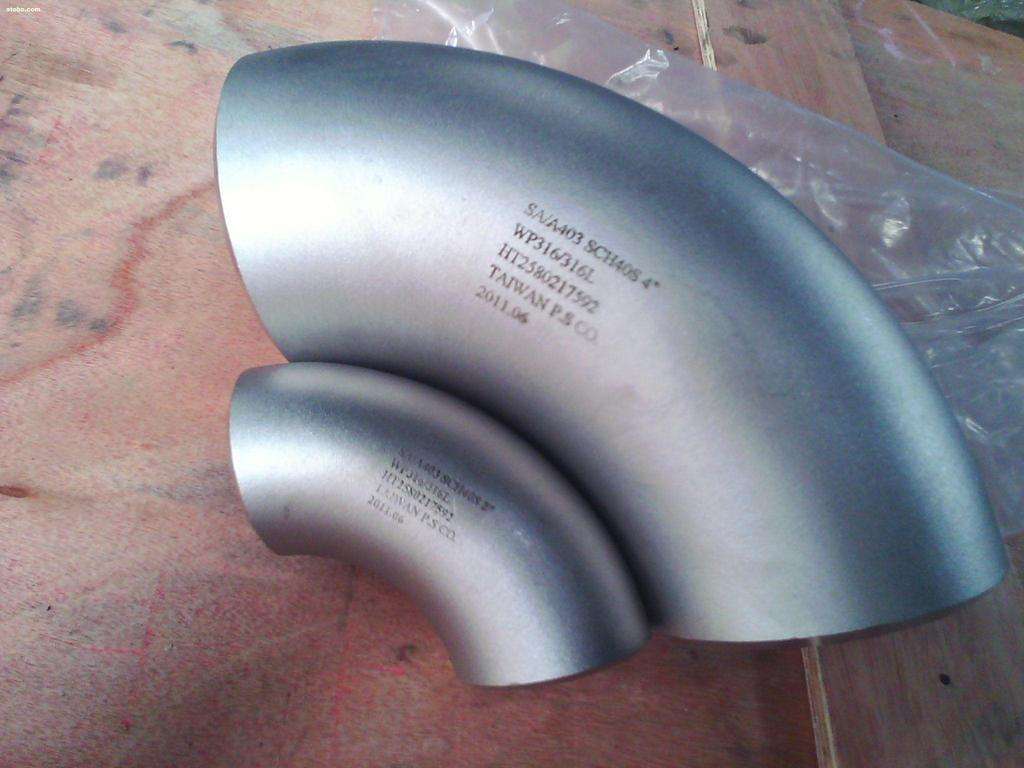
A 45° elbow, 90° elbow, and 180° elbow are pipe fittings used to change the direction of a piping system. These fittings are widely used in various industries, such as oil and gas, petrochemical, power generation, water treatment, and many more. This article discusses the differences between these elbow fittings, focusing on long radius (LR) and short radius (SR) elbows.
1. Angle of the elbow
The most obvious difference among the three types of elbows is the angle they create:
- 45° elbow: Changes the direction of the pipeline by 45 degrees.
- 90° elbow: Changes the direction of the pipeline by 90 degrees, making a right-angle turn.
- 180° elbow: Changes the direction of the pipeline by 180 degrees, creating a U-turn or complete reversal of flow direction.
2. Long Radius (LR) vs. Short Radius (SR) elbows
Another key distinction between elbow fittings is the radius of curvature, which determines the space required for installation and the pressure drop across the fitting:
-
Long Radius (LR) elbows: These elbows have a center-to-end distance equal to 1.5 times the nominal pipe size (NPS) or the outside diameter (OD) of the pipe. LR elbows offer less resistance to fluid flow and consequently produce lower pressure drop, making them suitable for low-pressure systems or applications with strict pressure limitations.
-
Short Radius (SR) elbows: These elbows have a center-to-end distance equal to the nominal pipe size (NPS) or the outside diameter (OD) of the pipe. SR elbows have a tighter curve compared to LR elbows, resulting in a higher pressure drop. They are typically used in tight spaces or applications where space constraints are critical.
-
Elbows are split into two groups which define the distance over which they change direction; the center line of one end to the opposite face. This is known as the center to face distance and is equivalent to the radius through which the elbow is bent.
The center to face distance for a long radius elbow, abbreviated LR always is 1.1/2 x Nominal Pipe Size (NPS) (1.1/2D), while the center to face distance for a short radius elbow, abbreviated SR even is to nominal pipe size.Here below, for example, you will find the
center to face distance of NPS 2 elbows
(the A distance on the image)1. 90°-LR.. = 1.1/2 x 2(NPS) x 25.4 A=76.2 mm
2. 180°-LR.. = 2 times the 90° LR elbow A=152.4 mm
3. 90°-SR.. = 2(NPS) x 25.4 A=50.8 mm
4. 180°-SR.. = 2 times the 90° SR elbow A=101.6 mm
3D elbows as an example, are calculated with..
3(D) x 2(NPS) x 25.4
3. Flow characteristics
The angle and radius of an elbow fitting can significantly affect the flow characteristics within a piping system:
-
45° elbows: These elbows cause the least disturbance to the flow and thus generate the lowest pressure drop among the three types. They are often used for gradual changes in direction or in combination with other elbow fittings to achieve a specific angle.
-
90° LR elbows: Offering a smoother flow path than SR elbows, LR elbows cause a lower pressure drop and are preferred in applications where maintaining flow characteristics is important.
-
90° SR elbows: Due to their tighter bend, SR elbows generate a higher pressure drop and are more likely to cause turbulent flow, which may lead to increased erosion, vibration, or noise in the piping system.
-
180° elbows: These fittings cause the greatest disruption to the flow, as they force the fluid to reverse direction completely. However, they are essential in specific applications where a complete change in flow direction is required.
4. Applications
Each type of elbow fitting is suited for different applications based on their angle and radius:
-
45° elbows: Typically used in applications where a moderate change in direction is needed, such as water and wastewater treatment, chemical processing, and power generation.
-
90° LR elbows: Commonly used in applications where a right-angle turn is required, and pressure drop is a concern, such as oil and gas, petrochemical, and process industries.
-
90° SR elbows: Suitable for space-constrained applications or where a right-angle turn is required, and pressure drop is not a significant concern.
-
180° elbows: Often used in applications where a complete reversal in flow direction is necessary, such as process industries, heat exchangers, and cooling systems.
5. Material and manufacturing
Elbow fittings are made from various materials, including carbon steel, stainless steel, alloy steel, and more, depending on the requirements of the specific application. The manufacturing process for these fittings typically involves forging, casting, or welding.
6. Standards and specifications
Elbow fittings are manufactured according to various international standards, such as ASME B16.9 (for factory-made wrought buttwelding fittings), ASME B16.11 (for forged fittings), and ASME B16.28 (for wrought steel buttwelding short radius elbows and returns). These standards define the dimensions, tolerances, marking, and material requirements for elbows.
In conclusion, 45°, 90°, and 180° elbows differ in their angle and radius, which affects the flow characteristics, pressure drop, and space requirements of the piping system. These differences make each type of elbow fitting suitable for specific applications, industries, and conditions. It is essential to select the appropriate elbow fitting based on the requirements of the system to ensure optimal performance, reliability, and safety.
45° Elbow
The function of a 45° elbow is the same as a 90° elbow, but the measurement of dimensions is different to that of the 90° elbow.
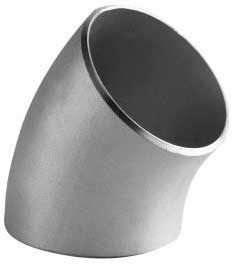

The radius of a 45° elbow is the same as the radius of the 90° LR (1.1/2D). However, the center to face dimension is not equivalent to the radius as in 90° LR elbows. This is measured from each face to the point of intersection of the center lines perpendicular to each other, distances B on the image. This is due to the smaller degree of bend. Short radius 45° elbows are not available.
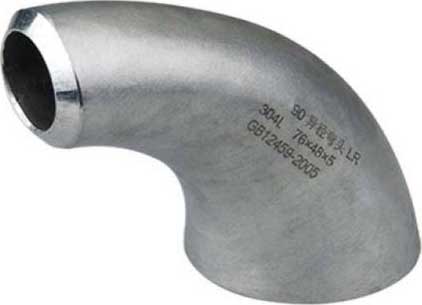
Wall Thickness of Elbows
The weakest point on an elbow is the inside radius. ASME B16.9 only standardizes the center to face dimensions and some squareness dimensional tolerances. The wall thickness at the weld line location even is standardized, but not through the rest of an elbow. The standard states that the minimum tolerance will be within 12.5% of the minimum ordered wall thickness of the pipe. A maximum tolerance is specified only at the ends of the fitting.
Many providers of buttweld elbows (and tees) provide one schedule greater thickness so that sufficient wall thickness, after forming, remains.
You must be logged in to post a comment.