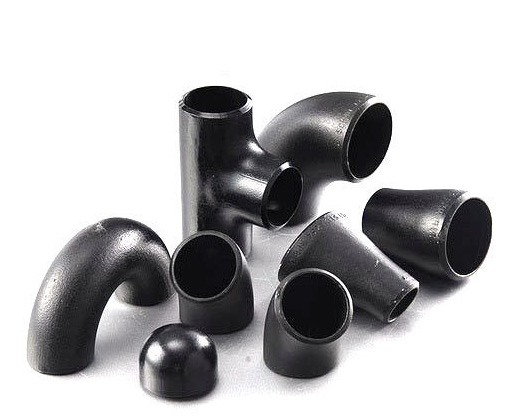
BUTT WELD FITTINGS
Butt weld fittings are the most common type of pipe fittings used for pipelines above 2 inches in diameter and are connected to pipes by welding. Pipe fittings change the pathway and the layout of the pipeline or of a pipework (elbows with 45, 90 and 180 degrees angle curve), reduce/increase its flow conveyance capacity (concentric and eccentric reducers), branch (tees, cross) or blind it (butt weld cap). For smaller pipe sizes, 2 inches and below, forged fittings (socket weld or threaded) are used instead of butt weld fittings.
The material of the pipe shall generally match the material of the connecting butt weld fitting (hence an ASTM A106 Gr. B pipe shall be connected to an ASTM A234 WPB pipe fitting, or an ASTM A312 T304 pipe to an ASTM A403 WP304 pipe fitting and so on).
Also, the dimension a butt weld fitting shall match the dimension of the pipe to be connected (so, for instance, a 6″ schedule 40 pipe matches a 6″ schedule 40 butt weld elbow).
BENEFITS OF BUTT WELD FITTINGS
Butt welding fittings have the following benefits
- allow a strong and leak-proof pipe to fitting connection
- minimize the pressure drops and the turbulence along the pipeline
- have a long service life
- are rather cheap to purchase and deploy
TYPES OF PIPE FITTINGS (BUTT WELD)
Multiple types of pipe fittings are available, which differ in shape and function, such as elbows, tees and crosses, reducers and caps, stub ends, etc (see image below).
Each of this type of pipe fitting is reviewed in separate articles of the projectmaterials.com knowledge base.
PIPE FITTINGS DIMENSIONS AND MATERIALS
Butt weld fittings are manufactured in a wide range of dimensions (combinations of outside diameter and wall thickness, i.e. schedule) and material grades (the most common are ASTM A234 WPB for carbon steel/alloy steel, ASTM A403 WP304 and WP316 for stainless steel wrought fittings, ASTM A815 for duplex and super duplex fittings).
Carbon steel fittings are common for pipelines and process piping applications in the oil and gas and power generation industry, stainless steel fittings are for applications where corrosion and erosion are a key issue (desalination, pharmaceutical and, food sectors).
For specific applications, steel fittings are either coated on the outer surface or internally lined or clad (see the example of an overlay clad tee below).
SEAMLESS VS WELDED FITTINGS
Butt weld fittings are available in seamless and welded execution (seamless for bore sizes below 24 inches, welded for sizes above 24 inches). They are manufactured, respectively, using seamless pipes (butt weld fittings <24 inches), welded pipes (butt weld fittings >24 inches) or steel plates (large diameter fittings, like metered ones).
- Seamless butt weld pipe fittings are manufactured using sections of seamless pipes and applying heat and pressure that shapes the tube into a pipe fitting shape
- A seamless butt weld fitting has no welding, which is a requirement in some high pressure and high-temperature applications. The absence of welds and the related porosities guarantees strength, durability and superior mechanical performance (the pipe fitting is less prone to corrosion attacks)
- A welded butt weld fitting has one, two or more welds, depending on dimension, the required shape and manufacturing process
INDUSTRIES USING BUTT WELD FITTINGS
Butt weld fittings are used in any industry where liquids, gases, chemicals and other fluids are used (manufactured, transported, distributed, processed), such as:
- Oil & Gas: Oil and gas industry, including upstream, midstream (transportation, storage, and local distribution) and downstream (petrochemical refining).
- Power generation: Power plants of any nature, thermal, fossil, nuclear
- Desalination: Plants to produce drinkable water from seawater
- Food and beverage
- Pharma
- Semiconductors
- Pulp and paper
- Construction industry
BUTT WELD FITTINGS MANUFACTURERS
- Awaji
- APP/CB&I
- Bassi Luigi
- Canadoil
- Close Bend
- Colonial Machine
- Erne Fittings
- Ezeflow
- Hackney-Ladish
- Houston Pipe Benders
- IRC Spa
- Mills Iron Works
- OMR Raccordi (Officine Meccaniche Righi)
- Raccortubi
- Shanghai Gateway Fittings Co
- Steel Forgings
- Sungkwang Bend
- Tectubi
- Tenaris
- TK Bend
- Tube Forgings of America
PIPE FITTINGS SPECIFICATIONS
ASME B16.9, ASME B16.28 and, MSS SP43 are the key specifications covering the dimensions and the manufacturing tolerances of butt weld fittings. ASME B16.25 covers the preparation of butt weld connections between pipes and fittings. ASME B16.49 covers the marking details.
ASME B16.9 AND ASME B16.28 (CARBON AND ALLOY PIPE FITTINGS)
“This Standard covers overall dimensions, tolerances, ratings, testing, and markings for wrought carbon and alloy steel factory-made buttwelding fittings of NPS 1/2 through 48. It covers fittings of any producible wall thickness. This standard does not cover low pressure corrosion resistant buttwelding fittings. See MSS SP-43, Wrought Stainless Steel Butt-Welding Fittings. Short radius elbows and returns, which were previously included in ASME B16.28-1994, are included in this standard. B16.9 is to be used in conjunction with equipment described in other volumes of the ASME B16 series of standards as well as with other ASME standards, such as the Boiler and Pressure Vessel Code and the B31 Piping Codes”. (source: ASME)
MSS SP 43 (STAINLESS STEEL AND NICKEL ALLOY PIPE FITTINGS)
The MSS SP 43 sets the dimensions, tolerances, and markings for butt weld fittings for low pressure, corrosion resistant applications. It covers only fittings for use with Schedule 5S or 10S pipe, for all NPS sizes listed in ASME B36.19M, except that for short pattern stub ends suitable for use with Schedule 40S are also shown. Essentially, MSS SP 43 is the reference standard for lightweight corrosion resistant butt weld fittings (stainless steel, duplex).
ASME B16.25 (BUTT WELD ENDS)
ASME B16.25 sets standards for the preparation of the ends of components that need to be welded together. As stated in the ASME website: “This Standard covers the preparation of buttwelding ends of piping components to be joined into a piping system by welding. It includes requirements for welding bevels, for external and internal shaping of heavy-wall components, and for preparation of internal ends (including dimensions and tolerances). Coverage includes preparation for joints with the following: no backing rings; split or noncontinuous backing rings; solid or continuous backing rings; consumable insert rings; gas tungsten arc welding (GTAW) of the root pass” (source: ASME).
Cut square or slight chamfer, at manufacturer’s option for :
- t ≤ 0.19” carbon steel or ferritic alloy steels
- t ≤ 0.12” austenitic alloy steels
Notes :
(1) The value of t mini is whichever of the following is applicable: a) the minimum ordered wall thickness of the pipe, b) 0.875 times the nominal wall thickness of pipe ordered to a pipe schedule wall thickness that has an under tolerance of – 12.5 %.
(2) The maximum thickness at the end of the component is: a) the greater of (t mini + 0.16”) or (1.15 t mini), when ordered on a minimum wall basis, b) the greater of (t mini + 0.16”) or (1.10 t nom.), when ordered on a nominal wall basis.
(3) Weld bevel is shown for illustration only.
(4) The weld reinforcement permitted by the applicable code may lie outside the maximum envelope.
(5) Where transitions using maximum slope do not intersect outside surface within the transition region, as shown by phantom outline, maximum slopes shown shall be used. Alternately, radii lying within the envelope may be used
ASME B16.49
The ASME B16.49 Norm covers the manufacturing, marking, design, material, testing, and inspection requirements for factory-made bends of carbon steel materials having controlled chemistry and mechanical properties, produced by the induction bending process, with or without tangents. This standard covers induction bends for transportation and distribution piping applications (e.g., ASME B31.4, B31.8, and B31.11).
You must be logged in to post a comment.