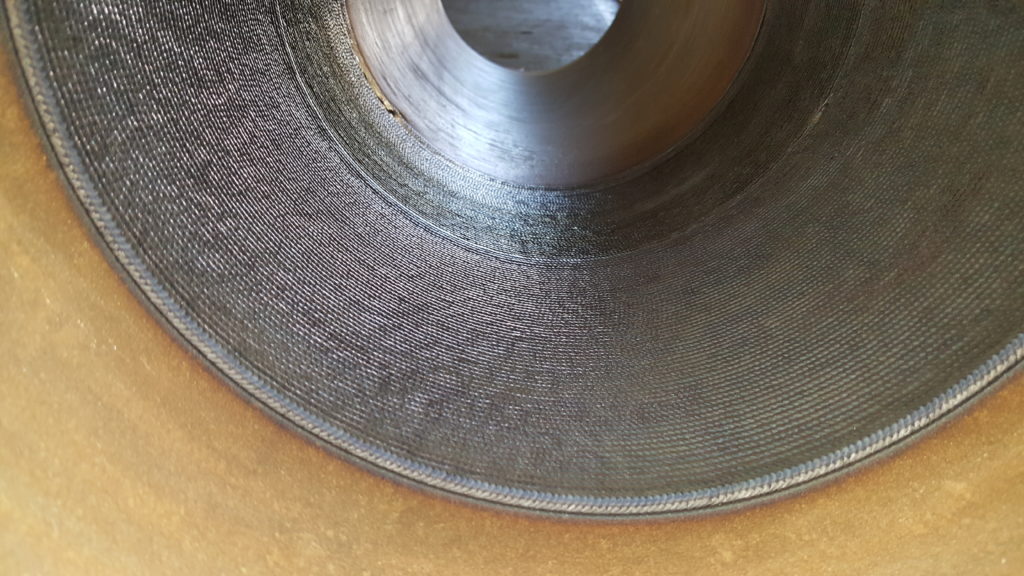
The Advantages of Nickel Alloy Cladding in Industrial Piping Solutions
Introduction
In the ever-evolving landscape of industrial engineering, the quest for materials that can withstand harsh environments while maintaining structural integrity is ongoing. Among the myriad of solutions available, nickel alloy cladding has emerged as a formidable choice in industrial piping solutions. This article delves into the advantages of nickel alloy cladding, exploring its properties, applications, and the reasons behind its growing popularity in various industries.
1. Understanding Nickel Alloy Cladding
1.1 What is Nickel Alloy Cladding?
Nickel alloy cladding involves the application of a nickel-based alloy layer onto a substrate material, typically carbon or low alloy steel. This process enhances the surface properties of the substrate, imparting superior resistance to corrosion, wear, and high temperatures. The cladding process can be achieved through various methods, including welding, roll bonding, and explosive bonding, each offering distinct advantages depending on the application requirements.
1.2 Types of Nickel Alloys Used in Cladding
-
Inconel: Known for its excellent oxidation and corrosion resistance at high temperatures, Inconel is a popular choice in industries such as aerospace and chemical processing.
-
Monel: Comprising nickel and copper, Monel alloys offer exceptional resistance to seawater and acidic environments, making them ideal for marine applications.
-
Hastelloy: With a high molybdenum content, Hastelloy alloys provide outstanding resistance to pitting and crevice corrosion, especially in aggressive chemical environments.
2. Advantages of Nickel Alloy Cladding
2.1 Corrosion Resistance
One of the primary advantages of nickel alloy cladding is its exceptional corrosion resistance. Nickel alloys form a protective oxide layer on their surface, which acts as a barrier against corrosive agents. This property is particularly beneficial in industries such as oil and gas, chemical processing, and power generation, where pipes are exposed to corrosive substances.
-
Oil and Gas Industry: In offshore drilling and production, pipes are subjected to harsh conditions, including exposure to seawater, hydrogen sulfide, and carbon dioxide. Nickel alloy cladding provides a robust defense against these corrosive elements, prolonging the lifespan of piping systems and reducing maintenance costs.
-
Chemical Processing: In chemical plants, pipes often transport aggressive chemicals that can cause rapid degradation of unprotected materials. Nickel alloy cladding ensures that pipes remain intact and functional, even in the presence of strong acids and bases.
2.2 High-Temperature Stability
Nickel alloys are renowned for their ability to maintain structural integrity at elevated temperatures. This makes them an ideal choice for applications involving high-temperature processes, such as power generation and petrochemical refining.
-
Power Generation: In power plants, pipes are exposed to high temperatures and pressures. Nickel alloy cladding prevents thermal degradation and ensures the safe and efficient operation of piping systems.
-
Petrochemical Refining: The refining process involves high-temperature reactions that can weaken conventional materials. Nickel alloy cladding provides the necessary thermal stability to withstand these conditions, enhancing the reliability of the piping infrastructure.
2.3 Wear and Erosion Resistance
In addition to corrosion and temperature resistance, nickel alloy cladding offers excellent wear and erosion resistance. This is particularly important in industries where pipes are subjected to abrasive materials or high-velocity fluids.
-
Mining Industry: In mining operations, pipes transport slurry and other abrasive materials. Nickel alloy cladding protects the pipes from wear and erosion, reducing the frequency of replacements and downtime.
-
Hydropower: In hydropower plants, pipes carry water at high velocities, which can cause erosion of the pipe surface. Nickel alloy cladding provides a durable barrier against this erosion, ensuring the longevity of the piping system.
2.4 Cost-Effectiveness
While the initial cost of nickel alloy cladding may be higher than traditional materials, its long-term benefits often outweigh the upfront investment. The extended lifespan, reduced maintenance requirements, and improved reliability of cladded pipes result in significant cost savings over time.
-
Reduced Maintenance: The superior resistance properties of nickel alloy cladding minimize the need for frequent inspections and repairs, leading to lower maintenance costs.
-
Extended Lifespan: By protecting the substrate material from corrosion, wear, and thermal degradation, nickel alloy cladding extends the service life of piping systems, delaying the need for replacements.
3. Applications of Nickel Alloy Cladding
3.1 Oil and Gas Industry
In the oil and gas sector, nickel alloy cladding is used extensively in pipelines, risers, and flowlines. Its corrosion resistance and high-temperature stability make it an ideal choice for transporting hydrocarbons in challenging environments.
-
Offshore Drilling: In offshore platforms, nickel alloy cladding protects pipes from the corrosive effects of seawater and hydrocarbons, ensuring safe and efficient operations.
-
Refineries: In refineries, cladded pipes handle high-temperature processes and corrosive substances, maintaining the integrity of the piping network.
3.2 Chemical Processing
Chemical plants rely on nickel alloy cladding to protect pipes from aggressive chemicals and high temperatures. This ensures the safe and efficient transport of chemicals, reducing the risk of leaks and contamination.
-
Acid Production: In acid production facilities, nickel alloy cladding withstands the corrosive effects of sulfuric and hydrochloric acids, preventing pipe degradation.
-
Pharmaceutical Manufacturing: In pharmaceutical plants, cladded pipes maintain purity and prevent contamination during the transport of sensitive chemicals.
3.3 Power Generation
In power plants, nickel alloy cladding is used in steam and gas turbines, heat exchangers, and boilers. Its high-temperature stability and corrosion resistance ensure the efficient operation of these critical components.
-
Nuclear Power: In nuclear power plants, cladded pipes transport radioactive fluids, requiring materials that can withstand extreme conditions without compromising safety.
-
Fossil Fuel Power: In fossil fuel plants, nickel alloy cladding protects pipes from the corrosive effects of flue gases and high-temperature steam.
3.4 Marine Applications
Nickel alloy cladding is widely used in marine environments, where pipes are exposed to seawater and other corrosive elements. Its resistance to seawater corrosion makes it an ideal choice for shipbuilding and offshore structures.
-
Shipbuilding: In shipbuilding, cladded pipes transport fuel and other fluids, ensuring reliable performance in harsh marine conditions.
-
Offshore Structures: In offshore platforms, nickel alloy cladding protects pipes from the corrosive effects of seawater and hydrocarbons, ensuring safe and efficient operations.
4. Methods of Nickel Alloy Cladding
4.1 Welding
Welding is a common method for applying nickel alloy cladding to pipes. Techniques such as overlay welding and laser cladding are used to deposit a nickel alloy layer onto the substrate material.
-
Overlay Welding: Overlay welding involves the application of a nickel alloy layer using arc welding techniques. This method is suitable for large-diameter pipes and provides a uniform cladding layer.
-
Laser Cladding: Laser cladding uses a laser beam to melt and deposit a nickel alloy powder onto the substrate. This method offers precise control over the cladding thickness and is ideal for complex geometries.
4.2 Roll Bonding
Roll bonding is a process in which a nickel alloy sheet is bonded to the substrate material through a combination of heat and pressure. This method is suitable for large-scale production and provides a strong metallurgical bond between the cladding and substrate.
-
Advantages: Roll bonding offers excellent adhesion and uniformity, making it suitable for high-pressure applications.
-
Applications: This method is commonly used in the production of cladded plates for heat exchangers and pressure vessels.
4.3 Explosive Bonding
Explosive bonding is a unique process that uses controlled explosions to bond a nickel alloy layer to the substrate material. This method is ideal for cladding large areas and provides a strong bond with minimal distortion.
-
Advantages: Explosive bonding offers excellent adhesion and is capable of bonding dissimilar metals.
-
Applications: This method is used in the production of cladded plates for heat exchangers and pressure vessels.
5. Challenges and Considerations
5.1 Cost
While nickel alloy cladding offers numerous benefits, its initial cost can be higher than traditional materials. However, the long-term savings in maintenance and replacement costs often justify the investment.
-
Cost-Benefit Analysis: A thorough cost-benefit analysis should be conducted to determine the feasibility of nickel alloy cladding for a specific application.
-
Return on Investment: The extended lifespan and reduced maintenance requirements of cladded pipes contribute to a favorable return on investment.
5.2 Technical Expertise
The application of nickel alloy cladding requires specialized technical expertise and equipment. Ensuring the proper selection of cladding method and material is crucial for achieving optimal results.
-
Training and Certification: Personnel involved in the cladding process should receive appropriate training and certification to ensure quality and safety.
-
Quality Control: Rigorous quality control measures should be implemented to ensure the integrity and performance of cladded pipes.
5.3 Compatibility
The compatibility of nickel alloy cladding with the substrate material and the operating environment should be carefully considered. Factors such as thermal expansion and galvanic corrosion must be addressed to prevent issues during service.
-
Material Selection: The selection of compatible materials is essential for ensuring the long-term performance of cladded pipes.
-
Environmental Considerations: The operating environment, including temperature, pressure, and chemical exposure, should be considered when selecting cladding materials.
Conclusion
Nickel alloy cladding offers a range of advantages that make it an attractive choice for industrial piping solutions. Its exceptional corrosion resistance, high-temperature stability, and wear resistance ensure the reliable performance of piping systems in demanding environments. While the initial cost may be higher, the long-term benefits of reduced maintenance, extended lifespan, and improved reliability make nickel alloy cladding a cost-effective solution for many industries. As technology advances and the demand for durable materials grows, nickel alloy cladding is poised to play an increasingly important role in the future of industrial engineering.
You must be logged in to post a comment.