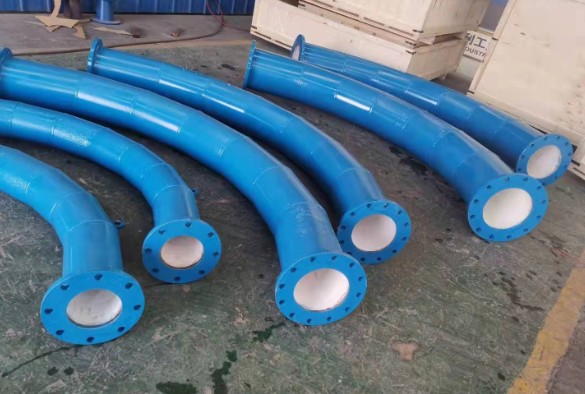
Ceramic Lined Elbow: Comprehensive Analysis
Ceramic lined elbows are critical components in industrial piping systems, designed to handle abrasive, corrosive, and high-temperature materials. These elbows combine the durability of steel with the exceptional wear and corrosion resistance of ceramic linings, making them indispensable in industries such as power generation, mining, metallurgy, and chemical processing. This document provides an in-depth analysis of ceramic lined elbows, including a parameters table, material composition, mechanical properties, wear resistance, bending angles, and a detailed discussion of their performance and applications.
Parameters Table
Parameter | Description | Typical Values |
---|---|---|
Outer Pipe Material | Base material of the elbow | Carbon Steel (e.g., 20# seamless steel), Stainless Steel |
Ceramic Lining Material | Inner lining material | Alumina (Al₂O₃, ≥90%), Zirconia Toughened Alumina (ZTA) |
Pipe Diameter | Inner diameter of the pipe | 0.5 inch to 24 inches (customizable) |
Ceramic Thickness | Thickness of the ceramic lining | 6 mm – 25 mm |
Bending Angle | Angle of direction change | 22.5°, 45°, 90°, 180° (custom angles available) |
Bend Radius | Radius of curvature | 1.5D – 5D (D = pipe diameter) |
Operating Temperature | Maximum temperature resistance | -50°C to 900°C (long-term), up to 2000°C (short-term) |
Pressure Resistance | Hoop strength | 300 – 500 MPa |
Wear Resistance | Relative to carbon steel | 15 – 20 times higher |
Microhardness | Hardness of ceramic lining | HV 1000 – 1600 |
Density | Density of ceramic lining | 3.62 g/cm³ (Alumina) |
Service Life | Expected lifespan under abrasive conditions | 5 – 20 years (depending on application) |
Material Composition
Ceramic lined elbows consist of two primary material layers: the outer steel pipe and the inner ceramic lining. The outer pipe is typically made from carbon steel (e.g., 20# seamless steel) or stainless steel, providing structural integrity and ease of welding or flanging. The ceramic lining, usually composed of high-purity alumina (Al₂O₃) or zirconia toughened alumina (ZTA), is bonded to the inner surface using high-temperature-resistant adhesives or mechanical interlocking techniques.
Outer Pipe Material
The outer pipe serves as the structural backbone of the elbow. Carbon steel is commonly used due to its cost-effectiveness, high strength, and weldability. For applications involving corrosive environments, stainless steel may be preferred to enhance corrosion resistance. The steel layer ensures the elbow can withstand mechanical stresses, such as pressure and impact, while facilitating integration into existing piping systems.
Ceramic Lining Material
The ceramic lining is the key to the elbow’s exceptional performance. Alumina, with an Al₂O₃ content of 90% or higher, is the most widely used material due to its high hardness, wear resistance, and thermal stability. Zirconia toughened alumina (ZTA) is an advanced variant that offers improved toughness and impact resistance, making it suitable for dynamic systems with high mechanical shock. The ceramic layer is typically applied as tiles, sleeves, or a monolithic coating, depending on the manufacturing process.
The ceramic material’s fine grain structure and high density contribute to its durability. For instance, alumina ceramics exhibit a diamond-like hardness and superior mechanical strength, making them ideal for demanding applications. The choice of ceramic material can be tailored to specific operational requirements, such as extreme abrasion or chemical exposure.
Mechanical Properties
The mechanical properties of ceramic lined elbows are a composite of the steel outer layer and the ceramic inner lining. These properties determine the elbow’s ability to withstand pressure, impact, and thermal shock, ensuring reliable performance in harsh environments.
Strength
The hoop strength of ceramic lined elbows, which measures resistance to radial pressure, typically ranges from 300 to 500 MPa. This strength is primarily derived from the steel outer layer, which provides structural support. The ceramic lining, while brittle, contributes to the overall integrity by resisting surface degradation and maintaining the elbow’s shape under abrasive conditions.
Flexural strength, or bending strength, is a critical property for the ceramic lining. Alumina ceramics exhibit high flexural strength, often tested via 3-point or 4-point bending tests. Values can exceed 300 MPa, depending on grain size, porosity, and manufacturing quality. However, the ceramic’s brittleness means it relies on the steel layer to absorb bending stresses without cracking.
Hardness
The microhardness of the ceramic lining, measured on the Vickers scale, ranges from HV 1000 to 1600 for alumina-based materials. This hardness is significantly higher than that of carbon steel (approximately HV 150-200 after quenching) or even tungsten carbide (HV 1200-1500), making the ceramic layer exceptionally resistant to scratching and wear. The high hardness ensures the elbow can handle abrasive materials like coal powder, ash, or ore slurry without significant surface damage.
Toughness and Impact Resistance
While alumina ceramics are inherently brittle, their toughness can be enhanced by using ZTA or by optimizing the bonding with the steel layer. The steel outer pipe provides excellent impact resistance, absorbing mechanical shocks that might otherwise fracture the ceramic lining. In practice, ceramic lined elbows have demonstrated resilience in applications involving high-velocity particle impacts, such as pneumatic conveying systems.
Thermal Shock Resistance
Ceramic lined elbows can operate in temperatures ranging from -50°C to 900°C for extended periods, with short-term resistance up to 2000°C. The ceramic lining’s low thermal expansion coefficient minimizes cracking under rapid temperature changes, while the steel layer provides additional stability. This thermal shock resistance is crucial in industries like power generation, where pipelines may experience fluctuating temperatures.
Wear Resistance
Wear resistance is the defining characteristic of ceramic lined elbows, setting them apart from traditional steel or cast iron fittings. The ceramic lining’s ability to withstand abrasion and erosion extends the elbow’s service life by 15 to 20 times compared to unlined carbon steel elbows, reducing maintenance costs and downtime.
Mechanism of Wear Resistance
The high hardness and smooth surface of the ceramic lining minimize material loss due to abrasive wear. In applications involving high-velocity slurries or powders (e.g., coal ash, limestone, or sand), the ceramic layer resists erosion by reducing friction and preventing particle embedment. The wear resistance is quantified by comparing the ceramic lining’s performance to that of carbon steel, with studies showing a lifespan increase of up to 20 times in abrasive conditions.
The ceramic’s low friction factor at low impingement angles further enhances wear resistance by reducing the abrasive impact of particles. This property is particularly beneficial in elbows, where flow direction changes increase turbulence and wear. The smooth inner surface also prevents material buildup, ensuring consistent flow rates and reducing the risk of blockages.
Comparative Analysis
Compared to other wear-resistant materials, such as cast basalt or alloy steel, ceramic linings offer superior performance. Cast basalt, while durable, has lower wear resistance and is prone to cracking under high-velocity impacts. Alloy steel, with a surface hardness of approximately 60 HRC, wears out faster than ceramics (80+ HRC equivalent). In real-world applications, such as coal-fired power plants, ceramic lined elbows have outlasted thick-walled steel elbows by a factor of five or more.
Service Life
The service life of a ceramic lined elbow depends on the application’s severity. In pneumatic conveying systems for fly ash or cement, where abrasion is intense, the ceramic lining can last 5 to 10 years, compared to 1-2 years for steel elbows. In less abrasive conditions, such as chemical processing, lifespans can exceed 20 years. The average wear rate of the ceramic layer is approximately 0.5-1 mm per year, meaning a 6 mm lining could last over 5 years in demanding environments.
Bending Angles
Ceramic lined elbows are available in various bending angles to accommodate different piping layouts. The angle determines the degree of direction change, affecting flow dynamics and wear patterns within the elbow.
Standard Bending Angles
The most common bending angles are 22.5°, 45°, 90°, and 180°, though custom angles can be manufactured to meet specific requirements. These angles correspond to standard pipe fitting designs:
- 22.5° Elbow: Used for slight directional adjustments in piping systems.
- 45° Elbow: Provides a moderate change in direction, reducing turbulence compared to 90° elbows.
- 90° Elbow: The most widely used angle for perpendicular turns, common in tight layouts.
- 180° Elbow: A return bend for reversing flow direction, often used in heat exchangers or compact systems.
Bend Radius
The bend radius, typically expressed as a multiple of the pipe diameter (D), ranges from 1.5D to 5D. A larger radius (e.g., 5D) results in a gentler curve, reducing flow resistance and wear concentration at the bend. Short-radius elbows (1.5D) are more compact but experience higher wear due to sharper turns. The choice of radius depends on space constraints, flow requirements, and wear considerations.
Impact on Performance
The bending angle and radius significantly influence the elbow’s performance. Sharper angles (e.g., 90°) and smaller radii increase turbulence and particle impact, accelerating wear at the outer curve. Ceramic linings mitigate this by providing a hard, smooth surface that deflects abrasive particles. In contrast, larger radii and smaller angles distribute wear more evenly, enhancing longevity.
Detailed Analysis
Ceramic lined elbows represent a fusion of advanced materials and engineering design, tailored to address the challenges of abrasive and corrosive material transport. This section explores their manufacturing processes, applications, advantages, limitations, and recent advancements, providing a holistic understanding of their role in modern industry.
Manufacturing Processes
Ceramic lined elbows are produced using several techniques, each influencing their performance and cost:
- Centrifugal Casting: Molten alumina is cast inside a steel pipe under centrifugal force, forming a dense, uniform ceramic layer. This method ensures high bonding strength and is ideal for large-diameter elbows.
- Tile Lining: Pre-formed ceramic tiles are adhered to the steel pipe’s inner surface using high-temperature adhesives or mechanical interlocking. This approach allows precise control over lining thickness and is suitable for complex shapes.
- Sleeve Lining: A pre-fabricated ceramic sleeve is inserted into the steel pipe and secured with adhesives or shrink-fitting. This method is efficient for standard elbows and ensures a smooth inner surface.
The steel pipe is typically formed by hot bending or welding, with seamless options preferred for high-pressure applications. Post-lining, the elbow undergoes heat treatment to solidify the ceramic-steel bond, ensuring durability under operational stresses.
Applications
Ceramic lined elbows are deployed across a wide range of industries due to their versatility and robustness:
- Power Generation: Used in coal-fired plants for conveying pulverized coal, ash, and limestone slurry in flue gas desulfurization systems.
- Mining: Handles abrasive slurries, such as ore tailings and sand, in mineral processing pipelines.
- Metallurgy: Transports molten metal or slag in high-temperature environments.
- Chemical Processing: Manages corrosive liquids and gases, benefiting from the ceramic’s chemical inertness.
- Cement Industry: Conveys cement clinker and raw materials, resisting wear from abrasive particles.
Advantages
The adoption of ceramic lined elbows offers numerous benefits:
- Extended Service Life: Outlasts traditional steel elbows by a significant margin, reducing replacement frequency.
- Cost Efficiency: Lower maintenance and downtime costs offset the higher initial investment.
- Improved Flow: Smooth ceramic surfaces reduce friction and pressure loss, enhancing system efficiency.
- Versatility: Suitable for a wide range of temperatures, pressures, and media types.
- Easy Installation: Lightweight design and compatibility with standard flanges simplify integration.
Limitations
Despite their advantages, ceramic lined elbows have some drawbacks:
- Higher Initial Cost: The use of ceramics and specialized manufacturing processes increases upfront expenses compared to steel elbows.
- Brittleness: The ceramic lining can crack under extreme mechanical shock if not supported by the steel layer.
- Complex Repairs: Damaged ceramic linings are difficult to repair on-site, often requiring replacement.
Recent Advancements
Recent developments in ceramic lined elbow technology have focused on enhancing performance and reducing costs:
- Advanced Ceramics: The use of ZTA and silicon carbide (SiC) has improved toughness and wear resistance, expanding application ranges.
- Backpack Design: Adding a steel plate or ceramic “backpack” at the outer curve of the elbow increases wear resistance in high-impact zones.
- Self-Locking Tiles: Innovative tile designs with 360° mechanical interlocking enhance bonding strength and reduce delamination risks.
- Hybrid Linings: Combining ceramics with polymers or metals creates hybrid linings that balance cost, toughness, and wear resistance.
These advancements reflect ongoing efforts to optimize ceramic lined elbows for increasingly demanding industrial conditions, ensuring they remain a preferred solution for wear-intensive applications.
Conclusion
Ceramic lined elbows are a testament to the synergy between material science and engineering, offering unmatched wear resistance, corrosion resistance, and thermal stability. Their parameters—ranging from material composition to bending angles—can be tailored to meet specific operational needs, making them a versatile choice for industries worldwide. While their higher initial cost and brittleness pose challenges, the long-term benefits of reduced maintenance and extended service life far outweigh these drawbacks. As technology advances, ceramic lined elbows will continue to evolve, solidifying their role as a cornerstone of modern industrial piping systems.
You must be logged in to post a comment.