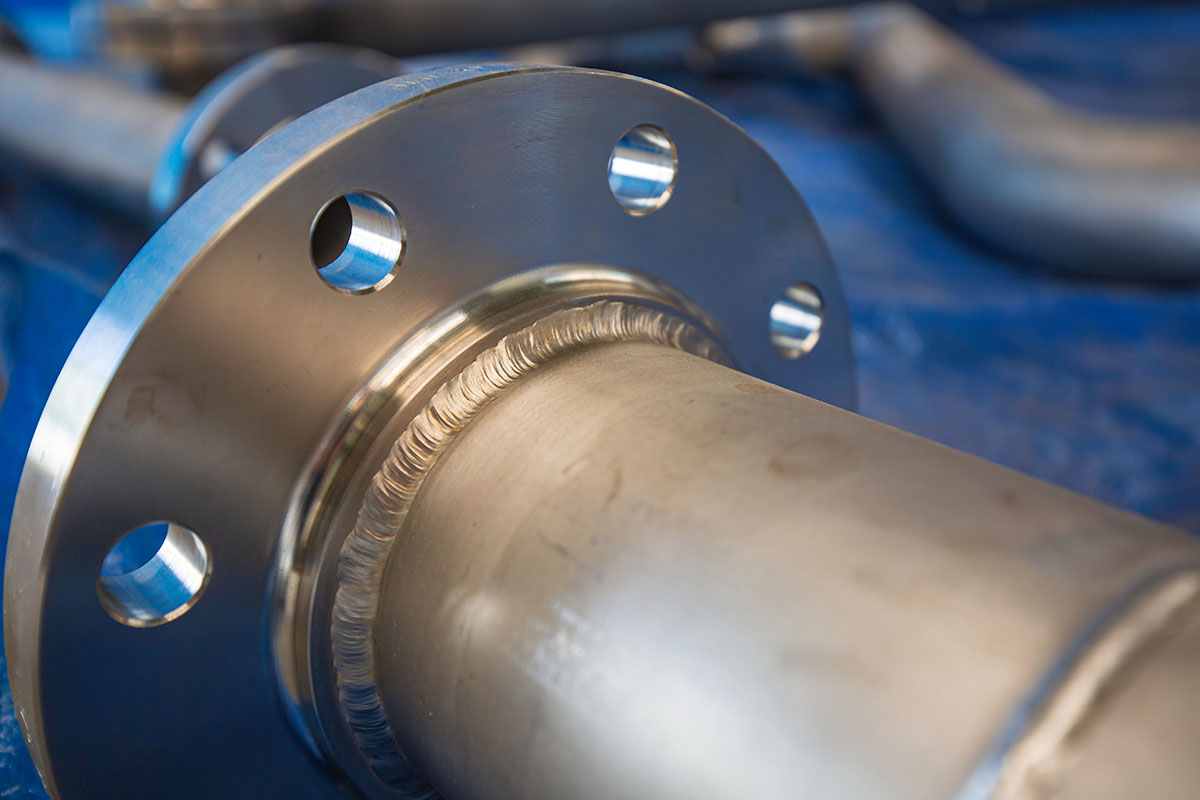
Comprehensive Outline for: “Acceptance Criteria for Super Alloy Steel Pipe Welds”
Below is a detailed and structured outline to create a long-form article covering the topic thoroughly:
Main Heading | Subheading |
---|---|
1. Introduction | – Overview of Super Alloy Steel Pipes – Importance of Weld Quality in Critical Applications |
2. Understanding Super Alloys | – What are Super Alloys? – Properties of Super Alloys – Common Uses of Super Alloy Steel Pipes |
3. Importance of Weld Acceptance Criteria | – Role of Welds in Super Alloy Applications – Safety, Durability, and Compliance – Industry Standards for Weld Acceptance |
4. Welding Process for Super Alloy Steel Pipes | – Common Welding Techniques – Challenges in Welding Super Alloys – Preventing Weld Defects |
5. Key Weld Acceptance Criteria | – Visual Inspection Requirements – Dimensional Tolerance – Weld Surface Quality Standards |
6. Non-Destructive Testing (NDT) for Super Alloy Welds | – Overview of NDT Methods – Radiographic Testing – Ultrasonic Testing – Magnetic Particle Testing – Dye Penetrant Testing |
7. Mechanical Testing for Welds | – Tensile Testing – Bend Testing – Hardness Testing – Impact Testing for Toughness Evaluation |
8. Microstructure and Metallurgical Analysis | – Grain Structure Evaluation – Detecting Heat-Affected Zone (HAZ) Issues – Corrosion Resistance Testing |
9. Common Weld Defects in Super Alloys | – Porosity – Cracks (Hot and Cold) – Lack of Fusion – Undercut and Overlap – Inclusion Defects |
10. Criteria for Allowable Defects | – Limits for Porosity – Crack-Free Welds – Allowable Undercuts and Overlaps – Standards for Internal Inclusions |
11. Standards and Codes for Weld Acceptance | – ASME Boiler and Pressure Vessel Code (BPVC) – AWS D1.1 Standards – ISO 5817 and Other International Standards |
12. Documentation and Record Keeping | – Inspection Reports – Weld Maps – Test Certificates and Records |
13. Role of Experienced Welders and Inspectors | – Importance of Certified Welders – Role of Qualified Inspectors – Continuous Training and Certifications |
14. Case Studies: Success and Failures in Super Alloy Welds | – Examples of Successful Welds – Analysis of Failure Cases and Lessons Learned |
15. Conclusion and Recommendations | – Summary of Key Points – Best Practices for Super Alloy Steel Pipe Welds – Importance of Adhering to Standards |
Long-Form Article: Acceptance Criteria for Super Alloy Steel Pipe Welds
1. Introduction
Super alloy steel pipes are used in industries that demand exceptional strength, heat resistance, and corrosion resistance. From power plants to aerospace, these materials play a critical role in ensuring safety and performance. However, the quality of welds in these pipes determines their overall reliability. This article delves into the acceptance criteria for super alloy steel pipe welds, ensuring compliance with industry standards.
2. Understanding Super Alloys
What are Super Alloys?
Super alloys, also known as high-performance alloys, are materials designed to withstand extreme conditions. They exhibit exceptional mechanical strength, thermal stability, and resistance to oxidation and corrosion.
Properties of Super Alloys
- High tensile strength at elevated temperatures.
- Resistance to creep and deformation.
- Excellent weldability (with proper techniques).
- Corrosion resistance in harsh environments.
Common Uses of Super Alloy Steel Pipes
- Nuclear reactors
- Aerospace and jet engines
- Petrochemical plants
- Heat exchangers in power plants
3. Importance of Weld Acceptance Criteria
Role of Welds in Super Alloy Applications
Welds act as the backbone of super alloy pipe systems. Proper weld quality ensures operational safety, especially in high-stress or high-temperature environments.
Safety, Durability, and Compliance
Poor-quality welds can lead to catastrophic failures, resulting in downtime, costly repairs, and even loss of life in severe cases. Adhering to weld acceptance criteria ensures safety and prolongs equipment life.
Industry Standards for Weld Acceptance
Standards such as ASME, AWS, and ISO provide a framework for assessing weld quality in super alloy steel pipes. These standards ensure uniformity and reliability in critical applications.
4. Welding Process for Super Alloy Steel Pipes
Common Welding Techniques
- Tungsten Inert Gas (TIG) Welding
- Metal Inert Gas (MIG) Welding
- Laser Beam Welding
- Electron Beam Welding
Challenges in Welding Super Alloys
- High thermal expansion leading to distortion.
- Sensitivity to oxidation at high temperatures.
- Potential for cracking in the heat-affected zone (HAZ).
Preventing Weld Defects
- Use of preheating and post-weld heat treatment.
- Controlling weld parameters such as current, voltage, and travel speed.
- Employing skilled welders with experience in super alloys.
5. Key Weld Acceptance Criteria
Visual Inspection Requirements
- No visible cracks or surface porosity.
- Uniform weld bead with smooth transitions.
- Absence of spatter or contamination.
Dimensional Tolerance
- Weld width, height, and alignment must meet design specifications.
Weld Surface Quality Standards
- Smooth and free from irregularities.
- Proper penetration without undercuts or overlaps.
6. Non-Destructive Testing (NDT) for Super Alloy Welds
Overview of NDT Methods
NDT techniques assess weld quality without damaging the material.
Radiographic Testing
- Uses X-rays or gamma rays to detect internal flaws.
Ultrasonic Testing
- Employs high-frequency sound waves to identify subsurface defects.
Magnetic Particle Testing
- Detects surface and near-surface defects in ferromagnetic materials.
Dye Penetrant Testing
- Highlights surface cracks and imperfections using a dye solution.
7. Mechanical Testing for Welds
Tensile Testing
Measures the weld’s ability to withstand tension.
Bend Testing
Evaluates the ductility and soundness of welds.
Hardness Testing
Assesses the material’s resistance to deformation.
Impact Testing
Determines the weld’s toughness under sudden force or extreme temperatures.
8. Microstructure and Metallurgical Analysis
Grain Structure Evaluation
Ensures proper grain refinement in the weld and HAZ.
Detecting Heat-Affected Zone (HAZ) Issues
Examines changes in material properties due to welding heat.
Corrosion Resistance Testing
Confirms that the weld maintains its resistance to corrosive environments.
9. Common Weld Defects in Super Alloys
Porosity
Caused by trapped gases, resulting in weak welds.
Cracks (Hot and Cold)
Hot cracks occur during solidification, while cold cracks form post-welding.
Lack of Fusion
Occurs when the weld metal does not fuse with the base material.
Undercut and Overlap
Reduces weld strength and compromises integrity.
Inclusion Defects
Results from foreign materials trapped in the weld.
10. Criteria for Allowable Defects
Limits for Porosity
- Defined by standards based on size and frequency.
Crack-Free Welds
- No cracks are permissible for super alloy welds.
Allowable Undercuts and Overlaps
- Minimal deviations allowed as per industry guidelines.
Standards for Internal Inclusions
- Small, isolated inclusions may be acceptable depending on application.
11. Standards and Codes for Weld Acceptance
ASME Boiler and Pressure Vessel Code (BPVC)
Covers pressure-containing components and weld quality.
AWS D1.1 Standards
Focuses on structural welding.
ISO 5817
International standard for the quality levels of fusion-welded joints.
12. Documentation and Record Keeping
Inspection Reports
Detail findings from visual and NDT inspections.
Weld Maps
Track weld locations and associated tests.
Test Certificates and Records
Provide proof of compliance with specifications.
13. Role of Experienced Welders and Inspectors
Importance of Certified Welders
Skilled professionals minimize the risk of defects.
Role of Qualified Inspectors
Ensure compliance with standards through thorough inspections.
Continuous Training and Certifications
Regular training updates welders and inspectors on the latest techniques and standards.
14. Case Studies: Success and Failures in Super Alloy Welds
Examples of Successful Welds
- Successful applications in aerospace and nuclear industries.
Analysis of Failure Cases and Lessons Learned
- Failures caused by inadequate inspection and poor weld techniques.
15. Conclusion and Recommendations
Summary of Key Points
- Weld acceptance criteria ensure the safety and durability of super alloy steel pipe systems.
Best Practices for Super Alloy Steel Pipe Welds
- Use certified welders, follow standards, and conduct thorough inspections.
Importance of Adhering to Standards
Strict compliance ensures reliable and long-lasting performance.
Frequently Asked Questions (FAQs)
-
What are super alloys used for? Super alloys are used in high-temperature and high-stress environments like jet engines, power plants, and chemical refineries.
-
What is the most common weld defect in super alloys? Porosity and cracking are common defects due to the high-temperature nature of welding super alloys.
-
Why is NDT important for welds? NDT ensures the weld’s internal and external quality without damaging the material.
-
What standards govern weld acceptance? Standards like ASME BPVC, AWS D1.1, and ISO 5817 are commonly used.
-
How can weld defects be minimized? By using proper techniques, skilled welders, and thorough inspections.
-
What happens if a weld fails inspection? Repairs or re-welding may be required, followed by re-inspection to meet acceptance criteria.
16. Advanced Techniques for Ensuring Weld Quality
Pre-Weld Preparation
Before welding, it’s essential to prepare the surface and material to ensure defect-free results. This includes:
- Cleaning the surface to remove dirt, oil, and contaminants.
- Preheating super alloy steel pipes to prevent thermal shock and cracking.
- Aligning the pipe joints properly to avoid misalignment or strain during welding.
Post-Weld Heat Treatment (PWHT)
PWHT is crucial for super alloys to:
- Relieve residual stresses.
- Enhance metallurgical properties.
- Prevent long-term cracking or deformation in high-temperature environments.
Welding Automation for Super Alloys
Automated systems such as robotic welding or laser-guided setups are increasingly used for super alloys. These systems offer:
- High precision and repeatability.
- Reduction in human error.
- Consistent weld quality, especially in large-scale applications.
17. Welding Super Alloys in Extreme Environments
High-Temperature Welding
When welding in extreme heat, super alloys require careful control of parameters like:
- Welding current and voltage.
- Cooling rates to avoid distortion.
- Shielding gas composition to prevent oxidation.
Subsea Welding
Super alloy pipes are commonly used in subsea applications like oil and gas pipelines. Special considerations include:
- Use of hyperbaric welding chambers.
- Ensuring weld integrity under immense pressure.
- Testing for resistance to saltwater corrosion.
Space and Aerospace Applications
Super alloys are vital in aerospace systems due to their strength and heat resistance. Welding for these applications requires:
- Vacuum or inert gas shielding to prevent contamination.
- Extreme precision to avoid defects that could compromise safety.
18. Emerging Trends in Super Alloy Welding
Laser Welding
Laser welding offers a focused, high-energy beam for precision welding in super alloys. Benefits include:
- Minimal heat-affected zone (HAZ).
- High-speed welding with consistent results.
- Reduced risk of cracking or distortion.
Additive Manufacturing (3D Printing)
Super alloy welding is being integrated with 3D printing techniques for applications like:
- Repairing super alloy components with welding-based additive manufacturing.
- Building complex shapes layer by layer using super alloys.
Artificial Intelligence (AI) and Machine Learning in Weld Quality Monitoring
AI-powered systems are being developed to monitor and evaluate weld quality in real time. These systems:
- Use sensors and cameras to detect defects.
- Automatically adjust welding parameters for optimal results.
19. Environmental Considerations in Super Alloy Welding
Reducing Environmental Impact
The welding process for super alloys can have significant energy requirements and waste generation. To mitigate this:
- Use energy-efficient welding systems.
- Recycle metal scraps and consumables.
- Minimize emissions from welding gases.
Safety and Health Concerns
Welding super alloys can release harmful fumes and particulates. To ensure worker safety:
- Provide proper ventilation and fume extraction.
- Equip welders with high-quality respiratory protection.
- Use low-emission consumables when possible.
20. Tools and Equipment for Super Alloy Steel Pipe Welding
Welding Machines
- TIG welders for precise control and clean welds.
- MIG welders for faster and more efficient production.
- Advanced systems like plasma arc welding for complex joints.
Consumables
- High-quality filler materials compatible with the super alloy composition.
- Shielding gases like argon and helium to protect the weld pool.
Inspection Tools
- Portable ultrasonic testers.
- Radiographic film and digital radiography systems.
- Handheld dye penetrant kits for field inspections.
21. Training and Certification for Super Alloy Welders
Welding Certifications
Certified training programs, such as those offered by the American Welding Society (AWS) or TWI, ensure welders have the skills needed for super alloy applications.
Hands-On Experience
Practical experience is crucial in mastering the nuances of welding super alloys. Training programs often include:
- Simulation of extreme welding environments.
- Testing on various super alloy materials and geometries.
Continuous Learning
Super alloys are continually evolving, and so are welding techniques. Regular workshops, webinars, and industry updates help welders stay ahead.
22. How to Handle Weld Repairs in Super Alloy Steel Pipes
Identifying Repair Needs
Repairs may be needed if:
- Defects are detected during inspection.
- Welds fail to meet acceptance criteria.
Repair Techniques
- Grinding out the defective weld area and re-welding.
- Applying a weld overlay for reinforcement.
- Using advanced techniques like friction stir welding for precise repairs.
Inspection After Repairs
After repairs, all welds must undergo the same rigorous testing as the original welds to ensure quality and compliance.
23. Frequently Overlooked Factors in Super Alloy Welding
Environmental Conditions
- Humidity and temperature in the welding environment can impact weld quality.
- Use of climate-controlled facilities when welding sensitive super alloys.
Material Traceability
- Maintaining records of material batches to ensure compatibility.
- Avoiding mixing of incompatible alloys during welding.
Consumable Storage
- Proper storage of electrodes and filler materials to prevent contamination or moisture absorption.
24. Key Industry Players and Resources
Organizations and Standards Bodies
- ASME (American Society of Mechanical Engineers): Sets global standards for weld quality.
- AWS (American Welding Society): Provides training, certification, and guidelines.
- ISO (International Organization for Standardization): Maintains international standards for welded joints.
Leading Manufacturers
- Companies specializing in super alloy welding equipment and consumables, such as Lincoln Electric, ESAB, and Fronius.
25. Conclusion and Final Thoughts
The acceptance criteria for super alloy steel pipe welds represent a comprehensive approach to ensuring safety, reliability, and compliance in high-performance applications. By following established standards, leveraging advanced technologies, and prioritizing quality at every stage, industries can maintain the integrity of their systems and achieve long-term success.
Whether it’s power generation, aerospace, or petrochemical applications, the role of weld quality cannot be overstated. Investing in skilled personnel, modern equipment, and thorough inspections is the key to meeting and exceeding acceptance criteria.
You must be logged in to post a comment.