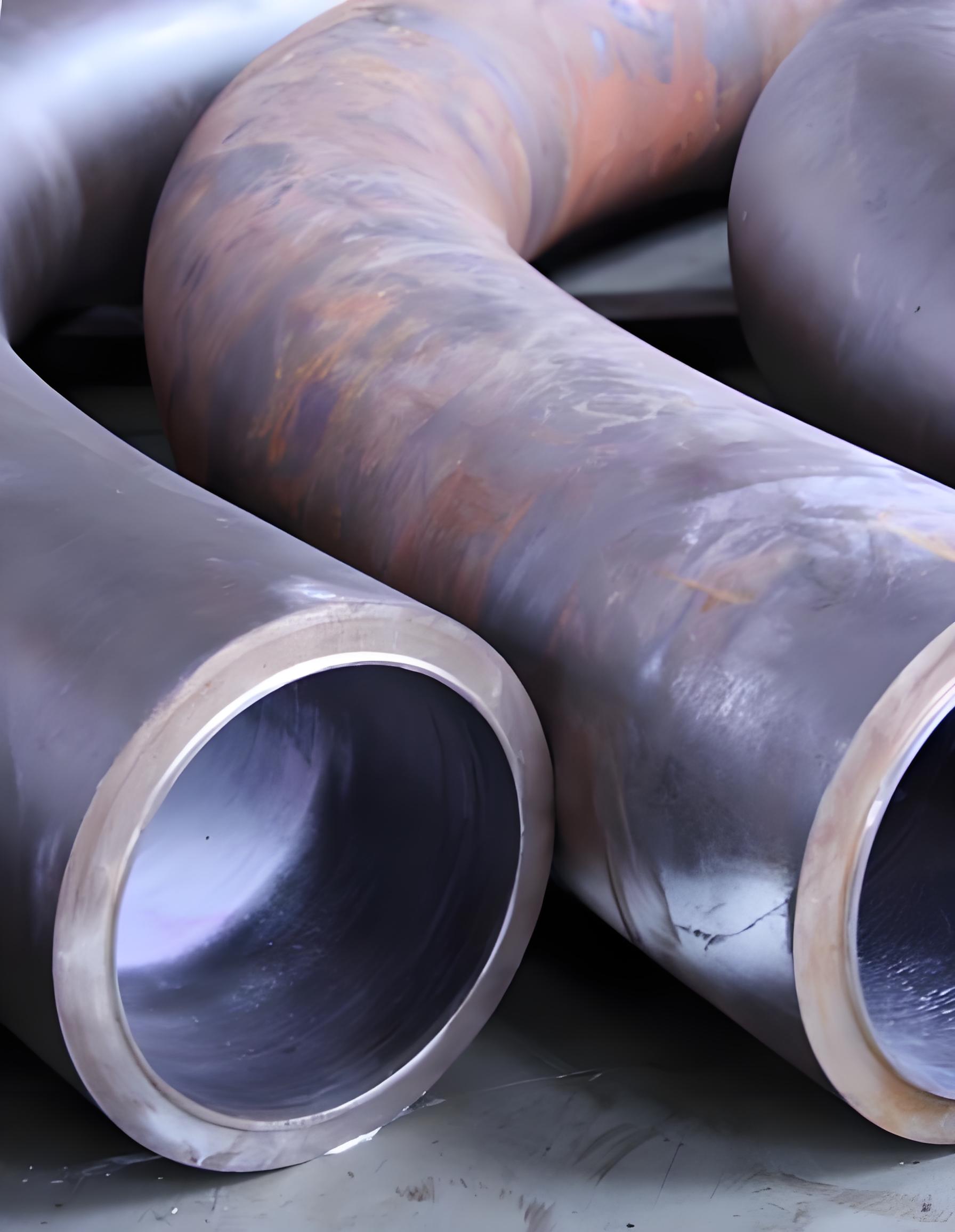
The Ratcheting Behavior of Plain Carbon Steel Pipe Elbows Subjected to Simulated Seismic In-Plane Bending
Introduction
In the realm of structural engineering, understanding how materials behave under stress is crucial, especially in seismic-prone areas. Pipe elbows, often made from plain carbon steel, are integral components in piping systems, allowing for directional changes in fluid flow. These components are particularly vulnerable during seismic events due to their geometric configuration and material properties. This article explores the ratcheting behavior of plain carbon steel pipe elbows when subjected to simulated seismic in-plane bending, examining the factors influencing this behavior, experimental observations, and potential mitigation strategies.
1. Understanding Ratcheting Behavior
1.1 Definition of Ratcheting
Ratcheting is a progressive, incremental deformation that occurs in materials subjected to cyclic loading, particularly when there is an imbalance between tensile and compressive stresses. In the context of pipe elbows, ratcheting can lead to permanent deformation, compromising the structural integrity of the piping system.
1.2 Factors Influencing Ratcheting
Several factors influence the ratcheting behavior of pipe elbows:
- Material Properties: The ductility and yield strength of the carbon steel used in the elbows affect their susceptibility to ratcheting.
- Geometry: The curvature and thickness of the elbow play a significant role in its deformation characteristics.
- Loading Conditions: The magnitude, frequency, and direction of the applied loads influence ratcheting behavior.
- Temperature: Elevated temperatures can exacerbate ratcheting by reducing material strength.
2. Seismic In-Plane Bending
2.1 Simulating Seismic Loads
Seismic events induce complex loading patterns on structures, including in-plane bending moments on pipe elbows. Simulating these conditions in a controlled environment allows for the study of ratcheting behavior under realistic scenarios.
- In-Plane Bending: Refers to bending that occurs within the plane of the elbow’s curvature, typical in seismic loading.
- Cyclic Loading: Repeated application of bending moments to mimic the dynamic nature of seismic forces.
2.2 Experimental Setup
To study the ratcheting behavior, experiments are conducted using:
- Hydraulic Actuators: Apply controlled cyclic bending moments to the pipe elbows.
- Strain Gauges: Measure the deformation and strain experienced by the elbows.
- Temperature Control: Maintain consistent environmental conditions to isolate the effects of mechanical loading.
3. Observations and Findings
3.1 Deformation Patterns
Experiments reveal distinct deformation patterns in pipe elbows subjected to seismic in-plane bending:
- Localized Buckling: Occurs at the intrados (inner curve) of the elbow, leading to localized thinning and increased susceptibility to ratcheting.
- Progressive Ovalization: The cross-section of the elbow becomes oval over successive cycles, indicating cumulative deformation.
3.2 Ratcheting Strain Accumulation
The accumulation of ratcheting strain is influenced by:
- Load Magnitude: Higher bending moments result in greater ratcheting strain accumulation.
- Cycle Count: The number of loading cycles correlates with the extent of permanent deformation.
- Material Hardening: The strain-hardening capacity of the carbon steel can mitigate ratcheting to some extent.
3.3 Failure Modes
Failure modes observed in the experiments include:
- Crack Initiation and Propagation: Initiated at areas of high stress concentration, such as the intrados.
- Fracture: Complete separation of the material due to excessive ratcheting strain.
4. Mitigation Strategies
4.1 Design Improvements
Design modifications can enhance the resilience of pipe elbows against ratcheting:
- Increased Wall Thickness: Provides additional material to resist deformation.
- Optimized Curvature: Reducing the curvature can decrease stress concentration and improve load distribution.
4.2 Material Selection
Using materials with superior mechanical properties can reduce ratcheting:
- High-Strength Alloys: Alloys with higher yield strength and ductility can better withstand cyclic loading.
- Heat Treatment: Processes such as annealing can enhance the material’s resistance to ratcheting.
4.3 Seismic Dampers
Incorporating seismic dampers can reduce the impact of seismic loads:
- Viscoelastic Dampers: Absorb and dissipate energy, reducing the load transmitted to the pipe elbows.
- Base Isolation: Techniques that isolate the piping system from ground motion can minimize deformation.
Conclusion
The ratcheting behavior of plain carbon steel pipe elbows under simulated seismic in-plane bending is a critical consideration in the design and maintenance of piping systems in seismic regions. Understanding the factors influencing ratcheting, such as material properties, geometry, and loading conditions, is essential for developing effective mitigation strategies. By implementing design improvements, selecting appropriate materials, and incorporating seismic dampers, engineers can enhance the resilience of piping systems against seismic events. Ongoing research and advancements in materials science and structural engineering will continue to improve our understanding and management of ratcheting behavior, ensuring the safety and reliability of critical infrastructure.
You must be logged in to post a comment.