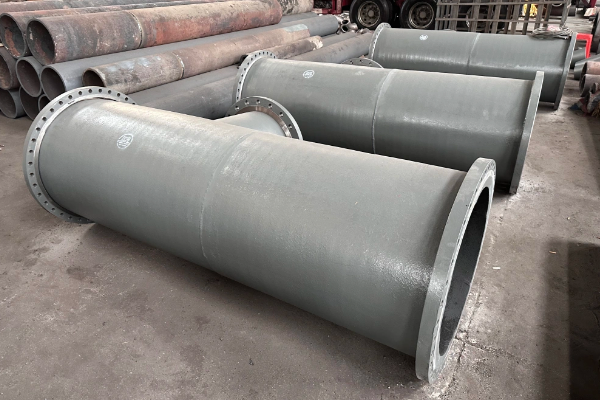
Bimetallic Composite Pipe: Preparation and Performance Evaluation of Erosion-Resistant Lining
Introduction
In many industrial sectors, such as oil and gas, mining, and chemical processing, piping systems are exposed to severe erosive environments. These environments often involve the transport of abrasive materials, such as slurry, sand, or other particulates, which can cause significant wear and tear on the internal surfaces of pipes. Traditional metallic pipes, while strong, often suffer from erosion-related failures, leading to costly repairs, downtime, and reduced operational efficiency. To address this challenge, bimetallic composite pipes have emerged as a promising solution, combining the strength of a metallic outer layer with the erosion resistance of a specialized inner lining.
The concept of bimetallic composite pipes involves the use of two distinct materials: a base metal (typically steel) for structural integrity and a corrosion- or erosion-resistant lining material, such as a hard alloy or ceramic, to protect against wear. This article provides an in-depth exploration of the preparation and performance evaluation of erosion-resistant linings in bimetallic composite pipes. We will examine the materials used, the manufacturing processes, and the performance of these pipes in erosive environments, supported by tables and data.
The construction of a bimetallic composite pipe consists of an inner layer made from a corrosion-resistant material, commonly referred to as the cladding or lining layer, and an outer layer composed of a structural base material. The cladding material is chosen for its resistance to corrosion, erosion, and specific environmental conditions, while the base material is selected for its mechanical strength and cost-effectiveness.
The bonding between the cladding and base materials is achieved through methods such as explosive bonding, roll bonding, or welding. These techniques ensure a strong and durable connection, allowing the pipe to withstand its intended operating conditions.
Bimetallic composite pipes are utilized across various industries, including oil and gas, chemical processing, power generation, and mining. They are particularly effective in environments where corrosion, erosion, or high temperatures are concerns. The corrosion-resistant cladding safeguards the pipe from chemical damage, while the base material provides structural integrity.
It’s crucial to recognize that the specific properties and performance of bimetallic composite pipes can vary based on the materials used, manufacturing processes, and application requirements. Therefore, consulting with manufacturers or industry experts is recommended for detailed guidance on selecting and utilizing these pipes.
Technical Specifications
- Outer Layer: Made from ordinary steel pipe.
- Inner Lining: Composed of high-chromium cast iron, formed through a casting process.
- Material Grade for Elbow: KMTBCr26
- Working Temperature: 150°C
- Working Pressure: 0.4 MPa
- Working Medium: Pulverized coal and air two-phase flow
- Maximum Flow Velocity: 28 m/s
Technical Requirements
The bimetallic wear-resistant composite elbow must meet the following performance criteria:
- Flexural Strength: > 610 MN/m²
- Tensile Strength: > 415 MN/m²
- Impact Toughness: > 15 J/cm²
- Hardness of Wear-Resistant Layer: > 50
The inner and outer surfaces of the bimetallic wear-resistant composite elbow should be smooth and free from defects such as burrs, cracks, porosity, and air bubbles. The flow direction of the medium must be clearly marked. Each elbow’s inner lining must be formed in a single process, with no welded seams allowed post-production.
Dimensional and Material Specifications
- Dimensional Deviation: Compliance with GB3092, GB8162, and GB8163 standards.
- Thickness Deviation of Inner Lining: ≤ +1.2 mm.
- Weight: Each elbow must not exceed the design weight, which must be clearly marked.
The composite pipe is manufactured using seamless steel pipe, adhering to relevant performance agreements. The installation of the bimetallic wear-resistant composite elbow is performed through direct welding, using 16MnR# steel for the outer welded pipe.
Installation and Maintenance
Each inlet and outlet of the elbow features a straight section of specified length, consistent with the elbow body’s material and wall thickness. An additional 100mm transition section is provided for welding to the powder feeding pipeline. On-site welding must ensure good performance at room temperature.
The service life of the bimetallic wear-resistant composite elbow is expected to last no less than 10 years (approximately 8,000 hours of operation per year). Under abnormal conditions, such as spontaneous combustion in the powder feeding pipeline, the lining wear-resistant layer should remain intact without cracking or peeling. The design should facilitate easy unloading, installation, and maintenance.
Quality Assurance
Before leaving the factory, each elbow undergoes sealing performance testing according to relevant standards. Products failing to meet specified quality and performance standards are not allowed to leave the factory. Compliance with the “DL/T 680-1999 Technical Conditions Standard for Wear-Resistant Pipelines” is mandatory.
Main Technical Parameters of Bimetal Composite Wear-Resistant Elbow
- Thickness:
- Inner Arc: 22 mm
- Outer Arc: 32 mm
- Eccentricity: 5 mm
- Design Pressure: 1.6 MPa
- Hydraulic Test Pressure: 5.6-19 MPa
- Design Temperature: 350°C
Special corundum ceramics, made from rare metal oxides and sintered at 1730°C, are incorporated into the wear surface to enhance wear resistance, while the matrix remains an ordinary metal composite pipe.
The Need for Erosion-Resistant Linings in Industrial Piping
Challenges in Erosive Environments
Pipes used in industries like oil and gas, mining, and chemical processing are often subjected to harsh conditions where abrasive particles are transported at high velocities. These particles can cause erosion, leading to material loss, thinning of the pipe walls, and eventual failure. The key challenges posed by erosive environments include:
- Material Loss: Continuous impact of abrasive particles leads to the gradual removal of material from the pipe surface.
- Reduced Lifespan: Erosion accelerates the degradation of pipes, reducing their operational lifespan.
- Increased Maintenance Costs: Frequent repairs or replacements of eroded pipes result in higher maintenance costs and operational downtime.
- Safety Risks: Erosion-related failures can lead to leaks, spills, or even catastrophic failures, posing safety risks to personnel and the environment.
Advantages of Bimetallic Composite Pipes
Bimetallic composite pipes offer a solution to the challenges posed by erosive environments by combining the benefits of two materials:
- Structural Strength: The outer layer, typically made of carbon steel or stainless steel, provides the necessary mechanical strength to withstand internal pressure and external forces.
- Erosion Resistance: The inner lining, made of a hard alloy or ceramic material, offers superior resistance to erosion, protecting the pipe from abrasive wear.
By using bimetallic composite pipes, industries can significantly extend the lifespan of their piping systems, reduce maintenance costs, and improve overall operational efficiency.
Materials Used in Bimetallic Composite Pipes
Base Metal (Outer Layer)
The base metal of a bimetallic composite pipe is selected based on the mechanical requirements of the application. Common materials used for the outer layer include:
- Carbon Steel: Carbon steel is widely used due to its high strength, low cost, and ease of fabrication. It is suitable for applications where corrosion is not a major concern.
- Stainless Steel: Stainless steel offers better corrosion resistance than carbon steel and is often used in environments where both erosion and corrosion are concerns.
- Alloy Steel: Alloy steels, such as chromium-molybdenum steels, provide enhanced strength and temperature resistance, making them suitable for high-temperature applications.
Lining Material (Inner Layer)
The inner lining material is selected for its ability to resist erosion and withstand the abrasive forces of the transported materials. Common lining materials include:
- Hard Alloys: Hard alloys, such as chromium carbide or tungsten carbide, are commonly used for erosion-resistant linings. These materials offer excellent hardness and wear resistance, making them ideal for protecting against abrasive particles.
- Ceramics: Ceramic materials, such as alumina (Al₂O₃) or silicon carbide (SiC), are known for their exceptional hardness and erosion resistance. Ceramics are often used in highly abrasive environments where metal linings may not provide sufficient protection.
- Polymer-Based Linings: In some cases, polymer-based linings, such as polyurethane or epoxy coatings, are used to provide erosion resistance. These materials are typically used in applications with moderate erosion and where flexibility is required.
Table 1: Common Materials Used in Bimetallic Composite Pipes
Component | Material | Properties | Applications |
---|---|---|---|
Outer Layer | Carbon Steel | High strength, low cost, easy to fabricate | General industrial applications |
Stainless Steel | Corrosion resistance, good mechanical properties | Chemical processing, oil & gas | |
Alloy Steel | High-temperature resistance, enhanced strength | High-temperature piping systems | |
Inner Lining | Chromium Carbide | High hardness, excellent wear resistance | Mining, slurry transport |
Tungsten Carbide | Extreme hardness, superior erosion resistance | Oil & gas, high-abrasion environments | |
Alumina (Al₂O₃) | Exceptional hardness, high erosion resistance | Chemical processing, high-abrasion applications | |
Silicon Carbide (SiC) | High hardness, thermal stability, chemical resistance | High-temperature, high-abrasion environments | |
Polyurethane | Flexibility, moderate erosion resistance | Low to moderate abrasion applications | |
Epoxy Coatings | Chemical resistance, moderate erosion resistance | Chemical processing, water treatment |
Preparation of Bimetallic Composite Pipes
Cladding and Lining Techniques
The preparation of bimetallic composite pipes involves the application of the erosion-resistant lining to the base metal. Several techniques are used to achieve a strong bond between the outer layer and the inner lining, ensuring that the composite pipe can withstand the harsh conditions of erosive environments. Common techniques include:
1. Weld Overlay Cladding
Weld overlay cladding involves the deposition of a hard alloy material onto the inner surface of the base metal pipe using welding techniques. The process typically involves the following steps:
- Surface Preparation: The inner surface of the base metal pipe is cleaned and prepared to ensure proper adhesion of the cladding material.
- Welding: A hard alloy material, such as chromium carbide, is deposited onto the inner surface using welding techniques such as plasma arc welding or submerged arc welding.
- Post-Weld Treatment: After the cladding is applied, the pipe may undergo heat treatment to relieve residual stresses and improve the bond between the base metal and the cladding.
2. Centrifugal Casting
Centrifugal casting is a technique used to apply ceramic or metal linings to the inner surface of a pipe. The process involves the following steps:
- Mold Preparation: A mold is prepared with the desired dimensions of the pipe.
- Casting: Molten metal or ceramic material is poured into the mold, and the mold is rotated at high speed. The centrifugal force pushes the material against the inner surface of the mold, forming a uniform lining.
- Cooling and Solidification: The lining material is allowed to cool and solidify, forming a strong bond with the base metal.
3. Thermal Spraying
Thermal spraying is a process in which a hard alloy or ceramic material is melted and sprayed onto the inner surface of the pipe. The process involves the following steps:
- Surface Preparation: The inner surface of the pipe is cleaned and roughened to improve adhesion.
- Spraying: The lining material is melted and sprayed onto the surface using techniques such as plasma spraying or high-velocity oxygen fuel (HVOF) spraying.
- Post-Spray Treatment: The pipe may undergo heat treatment or machining to achieve the desired surface finish and mechanical properties.
Table 2: Common Cladding and Lining Techniques for Bimetallic Composite Pipes
Technique | Lining Material | Process Description | Advantages | Applications |
---|---|---|---|---|
Weld Overlay Cladding | Chromium Carbide, Tungsten Carbide | Hard alloy is deposited onto the inner surface using welding techniques | Strong bond, high erosion resistance | Oil & gas, mining, slurry transport |
Centrifugal Casting | Ceramics, Metal Alloys | Molten material is cast onto the inner surface using centrifugal force | Uniform lining, good adhesion | High-temperature, high-abrasion environments |
Thermal Spraying | Ceramics, Hard Alloys | Lining material is melted and sprayed onto the surface | Versatile, can apply a wide range of materials | Chemical processing, high-abrasion applications |
Performance Evaluation of Erosion-Resistant Linings
Testing Methods
The performance of erosion-resistant linings in bimetallic composite pipes is evaluated through a series of tests designed to simulate real-world erosive conditions. Common testing methods include:
1. Erosion Testing
Erosion testing involves subjecting the lined pipe to a stream of abrasive particles, such as sand or slurry, at high velocity. The test is designed to measure the rate of material loss from the lining over time. Key parameters measured during erosion testing include:
- Erosion Rate: The rate at which material is removed from the lining due to the impact of abrasive particles.
- Weight Loss: The total weight loss of the lining material after a specified period of testing.
- Surface Roughness: Changes in the surface roughness of the lining material due to erosion.
2. Hardness Testing
Hardness testing is used to evaluate the resistance of the lining material to indentation and wear. Common hardness tests include the Vickers hardness test and the Rockwell hardness test. Higher hardness values indicate better resistance to wear and erosion.
3. Adhesion Testing
Adhesion testing is used to evaluate the strength of the bond between the base metal and the lining material. Poor adhesion can lead to delamination or spalling of the lining, reducing its effectiveness. Common adhesion tests include pull-off tests and shear tests.
Table 3: Performance Testing Methods for Erosion-Resistant Linings
Test | Purpose | Measured Parameters | Significance |
---|---|---|---|
Erosion Testing | Evaluate erosion resistance | Erosion rate, weight loss, surface roughness | Determines the durability of the lining in abrasive environments |
Hardness Testing | Measure material hardness | Vickers hardness, Rockwell hardness | Higher hardness indicates better wear resistance |
Adhesion Testing | Evaluate bond strength | Pull-off strength, shear strength | Ensures the lining remains intact during service |
Performance Results
Erosion Resistance
Erosion testing of bimetallic composite pipes has shown that the use of hard alloy or ceramic linings significantly improves the erosion resistance of the pipe. In a typical erosion test, pipes lined with chromium carbide or alumina exhibited erosion rates that were 50-70% lower than those of unlined carbon steel pipes. The results indicate that the use of erosion-resistant linings can extend the operational lifespan of the pipe by several years, even in highly abrasive environments.
Hardness
Hardness testing of the lining materials revealed that ceramic linings, such as alumina and silicon carbide, had the highest hardness values, ranging from 1500 to 2000 HV (Vickers Hardness). Hard alloy linings, such as chromium carbide, had hardness values in the range of 600 to 800 HV, while unlined carbon steel had a hardness of 150 to 200 HV. The higher hardness of the lining materials correlates with their improved erosion resistance.
Adhesion
Adhesion testing of the lined pipes demonstrated that both weld overlay cladding and centrifugal casting techniques produced strong bonds between the base metal and the lining material. Pull-off tests showed that the adhesion strength of the lining was greater than the tensile strength of the base metal, indicating that the lining would not delaminate or spall under normal operating conditions.
Conclusion
Bimetallic composite pipes with erosion-resistant linings offer a highly effective solution for industries facing erosive environments. By combining the structural strength of a metallic outer layer with the superior wear resistance of a hard alloy or ceramic lining, these pipes can significantly extend the lifespan of piping systems, reduce maintenance costs, and improve operational efficiency. The preparation of these pipes involves advanced techniques such as weld overlay cladding, centrifugal casting, and thermal spraying, each of which offers unique advantages depending on the application.
Performance evaluations, including erosion testing, hardness testing, and adhesion testing, have demonstrated the effectiveness of erosion-resistant linings in protecting against abrasive wear. The results of these tests show that bimetallic composite pipes can withstand the harsh conditions of erosive environments, making them an ideal choice for industries such as oil and gas, mining, and chemical processing.
FAQ
What are bimetallic composite pipes?
Bimetallic composite pipes consist of two distinct materials: a base metal (typically steel) for structural strength and an erosion-resistant lining material, such as a hard alloy or ceramic, to protect against wear.
What materials are used for the lining in bimetallic composite pipes?
Common lining materials include hard alloys (e.g., chromium carbide, tungsten carbide) and ceramics (e.g., alumina, silicon carbide), which offer superior erosion resistance.
How are bimetallic composite pipes prepared?
Bimetallic composite pipes are prepared using techniques such as weld overlay cladding, centrifugal casting, and thermal spraying, which ensure a strong bond between the base metal and the lining material.
What tests are used to evaluate the performance of erosion-resistant linings?
Performance evaluation includes erosion testing, hardness testing, and adhesion testing to assess the durability, wear resistance, and bond strength of the lining material.
What are the benefits of using bimetallic composite pipes in erosive environments?
Bimetallic composite pipes offer extended lifespan, reduced maintenance costs, and improved operational efficiency by protecting against erosion-related wear and tear.
You must be logged in to post a comment.