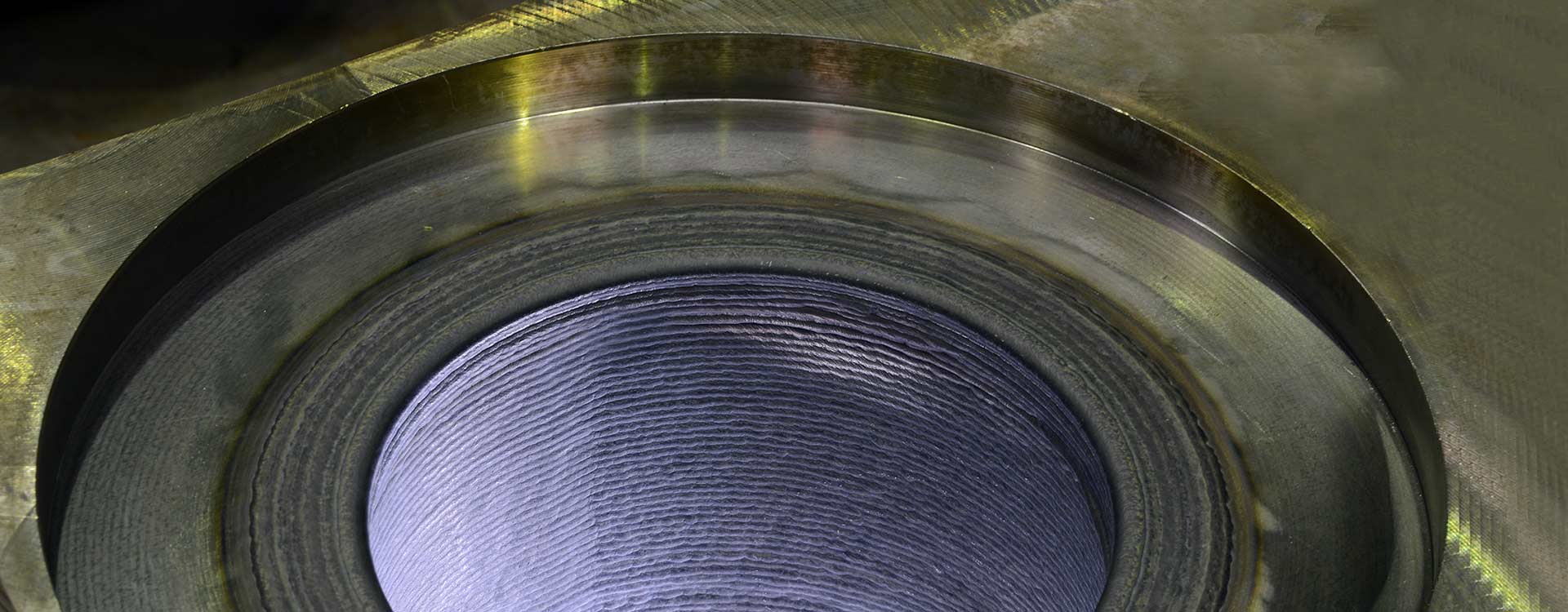
Research on Wear-Resistant Steel for Wear Layer of Composite Steel Pipes
Wear-resistant composite steel pipes are widely used in industries such as mining, power generation, cement production, and metallurgy, where the transportation of abrasive materials causes significant wear on pipelines. These pipes typically consist of an outer steel layer for structural strength and an inner wear-resistant layer designed to withstand abrasion, erosion, and corrosion. The wear-resistant layer plays a critical role in extending the service life of the pipe under harsh operating conditions. This research focuses on the study of steel used in the wear layer of composite steel pipes, analyzing material composition, mechanical properties, and performance parameters.
The primary objective of this study is to identify suitable steel grades for the wear layer, evaluate their performance through key parameters such as hardness, toughness, and wear resistance, and present the findings in a structured format. The research also explores the influence of alloying elements and heat treatment processes on the performance of wear-resistant steel. A detailed table of parameters will be provided to summarize the properties of various steel grades, followed by an in-depth analysis of their suitability for wear-resistant applications.
1. Introduction to Wear-Resistant Composite Steel Pipes
Composite steel pipes designed for wear resistance typically consist of two or more layers: an outer structural layer and an inner wear-resistant layer. The outer layer is often made from carbon steel or low-alloy steel to provide mechanical strength and flexibility, while the inner layer, or wear layer, is engineered to resist abrasive wear, erosion, and sometimes corrosion. The wear layer can be made from various materials, including ceramics, high-chromium cast iron, or specially alloyed steel. In this research, the focus is on steel-based wear layers due to their balance of wear resistance, toughness, and cost-effectiveness.
The wear layer must endure extreme conditions, such as the abrasive impact of coal slurry, mineral ores, or cement clinker. Traditional carbon steel pipes fail quickly under such conditions due to their limited hardness and wear resistance. To address this, wear-resistant steels with high hardness, good toughness, and resistance to impact and fatigue are developed. These steels often incorporate alloying elements such as chromium (Cr), molybdenum (Mo), vanadium (V), and nickel (Ni) to enhance their properties.
The selection of wear-resistant steel for the inner layer of composite pipes involves a trade-off between hardness and toughness. High hardness improves resistance to abrasion but may reduce toughness, making the material brittle and prone to cracking under impact. Conversely, high toughness enhances resistance to impact but may compromise wear resistance. This study examines several steel grades to determine their suitability for wear layers, focusing on their chemical composition, mechanical properties, and wear performance.
2. Material Selection for Wear-Resistant Steel
The choice of steel for the wear layer of composite pipes depends on several factors, including the operating environment, type of abrasive material, and cost considerations. Commonly used wear-resistant steels include high-chromium white cast iron, martensitic steel, and bainitic steel. Each type has distinct advantages and limitations, which are discussed below.
2.1 High-Chromium White Cast Iron
High-chromium white cast iron is widely used in wear-resistant applications due to its excellent hardness and abrasion resistance. The high chromium content (typically 15–30%) promotes the formation of hard chromium carbides (M7C3 type) in a martensitic matrix, which significantly enhances wear resistance. However, its brittleness limits its use in applications involving high impact.
2.2 Martensitic Steel
Martensitic steels are heat-treated to achieve a fully martensitic microstructure, which provides high hardness and wear resistance. These steels are often alloyed with elements like chromium, molybdenum, and vanadium to improve hardenability and wear properties. Martensitic steels offer a better balance of hardness and toughness compared to high-chromium cast iron, making them suitable for applications with moderate impact.
2.3 Bainitic Steel
Bainitic steels are characterized by a bainitic microstructure, which offers a combination of high strength, toughness, and wear resistance. These steels are often used in applications requiring resistance to both abrasion and impact. The addition of alloying elements such as boron (B) and molybdenum enhances the formation of bainite during heat treatment.
3. Parameters of Wear-Resistant Steel for Wear Layer
To evaluate the suitability of different steel grades for the wear layer of composite steel pipes, several key parameters are considered, including chemical composition, hardness, impact toughness, and wear rate. These parameters are summarized in the table below.
Steel Grade | Chemical Composition (%) | Hardness (HRC) | Impact Toughness (J/cm²) | Wear Rate (mm³/N·m) | Heat Treatment |
---|---|---|---|---|---|
High-Cr Cast Iron (A) | C: 2.5, Cr: 25, Mo: 1.0, Si: 0.8 | 58–62 | 5–10 | 1.2 × 10⁻⁵ | As-cast + Tempering |
Martensitic Steel (B) | C: 0.4, Cr: 12, Mo: 0.5, V: 0.2 | 50–55 | 20–30 | 2.5 × 10⁻⁵ | Quenching + Tempering |
Bainitic Steel (C) | C: 0.3, Cr: 3, Mo: 0.5, B: 0.003 | 45–50 | 40–50 | 3.0 × 10⁻⁵ | Austempering |
Low-Alloy Steel (D) | C: 0.2, Cr: 1.5, Mn: 1.0 | 40–45 | 60–80 | 5.0 × 10⁻⁵ | Normalizing |
Notes on Table Parameters:
- Chemical Composition: The percentage of alloying elements affects the microstructure and mechanical properties of the steel.
- Hardness: Measured in Rockwell Hardness (HRC), higher values indicate better resistance to abrasion.
- Impact Toughness: Measured in Joules per square centimeter (J/cm²), higher values indicate better resistance to impact.
- Wear Rate: Measured in cubic millimeters per Newton-meter (mm³/N·m), lower values indicate better wear resistance.
- Heat Treatment: The process used to achieve the desired microstructure and properties.
4. Analysis of Steel Parameters for Wear Layer Applications
4.1 High-Chromium Cast Iron (Steel A)
High-chromium cast iron (Steel A) exhibits the highest hardness among the evaluated materials, with an HRC range of 58–62. This is attributed to the presence of hard M7C3 carbides in a martensitic matrix. The wear rate of 1.2 × 10⁻⁵ mm³/N·m is the lowest, indicating excellent wear resistance. However, its impact toughness is poor (5–10 J/cm²), making it susceptible to cracking under high-impact conditions. This steel is best suited for applications involving pure abrasion, such as transporting fine coal ash or cement slurry, where impact is minimal.
4.2 Martensitic Steel (Steel B)
Martensitic steel (Steel B) offers a balanced combination of hardness (50–55 HRC) and impact toughness (20–30 J/cm²). Its wear rate of 2.5 × 10⁻⁵ mm³/N·m is higher than that of high-chromium cast iron but still acceptable for many applications. The addition of 12% chromium enhances corrosion resistance, while molybdenum and vanadium improve hardenability and wear resistance. This steel is suitable for applications involving moderate impact and abrasion, such as transporting coarse mineral ores.
4.3 Bainitic Steel (Steel C)
Bainitic steel (Steel C) provides the best impact toughness (40–50 J/cm²) among the wear-resistant steels evaluated, with a hardness of 45–50 HRC. Its wear rate of 3.0 × 10⁻⁵ mm³/N·m is higher than that of martensitic steel, indicating slightly lower wear resistance. The bainitic microstructure, achieved through austempering, offers excellent resistance to fatigue and impact. This steel is ideal for applications involving high impact and moderate abrasion, such as pipelines in mining operations with large particle sizes.
4.4 Low-Alloy Steel (Steel D)
Low-alloy steel (Steel D) serves as a baseline for comparison. With a hardness of 40–45 HRC and a wear rate of 5.0 × 10⁻⁵ mm³/N·m, it has the lowest wear resistance among the evaluated materials. However, its impact toughness (60–80 J/cm²) is the highest, making it suitable for applications where impact resistance is critical, but wear resistance is less of a concern. This steel is not typically used for wear layers but can serve as an outer structural layer in composite pipes.
5. Influence of Alloying Elements and Heat Treatment
The performance of wear-resistant steel is heavily influenced by its chemical composition and heat treatment process. Below is a detailed discussion of these factors.
5.1 Role of Alloying Elements
Alloying elements play a critical role in determining the microstructure and properties of wear-resistant steel. Chromium is the most important element for enhancing hardness and wear resistance by forming carbides. In high-chromium cast iron (Steel A), the 25% chromium content results in a high volume fraction of M7C3 carbides, contributing to its exceptional wear resistance. Molybdenum improves hardenability and resistance to tempering, while vanadium refines the grain structure and enhances wear resistance by forming fine carbides. In bainitic steel (Steel C), the addition of boron promotes the formation of bainite, improving toughness and fatigue resistance.
5.2 Effect of Heat Treatment
Heat treatment processes such as quenching, tempering, and austempering are used to achieve the desired microstructure and properties. For martensitic steel (Steel B), quenching followed by tempering produces a fully martensitic microstructure with high hardness and moderate toughness. Austempering, used for bainitic steel (Steel C), involves isothermal transformation to form bainite, which offers a good balance of hardness and toughness. High-chromium cast iron (Steel A) is typically used in the as-cast condition with optional tempering to relieve residual stresses.
6. Practical Considerations for Wear Layer Design
When designing the wear layer of composite steel pipes, several practical considerations must be addressed:
-
- Operating Environment: The type of abrasive material, particle size, velocity, and impact conditions dictate the choice of steel. For fine abrasives with low impact, high-chromium cast iron is ideal. For coarse materials with high impact, bainitic steel is preferable.
- Cost vs. Performance: High-chromium cast iron is more expensive than martensitic or bainitic steel but offers superior wear resistance. The choice depends on the required service life and budget constraints.
- Manufacturability: The wear layer must be metallurgically bonded to the outer steel layer, often through centrifugal casting or cladding. The steel’s compatibility with these processes must be considered.
- Maintenance and Replacement: The wear layer should be designed for easy replacement if necessary. Composite pipes with detachable wear layers can reduce downtime and maintenance costs.
7. Conclusion
The wear-resistant layer of composite steel pipes plays a crucial role in extending the service life of pipelines in abrasive environments. This research evaluated four steel grades for their suitability as wear layers: high-chromium cast iron, martensitic steel, bainitic steel, and low-alloy steel. High-chromium cast iron exhibited the best wear resistance but poor toughness, making it suitable for low-impact applications. Martensitic steel offered a balanced combination of hardness and toughness, while bainitic steel provided the best impact resistance. Low-alloy steel, while tough, lacked the necessary wear resistance for most applications.
The choice of steel depends on the specific operating conditions, including the type of abrasive material, impact level, and cost constraints. Alloying elements and heat treatment processes significantly influence the performance of wear-resistant steel, allowing for tailored solutions to meet diverse requirements. The parameters presented in the table provide a comprehensive overview of the properties of each steel grade, serving as a valuable reference for engineers and designers.
You must be logged in to post a comment.