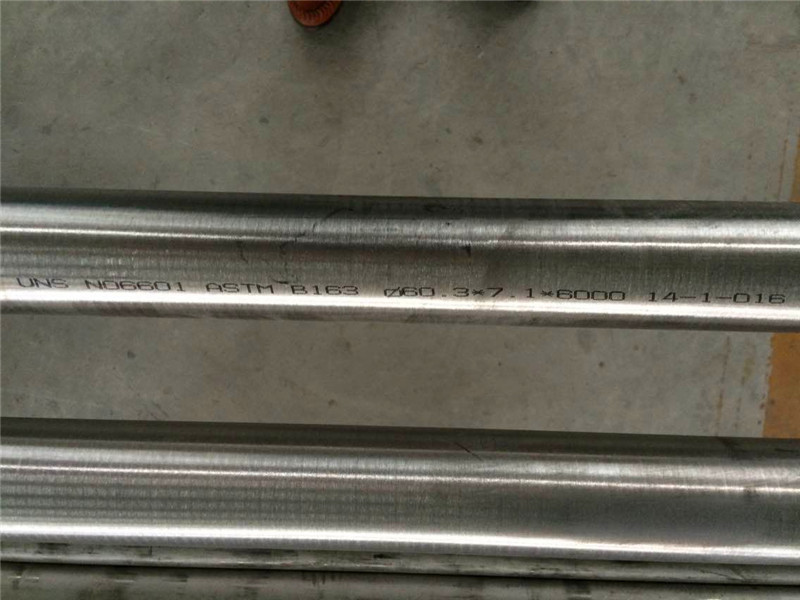
Comprehensive analysis of Inconel 601 (UNS N06601) seamless pipes under ASTM B163 standard
1. Core requirements of ASTM B163
ASTM B163 is a specification for nickel and nickel alloy seamless condenser and heat exchanger tubes, covering 26 alloys including UNS N06601 (Inconel 601). Its core requirements include:
- Dimensions and Tolerances :
- Outside diameter : ≤3 inches (76.2 mm), the allowable deviation is controlled according to the pipe diameter classification (for example, the outside diameter of 12.7-38.1 mm allows a deviation of ±0.19 mm).
- Wall thickness : minimum wall thickness ≤3.76 mm, average wall thickness ≤4.19 mm. Wall thickness tolerance is set by outer diameter (for example, 38.1-76.2 mm pipe diameter allows average wall thickness ±10%, minimum wall thickness +22%/-0%).
- Length : Standard length tolerance is ±3.2 mm, relaxed to ±6.4 mm over 30 feet (9.14 m).
- Chemical composition : It must meet the alloy composition limits in Table 1 of the standard. Taking UNS N06601 as an example, the Ni content is 58-63%, Cr 21-25%, Al 1.0-1.7%, and the impurity elements are strictly controlled (such as C≤0.10%, S≤0.015%).
- Mechanical properties :
- Tensile strength ≥586 MPa, yield strength ≥241 MPa, elongation ≥30% (at room temperature).
- Annealed hardness requirements (such as Rockwell hardness HRB ≤ 75).
- Manufacturing and testing :
- Seamless technology must be used, the surface must be uniform and free of defects, and strict straightness requirements must be met.
- Each pipe must pass a hydrostatic test or non-destructive electrical test (such as eddy current testing).
2. Material properties of Inconel 601 (UNS N06601)
- Chemical composition and metallurgical design :
- High nickel (58-63%) and chromium (21-25%) contents provide basic corrosion resistance, and the addition of aluminum (1.0-1.7%) significantly improves high-temperature oxidation resistance, especially forming a dense oxide film under cyclic thermal loads.
- Iron is used as a residual element to balance cost and performance, and the carbon content is ≤0.10% to reduce the risk of intergranular corrosion.
- Physical and high temperature properties :
- Density 8.11 g/cm³, melting point 1320-1411℃, thermal expansion coefficient 13.1 μm/m·℃ (25-1000℃), thermal conductivity 11.4 W/(m·K) (25℃).
- It maintains excellent oxidation resistance below 1204℃ and has better corrosion resistance than conventional stainless steel in sulfide environment.
- Mechanical properties :
- The tensile strength at room temperature is ≥650 MPa, and the creep rupture strength is still ≥100 MPa at high temperature (such as 800°C).
- The hardness is controllable in the solution annealing state (HB≤220), which is suitable for cold forming.
3. ASTM B163 manufacturing process requirements for UNS N06601 pipes
- Processing technology :
- Hot working : recommended deformation temperature is 870-1230℃, large deformation needs to be carried out at 1040-1230℃ to avoid cracking.
- Cold processing : The deformation needs to be controlled, and annealing treatment is used to eliminate residual stress (such as annealing temperature 1100-1150℃).
- Welding : It is recommended to use matching welding materials (such as ERNiCrFe-11) and adopt TIG or plasma welding to reduce embrittlement of the heat affected zone.
- Quality Control :
- Flattening tests (to verify ductility), expansion tests (to check the tendency of edge cracking) and non-destructive testing (such as ultrasonic testing) are required.
- The microstructure must meet the grain size requirements (usually ASTM grade 5 or finer), and the decarburization layer depth must be ≤0.1 mm.
4. Typical application scenarios
- High temperature heat exchange system :
- The radiation tubes and cracking furnace tubes of chemical reactors can withstand high-temperature corrosive media (such as nitric acid and hydrogen sulfide).
- The gas turbine exhaust duct can withstand the erosion of 900-1100℃ exhaust gas.
- Industrial furnace equipment :
- The trays and conveyor belts of heat treatment furnaces, as well as the muffles of annealing furnaces, need to maintain structural stability under long-term high temperatures.
- Combustion chamber linings in solid waste incinerators to resist ash erosion and thermal shock.
- Special environment :
- Heat exchange tubes in nuclear reactor high temperature gas cooling systems (e.g. helium coolant environments).
- The U-shaped tube bundle of the flue gas desulfurization device of the offshore platform is resistant to wet hydrogen sulfide corrosion.
5. Relationship with other standards
- ASME SB163 : The technical content is consistent with ASTM B163, but it adds the compliance requirements of the ASME Boiler and Pressure Vessel Code, which is suitable for strictly regulated fields such as nuclear power plants.
- International equivalent standards :
- Europe: EN 10305-4 (precision seamless tubes) and DIN 17458 (nickel alloy tubes) partially cover similar requirements.
- Japan: The chemical composition of JIS G4902 (nickel alloy seamless pipe) is close to that of ASTM B163, but the mechanical property requirements are slightly different.
6. Selection and design considerations
- Wall thickness optimization : When calculating the minimum wall thickness according to ASME BPVC Section VIII, the strength reduction factor of Inconel 601 at high temperatures must be considered (e.g. the allowable stress drops by about 40% at 800°C).
- U-bend restrictions : ASTM B163 stipulates that the U-bend radius R ≥ 2.5 times the pipe diameter, and the wall thickness reduction rate after bending must be verified by the formula (Tf = T × 2R / (2R + D)).
- Economic balance : The cost of Inconel 601 is significantly higher than that of 304 stainless steel (about 5-8 times), and the maintenance cost savings brought by its high corrosion resistance need to be evaluated through life cycle analysis (LCC).
Comprehensive Analysis of ASTM B163 Inconel 601 (UNS N06601) Seamless Tubing
1. Key Requirements of ASTM B163 Standard
ASTM B163 governs the specifications for seamless nickel and nickel-alloy condenser and heat-exchanger tubes, covering 26 alloys including UNS N06601 (Inconel 601). Core requirements include:
- Dimensions and Tolerances:
- Outside Diameter (OD): ≤3 inches (76.2 mm), with deviations controlled by diameter class (e.g., ±0.19 mm for 12.7–38.1 mm OD).
- Wall Thickness: Minimum ≤3.76 mm, average ≤4.19 mm. Tolerances vary by OD (e.g., ±10% average and +22%/-0% minimum for 38.1–76.2 mm OD).
- Length: Standard tolerance ±3.2 mm; extended to ±6.4 mm for tubes >30 ft (9.14 m).
- Chemical Composition: Must comply with Table 1 limits. For UNS N06601: Ni 58–63%, Cr 21–25%, Al 1.0–1.7%, with strict impurity controls (e.g., C ≤0.10%, S ≤0.015%).
- Mechanical Properties:
- Tensile Strength ≥586 MPa, Yield Strength ≥241 MPa, Elongation ≥30% (room temperature).
- Annealed hardness ≤75 HRB.
- Manufacturing and Testing:
- Mandatory seamless production with uniform surfaces and strict straightness.
- Hydrostatic or nondestructive electric testing (e.g., eddy current) required for every tube.
2. Material Characteristics of Inconel 601 (UNS N06601)
- Composition and Metallurgy:
- High Ni (58–63%) and Cr (21–25%) content ensures corrosion resistance. Al (1.0–1.7%) enhances cyclic oxidation resistance via dense oxide layer formation.
- Fe acts as a balance element; C ≤0.10% minimizes carbide precipitation.
- Physical and High-Temperature Properties:
- Density: 8.11 g/cm³; Melting range: 1320–1411°C; Thermal expansion: 13.1 μm/m·°C (25–1000°C); Thermal conductivity: 11.4 W/(m·K) (25°C).
- Superior oxidation resistance up to 1204°C; outperforms stainless steels in sulfidizing environments.
- Mechanical Performance:
- Room-temperature tensile strength ≥650 MPa; creep rupture strength ≥100 MPa at 800°C.
- Annealed hardness ≤220 HB for cold-forming compatibility.
3. ASTM B163 Manufacturing Requirements for UNS N06601 Tubing
- Processing Guidelines:
- Hot Working: Deformation at 870–1230°C; major reductions at 1040–1230°C to avoid cracking.
- Cold Working: Controlled deformation with stress-relief annealing (e.g., 1100–1150°C).
- Welding: Use matching filler (e.g., ERNiCrFe-11) with TIG/plasma methods to reduce HAZ embrittlement.
- Quality Control:
- Flattening tests (ductility verification), flaring tests (edge cracking resistance), and nondestructive testing (e.g., UT).
- Microstructure must meet grain size requirements (ASTM 5 or finer); decarburization ≤0.1 mm.
4. Typical Applications
- High-Temperature Heat Exchangers:
- Radiant tubes in chemical reactors and pyrolysis furnaces (resists HNO₃, H₂S).
- Gas turbine exhaust ducts (900–1100°C gas erosion).
- Industrial Furnace Components:
- Heat treatment furnace trays, annealing furnace muffles (long-term thermal stability).
- Combustion chamber liners in waste incinerators (resists ash erosion and thermal shock).
- Specialized Environments:
- High-temperature gas-cooled reactor systems (helium coolant).
- FGD U-tube bundles in offshore platforms (wet H₂S resistance).
5. Cross-Standard Compatibility
- ASME SB163: Technically identical to ASTM B163 but adds ASME BPVC compliance for nuclear applications.
- Global Equivalents:
- Europe: EN 10305-4 (precision tubes) and DIN 17458 partially overlap.
- Japan: JIS G4902 aligns chemically but differs in mechanical specs.
6. Design and Selection Considerations
- Wall Thickness Optimization: Account for elevated-temperature strength reduction (e.g., 40% allowable stress drop at 800°C per ASME BPVC VIII).
- U-Bend Limitations: Minimum bend radius ≥2.5× OD; post-bend thinning calculated via formula: Tf = T × 2R/(2R + D).
- Cost-Benefit Analysis: Inconel 601 costs 5–8× more than 304 stainless steel; justify via lifecycle cost (LCC) savings from reduced maintenance.
ASTM B163 Inconel 601 (UNS N06601) seamless tubing delivers unmatched high-temperature strength and corrosion resistance, making it indispensable in chemical processing, energy, and aerospace. From precise compositional control to rigorous performance validation, its production and application demand strict adherence to standards while requiring tailored engineering solutions for extreme operating conditions.
You must be logged in to post a comment.