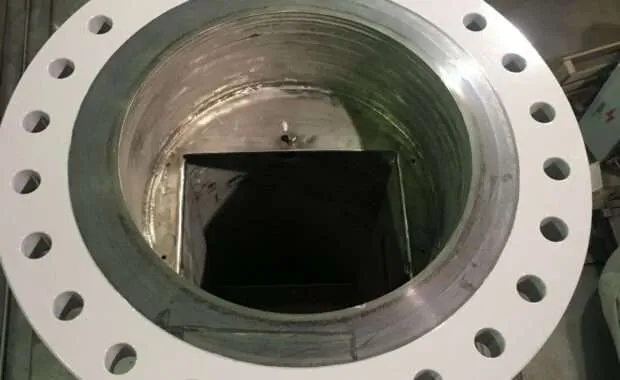
Clad Flange – Cladding Flange – Weld Overlay Flange
Main Headings | Subheadings |
---|---|
H1: Introduction to Clad Flange/Cladding Flange/Weld Overlay Flange | – Definition of Clad Flanges and Their Purpose |
– Why Cladding Is Important in Industrial Piping | |
H2: Understanding Cladding and Overlay Process | – What Is Cladding? |
– Types of Cladding Techniques | |
– What Is Weld Overlay? | |
H2: Components and Structure of Clad Flanges | – Base Material |
– Cladding Material | |
– Bonding Interface | |
H2: Material Selection for Clad Flanges | – Common Base Materials: Carbon Steel, Alloy Steel |
– Common Cladding Materials: Stainless Steel, Nickel Alloys | |
– Material Combinations Based on Application | |
H2: Manufacturing Process of Clad Flanges | – Weld Overlay Process |
– Explosive Cladding | |
– Roll Bonding | |
H2: Design and Structural Features | – Dimensional Standards (ASME, ANSI, API, DIN) |
– Thickness and Bonding Ratio | |
– Pressure Ratings and Classes | |
H2: Types of Clad Flanges | – Weld Overlay Flanges |
– Explosively Clad Flanges | |
– Roll Bonded Flanges | |
H2: Applications of Clad Flanges | – Oil and Gas Industries |
– Petrochemical and Refinery Applications | |
– Chemical Processing Industries | |
– Power Generation | |
H2: Advantages of Clad Flanges | – Corrosion Resistance |
– Cost Efficiency | |
– Enhanced Durability and Longevity | |
H2: Challenges and Limitations of Clad Flanges | – Welding and Bonding Challenges |
– Compatibility Issues | |
– Cost Considerations for Specialized Materials | |
H2: Differences Between Clad Flanges and Solid Flanges | – Clad Flange vs Stainless Steel Flange |
– Clad Flange vs Carbon Steel Flange | |
H2: Inspection and Quality Control for Clad Flanges | – Non-Destructive Testing (NDT) Methods |
– Bonding Quality Check | |
– Dimensional and Pressure Testing | |
H2: Clad Flange Dimensions Table | – ANSI/ASME Pressure Ratings Table |
– Dimensional Data for Classes 150, 300, and 600 | |
H2: Cost and Pricing Factors | – Factors Influencing Cost (Material, Cladding Method) |
– Market Trends and Demand | |
H2: Maintenance and Lifespan of Clad Flanges | – Routine Inspection and Maintenance |
– Common Problems and Solutions | |
H2: Buying Guide for Clad Flanges | – Key Selection Factors (Material, Pressure Rating) |
– How to Identify Quality Clad Flanges | |
H2: Frequently Asked Questions (FAQs) | – What Is a Clad Flange? |
– How Are Clad Flanges Manufactured? | |
– What Are the Benefits of Clad Flanges? | |
– What Applications Require Clad Flanges? | |
– How Do You Inspect Clad Flanges? | |
H2: Conclusion | – Summary of Key Points |
– Final Thoughts on the Importance of Clad Flanges |
Long-Form Article on Clad Flange/Cladding Flange/Weld Overlay Flange
H1: Introduction to Clad Flange/Cladding Flange/Weld Overlay Flange
A clad flange (also known as cladding flange or weld overlay flange) is a specialized flange that combines two different materials: a base material for structural strength and a corrosion-resistant layer (cladding) to protect against harsh environments. Cladding ensures that flanges can withstand corrosive fluids without compromising mechanical integrity, making them a cost-effective alternative to solid exotic alloy flanges.
The significance of cladding in industrial piping systems lies in its ability to combine the best of both worlds: the strength of carbon or alloy steel and the corrosion resistance of materials like stainless steel, nickel, or titanium.
H2: Understanding Cladding and Overlay Process
What Is Cladding?
Cladding is the process of bonding a corrosion-resistant material onto a base metal to enhance its resistance to corrosion and wear without replacing the entire component.
Types of Cladding Techniques
- Weld Overlay: A corrosion-resistant alloy (CRA) is welded onto the flange surface.
- Explosive Cladding: High-energy explosives bond the cladding material to the base metal.
- Roll Bonding: Rolling pressure bonds the corrosion-resistant layer with the base material.
What Is Weld Overlay?
Weld overlay is a technique where a corrosion-resistant material is applied in layers using welding processes like submerged arc welding (SAW) or gas metal arc welding (GMAW) to form a metallurgically bonded layer.
H2: Components and Structure of Clad Flanges
A clad flange consists of:
- Base Material: Provides mechanical strength and structural support. Common base materials include carbon steel or alloy steel.
- Cladding Material: A thin layer of corrosion-resistant material such as stainless steel, nickel, or titanium.
- Bonding Interface: The boundary between the base and cladding layers, crucial for the flange’s durability.
H2: Material Selection for Clad Flanges
Common Base Materials
- Carbon Steel (ASTM A105)
- Low Alloy Steel (ASTM A182 F22)
- High-Strength Steel
Common Cladding Materials
- Stainless Steel (304, 316, 321, etc.)
- Nickel Alloys (Inconel 625, Monel 400)
- Titanium Alloys
Material Combinations Based on Application
Base Material | Cladding Material | Application |
---|---|---|
Carbon Steel | Stainless Steel 316L | Chemical and Petrochemical Plants |
Alloy Steel | Inconel 625 | High-Temperature Pipelines |
Carbon Steel | Titanium | Corrosive Offshore Environments |
H2: Manufacturing Process of Clad Flanges
1. Weld Overlay Process
In weld overlay, a layer of CRA material is welded onto the base flange using arc welding techniques. This process creates a strong metallurgical bond.
2. Explosive Cladding
This process uses controlled explosions to bond the corrosion-resistant material to the base metal at high pressure.
3. Roll Bonding
The CRA layer is rolled and bonded under extreme pressure, creating a uniform interface.
H2: Design and Structural Features
Dimensional Standards
Clad flanges are manufactured according to the following standards:
- ASME B16.5: Pipe flanges and flanged fittings.
- API 6A: Flanges for oil and gas industries.
- DIN EN 1092-1: European flange standards.
Pressure Ratings
Clad flanges are available in classes:
- Class 150
- Class 300
- Class 600
- Class 900
- Class 1500
Bonding Thickness
The thickness of the cladding layer typically ranges between 2.5mm to 3mm, depending on the service conditions.
H2: Types of Clad Flanges
- Weld Overlay Flanges: CRA material applied through welding.
- Explosively Clad Flanges: Bonded using high-energy explosions.
- Roll Bonded Flanges: Pressure-rolled to achieve a strong bond.
H2: Applications of Clad Flanges
- Oil and Gas Industries: Offshore and onshore pipelines.
- Petrochemical Plants: Transport of corrosive chemicals.
- Power Generation: Steam systems and heat exchangers.
- Chemical Processing: Highly acidic and alkaline environments.
H2: Advantages of Clad Flanges
- Corrosion Resistance: Protects against harsh chemicals and environments.
- Cost Efficiency: Less expensive than solid alloy flanges.
- Enhanced Longevity: Combines durability with performance.
H2: Differences Between Clad Flanges and Solid Flanges
Aspect | Clad Flange | Solid Flange |
---|---|---|
Cost | More cost-effective | More expensive |
Corrosion Resistance | Excellent due to cladding | Inherent corrosion resistance |
Material | Dual-material design | Single alloy throughout |
H2: Inspection and Quality Control for Clad Flanges
- Non-Destructive Testing (NDT): Ultrasonic Testing (UT) and Dye Penetrant Testing (DPT).
- Bonding Quality: Ensuring strong adhesion between base and cladding.
H2: Frequently Asked Questions (FAQs)
1. What Is a Clad Flange?
A flange with a corrosion-resistant layer bonded to a strong base material.
2. How Are Clad Flanges Manufactured?
Through weld overlay, explosive bonding, or roll bonding.
3. What Are the Benefits of Clad Flanges?
Cost-effectiveness, corrosion resistance, and durability.
4. What Applications Require Clad Flanges?
Oil & gas, petrochemical, and chemical industries.
5. How Do You Inspect Clad Flanges?
Using ultrasonic and dye penetrant testing.
H2: Maintenance and Lifespan of Clad Flanges
Proper maintenance ensures that clad flanges deliver long-term reliability, even in harsh environments.
Routine Inspection and Maintenance
- Visual Inspection: Regularly check for signs of corrosion, wear, or damage.
- Non-Destructive Testing (NDT): Use ultrasonic and radiographic testing to verify the bond integrity between the base and cladding material.
- Pressure Testing: Periodic pressure tests ensure the flange can handle its designated operating conditions.
Common Problems and Solutions
Problem | Cause | Solution |
---|---|---|
Delamination of Cladding | Poor bonding during manufacturing | Use high-quality bonding processes. |
Localized Corrosion | Chemical exposure or material mismatch | Choose proper cladding material. |
Cracking in Weld Overlay | Poor welding techniques | Use certified welding procedures. |
Extending the Lifespan
- Use appropriate gaskets to ensure tight and leak-proof connections.
- Perform regular inspections under severe operating conditions.
- Ensure proper handling and storage to avoid mechanical damage before installation.
With appropriate maintenance, clad flanges can have a lifespan exceeding 20-30 years, even in aggressive service environments.
H2: Clad Flange Dimensions Table
Clad flanges are manufactured to precise standards, with dimensions tailored to match industry requirements. Below are standard ASME B16.5 dimensional data for Class 150, 300, and 600 pressure ratings.
Class 150 Dimensions (ASME B16.5)
Nominal Pipe Size (NPS) | Flange OD (mm) | Thickness (mm) | Cladding Thickness (mm) |
---|---|---|---|
1 | 88.9 | 12.7 | 3.0 |
2 | 152.4 | 19.1 | 3.0 |
4 | 228.6 | 23.9 | 3.0 |
6 | 279.4 | 25.4 | 3.0 |
8 | 342.9 | 28.6 | 3.0 |
Class 300 Dimensions (ASME B16.5)
Nominal Pipe Size (NPS) | Flange OD (mm) | Thickness (mm) | Cladding Thickness (mm) |
---|---|---|---|
1 | 95.3 | 15.9 | 3.0 |
2 | 165.1 | 22.4 | 3.0 |
4 | 254.0 | 28.6 | 3.0 |
6 | 320.7 | 31.8 | 3.0 |
8 | 381.0 | 35.1 | 3.0 |
Class 600 Dimensions (ASME B16.5)
Nominal Pipe Size (NPS) | Flange OD (mm) | Thickness (mm) | Cladding Thickness (mm) |
---|---|---|---|
1 | 101.6 | 19.1 | 3.0 |
2 | 190.5 | 28.6 | 3.0 |
4 | 279.4 | 38.1 | 3.0 |
6 | 368.3 | 41.3 | 3.0 |
8 | 451.0 | 47.8 | 3.0 |
H2: Cost and Pricing Factors
Several factors influence the cost of clad flanges:
1. Material Costs
- The price of base materials (e.g., carbon steel) is lower, but cladding materials (e.g., stainless steel, Inconel) significantly increase the overall cost.
2. Manufacturing Technique
- Weld overlay is typically less expensive than explosive cladding but may have limitations in high-pressure applications.
- Roll bonding is cost-efficient for large-scale production.
3. Pressure Class and Size
- Higher-pressure classes (Class 600 and above) require thicker and stronger materials, increasing costs.
4. Market Trends
- Demand for corrosion-resistant materials in industries like oil and gas influences pricing.
Approximate Pricing:
Flange Type | Material Combination | Estimated Cost (USD) |
---|---|---|
Weld Overlay Flange | Carbon Steel + SS 316L | $100 – $500 |
Explosively Clad Flange | Carbon Steel + Inconel 625 | $400 – $1,200 |
Roll Bonded Clad Flange | Alloy Steel + SS 321 | $150 – $700 |
H2: Buying Guide for Clad Flanges
When purchasing clad flanges, consider the following:
1. Material Selection
- Choose base and cladding materials based on the operating environment (temperature, pressure, and corrosive nature).
2. Pressure Rating
- Ensure the flange meets the required ASME pressure class.
3. Standards Compliance
- Look for certifications like ASME B16.5, API 6A, and DIN EN 1092-1.
4. Vendor Reliability
- Buy from certified manufacturers with quality assurance processes.
5. Inspection Reports
- Ensure flanges come with non-destructive testing (NDT) reports and dimensional checks.
H2: Frequently Asked Questions (FAQs)
1. What Is a Clad Flange?
A flange made by bonding a corrosion-resistant alloy (CRA) to a base metal for improved corrosion resistance and cost-efficiency.
2. How Are Clad Flanges Manufactured?
Through processes like weld overlay, explosive cladding, and roll bonding.
3. What Are the Benefits of Clad Flanges?
Clad flanges provide superior corrosion resistance, durability, and cost savings compared to solid alloy flanges.
4. What Applications Require Clad Flanges?
Industries such as oil and gas, petrochemical, power generation, and chemical processing.
5. How Do You Inspect Clad Flanges?
Using ultrasonic testing (UT), dye penetrant testing (DPT), and dimensional checks.
H2: Conclusion
Clad flanges are a critical innovation in industrial piping systems, offering a reliable and cost-effective solution for handling corrosive fluids. By combining the mechanical strength of base metals like carbon steel with the corrosion resistance of alloys like stainless steel and Inconel, clad flanges provide long-term performance in challenging environments.
Understanding the manufacturing processes, material combinations, and applications allows industries to select the right type of clad flange for their operations. With proper maintenance and quality control, clad flanges offer unmatched durability, safety, and cost savings.
You must be logged in to post a comment.