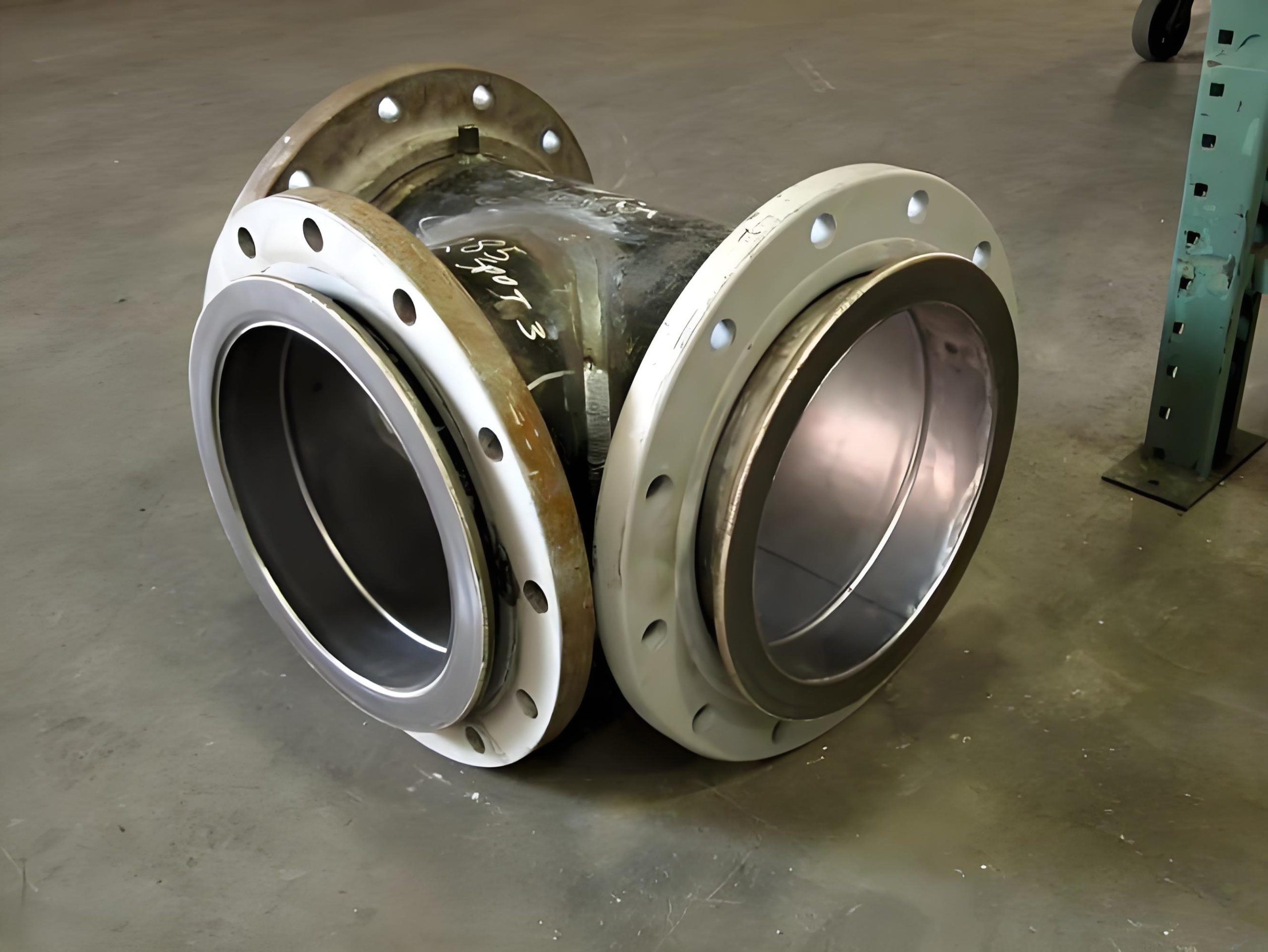
Welding Process for Carbon Steel Pipe and Stainless Steel Flange
1. Material Preparation
Before you even strike an arc, proper preparation is key. Here’s what you need to do:
-
Cleaning: Ensure both the carbon steel pipe and the stainless steel flange are clean. Remove any dirt, oil, or rust using a wire brush or chemical cleaner. This helps prevent contamination during welding.
-
Fit-Up: Align the pipe and flange properly. Use clamps or tack welds to hold them in place. Proper alignment is crucial for a strong joint and to avoid any stress during operation.
2. Choosing the Right Filler Material
The choice of filler material is crucial when welding dissimilar metals like carbon steel and stainless steel. A common choice is austenitic stainless steel filler, such as ER309 or ER309L, which provides good compatibility between the two materials.
3. Welding Technique
-
TIG Welding (GTAW): Tungsten Inert Gas welding is often preferred for this task due to its precision and control. It produces high-quality welds with minimal contamination.
-
MIG Welding (GMAW): Metal Inert Gas welding can also be used, especially for larger projects. It’s faster than TIG but requires careful control to avoid defects.
-
Stick Welding (SMAW): Shielded Metal Arc Welding is another option, particularly for fieldwork. Using a stainless steel electrode, like E309, can help bridge the materials.
4. Welding Parameters
-
Heat Control: Stainless steel is sensitive to heat, which can cause warping or corrosion if not managed properly. Use lower heat input and allow for cooling between passes to prevent overheating.
-
Interpass Temperature: Maintain a low interpass temperature, ideally below 300°F (150°C), to prevent carbide precipitation in stainless steel, which can lead to corrosion.
5. Post-Weld Treatment
-
Inspection: After welding, inspect the joint for defects such as cracks, porosity, or incomplete fusion. Non-destructive testing methods like ultrasonic testing can be useful.
-
Pickling and Passivation: For stainless steel, consider pickling and passivation to restore the protective oxide layer and enhance corrosion resistance.
Suggestions for a Successful Weld
-
Preheat the Carbon Steel: Preheating the carbon steel pipe can help reduce the risk of cracking by minimizing the temperature gradient between the two materials.
-
Use Backing Gas: When TIG welding, use a backing gas like argon to protect the root side of the weld from oxidation, ensuring a cleaner weld.
-
Practice Good Technique: Consistent travel speed and torch angle are crucial for a uniform weld bead. Practice on scrap material if you’re new to welding dissimilar metals.
-
Consider Expansion Differences: Remember that carbon steel and stainless steel have different thermal expansion rates. Design the joint to accommodate this, especially in high-temperature applications.
-
Consult Standards and Codes: Refer to relevant welding standards and codes (like ASME or AWS) for guidance on procedures and qualifications specific to your application.
By following these steps and suggestions, you can achieve a strong, reliable weld between carbon steel pipes and stainless steel flanges. It’s all about preparation, using the right materials, and controlling the welding process to accommodate the unique properties of each metal. Happy welding!
You must be logged in to post a comment.