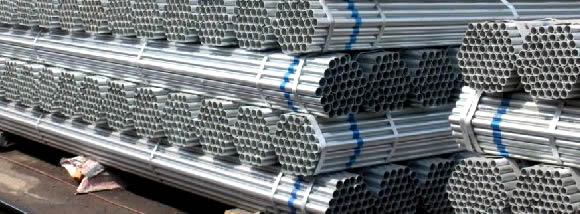
Hot-dip galvanizing (HDG) is the process of dipping fabricated steel into a kettle or vat containing molten zinc. The process is inherently simple which provides a distinct advantage over other corrosion protection methods. While the steel is in the kettle, the iron in the steel metallurgically reacts with the molten zinc to form a tightly-bonded alloy coating that provides superior corrosion protection to steel.
Galvanized steel pipe, hot-dip galvanized and galvanized two kinds, hot-dip galvanized coating thick, zinc plating cost is low, the surface is not very smooth.
Nominal wall thickness: mm2.0, 2.5, 2.8, 3.2, 3.5, 3.8, 4.0, 4.5;
Coefficients: c1.064, 1.051, 1.045, 1.040, 1.036, 1.034, 1.032, 1.028. Note: The mechanical property of steel is an important index to ensure the final use of steel, which depends on the chemical composition and heat treatment system. In the steel pipe standard, according to the different use requirements, the tensile properties (tensile strength, yield intensity or yield point, elongation) as well as hardness, toughness index, and user requirements of high and low temperature performance.
Specification for galvanized pipe steels: q215a;q215b;q235a;q235b
The test pressure value is/mpa:d10.2-168.3mm 3mpa;d177.8-323.9mm 5Mpa. A hot-dip galvanized tube is an alloy layer that reacts with a molten metal to a iron-based body, thus combining the substrate and the coating. Hot-Dip Galvanizing is the first steel pipe pickling, in order to remove iron oxide on the surface of the steel tube, after pickling, through ammonium chloride or zinc chloride aqueous solution or ammonium chloride and zinc chloride mixed water solution trough cleaning, and then into the hot dip bath. Hot-Dip galvanizing has the advantages of uniform coating, strong adhesion and long service life. The complex physical and chemical reaction of the steel tube matrix and molten plating solution forms a close zinc-iron alloy layer with corrosion resistance. The alloy layer blends with the pure zinc layer and the steel tube matrix.
Therefore, its corrosion resistance is strong.
1, the uniformity of galvanized coating: steel tube specimen in copper sulfate solution continuous impregnation 5 times not to red (copper-plated)
2, Surface quality: Galvanized steel pipe surface should be a complete galvanized layer, no plating on the black spots and bubbles exist, allowing a small rough surface and local zinc tumors exist. 3, Galvanized coating weight: According to demand side requirements, galvanized steel pipe can be used for zinc coating weight measurement, the average should be no less than 500g/square meters, of which any sample shall not be less than 480g/square meters.
Hot Dip Galvanized and Related Finishing Methods
Pipeline System provides standard finishing methods for tubing and pipes. We do offer metal tubing and pipe products in aluminum and steel (contact us about alloys). Our most common finishing methods include:
Pre-Galvanized
Plain steel and powder coated finishings
Standard hot dip galvanized methodologies (Galvanneal, G-60 and G-90)
Stainless steel
Flo-Form Galvanized Angle – unique process using our triple-coat process is superior to hot dipped galvanized methods
Gatorshield and Zinc Flo-Coat – coating is applied in-line on the tube mill providing the most corrosion protection over any other method of zinc coating, zinc coating is 99.99% pure zinc (virtually lead free), secondary conversion coating application, and an organic clear polymer coating is then applied
GatorStitch – using the Gatorshield/Zinc Flo-Coat
Triple-coat Process – our innovative, proprietary solution for highly durable coatings for products to be used outdoors or in corrosive environments
You must be logged in to post a comment.