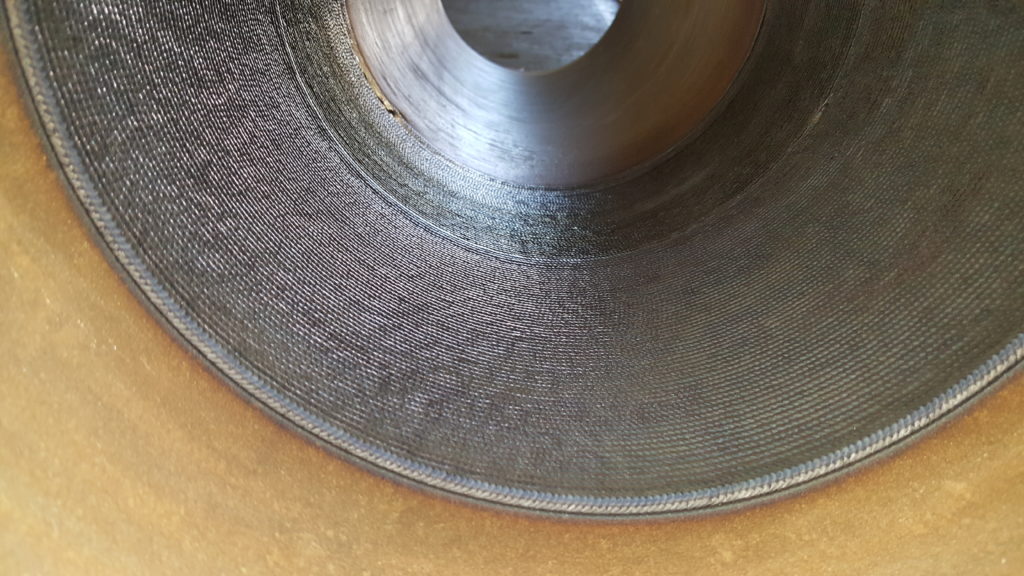
Exploring the buckling failure mechanism of liner pipes in bimetal mechanical clad pipes under complex loading conditions is crucial for understanding their structural integrity and reliability, especially in demanding applications such as oil and gas transportation. Bimetal mechanical clad pipes combine the advantages of two different materials, typically a corrosion-resistant alloy as the liner and a carbon steel or other high-strength material as the outer pipe. This combination provides both strength and corrosion resistance, making them ideal for harsh environments. However, the interaction between these materials under complex loading can lead to buckling, a critical failure mode that must be thoroughly understood and mitigated.
Introduction to Bimetal Mechanical Clad Pipes
Bimetal mechanical clad pipes are engineered to withstand extreme conditions by leveraging the properties of two distinct materials. The outer pipe, often made from carbon steel, provides mechanical strength and load-bearing capacity, while the inner liner, typically a corrosion-resistant alloy like stainless steel or Inconel, offers protection against corrosive substances. This dual-layer construction is particularly beneficial in industries such as oil and gas, where pipes are exposed to high pressures, temperatures, and corrosive environments.
Understanding Buckling in Liner Pipes
Buckling refers to the sudden failure of a structural component subjected to compressive stress, leading to a deformation mode characterized by bending or collapsing. In the context of liner pipes within bimetal mechanical clad pipes, buckling can occur due to various factors, including differential thermal expansion, external pressure, and axial loads. Understanding the buckling mechanism is essential for designing pipes that can withstand complex loading without failure.
Factors Influencing Buckling in Liner Pipes
-
Material Properties
- Elastic Modulus and Yield Strength: The elastic modulus and yield strength of both the liner and outer pipe materials influence the buckling resistance. A higher elastic modulus generally enhances buckling resistance.
- Thermal Expansion Coefficient: Differences in thermal expansion coefficients between the liner and outer pipe can induce thermal stresses, contributing to buckling.
-
Geometric Parameters
- Pipe Diameter and Wall Thickness: Larger diameters and thinner walls increase the susceptibility to buckling. The ratio of diameter to wall thickness is a critical parameter in buckling analysis.
- Liner Thickness: The thickness of the liner relative to the outer pipe affects the load distribution and buckling behavior.
-
Loading Conditions
- Axial Loads: Compressive axial loads can induce buckling, especially if they exceed the critical buckling load of the liner.
- External Pressure: High external pressure, common in subsea applications, can exacerbate buckling by reducing the effective load-bearing capacity.
- Bending Moments: Complex loading often involves bending moments, which can interact with axial loads to trigger buckling.
-
Boundary Conditions and Constraints
- End Conditions: The manner in which the pipe ends are constrained (e.g., fixed, pinned, or free) significantly affects the buckling behavior.
- Support Conditions: Intermediate supports or constraints can alter the effective length and buckling mode of the liner.
Buckling Analysis Methodologies
-
Analytical Methods
- Euler’s Buckling Theory: Provides a fundamental approach to estimating the critical buckling load for idealized conditions, assuming perfect geometry and material properties.
- Energy Methods: Utilize the principle of minimum potential energy to derive buckling loads, accounting for imperfections and non-linearities.
-
Numerical Methods
- Finite Element Analysis (FEA): A powerful tool for simulating complex loading scenarios and predicting buckling behavior. FEA models can incorporate material non-linearities, geometric imperfections, and detailed loading conditions.
- Non-linear Analysis: Involves solving the governing equations of motion with non-linear material and geometric properties to capture realistic buckling behavior.
-
Experimental Methods
- Physical Testing: Conducting laboratory tests on scaled models or full-size pipes to observe buckling behavior under controlled conditions. These tests validate analytical and numerical predictions.
- Strain Gauges and Sensors: Employing strain gauges and other sensors to monitor deformation and identify the onset of buckling during tests.
Buckling Failure Mechanism: Case Study
Scenario Description
In this case study, we analyze the buckling failure mechanism of a liner pipe in a bimetal mechanical clad pipe used in a subsea oil pipeline. The pipe is subjected to complex loading, including axial compression, external pressure, and bending due to seabed irregularities.
Material and Geometric Parameters
Parameter | Liner Material | Outer Pipe Material |
---|---|---|
Material Type | Inconel 625 | Carbon Steel |
Elastic Modulus (GPa) | 205 | 210 |
Yield Strength (MPa) | 450 | 350 |
Thermal Expansion Coefficient (µm/m°C) | 12.8 | 11.7 |
Pipe Diameter (mm) | 600 | 600 |
Liner Thickness (mm) | 10 | – |
Outer Pipe Thickness (mm) | – | 20 |
Loading Conditions
Load Type | Magnitude |
---|---|
Axial Compression | 5,000 kN |
External Pressure | 10 MPa |
Bending Moment | 1,000 kNm |
Analysis Approach
-
Analytical Estimation
- Critical Buckling Load: Using Euler’s buckling theory, the critical buckling load is estimated for the liner pipe, considering idealized conditions.
- Thermal Stress Analysis: The differential thermal expansion between the liner and outer pipe is calculated to assess additional stresses.
-
Finite Element Analysis (FEA)
- Model Setup: A 3D FEA model of the bimetal clad pipe is created, incorporating material properties, geometric details, and loading conditions.
- Non-linear Analysis: Non-linear material and geometric properties are included to capture realistic buckling behavior.
- Imperfection Sensitivity: The model is analyzed for various geometric imperfections to assess their impact on buckling.
-
Experimental Validation
- Test Setup: A scaled model of the bimetal clad pipe is subjected to similar loading conditions in a laboratory setting.
- Data Collection: Strain gauges and displacement sensors are used to monitor deformation and identify the onset of buckling.
Results and Discussion
Analytical Estimation Results
- Critical Buckling Load: The analytical estimation provides a baseline critical buckling load of 4,500 kN for the liner pipe under ideal conditions.
- Thermal Stress Contribution: Differential thermal expansion induces additional compressive stresses, reducing the effective buckling resistance.
FEA Results
- Buckling Mode Shapes: The FEA model identifies multiple buckling mode shapes, with the first mode being a global buckling of the liner.
- Effect of Imperfections: Geometric imperfections significantly reduce the critical buckling load, with a 5% imperfection leading to a 20% reduction in buckling resistance.
- Stress Distribution: High stress concentrations are observed at the interface between the liner and outer pipe, indicating potential sites for crack initiation.
Experimental Validation Results
- Onset of Buckling: Experimental tests confirm the FEA predictions, with buckling observed at loads slightly below the analytical estimation due to imperfections.
- Deformation Patterns: The deformation patterns observed in the tests align with the predicted buckling mode shapes from the FEA model.
Strategies for Mitigating Buckling
-
Material Selection and Design
- Optimized Material Pairing: Selecting materials with compatible thermal expansion coefficients reduces thermal stresses.
- Increased Liner Thickness: Increasing the liner thickness enhances buckling resistance by improving load distribution.
-
Manufacturing and Installation Practices
- Precision Fabrication: Ensuring high precision in fabrication minimizes geometric imperfections that contribute to buckling.
- Controlled Installation: Implementing controlled installation procedures reduces residual stresses and enhances structural integrity.
-
Support and Constraint Optimization
- Intermediate Supports: Adding intermediate supports or constraints can reduce the effective length and improve buckling resistance.
- End Condition Optimization: Optimizing end conditions, such as using fixed or guided supports, enhances stability.
-
Monitoring and Maintenance
- Structural Health Monitoring: Implementing monitoring systems with sensors provides real-time data on pipe condition and detects early signs of buckling.
- Regular Inspections: Conducting regular inspections using non-destructive testing methods helps identify and address potential issues before failure.
Conclusion
The buckling failure mechanism of liner pipes in bimetal mechanical clad pipes under complex loading conditions is a multifaceted issue that requires a thorough understanding of material properties, geometric parameters, and loading scenarios. By employing a combination of analytical, numerical, and experimental methodologies, engineers can accurately predict and mitigate buckling risks. Implementing strategies for material selection, design optimization, and monitoring ensures the long-term reliability and safety of bimetal mechanical clad pipes in demanding applications. As technology advances, the ability to predict and manage buckling behavior will continue to improve, contributing to more resilient and efficient infrastructure solutions.
You must be logged in to post a comment.