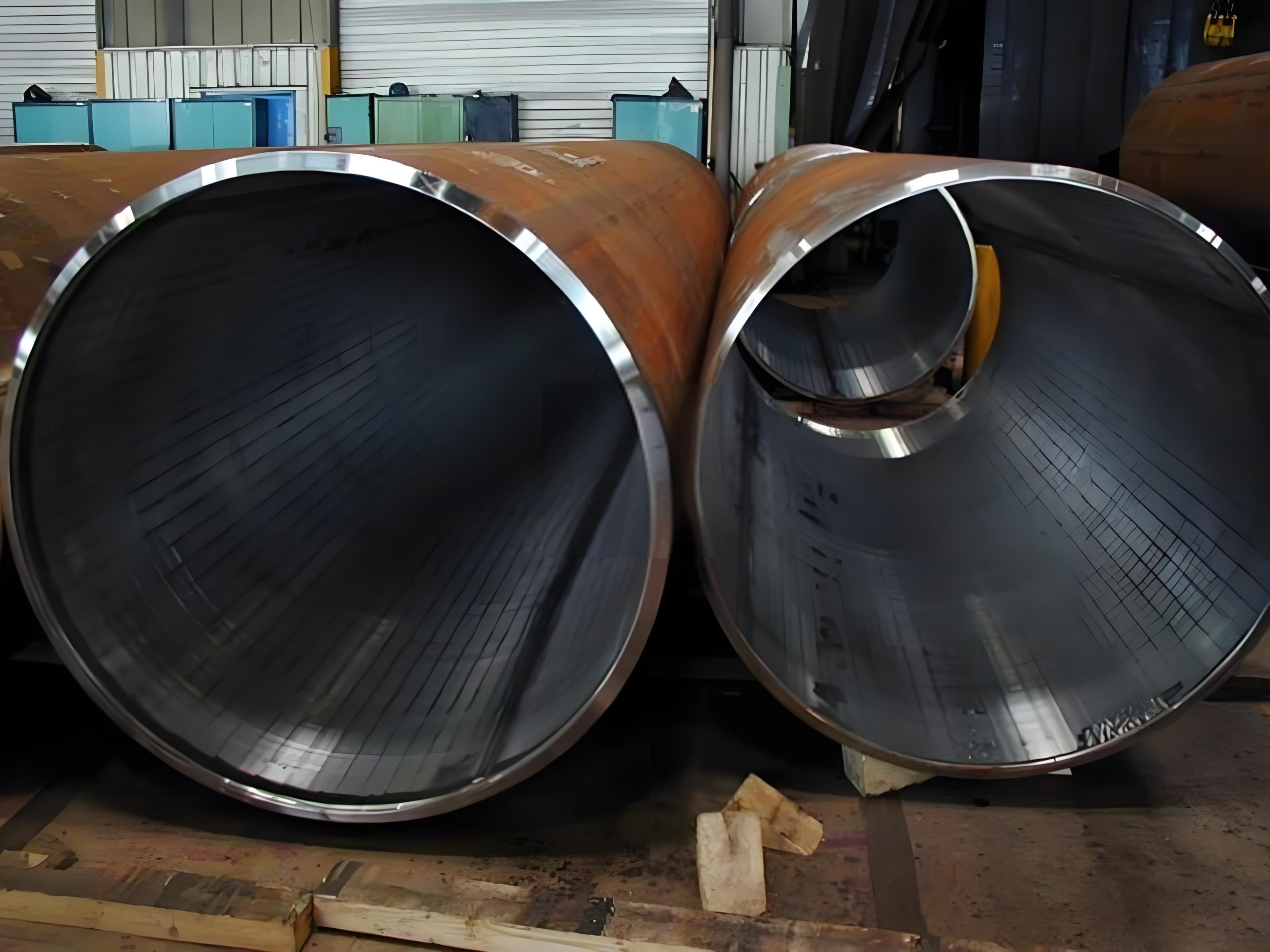
Cladded Pipes Specification
Cladded pipes, also known as clad pipes or CRA (Corrosion Resistant Alloy) cladded pipes, are composed of a carbon steel or alloy steel base pipe with an internal or external layer of corrosion-resistant alloy. These pipes combine the mechanical strength of the steel base with the corrosion resistance of the alloy, making them ideal for harsh environments in industries such as oil and gas, chemical processing, and power generation.
Key Specifications
-
Base Materials:
- API 5L Grade B, X42, X46, X52, X56, X60, X65, X70, X80
- ASTM A106 Gr.B, ASTM A333 Gr.6, ASTM A335 Cr-Mo alloys (P5, P11, P22, P9, P91)
-
Cladding Materials:
- Stainless Steels: SS 304/304L, SS 316/316L, SS 317/317L, Duplex 2205, Duplex 2506, Super Duplex 2507, Alloy 254 SMO, 904L
- Nickel Alloys: Incoloy 825, Inconel 625, Inconel 59, Alloy 31, AL6XN, Alloy 20, Monel 400
- Other Alloys: Hastelloy C-276, Titanium Grades 2, 5, 7, 9, 12, Zirconium R60702, various copper alloys
-
Manufacturing Standards:
- API 5LD
- ASTM A240, A263, A264, A265, B898, B424, B443, B619, B622, B675, B265, B551
-
Dimensions:
- Pipe Diameter Range: Ф50mm-Ф1800mm
- Liner Wall Thickness: 0.5mm-3.5mm
- Length: ≤15m
-
Surface Treatment:
- Digital underwater deflagration composite technology
- Hydraulic composite technology
- Pipe end surfacing and inner wall boring
-
Inspection and Testing:
- Ultrasonic Testing (UT)
- Radiographic Testing (RT)
- Hydrostatic Testing
- Mechanical Testing (tensile, hardness, impact)
- Corrosion Testing
Cladding Pipe Process
Cladding involves bonding a corrosion-resistant alloy (CRA) to a carbon steel or alloy steel base pipe. This process can be achieved through various methods, each with its own advantages and applications:
Cladding Methods
-
Hot Rolling:
- Involves rolling the CRA and base material together at high temperatures to achieve a metallurgical bond.
-
Coextrusion:
- Both materials are extruded together, ensuring a tight bond through simultaneous deformation.
-
Weld Overlay:
- CRA is welded onto the base material, creating a layer of corrosion-resistant metal.
-
Explosion Bonding:
- Uses controlled explosions to bond the CRA to the base material. This method is particularly useful for large or complex shapes.
-
Powder Metallurgy:
- CRA powder is applied to the base material and then sintered to create a bond.
-
Mechanical Bonding:
- Involves expanding or shrinking the CRA liner to fit tightly within the base pipe. This method is less strong than metallurgical bonding but is useful for certain applications.
Process Steps
-
Base Pipe Preparation:
- Cleaning and inspection of the base pipe to ensure it meets required standards.
-
Cladding Application:
- Applying the CRA layer using one of the methods mentioned above.
-
Heat Treatment:
- To relieve stresses and ensure a strong bond between the materials.
-
Machining and Finishing:
- Final shaping, surfacing, and inspection to meet dimensional and quality specifications.
-
Testing and Inspection:
- Comprehensive testing to ensure the integrity and performance of the cladded pipe.
What is Cladded Pipe?
A cladded pipe is a composite pipe that combines the mechanical strength of a carbon steel or alloy steel base pipe with the corrosion resistance of a CRA layer. The cladding process bonds the CRA to the base material, offering enhanced durability and resistance to corrosive environments. These pipes are crucial in industries where both mechanical strength and corrosion resistance are essential, such as oil and gas, petrochemical, and marine applications.
Size Range of Cladding Steel Pipes
Cladded steel pipes come in a variety of sizes to meet different industrial requirements:
- Pipe Diameter Range: Ф50mm-Ф1800mm
- Liner Wall Thickness: 0.5mm-3.5mm
- Length: Up to 15 meters
Size Range of Cladding Steel Pipes (Continued)
These dimensions ensure that cladded pipes can be tailored to specific applications, providing the necessary robustness and corrosion resistance required for their intended use. The flexibility in size range allows for customization to meet the specific needs of various industrial processes.
Clad Pipe Price List
The price of cladded pipes can vary significantly based on several factors, including the base material, the type of CRA used, the dimensions of the pipe, and the manufacturing process. Here is a general guide on how these factors influence the cost:
-
Base Material:
- Carbon Steel: Generally less expensive.
- Alloy Steels: Higher cost due to enhanced mechanical properties.
-
CRA Material:
- Stainless Steels (e.g., 304/304L, 316/316L): Moderate cost.
- Nickel Alloys (e.g., Inconel 625, Hastelloy C-276): Higher cost due to superior corrosion resistance.
- Specialty Alloys (e.g., Titanium, Zirconium): Highest cost due to unique properties.
-
Pipe Dimensions:
- Larger diameters and thicker walls increase the material cost.
- Longer pipes require more extensive manufacturing processes.
-
Manufacturing Process:
- Simple mechanical bonding methods are less expensive.
- Advanced processes like explosion bonding or weld overlay are more costly.
For specific pricing, it is recommended to contact manufacturers or suppliers who can provide detailed quotes based on the exact specifications required.
Pipe Cladding Surface Treatment
Surface treatment of cladded pipes is crucial to ensure the longevity and performance of the pipe in service. The surface treatment process includes:
-
Cleaning:
- Removal of any contaminants, rust, or scale from the surface to ensure a clean bonding surface.
-
Surface Roughening:
- Techniques like grit blasting or sandblasting are used to roughen the surface, improving the adhesion of the CRA layer.
-
Application of CRA:
- The CRA layer is applied using methods like weld overlay, hot rolling, or explosion bonding.
-
Post-Cladding Treatment:
- Heat treatment to relieve stresses and enhance the bond between the CRA and base material.
- Final machining and polishing to achieve the desired surface finish.
-
Inspection and Testing:
- Non-destructive testing (NDT) methods such as ultrasonic testing (UT) and radiographic testing (RT) are used to check for defects.
- Visual inspections to ensure surface quality.
CRA Cladded Pipe Material
CRA cladded pipes use a variety of corrosion-resistant materials, each selected based on the specific requirements of the application:
-
Stainless Steels:
- SS 304/304L, SS 316/316L, SS 317/317L
- Duplex 2205, Duplex 2506, Super Duplex 2507
- Alloy 254 SMO, 904L
-
Nickel Alloys:
- Incoloy 825, Inconel 625, Inconel 59
- Alloy 31, AL6XN, Alloy 20
- Monel 400
-
Other Alloys:
- Hastelloy C-276
- Titanium Grades 2, 5, 7, 9, 12
- Zirconium R60702
- Various copper alloys
The choice of CRA material depends on factors such as the type of corrosion (e.g., pitting, crevice, stress corrosion cracking), operating temperature, and chemical environment.
Types of Cladded Pipes
Cladded pipes can be categorized based on the cladding method and the type of CRA used:
Based on Cladding Method
-
Weld Overlay Clad Pipes:
- CRA is welded onto the base pipe, suitable for high-pressure applications.
-
Explosion Bonded Clad Pipes:
- Uses explosive force to bond the CRA to the base pipe, ideal for complex shapes and large diameters.
-
Hot Rolled Clad Pipes:
- CRA and base material are rolled together at high temperatures, ensuring a strong metallurgical bond.
-
Mechanically Bonded Lined Pipes:
- CRA liner is mechanically fitted inside the base pipe, less expensive but with lower bond strength.
Based on CRA Material
-
Stainless Steel Clad Pipes:
- Commonly used for their excellent corrosion resistance and mechanical properties.
-
Nickel Alloy Clad Pipes:
- Highly resistant to corrosion in aggressive environments, such as high-temperature and high-pressure conditions.
-
Titanium Clad Pipes:
- Extremely resistant to corrosion from seawater and chemicals.
-
Zirconium Clad Pipes:
- Used in applications involving strong acids due to their exceptional corrosion resistance.
Cladding Steel Pipes Tests and Inspection (Continued)
To ensure the quality and integrity of cladded pipes, a comprehensive range of tests and inspections are conducted during and after the manufacturing process. These tests are designed to verify the mechanical properties, corrosion resistance, and overall reliability of the pipes.
Non-Destructive Testing (NDT)
-
Ultrasonic Testing (UT):
- Used to detect internal defects and measure the thickness of the cladding layer.
- Ensures there are no discontinuities or voids in the bond between the cladding and base material.
-
Radiographic Testing (RT):
- Utilizes X-rays or gamma rays to identify internal flaws such as cracks or inclusions.
- Provides a detailed image of the internal structure of the pipe.
-
Magnetic Particle Inspection (MPI):
- Suitable for detecting surface and near-surface defects in ferromagnetic materials.
- The pipe is magnetized, and ferrous particles are applied to reveal defects.
-
Dye Penetrant Inspection (DPI):
- A liquid dye is applied to the surface, which penetrates any surface-breaking defects.
- Excess dye is removed, and a developer is applied to draw out the dye from defects for visual inspection.
Mechanical Testing
-
Tensile Testing:
- Measures the tensile strength, yield strength, and elongation of the cladded pipe.
- Ensures the pipe meets mechanical property requirements.
-
Hardness Testing:
- Determines the hardness of both the cladding and base materials.
- Common methods include Rockwell, Brinell, and Vickers hardness tests.
-
Impact Testing:
- Evaluates the toughness of the material by measuring its ability to absorb energy during fracture.
- Typically conducted at various temperatures to simulate service conditions.
Corrosion Testing
-
Salt Spray Test:
- Exposes the cladded pipe to a salt spray environment to evaluate its resistance to corrosion.
- Commonly used for stainless steel and other corrosion-resistant alloys.
-
Pitting and Crevice Corrosion Tests:
- Assesses the susceptibility of the cladded material to localized corrosion phenomena.
- Involves exposing the material to specific environments that promote pitting or crevice corrosion.
-
Intergranular Corrosion Test:
- Determines the resistance of the cladded material to corrosion along grain boundaries.
- Important for materials that may be exposed to high temperatures or corrosive chemicals.
Dimensional and Visual Inspections
-
Dimensional Inspection:
- Ensures the cladded pipe meets specified dimensional tolerances, including diameter, wall thickness, and length.
- Uses tools such as calipers, micrometers, and coordinate measuring machines (CMMs).
-
Visual Inspection:
- Conducted to identify surface defects, weld quality, and overall appearance.
- Typically performed by trained inspectors using visual aids and magnification tools.
Pipe Cladding and Insulation Tolerance
Cladding and insulation tolerances are critical to ensure the cladded pipes perform as expected in their intended applications. Tolerances are specified for various dimensions and properties to maintain consistency and quality.
Key Tolerances
-
Cladding Thickness Tolerance:
- The thickness of the cladding layer must be uniform and within specified limits.
- Typical tolerance ranges from ±0.1 to ±0.5 mm, depending on the application and cladding method.
-
Pipe Diameter Tolerance:
- Ensures the outer diameter of the cladded pipe meets specified requirements.
- Common tolerance is ±1% of the nominal diameter.
-
Wall Thickness Tolerance:
- The total wall thickness (base material plus cladding) must be within defined limits.
- Standard tolerance is ±10% of the nominal wall thickness.
-
Length Tolerance:
- The overall length of the cladded pipe must match specified dimensions.
- Typical tolerance is ±50 mm for lengths up to 12 meters.
-
Ovality Tolerance:
- Measures the deviation from a perfect circular cross-section.
- Ovality tolerance is usually within 1-2% of the nominal diameter.
-
Straightness Tolerance:
- Ensures the pipe is straight and free from excessive bending.
- Acceptable deviation is generally within 3-5 mm per meter of length.
Advantages of Cladded Pipe (Continued)
-
Cost-Effectiveness:
- Compared to using solid CRA pipes, cladded pipes are more economical as they use less expensive base materials while still providing the necessary corrosion resistance.
-
Extended Service Life:
- The combination of a durable base pipe and a corrosion-resistant cladding layer significantly extends the service life of the pipes in harsh environments.
-
Versatility:
- Cladded pipes can be customized to meet specific requirements, including different cladding materials and thicknesses, making them suitable for a wide range of applications.
-
Reduced Maintenance:
- The superior corrosion resistance of the cladding layer reduces the need for frequent maintenance and repairs, leading to lower operational costs over time.
-
High-Temperature Performance:
- Many CRA materials used in cladding can withstand high temperatures, making cladded pipes suitable for high-temperature applications.
-
Improved Safety:
- The high strength and corrosion resistance of cladded pipes enhance the safety and reliability of pipelines, reducing the risk of leaks and failures.
Common Differences between Clad and Lined Pipe
While both clad and lined pipes are designed to provide corrosion resistance, they differ in their construction, performance, and applications.
Clad Pipe
-
Construction:
- Consists of a carbon steel or alloy steel base pipe with a CRA layer metallurgically bonded to it.
- The cladding process ensures a strong bond between the materials.
-
Performance:
- Offers superior mechanical strength and corrosion resistance.
- Suitable for high-pressure and high-temperature applications.
-
Applications:
- Used in harsh environments such as oil and gas, petrochemical, and chemical processing industries.
- Ideal for applications where both mechanical strength and corrosion resistance are critical.
-
Cost:
- Generally more expensive than lined pipes due to the complex manufacturing process.
Lined Pipe
-
Construction:
- Consists of a carbon steel or alloy steel base pipe with a CRA liner mechanically fitted inside.
- The liner is not metallurgically bonded to the base pipe.
-
Performance:
- Provides good corrosion resistance but lower mechanical strength compared to clad pipes.
- Suitable for lower pressure and temperature applications.
-
Applications:
- Commonly used in water treatment, sewage, and low-pressure chemical transport.
- Ideal for applications where corrosion resistance is needed, but mechanical strength is less critical.
-
Cost:
- Typically less expensive than clad pipes due to the simpler manufacturing process.
Max Temperature of CRA Clad Pipes
The maximum temperature that CRA cladded pipes can withstand depends on the specific CRA material used in the cladding. Here are some examples:
-
Stainless Steel (e.g., 316L):
- Maximum temperature: Approximately 600°C (1112°F)
-
Duplex Stainless Steel (e.g., 2205):
- Maximum temperature: Approximately 300°C (572°F)
-
Inconel 625:
- Maximum temperature: Approximately 980°C (1796°F)
-
Hastelloy C-276:
- Maximum temperature: Approximately 650°C (1202°F)
-
Titanium (e.g., Grade 2):
- Maximum temperature: Approximately 350°C (662°F)
The specific maximum temperature for a given application should be verified with the manufacturer, considering factors such as operating conditions, pressure, and chemical environment.
Cladding Around Pipe Hardfacing Layer Chart
Hardfacing is a surface coating process used to enhance the wear resistance of cladded pipes. The hardfacing layer is typically applied to areas subject to severe wear and abrasion. Here is an example chart displaying various hardfacing materials and their typical applications:
Hardfacing Material | Composition | Application |
---|---|---|
Stellite 6 | Co-Cr-W alloy | High wear and abrasion resistance |
Tungsten Carbide | WC-Co | Extreme wear and impact resistance |
Chromium Carbide | Cr3C2-NiCr | High-temperature wear resistance |
Nickel-Based Alloys | Ni-Cr-B-Si alloys | Corrosion and wear resistance |
Cobalt-Based Alloys | Co-Cr-W-C alloys | High wear and thermal shock resistance |
Hardfacing layers are applied using methods such as:
-
Welding:
- Techniques like plasma-transferred arc (PTA) welding or MIG welding.
-
Thermal Spraying:
- Methods like high-velocity oxy-fuel (HVOF) spraying or plasma spraying.
Inconel Cladded Pipe Flatness Tolerances
Flatness tolerances for Inconel cladded pipes ensure that the pipes meet the geometric requirements necessary for their proper function and fit within a system. These tolerances are critical for maintaining the integrity and performance of the pipeline, especially in high-pressure and high-temperature applications where Inconel is commonly used.
Typical Flatness Tolerances
-
Straightness Tolerance:
- The deviation from a straight line, measured over the length of the pipe.
- Common tolerance: ±1 mm per meter of pipe length, with a maximum deviation often specified based on the total length.
-
Ovality Tolerance:
- The measure of how much the pipe’s cross section deviates from a perfect circle.
- Common tolerance: ±1% of the nominal diameter.
-
Surface Flatness:
- Ensures the cladded layer is uniformly flat, which is essential for proper sealing and connection in flanged joints.
- Specific tolerances depend on the application and standards but generally fall within a few millimeters over the length of the pipe.
Industry Standards
Flatness tolerances for Inconel cladded pipes are often governed by industry standards such as:
- ASME B31.3: Process Piping
- API 5LD: Specification for CRA Clad or Lined Steel Pipe
- ASTM B775: Standard Specification for Nickel and Nickel Alloy Welded Pipe
These standards provide detailed guidelines on acceptable flatness tolerances and testing methods to ensure compliance.
Clad Material Specification
When specifying clad materials for pipes, several key parameters must be considered to ensure the desired performance and durability. The specification typically includes the following details:
Base Material
-
Material Type:
- Carbon steel, alloy steel, or other suitable base materials.
-
Grade:
- Specific grade of the base material, such as ASTM A106 Grade B or API 5L X65.
-
Mechanical Properties:
- Yield strength, tensile strength, elongation, and hardness.
Cladding Material
-
Material Type:
- Specific CRA such as Inconel 625, Hastelloy C-276, or Stainless Steel 316L.
-
Thickness:
- Required thickness of the cladding layer, typically specified in millimeters or inches.
-
Bonding Method:
- The process used for bonding the cladding to the base material, such as weld overlay, explosion bonding, or hot rolling.
Additional Specifications
-
Heat Treatment:
- Any required post-cladding heat treatments to relieve stresses and enhance material properties.
-
Testing Requirements:
- Specific non-destructive testing (NDT) methods, such as ultrasonic testing (UT) or radiographic testing (RT).
- Mechanical testing requirements, such as tensile tests, hardness tests, and impact tests.
-
Certification:
- Compliance with relevant industry standards and certifications, such as ASME, API, or ASTM specifications.
Clad Pipe Chemical Composition
The chemical composition of both the base material and the cladding material is crucial for determining the overall performance of the cladded pipe. Here are typical compositions for some common materials used in cladded pipes:
Carbon Steel Base Material (e.g., ASTM A106 Grade B)
Element | Composition (wt%) |
---|---|
Carbon (C) | 0.25 max |
Manganese (Mn) | 0.27–0.93 |
Phosphorus (P) | 0.035 max |
Sulfur (S) | 0.035 max |
Silicon (Si) | 0.10–0.35 |
Inconel 625 Cladding Material
Element | Composition (wt%) |
---|---|
Nickel (Ni) | 58.0 min |
Chromium (Cr) | 20.0–23.0 |
Molybdenum (Mo) | 8.0–10.0 |
Niobium (Nb) | 3.15–4.15 |
Iron (Fe) | 5.0 max |
Manganese (Mn) | 0.50 max |
Silicon (Si) | 0.50 max |
Carbon (C) | 0.10 max |
Stainless Steel 316L Cladding Material (Continued)
Element | Composition (wt%) |
---|---|
Molybdenum (Mo) | 2.0–3.0 |
Iron (Fe) | Balance |
Manganese (Mn) | 2.0 max |
Silicon (Si) | 1.0 max |
Phosphorus (P) | 0.045 max |
Sulfur (S) | 0.030 max |
Carbon (C) | 0.030 max |
Hastelloy C-276 Cladding Material
Element | Composition (wt%) |
---|---|
Nickel (Ni) | Balance |
Molybdenum (Mo) | 15.0–17.0 |
Chromium (Cr) | 14.5–16.5 |
Iron (Fe) | 4.0–7.0 |
Tungsten (W) | 3.0–4.5 |
Cobalt (Co) | 2.5 max |
Manganese (Mn) | 1.0 max |
Silicon (Si) | 0.08 max |
Carbon (C) | 0.01 max |
Vanadium (V) | 0.35 max |
Phosphorus (P) | 0.04 max |
Sulfur (S) | 0.03 max |
Duplex Stainless Steel (e.g., 2205)
Element | Composition (wt%) |
---|---|
Chromium (Cr) | 22.0–23.0 |
Nickel (Ni) | 4.5–6.5 |
Molybdenum (Mo) | 3.0–3.5 |
Iron (Fe) | Balance |
Manganese (Mn) | 2.0 max |
Silicon (Si) | 1.0 max |
Phosphorus (P) | 0.03 max |
Sulfur (S) | 0.02 max |
Carbon (C) | 0.03 max |
Nitrogen (N) | 0.14–0.20 |
Summary
Cladded pipes combine the mechanical strength of a carbon or alloy steel base with the superior corrosion resistance of a cladding layer, such as Inconel, Hastelloy, or stainless steel. The manufacturing process, testing, and inspection ensure high reliability and performance in demanding environments. By adhering to strict tolerances and specifications, cladded pipes effectively meet the rigorous requirements of industries like oil and gas, petrochemical, and chemical processing. Understanding the chemical composition and mechanical properties of both the base and cladding materials is essential for selecting the appropriate cladded pipe for specific applications.
API 5LD clad or lined steel pipes including longitudinal seam clad steel pipe, helical seam clad steel pipe and seamless lined steel pipes in according with API SPEC 5LD, DNV-OS-F101, SY/T6623 AND CJ/T192.Clad material combines the corrosive and resistance properties of CRA with the high strength of carbon manganese steels. The result of this combination of CRA material in thinner wall thickness with the strength of heavy wall thickness carbon steel material is a cost efficiency.
Backing pipe OD: NPS 6″ ~ NPS28″
Cladding Material: LC1812, 2205, UNS S317030, S31803, S30400, S30403, S31600, S31603, S32100, N08904, N08825, N06600, N04400
You must be logged in to post a comment.