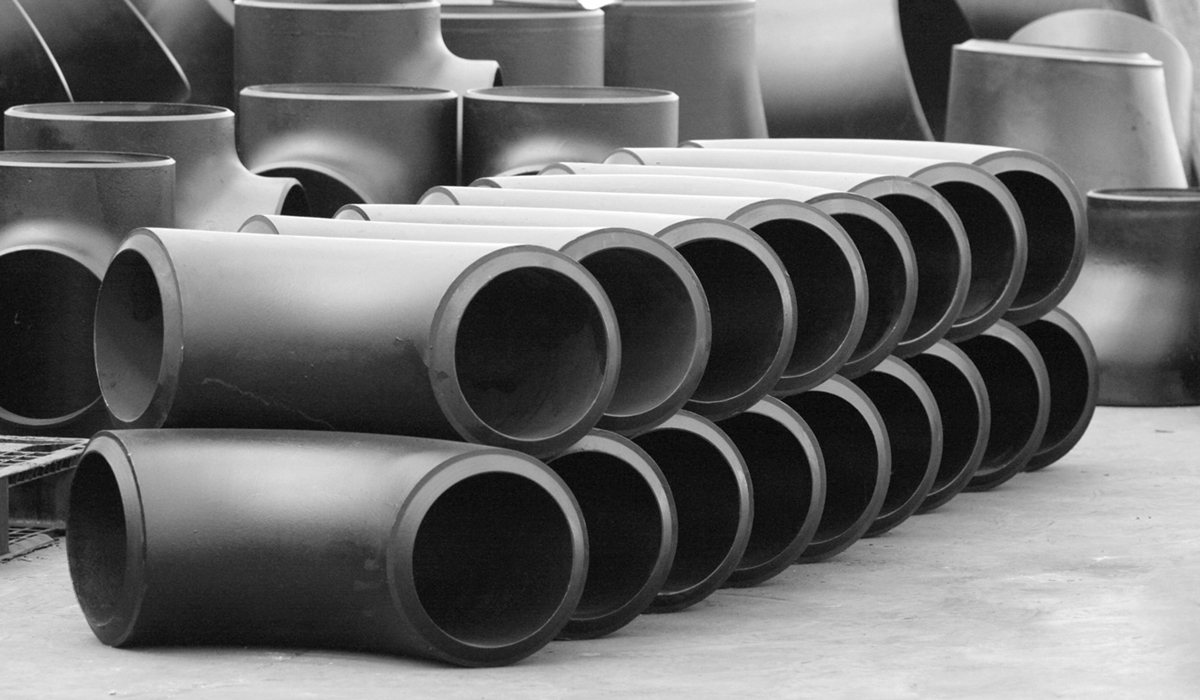
Even with all the advances in technology today, the wholly welded piping system has for decades remained the best choice for use in high pressure and high temperature application.
Many piping jobs in schools, industrial plants, refineries and factories have benefited from the inherent advantages of a completely welded system. It becomes a closed container joining pipes, valves, fittings, and flanges. A welded joint actually becomes part of the pipe, minimizing leak potential. This provides greater margins of safety, especially under conditions of high internal pressures. Additionally, welding fittings form a continuous metal structure with the pipe, adding forged-in strength to any piping system. Furthermore, smooth forged fittings simplify insulation and take up less space.
ASTM A 234
Scope
This standard covers wrought carbon steel fittings of seamless and welded construction which are manufactured to the dimensional specifications of ASME B16.9 and B16.28. These fittings are primarily for use in pressure piping and in pressure vessel fabrication for service at moderate and elevated temperatures.
Materials
The starting material for fittings shall consist of killed steel, forgings, bars, plates, seamless or fusion-welded tubular products with filler metal added and shall conform to the the chemical requirements of ASTM A 234. Unless otherwise specified, carbon steel plates may be either coarse grain or fine grain practice.
Manufacture
Forging or shaping operations are performed by hammering, pressing, piercing, extruding, upsetting, rolling, bending, machining, or by a combination of two or more of these operations. The forming process shall be applied so that it will not produce injurious imperfections in the fittings.
Heat Treatment
Hot-formed WPB fittings, upon which the final forming operation is completed at a temperature above 1150°F and below 1800°F, need not be heat treated. Cold-Formed WPB fittings, upon which the final forming operation is completed at a temperature below 1150°F, shall be normalized, or shall be stress relieved at 1100°F to 1275°F.
Chemical requirements (in %): |
|
Carbon Manganese Phosphorus (max) Sulfur (max) |
|
.30 max .29-1.06 .050 |
.058 |
Silicon Chromium Molybdenum Nickel |
Copper |
.10 min .40 max .15 max .40 max |
.40 max |
Vanadium Columbium |
|
.08 max .02 max |
|
Mechanical requirements: |
|
Tensile Strength 60,000-85,000 psi |
|
Yield Strength (min) 35,000 psi |
|
Elongation – Longitudinal: |
22% |
– Transverse: |
14% |
Dimensions
Butt-welding fittings and butt-welding short radius elbows and returns purchased in accordance with this specification shall conform to the dimensions and tolerances given in the latest revision of ANSI B16.9 and B16.28, respectively.
Certification
When requested by the purchaser, the manufacturer shall provide a certificate of compliance to this specification. If requested to provide test reports, the manufacturer shall also provide the following where applicable:
* Chemical analysis results. When the amount of an element is less than .02%, the analysis for that element is reported as “<0.02%.”
* Tensile property results, report the yield strength and ultimate strength in ksi [or MPa] and elongation in percent,
* Hardness acceptable in accordance with Section 10 of ASTM A-234,
* Seamless or Welded,
* Type of Heat Treatment, if any,
* Starting material, specifically pipe, plate, etc.,
* Statement regarding radiographic or ultrasonic examination.
* Any supplemental testing required by the purchase order.
Product Marking
All fittings shall have the prescribed information stamped or otherwise suitable marked on each fitting in accordance with ASTM A 234/MSS SP-25. A Weldbend fitting is marked as follows:
Weldbend’s Name, Nominal Pipe Size, Pipe Wall Thickness Designation, Material Grade (WPB/WPC) and Heat Identification Number.
Note: All information contained in this document, and for a complete description of all requirements, refer to ASTM A 105. Sheets are subject to change without notice.
You must be logged in to post a comment.