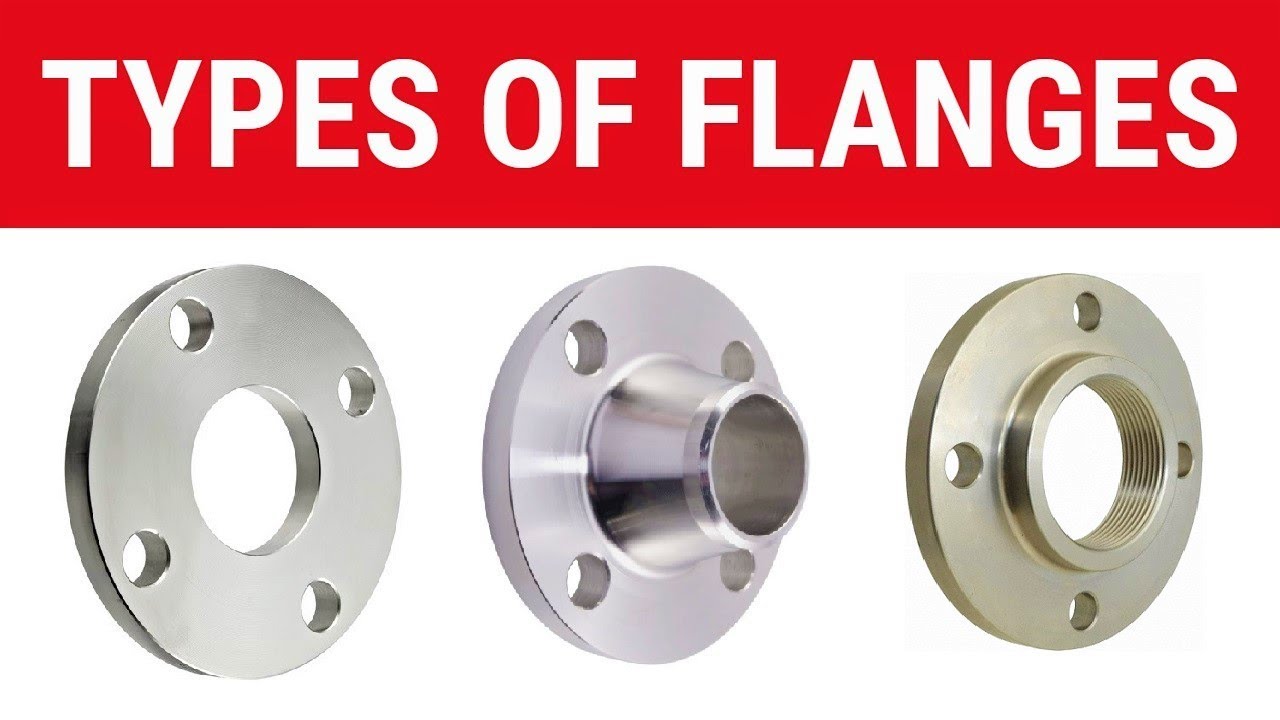
Abstract: Welding flanges have a pivotal role in mechanical production, for people who initially understand the welding flanges, welding flanges have several characteristics that are necessary to understand, for the application of welding flanges in production will be very helpful, the following will briefly introduce the characteristics of several common methods of welding flanges and influencing factors.
Keywords: welding flange type; Welding flange applications; Influencing factors
First, the type of welding flange
1. Argon arc welding
Argon arc welding is a relatively advanced welding flange method, in the welding flange process using argon protection, isolated from the air of oxygen, nitrogen and other gases on the arc and the impact of the pool, so argon arc welding obtained welding flange quality is better, beautiful molding, and welding flange efficiency is high, welding flange defects are few, weld strength is high, weld crack tendency is small, and argon arc welding is not affected by the position of the weldment, can be welded in all positions, is a favored welding flange method.
Argon arc welding welding argon arc welding argon arc welding in the field of strict requirements for weld strength is more widely used, such as in shipbuilding, boilers, pump shells and other pressure vessel welding flanges, pipe and pipe to get butt welds, defects need to be reworked welds, these positions need to have high efficiency argon arc welding to complete. Due to the use of argon protection in the welding flange process, argon arc welding specific welding consumables, its cost leaf correspondingly increased, so argon arc welding in the production can not be applied on a large scale, usually in the high quality requirements of the weld position is used, which is the actual application of argon arc welding deficiencies.
2. Carbon dioxide gas shielded welding
Two-warrant welding is a wide range of welding flange method, its welding flange speed is fast, welding flange productivity is relatively high, welding flange deformation is relatively small, crack resistance is better, can weld flange plate thickness range is relatively large, in the production is very commonly used. Carbon dioxide gas brazing weldable flange can be welded in a wide range of materials, ordinary carbon steel and stainless steel can be welded with two brach welding flanges
The application of two-warrant welding is more, the production of various thicknesses of plate and plate welding flanges, welding flanges of sections, and welding flanges of other structural parts, two-warrant welding can meet the use, the welding flange method greatly saves production costs. The second warrant welding also has certain shortcomings, mainly poor weld molding, easy to appear splash and porosity, the defect may need to use other welding flange methods such as argon arc welding rework to make up.
3. Submerged arc welding
Submerged arc welding is a relatively advanced welding flange method, welding flange must use submerged arc welding machine, its welding flange quality is stable, weld quality is good, welding flange productivity is high, due to the arc in the flux layer under the combustion of welding flange and very little smoke dust and arc radiation, labor conditions are better, submerged arc welding machine can be automated operation, reducing the labor intensity of manual welding. Submerged arc welding Due to the use of submerged arc welding machine for welding flanges, the welding flange flexibility is not as flexible as manual operation, and the full position welding flange cannot be carried out, which is also the shortcoming of submerged arc welding.
Submerged arc welding can be used to weld steel plate welds with relatively large flange thickness, long-distance welds and ring welds with large diameters, and is widely used in welding flanges in shipbuilding, boilers, marine structures and other equipment.
4. Robot welding flange
Robot welding flange as an emerging way of welding flange, has been more and more used in mechanical production, through the setting of procedures and parameters, can make the robot in the workpiece automatic welding flange, stabilize and improve the quality of welding flange, instead of manual welding flange, greatly reducing the labor intensity of manual operation, improve the speed and production efficiency of welding flange, reduce the requirements of workers operating technology. The robot welding flange also has the disadvantage of inflexible welding flange, and cannot weld the flange in full position.
Robot welding flanges have been greatly used in industrial production such as automobile production, construction machinery, mining machinery and so on.
5. Manual electrode welding
Manual welding electrode welding as the most traditional welding flange method, due to the slow speed of welding flange, welding flange stability is not high, weld quality is not high, the application in modern industrial production is relatively no longer extensive, replaced by other welding flange methods, in some enterprise production as an inherent welding flange qualification and existence.
Second, the influencing factors of welding flanges
When using various welding flange methods for welding flanges, the welding flange current, voltage and welding flange speed will affect the quality of the welding flange
1. Welding flange current
The influence of welding flange current on the quality of the weld seam is relatively large, and when the current is small, it will lead to difficulty in inducing arcs, unstable arcs, and welding impermeable phenomena, and when the current is too large, it will lead to defects such as biting edges and burn-through.
2. Welding flange voltage
When the welding flange current is fixed, the range of welding flange voltage variability is relatively small, under normal circumstances, when the welding flange voltage is small, the weld melting depth is large, the weld seam is narrow, and there is a surplus high; When the welding flange voltage is too large, it will produce defects such as porosity, slag clamping and unsolder penetration.
3. Welding flange speed
In a certain range, the greater the welding flange speed, the weld penetration depth will increase accordingly, and the weld width will decrease; Beyond this range, the melt depth and width of the weld will gradually decrease as the speed of the welding flange increases. In the actual production, as far as possible to increase the welding flange speed, improve production efficiency, it is necessary to grasp the impact of the increase or decrease of the welding speed, the welding flange speed to the best.
Therefore, in the actual production of welding flange applications, we must grasp the influence characteristics of voltage, current and welding flange speed, and set the best welding flange parameters to obtain the best weld performance
Third, the weld size
When welding flange parts, each weld has a specific size, there are specific considerations when setting the weld size, the weld size is too small will lead to insufficient strength, and the weld size will cause waste of welding consumables and labor consumption when the weld size is too large.
When level angle welding is carried out in production, welds below 8mm usually use single-layer single-channel welding flanges; 10-12mm weld seam using two layers of three welding flanges; 14-16mm weld seam needs to use two layers of four welding flanges; 18-20mm needs to use three layers of seven welding flanges; The weld seam of 22-25mm adopts three layers of eight welding flanges; 26-30mm weld seam needs to use four layers of twelve welds; In the design of the weld size, there should be a weld of the right size, which can ensure the strength of the weld and ensure that no man-hours are wasted.
4. Summary
The above welding flange method is a few welding flange methods that are more common in industrial production, each field according to the characteristics of the specific welding flange to choose the required welding flange, the selection of the appropriate welding flange method is very important for the welding flange operation, which determines the efficiency and cost of production, for welding flange technicians, it is necessary to better understand the characteristics of various welding flanges, choose the appropriate welding flange type; And grasp the influence of welding flange parameters on the performance of welding flanges, set appropriate welding flange parameters, and improve the efficiency of welding flanges; For designers, when setting the welding flange size, it is necessary to ensure the strength of the welding flange, but also to minimize the welding flange man-hours, better serve the production from all aspects, save costs, and improve production efficiency.
You must be logged in to post a comment.