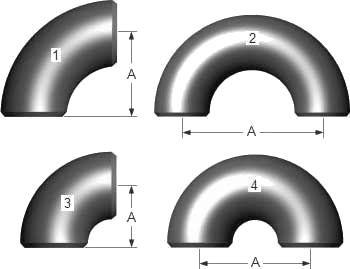
Socket weld fittings and buttweld fittings are two types of pipe fittings used to connect pipes or pipe sections in various applications. They differ in their design, installation method, and suitable applications. Here’s a comparison of the two types of fittings:
Socket Weld Fittings:
-
Design: Socket weld fittings have a socket (recess) into which the pipe is inserted. The pipe’s outside diameter is slightly smaller than the socket’s inside diameter, creating a tight fit. The socket is typically larger than the pipe to allow for expansion during welding.
-
Installation: To install a socket weld fitting, the pipe is inserted into the socket, and a fillet weld is made around the joint between the fitting and the pipe. This method does not require any pipe preparation, such as beveling.
-
Applications: Socket weld fittings are mainly used for small-diameter pipes (usually up to 2 inches) and in applications where there is limited space or a need for quick installation. They are commonly used in high-pressure systems, such as hydraulic and steam lines.
-
Advantages: These fittings offer strong, leak-proof connections and are relatively easy and quick to install. They are also suitable for applications with high pressure and temperature fluctuations.
-
Disadvantages: Socket weld fittings can be more prone to fatigue and stress corrosion cracking due to the crevices formed around the joint. Additionally, they may not be suitable for large-diameter piping systems or applications involving highly corrosive or erosive fluids.
Buttweld Fittings:
-
Design: Buttweld fittings have a smooth, beveled end that matches the bevel on the pipe to be connected. The pipe and fitting are aligned and then welded together, creating a strong, continuous joint.
-
Installation: To install a buttweld fitting, the pipe must be prepared by cutting it to the required length and beveling the end at the appropriate angle. The pipe and fitting are then aligned and welded together using a full penetration weld.
-
Applications: Buttweld fittings are used for larger-diameter pipes (typically above 2 inches) and in applications requiring a strong, leak-proof connection. They are commonly used in oil and gas, chemical, and power generation industries, where high-pressure, high-temperature, and corrosive conditions are present.
-
Advantages: These fittings provide a strong, continuous connection that is less prone to fatigue and stress corrosion cracking. They also offer a smoother flow path, reducing pressure losses and turbulence. Buttweld fittings are suitable for high-pressure, high-temperature, and corrosive applications.
-
Disadvantages: Buttweld fittings require more extensive pipe preparation and skilled welding for proper installation, making them more time-consuming and labor-intensive than socket weld fittings. They may also be less suitable for small-diameter piping systems or applications with limited space.
In summary, socket weld fittings are typically used for small-diameter pipes and in situations where quick installation is needed, while buttweld fittings are more suitable for larger-diameter pipes and applications requiring strong, continuous connections. The choice between these two types of fittings depends on factors such as pipe size, pressure and temperature requirements, installation constraints, and the specific application.
You must be logged in to post a comment.