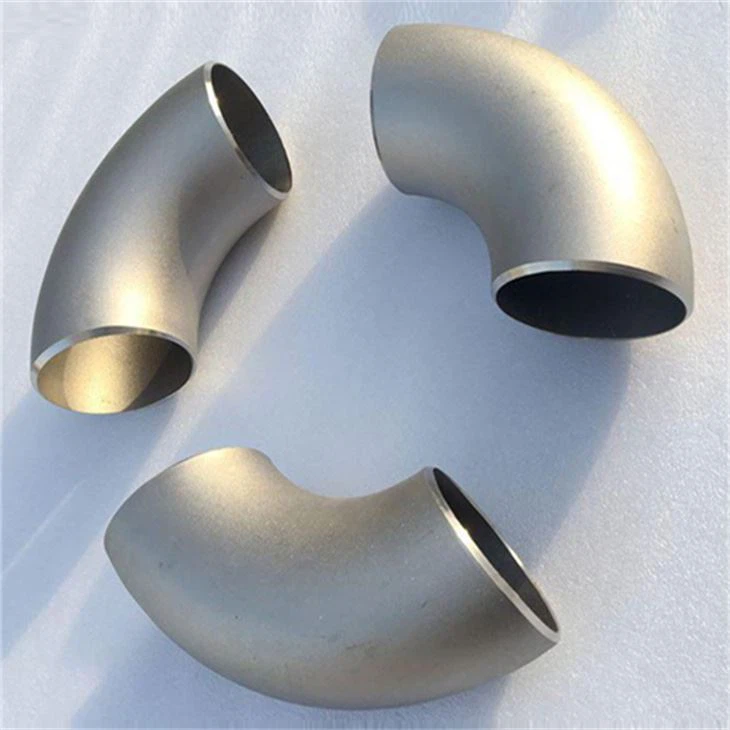
304 and 316 Stainless Steel Butt Welded Pipe Fittings
Introduction
In the world of piping systems, stainless steel butt welded pipe fittings are essential components that ensure seamless connections and efficient flow of fluids. Among the various grades of stainless steel, 304 and 316 are the most commonly used due to their excellent properties and versatility. This article explores the characteristics, applications, and benefits of 304 and 316 stainless steel butt welded pipe fittings, highlighting their role in enhancing the performance and reliability of piping systems.
Understanding 304 and 316 Stainless Steel
304 Stainless Steel
304 stainless steel is an austenitic grade known for its excellent corrosion resistance, formability, and weldability. It contains approximately 18% chromium and 8% nickel, which contribute to its durability and resistance to oxidation.
316 Stainless Steel
316 stainless steel is another austenitic grade that offers superior corrosion resistance, particularly in harsh environments. It contains molybdenum, which enhances its resistance to pitting and crevice corrosion, making it ideal for marine and chemical applications.
Characteristics of Butt Welded Pipe Fittings
Seamless Connections
Butt welded pipe fittings provide seamless connections between pipes, reducing the risk of leaks and ensuring a smooth flow of fluids. The welding process creates a strong joint that can withstand high pressures and temperatures.
Versatility
These fittings are available in various shapes and sizes, including elbows, tees, reducers, and caps, allowing for versatile configurations in piping systems. They can be customized to meet specific requirements, ensuring optimal performance.
Durability
Made from high-quality stainless steel, butt welded pipe fittings offer exceptional durability and longevity. They resist corrosion, oxidation, and wear, ensuring reliable operation in demanding environments.
Applications of 304 and 316 Stainless Steel Butt Welded Pipe Fittings
Chemical Processing
In chemical processing plants, 316 stainless steel fittings are preferred due to their resistance to corrosive chemicals and high temperatures. They ensure the safe and efficient transport of hazardous substances.
Food and Beverage Industry
304 stainless steel fittings are widely used in the food and beverage industry due to their hygienic properties and resistance to food acids. They ensure the safe transport of food products and prevent contamination.
Marine and Offshore
316 stainless steel fittings are ideal for marine and offshore applications, where exposure to saltwater and harsh conditions is common. Their superior corrosion resistance ensures long-term reliability and safety.
Pharmaceutical Industry
Both 304 and 316 stainless steel fittings are used in the pharmaceutical industry to maintain the purity and integrity of products. Their smooth surfaces and resistance to corrosion make them suitable for sterile environments.
Benefits of Using 304 and 316 Stainless Steel Butt Welded Pipe Fittings
Corrosion Resistance
Both 304 and 316 stainless steel fittings offer excellent corrosion resistance, ensuring long-lasting performance in various environments. This reduces maintenance costs and extends the lifespan of piping systems.
High Strength
The high strength of stainless steel butt welded fittings allows them to withstand high pressures and temperatures, making them suitable for demanding applications.
Aesthetic Appeal
Stainless steel fittings have a sleek and polished appearance, enhancing the aesthetic appeal of piping systems. This is particularly important in industries where appearance matters, such as food and beverage.
Cost-Effectiveness
While stainless steel fittings may have a higher initial cost, their durability and low maintenance requirements make them a cost-effective choice in the long run.
Conclusion
304 and 316 stainless steel butt welded pipe fittings are indispensable components in modern piping systems, offering seamless connections, durability, and versatility. Their excellent corrosion resistance and high strength make them suitable for a wide range of applications, from chemical processing to marine environments. As industries continue to demand reliable and efficient piping solutions, these stainless steel fittings will remain a preferred choice for enhancing the performance and reliability of piping systems.
FAQ
1. What are the main differences between 304 and 316 stainless steel?
The main difference is the addition of molybdenum in 316 stainless steel, which enhances its corrosion resistance, particularly in harsh environments.
2. Why are butt welded pipe fittings preferred in piping systems?
Butt welded pipe fittings provide seamless connections, reducing the risk of leaks and ensuring a smooth flow of fluids.
3. What industries commonly use 304 and 316 stainless steel fittings?
Industries such as chemical processing, food and beverage, marine, offshore, and pharmaceuticals commonly use these fittings due to their excellent properties.
4. How do stainless steel fittings enhance the performance of piping systems?
Their corrosion resistance, high strength, and durability ensure reliable operation and reduce maintenance costs, enhancing overall system performance.
5. Are stainless steel butt welded fittings cost-effective?
Yes, their durability and low maintenance requirements make them a cost-effective choice in the long run, despite a higher initial cost.
You must be logged in to post a comment.