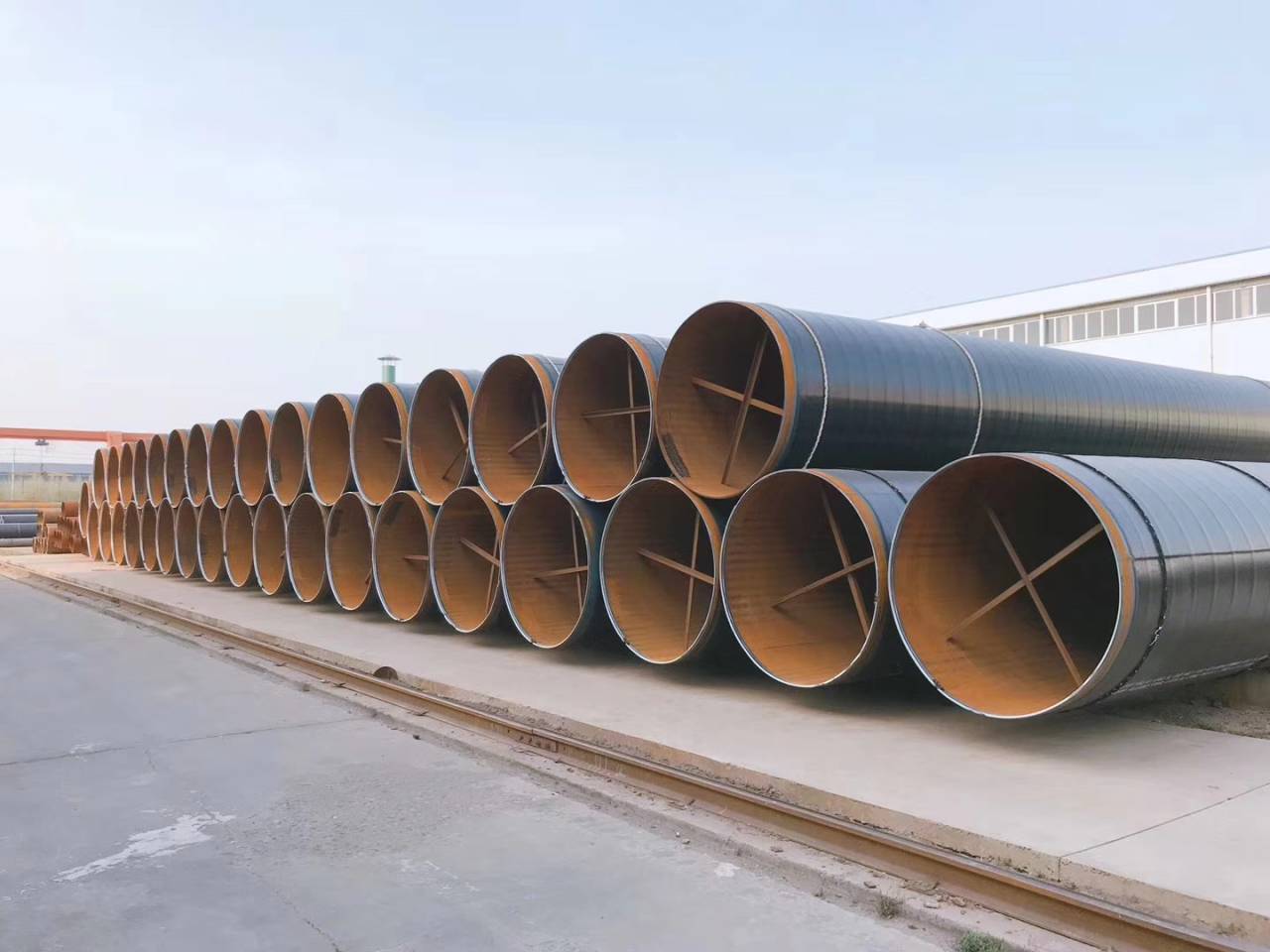
Comprehensive Analysis of LSAW Pipe / JCOE Pipe Products: Manufacturing, Standards, Applications, and Market Trends
Introduction
The LSAW Pipe (Longitudinally Submerged Arc Welded Pipe), also referred to as JCOE Pipe, is a widely used type of steel pipe with a unique welding process that makes it suitable for high-demand applications in industries such as oil and gas, construction, water pipelines, and energy infrastructure. This article delves into the manufacturing processes, technical specifications, material grades, applications, and market trends related to LSAW/JCOE pipes. We will also explore the significance of standards, such as API 5L, ISO 3183, and EN-10025, in ensuring the quality and reliability of these products.
1. Overview of LSAW/JCOE Pipe Technology
1.1 What is LSAW Pipe (JCOE Pipe)?
The LSAW pipe is a steel pipe manufactured using the Longitudinal Submerged Arc Welding (LSAW) process. In the LSAW process, steel plates are hot-rolled into a specific shape and welded longitudinally to form a pipe. This method is highly suitable for producing large-diameter, thick-walled pipes used in high-pressure environments such as oil and gas transportation pipelines.
The term JCOE refers to the specific forming process involved in LSAW pipe production. JCOE stands for the J-Shape, C-Shape, O-Shape, and E-Expanding processes. These are the steps in which the steel plates are gradually shaped into a pipe and then welded together using submerged arc welding.
Key Features of LSAW Pipe (JCOE):
- Manufacturing Process: Longitudinal submerged arc welding with JCOE forming.
- Pipe Strength: High tensile strength due to thick weld seams.
- Application: Suitable for heavy-duty applications requiring large diameter pipes.
2. Manufacturing Process of LSAW/JCOE Pipe
2.1 Steel Plate Preparation
The production of LSAW pipes begins with high-quality steel plates that are either rolled or hot-rolled into the required dimensions. These plates are then thoroughly cleaned to remove any contaminants such as rust, oil, or dust.
2.2 Forming the Pipe: JCOE Process
The JCOE forming process involves a series of mechanical steps, where the steel plate is bent into a J-shape, C-shape, and O-shape, followed by an expanding step. Here’s an overview of the process:
- J-Shape: The steel plate is first bent into a “J” shape, with the edges slightly overlapping.
- C-Shape: The edges of the “J” shape are then brought closer together to form a “C”.
- O-Shape: The “C” shape is gradually closed to form a complete circular shape.
- E-Expanding: Finally, the pipe is expanded to its final diameter, ensuring a uniform thickness along the entire length.
2.3 Welding
Once the pipe has been formed, the longitudinal edges are welded together using the submerged arc welding technique. This process involves the use of an electric arc and a continuous wire feed, which melts the edges of the plate and fuses them together under a protective flux.
2.4 Heat Treatment
After welding, the pipe is subjected to heat treatment to relieve any stress caused by the welding process and to enhance the overall strength of the pipe. This process ensures that the welded seam is both strong and resistant to cracking.
2.5 Testing and Inspection
Before the LSAW pipes are ready for use, they undergo several quality control procedures. Common tests include:
- Ultrasonic Testing (UT): To detect any internal flaws or defects.
- X-Ray Inspection: For checking the internal weld seam quality.
- Hydrostatic Testing: To check for leaks and to ensure the pipe can withstand high internal pressures.
- Visual Inspection: To assess surface quality.
3. Specifications of LSAW/JCOE Pipes
3.1 Technical Standards
LSAW pipes are manufactured according to a variety of international standards. These standards ensure consistency, safety, and reliability across different applications. The most commonly used standards for LSAW pipes include:
Standard | Description |
---|---|
API 5L | Specification for line pipe used in the transportation of oil and natural gas. |
ISO 3183 | Similar to API 5L but internationally recognized standard for pipelines. |
EN-10025 | European standard for hot-rolled structural steel. |
GB/T 3091 | Chinese standard for welded steel pipes for low-pressure fluid transport. |
GT/T 9711-2011 | Chinese standard for LSAW pipes used in the oil and gas industry. |
3.2 Pipe Sizes and Dimensions
LSAW pipes are available in a range of sizes and specifications. These include varying outer diameters, wall thicknesses, and lengths, making them suitable for different applications.
Parameter | Range |
---|---|
Outer Diameter | 406 mm to 1524 mm |
Wall Thickness | 8 mm to 60 mm |
Length | 3 m to 12 m, with customization options available |
3.3 Pipe Grades
LSAW pipes come in various grades to meet specific mechanical and chemical properties. The most common grades are:
Grade | Description |
---|---|
B | Standard carbon steel for general use. |
X42 | Suitable for medium-strength applications. |
X52 | Suitable for higher-pressure applications. |
X70 | High-strength steel for demanding environments. |
L245-L485 | Suitable for low to high-pressure pipelines. |
S235-S460 | Structural steel with varying strengths. |
Q235-Q460 | High-tensile steel suitable for construction and industrial applications. |
3.4 Coating Options
LSAW pipes often undergo additional coating to protect against corrosion and improve durability, especially for underground or subsea applications. The most common coatings include:
Coating Type | Description |
---|---|
3PE | Three-layer polyethylene coating for corrosion resistance. |
3PP | Three-layer polypropylene coating, offering similar corrosion resistance. |
FBE | Fusion bonded epoxy coating used for added protection. |
4. Applications of LSAW/JCOE Pipes
LSAW pipes are widely used in various industries due to their ability to withstand high pressure, mechanical stress, and aggressive environments. Here are the primary applications of LSAW pipes:
4.1 Oil and Gas Industry
The most prominent use of LSAW pipes is in the transportation of oil and natural gas. Their high strength and ability to handle high-pressure conditions make them ideal for long-distance pipelines, whether underground or subsea. LSAW pipes are commonly used in:
- Crude oil pipelines: Long pipelines that transport crude oil from extraction sites to refineries.
- Natural gas pipelines: High-pressure pipelines used to transport natural gas over vast distances.
4.2 Construction and Infrastructure
LSAW pipes are used in construction projects, particularly for structural applications. They are used in:
- Piling for foundations: Heavy-duty piles that are driven into the ground to support buildings, bridges, and other infrastructure.
- Structural steelwork: LSAW pipes serve as columns, beams, and other structural components.
4.3 Water Transportation
LSAW pipes are also used for the transportation of water in urban and rural infrastructure projects. The pipes’ resistance to corrosion and wear makes them suitable for:
- Water supply pipelines: Supplying water to cities and municipalities.
- Sewage and wastewater pipes: For both residential and industrial wastewater treatment and transportation.
5. Market Trends and Future Prospects
5.1 Increasing Demand for LSAW Pipes
The demand for LSAW pipes is growing, primarily driven by the increasing need for infrastructure in emerging economies and the expansion of energy networks globally. Particularly, regions with growing oil, gas, and water infrastructure markets, such as the Middle East, Asia-Pacific, and South America, are witnessing significant growth in LSAW pipe demand.
5.2 Technological Advancements
As the demand for high-quality, high-strength pipes increases, the industry is witnessing advancements in LSAW pipe manufacturing. Key technological advancements include:
- Automation and Robotics: The use of robotic welding systems and automated quality checks to enhance precision and reduce human error.
- Material Innovation: The development of advanced coatings and stronger alloys for greater durability in challenging environments.
5.3 Environmental Considerations
The shift towards sustainability is prompting the development of greener manufacturing processes for LSAW pipes. Increased environmental regulations are pushing manufacturers to adopt energy-efficient production methods and focus on recycling and reducing waste.
6. Conclusion
LSAW/JCOE pipes are crucial components in various industrial sectors, particularly in oil and gas, construction, and water infrastructure. With their robust manufacturing process and high durability, these pipes are ideally suited for challenging applications that require high-pressure resistance and long service life.
The future of LSAW pipes looks promising, with technological innovations and increasing infrastructure demands driving their production and use. Whether it’s for building pipelines across vast terrains or supporting critical infrastructure, LSAW pipes play an integral role in modern industry.
You must be logged in to post a comment.