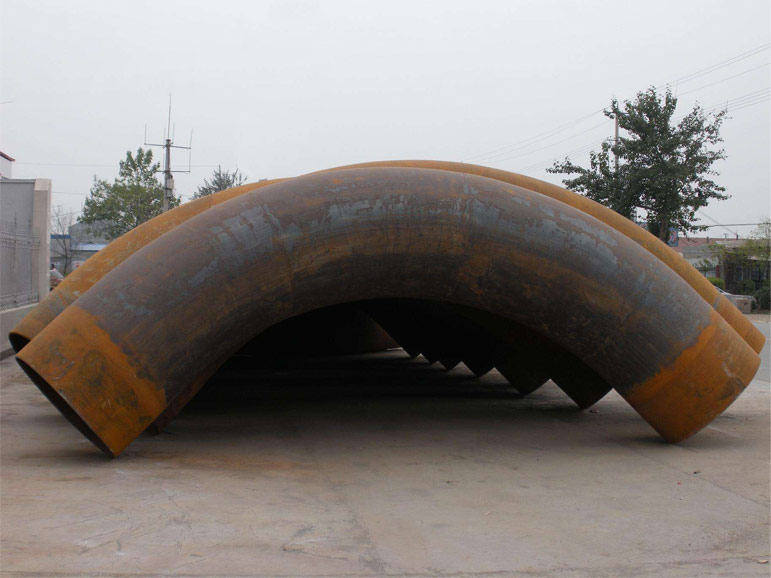
Hot Induction Bends: Manufacturing, Standards, and Applications
Introduction
Hot induction bends are widely used in industries such as oil and gas, petrochemical, power generation, and water distribution. These bends are crucial components in piping systems, allowing for smooth directional changes without the need for multiple fittings or welds. The induction bending process offers a highly controlled method for producing bends with consistent quality, precision, and structural integrity.
Induction bends are typically manufactured to meet the ASME B16.49 standard, which governs the dimensions, materials, and testing requirements for factory-made wrought bends. These bends can be made from either seamless or welded pipes, with or without tangent lengths, and are produced using either cold-forming or heat-forming methods. However, the heat-forming process, which utilizes induction heating, is the most common due to its ability to produce bends with high accuracy and minimal distortion.
This article explores the hot induction bending process, the ASME B16.49 standard, and the properties and applications of induction bends. We will also discuss the advantages of using hot induction bends over traditional bending methods and the factors that influence the quality of the final product.
Table of Contents
- What Are Hot Induction Bends?
- The Induction Bending Process
- 2.1 Induction Heating
- 2.2 Cooling Methods
- ASME B16.49 Standard for Induction Bends
- Materials Used in Induction Bends
- Applications of Hot Induction Bends
- Advantages of Hot Induction Bends
- Factors Influencing the Quality of Induction Bends
- Frequently Asked Questions (FAQ)
- Conclusion
What Are Hot Induction Bends? {#what-are-hot-induction-bends}
Hot induction bends are pipe bends that are formed using the induction heating process, which involves heating a narrow section of the pipe to a high temperature and then bending it to the desired angle. This process allows for the creation of bends with large diameters and thick walls, making them suitable for high-pressure and high-temperature applications.
Induction bends can be produced from both seamless and welded pipes and may include tangent lengths (straight sections at the ends of the bend) or be made without tangents, depending on the specific requirements of the application. The ASME B16.49 standard covers bends in a wide range of wall thicknesses and diameters, ensuring that they meet the necessary performance criteria for use in critical piping systems.
The Induction Bending Process {#the-induction-bending-process}
The induction bending process is a heat-forming method that utilizes induction heating to bend pipes or cylinders with high precision. This process is ideal for producing bends with minimal deformation and uniform wall thickness.
2.1 Induction Heating {#induction-heating}
The core of the induction bending process is the induction heating system, which uses an inductor coil to generate a magnetic field. As the pipe or cylinder passes through the coil, the magnetic field induces eddy currents in the material, causing it to heat up rapidly. The heating is localized to a narrow band around the pipe, typically 360 degrees around the circumference, ensuring that only the section to be bent is heated.
- The temperature in the heated zone is carefully controlled, usually between 850°C and 1100°C, depending on the material being bent.
- As the pipe is heated, it is pushed through the inductor coil at a constant velocity, allowing for a smooth, controlled bend.
- The bending angle and radius are determined by the bending arm, which applies a force to the pipe as it moves through the heated zone.
2.2 Cooling Methods {#cooling-methods}
Once the pipe has been bent, it must be cooled to set the bend in place. There are several methods for cooling the pipe after it passes through the inductor coil:
- Forced air cooling: In this method, air is blown over the heated section of the pipe to cool it rapidly. This method is often used for carbon steel and other materials that can withstand rapid cooling without cracking.
- Water spray cooling: Water is sprayed onto the heated section to cool it more quickly than air cooling. This method is commonly used for stainless steel and other materials that require faster cooling to maintain their mechanical properties.
- Still air cooling: In some cases, the pipe may be allowed to cool naturally in still air. This method is used when a slower cooling rate is desired to prevent thermal stresses or distortion.
ASME B16.49 Standard for Induction Bends {#asme-b1649-standard-for-induction-bends}
The ASME B16.49 standard provides the specifications for factory-made wrought bends used in piping systems. This standard covers bends made from both seamless and welded pipes and applies to bends with or without tangent lengths. The standard specifies the dimensions, materials, testing requirements, and marking for induction bends.
Key Provisions of ASME B16.49:
- Wall thickness: The standard covers bends in any producible wall thickness, ensuring that the bends can withstand the required internal pressures.
- Bend radius: The standard allows for a range of bend radii, typically from 1.5D to 5D, where D is the nominal pipe diameter.
- Material requirements: The standard specifies the types of materials that can be used for induction bends, including carbon steel, stainless steel, and alloy steel.
- Testing and inspection: Induction bends must undergo non-destructive testing (NDT), such as ultrasonic testing (UT) or radiographic testing (RT), to ensure that there are no defects in the material or welds.
- Marking: Each bend must be marked with the manufacturer’s name, material grade, bend radius, and other relevant information to ensure traceability.
For more detailed information on the ASME B16.49 standard, visit the ASME website.
Materials Used in Induction Bends {#materials-used-in-induction-bends}
Induction bends can be made from a variety of materials, depending on the specific requirements of the application. The most commonly used materials include:
- Carbon steel: Carbon steel is widely used for induction bends due to its strength, ductility, and cost-effectiveness. It is suitable for applications where corrosion resistance is not a primary concern.
- Stainless steel: Stainless steel bends are used in applications where corrosion resistance is critical, such as in chemical processing or offshore environments. Stainless steel also offers excellent high-temperature resistance.
- Alloy steel: Alloy steels, which contain additional elements such as chromium, molybdenum, or nickel, are used in high-performance applications where strength, toughness, and corrosion resistance are required.
- Duplex stainless steel: Duplex stainless steels offer a combination of high strength and excellent corrosion resistance, making them ideal for marine and oil and gas applications.
Applications of Hot Induction Bends {#applications-of-hot-induction-bends}
Hot induction bends are used in a wide range of industries and applications due to their ability to handle high pressures, high temperatures, and corrosive environments. Some common applications include:
- Oil and gas pipelines: Induction bends are used in onshore and offshore pipelines to change the direction of flow without the need for multiple fittings or welds. They are particularly useful in subsea pipelines, where reliability and durability are critical.
- Petrochemical plants: In refineries and chemical processing plants, induction bends are used to transport corrosive fluids and gases at high temperatures and pressures.
- Power generation: Induction bends are used in steam lines, boilers, and turbine systems in power plants, where they must withstand thermal cycling and high-pressure steam.
- Water distribution: Induction bends are used in municipal water systems to transport water over long distances, particularly in areas with uneven terrain where changes in direction are required.
Advantages of Hot Induction Bends {#advantages-of-hot-induction-bends}
The hot induction bending process offers several advantages over traditional bending methods, such as cold bending or welded fittings. These advantages include:
- Precision and accuracy: The induction bending process allows for precise control over the bend radius, angle, and wall thickness, ensuring that the final product meets the required specifications.
- Minimal distortion: Induction heating localizes the heat to a narrow band, minimizing the risk of distortion or flattening of the pipe during bending.
- Reduced welds: Induction bends eliminate the need for multiple fittings and welds, reducing the risk of leaks and weak points in the piping system.
- Consistent quality: The controlled nature of the induction bending process ensures that each bend is produced with consistent quality and mechanical properties.
- Cost-effectiveness: By reducing the need for additional fittings and welds, induction bends can lower the overall cost of a piping system.
Factors Influencing the Quality of Induction Bends {#factors-influencing-the-quality-of-induction-bends}
Several factors can influence the quality of hot induction bends, including:
- Material properties: The composition and microstructure of the material being bent can affect its ability to withstand the induction bending process. Materials with high ductility and toughness are generally more suitable for induction bending.
- Heating temperature: The temperature at which the pipe is heated during the induction bending process must be carefully controlled to prevent overheating or underheating, which can lead to defects such as cracking or distortion.
- Cooling rate: The rate at which the pipe is cooled after bending can affect its mechanical properties. Rapid cooling may cause thermal stresses, while slow cooling may result in grain growth or softening of the material.
- Bend radius: The bend radius must be chosen carefully to ensure that the pipe can withstand the applied loads without buckling or flattening.
- Inspection and testing: Non-destructive testing (NDT) methods, such as ultrasonic testing or radiographic testing, are essential for detecting any defects in the material or welds that could compromise the integrity of the bend.
Frequently Asked Questions (FAQ) {#faq}
1. What is hot induction bending?
Hot induction bending is a process that uses induction heating to bend pipes or cylinders with high precision. The pipe is heated in a narrow band and then bent to the desired angle while being pushed through an inductor coil.
2. What materials can be used for induction bends?
Induction bends can be made from materials such as carbon steel, stainless steel, alloy steel, and duplex stainless steel, depending on the application requirements.
3. What is the ASME B16.49 standard?
The ASME B16.49 standard specifies the dimensions, materials, and testing requirements for factory-made wrought bends used in piping systems. It covers bends made from both seamless and welded pipes.
4. What are the advantages of hot induction bends?
Hot induction bends offer several advantages, including precision, minimal distortion, reduced welds, consistent quality, and cost-effectiveness.
5. What industries use hot induction bends?
Hot induction bends are used in industries such as oil and gas, petrochemical, power generation, and water distribution, where they are required to handle high pressures, high temperatures, and corrosive environments.
Conclusion {#conclusion}
Hot induction bends are a vital component in modern piping systems, offering a reliable and cost-effective solution for changing the direction of flow in high-pressure and high-temperature applications. The induction bending process allows for the production of bends with precision, minimal distortion, and consistent quality, making them suitable for use in critical industries such as oil and gas, power generation, and chemical processing.
You must be logged in to post a comment.